How to Choose the Right Plastisol Ink for Screen Printing?
In the screen printing industry, selecting the appropriate Plastisol Ink is crucial to ensuring print quality and durability. With its vibrant colors, excellent opacity, and wear resistance, Plastisol Ink is widely used in textiles, apparel, advertising signage, and other fields. This article delves into the selection process of finding the most suitable Plastisol Ink for screen printing, revealing key purchasing points and techniques.
I. Understanding the Fundamental Characteristics of Plastisol Ink
1.1 Definition and Advantages of Plastisol Ink
Plastisol Ink is a type of ink composed of PVC resin particles mixed with plasticizers, pigments, and stabilizers. Its unique plasticizing process allows the ink to soften and adhere to the substrate upon heating, forming a soft and durable coating. Compared to other inks, Plastisol Ink boasts vibrant colors, strong opacity, water and wash resistance, and minimal fading, making it ideal for large-area printing and intricate patterns.
1.2 Overview of Selection Criteria
When selecting Plastisol Ink, it’s essential to consider factors such as color representation, printability, environmental friendliness, and cost-effectiveness. These elements directly impact the quality of the printed product, production efficiency, and market acceptance.
II. Key Factors in Choosing Plastisol Ink
2.1 Color Representation and Stability
High-quality Plastisol Ink should display vivid and stable colors that resist fading even under prolonged exposure to light or harsh environments. Requesting color swatches or sample tests from suppliers allows for a direct assessment of the ink’s color performance.
2.2 Printability and Operational Convenience
Plastisol Ink suitable for screen printing must possess excellent flow properties and viscosity control, ensuring even spread on the screen and minimizing clogging. The ink’s drying speed should be moderate, balancing printing efficiency with the avoidance of defects caused by premature drying. Furthermore, operational convenience, including mixing ratios, stirring methods, and cleaning ease, are also critical considerations.
2.3 Environmental Friendliness and Safety
With heightened environmental awareness, selecting Plastisol Ink that meets international environmental standards is paramount. Ensuring the ink is free from harmful substances like heavy metals and VOCs (Volatile Organic Compounds) protects the health of operators and the environment. Look for ink with RoHS, REACH, or other relevant environmental certifications.
2.4 Cost-Effectiveness
While maintaining quality, managing costs is a priority for every purchaser. Compare prices across different brands and models of Plastisol Ink, considering factors such as shelf life, printing efficiency, and overall cost-benefit. Additionally, assess storage stability, wastage rates, and subsequent maintenance costs.
III. Selection Suggestions for Specific Applications
3.1 Plastisol Ink for Inkjet Printers
While primarily used in screen printing, Plastisol Ink specifically designed for inkjet printers has emerged. These inks retain the properties of Plastisol while optimizing compatibility with inkjet printing, suitable for high-precision pattern printing. Ensure compatibility with your inkjet printer.
3.2 Matching Plastisol Ink with Printing Equipment
Choosing Plastisol Ink requires consideration of its compatibility with existing printing equipment. Different printer models have specific requirements for ink viscosity, drying speed, and other parameters. Ensuring a perfect match between ink and equipment is essential for achieving high-quality prints.
3.3 Post-Processing of Plastisol Ink
Understanding the post-processing techniques required for Plastisol Ink prints, such as curing temperatures and times, is crucial to ensuring print quality. Proper post-processing enhances the durability of printed products and further showcases the ink’s color appeal. Consult suppliers for post-processing recommendations.
3.4 Customized Needs for Plastisol Ink
For specific customer requirements, such as unique colors or effects, customized Plastisol Ink is becoming a trend. Communicate your needs with suppliers to explore customized solutions.
IV. Conclusion
When selecting Plastisol Ink for screen printing, comprehensive consideration of color representation, printability, environmental friendliness, cost-effectiveness, and specific application needs is vital. Through careful comparison and testing, finding the ink that best meets your requirements enhances print quality and lays a solid foundation for your business’s long-term success. Remember, quality ink is the cornerstone of high-quality prints and customer trust.
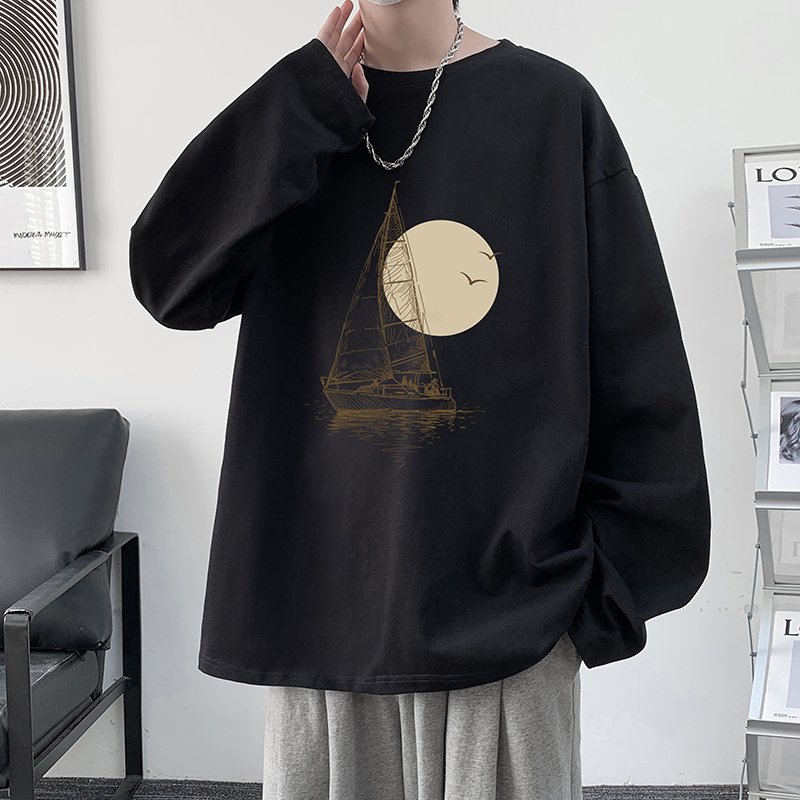