When it comes to screen printing, the versatility and uniqueness of plastisol glow ink have opened up a world of possibilities for designers and artists. With its ability to emit a vibrant glow in the dark, plastisol glow ink has become a popular choice for creating eye-catching graphics and designs. However, one question often arises among those considering this ink: are there any color limitations with plastisol glow ink? In this article, we’ll explore the answer to this question in detail, covering everything from the composition of plastisol glow ink to its compatibility with screen meshes and heat transfer processes.
Understanding the Composition of Plastisol Glow Ink
Before diving into the color limitations of plastisol glow ink, it’s essential to understand its composition. Plastisol glow ink is a type of ink formulated with a plasticizer and pigment dispersion. Unlike other types of inks, plastisol glow ink contains a special phosphorescent pigment that absorbs light during the day and then slowly releases it in the dark, creating a glowing effect. This unique composition allows plastisol glow ink to stand out in a variety of applications, from T-shirts and posters to signs and decorative items.
When it comes to color, plastisol glow ink can be formulated in a range of hues, from bright greens and blues to soft pinks and purples. However, the availability of colors may vary depending on the manufacturer and the specific formulation used.
Compatibility with Screen Meshes
One of the critical factors to consider when using plastisol glow ink is its compatibility with screen meshes. Screen meshes play a vital role in the screen printing process, as they hold the stencil that defines the design being printed. The type of mesh used can affect the flow and coverage of the ink, as well as the final appearance of the printed design.
Plastisol glow ink is generally compatible with standard screen meshes used for plastisol inks. However, it’s essential to choose a mesh with the appropriate thread count and opening size to ensure proper ink coverage and detail in the final print. When using plastisol glow ink, it’s often recommended to use a higher thread count mesh to achieve finer details and smoother ink coverage.
Plastisol Glow Ink Screen Mesh Considerations:
- Choose a mesh with an appropriate thread count for the desired detail level.
- Ensure the mesh openings are large enough to allow proper ink flow.
- Regularly clean and maintain the mesh to prevent clogging and ensure optimal performance.
Using Plastisol Glow Ink in Heat Transfer Processes
In addition to screen printing, plastisol glow ink can also be used in heat transfer processes. Heat transfer printing involves printing an image onto a transfer paper or film, which is then applied to the desired substrate using heat and pressure. This method allows for the creation of custom designs on a variety of materials, including fabrics, plastics, and metals.
When using plastisol glow ink in heat transfer processes, it’s essential to use a compatible transfer paper or film. Some transfer papers are specifically designed for use with plastisol inks, while others may require special handling or adjustments to ensure proper ink transfer and adherence.
Plastisol Glow Ink Heat Transfer Tips:
- Choose a transfer paper or film compatible with plastisol inks.
- Follow the manufacturer’s instructions for applying heat and pressure to ensure proper ink transfer.
- Test the transfer process on a sample substrate before proceeding with the final print.
Thinning Plastisol Glow Ink with Acetone
Like other types of plastisol inks, plastisol glow ink may require thinning to achieve the desired consistency for printing. Thinning the ink can improve its flow through the screen mesh, reduce clogging, and ensure even coverage in the final print.
Acetone is a common solvent used to thin plastisol inks. However, it’s essential to use acetone in moderation, as adding too much can affect the ink’s viscosity, glow properties, and durability. It’s always recommended to start with a small amount of acetone and gradually add more until the desired consistency is achieved.
Thinning Plastisol Glow Ink with Acetone:
- Start with a small amount of acetone and gradually add more as needed.
- Mix the ink thoroughly to ensure even distribution of the solvent.
- Test the thinned ink on a sample print to ensure it meets your requirements.
Ideal Running Temperature for Plastisol Glow Ink
The temperature of the ink during the printing process can affect its performance and final appearance. Plastisol inks, including plastisol glow ink, typically require a specific temperature range to ensure proper curing and adhesion to the substrate.
The ideal running temperature for plastisol glow ink can vary depending on the specific formulation and the type of substrate being printed. However, it’s generally recommended to cure plastisol glow ink at temperatures between 300°F and 320°F (149°C and 160°C). This temperature range ensures that the ink will fully cure and adhere to the substrate without causing damage or distortion.
Tips for Achieving the Ideal Running Temperature:
- Use a temperature-controlled oven or conveyor dryer to maintain a consistent curing temperature.
- Regularly monitor the oven or dryer temperature to ensure it remains within the recommended range.
- Adjust the temperature as needed based on the specific formulation and substrate being used.
Conclusion: No Color Limitations with Plastisol Glow Ink
In conclusion, plastisol glow ink offers a versatile and unique printing option for designers and artists looking to create eye-catching graphics and designs. Despite some concerns about color limitations, plastisol glow ink can be formulated in a range of hues, allowing for endless creative possibilities.
When using plastisol glow ink, it’s essential to consider factors such as compatibility with screen meshes, heat transfer processes, thinning with acetone, and the ideal running temperature. By following best practices and recommendations, designers can achieve vibrant, durable prints with no color limitations.
With its ability to glow in the dark and its compatibility with a range of printing methods and substrates, plastisol glow ink is a valuable addition to any screen printer’s toolkit. Whether you’re creating custom T-shirts, signs, or decorative items, plastisol glow ink can help you bring your designs to life in a way that truly stands out.
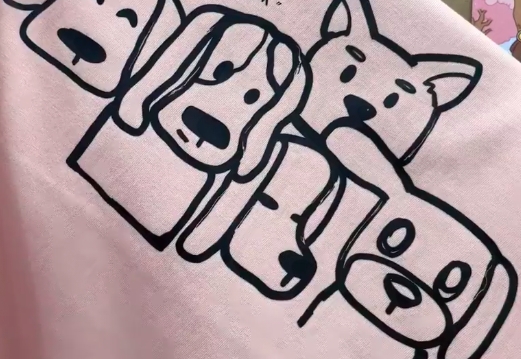