What Are the Main Differences Between Plastisol Ink and Water-Based Ink in Screen Printing?
In the world of screen printing, selecting the right ink type is crucial to achieving high-quality, long-lasting print results. This article delves into the primary differences between Plastisol Ink and water-based ink in screen printing, providing a comparative analysis to help readers understand the pros and cons of both inks, thereby enabling them to make informed decisions based on their specific needs.
I. Overview of Plastisol Ink
1.1 Definition and Characteristics of Plastisol Ink
Plastisol Ink, also known as plasticizer ink or oil-based paste, is a non-solvent-based ink that appears as a paste. It consists of resin (without solvents or water), pigments, and other additives, with a solid content of up to 100%. Its most notable feature is thixotropy, meaning it is thick when at rest but becomes thinner upon stirring. Additionally, Plastisol Ink does not dry at room temperature; it requires heating to 150°C to 180°C for 1 to 3 minutes to fully cure, resulting in strong adhesion and good elasticity.
1.2 Applicable Scenarios of Plastisol Ink
Plastisol Ink is widely used in textile printing, particularly for finished products such as T-shirts, sportswear, jackets, and canvas bags. Its exceptional adhesion and wash fastness make it suitable for printing complex patterns and high-color requirements. Furthermore, Plastisol Ink is also ideal for rounded-corner transparent sequin processes, enhancing the decorative value and added worth of products.
II. Overview of Water-Based Ink
2.1 Definition and Characteristics of Water-Based Ink
Water-based ink, as the name suggests, is soluble in water and comprises water-soluble resins, organic pigments, solvents, and related additives after compound grinding. The primary advantage of water-based ink lies in its environmental friendliness, as it does not require organic solvents, reducing volatile organic compound (VOC) emissions and posing minimal harm to the environment and human health. Additionally, water-based ink boasts good quick-drying and water-resistance properties, making it suitable for packaging printing products with stringent hygiene requirements.
2.2 Applicable Scenarios of Water-Based Ink
Water-based ink has widespread applications in screen printing, particularly in scenarios that require good adhesion and environmental performance. For instance, it is commonly used in the printing of books, picture albums, and other paper-based products, as well as in food and pharmaceutical packaging materials. With the increasing awareness of environmental protection, more and more printing enterprises are turning to water-based ink to meet market demands.
III. Main Differences Between Plastisol Ink and Water-Based Ink
3.1 Composition and Properties
- Plastisol Ink: Based on resins, it does not contain solvents or water and has a solid content of 100%. It exhibits thixotropy and non-drying properties, requiring heat for curing.
- Water-Based Ink: Soluble in water, composed of water-soluble resins, pigments, and additives. It dries quickly without heating.
3.2 Environmental Friendliness
- Plastisol Ink: Although it does not release harmful gases during use, its processing may be complex, and certain resin components may have environmental impacts.
- Water-Based Ink: Considered the green choice for printing due to its environmental friendliness. It eliminates VOC emissions and poses no harm to the environment or human health.
3.3 Printing Effects and Applicability
- Plastisol Ink: Excels in textile printing, particularly for complex patterns and high-color requirements. It boasts strong adhesion and wash fastness, suitable for long-lasting products.
- Water-Based Ink: Demonstrates good adhesion and printing effects on paper-based products. However, in textile printing, its adhesion and wash fastness may be inferior to Plastisol Ink.
3.4 Cost and Efficiency
- Plastisol Ink: Typically slightly more expensive but offers cost-effectiveness due to its superior printing results and durability. Heating for curing may increase production time and equipment requirements.
- Water-Based Ink: More affordable and easy to use and clean. Its quick-drying properties enhance production efficiency. However, additional fixing treatments may be necessary to enhance adhesion and wash fastness in some applications.
IV. Case Studies and Practical Applications
4.1 Practical Applications of Plastisol Ink
Wilflex Plastisol Ink, for example, enjoys a reputation in the textile printing industry for its exceptional adhesion and wash fastness. Its vibrant colors and clear patterns remain intact after multiple washes. Additionally, Wilflex Plastisol Ink offers a diverse range of colors and effects to cater to customers’ personalized needs.
4.2 Practical Applications of Water-Based Ink
In food packaging printing, water-based ink is highly favored due to its environmental friendliness and excellent printing effects. It ensures the safety standards of printed products while enhancing their overall image and market competitiveness. As environmental regulations become stricter, more packaging printing enterprises are adopting water-based ink.
V. Conclusion
In conclusion, Plastisol Ink and water-based ink each have their unique strengths in screen printing. Plastisol Ink dominates textile printing with its superior adhesion and wash fastness, while water-based ink excels in paper-based printing and food packaging due to its environmental friendliness and good printing effects. When selecting an ink type, factors such as printing materials, pattern requirements, environmental standards, and cost-effectiveness should be considered comprehensively to make the best decision.
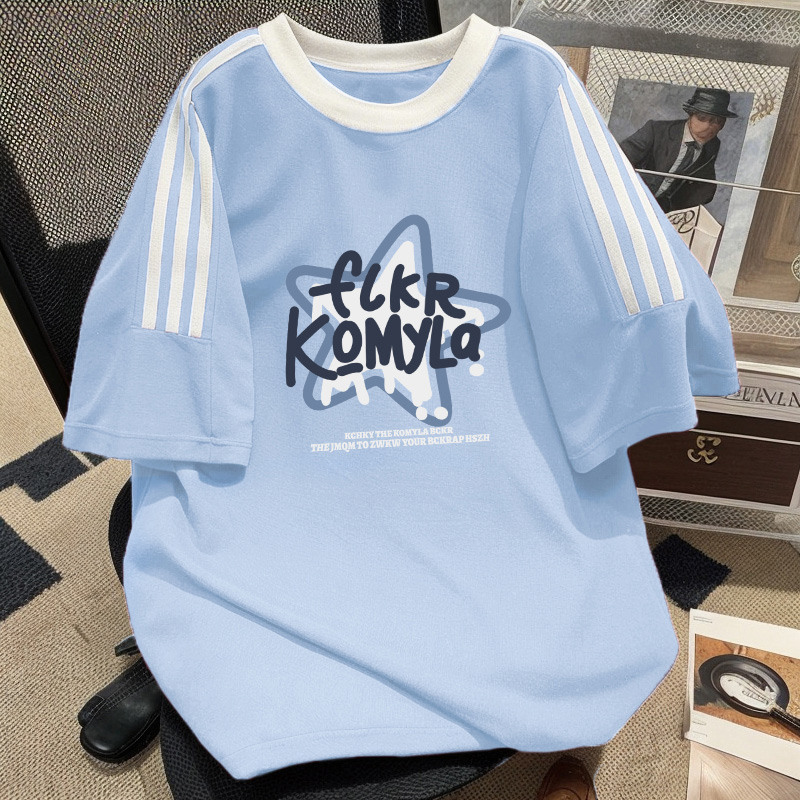