In the realm of screen printing, plastisol puff ink stands out for its ability to create a striking, raised, and three-dimensional (3D) effect on fabrics and other substrates. This unique ink type has revolutionized the industry, offering designers and printers new creative possibilities. But how does plastisol puff ink achieve this remarkable effect? This article delves into the intricacies of plastisol puff ink, exploring its composition, application, and the science behind its signature raised texture. By understanding the process, you can harness the full potential of this versatile ink type to enhance your screen printing projects.
The Basics of Plastisol Puff Ink
Plastisol puff ink is a type of plastisol ink formulated to produce a thick, raised layer once printed and heated. Unlike traditional plastisol inks, which typically result in a flat or slightly textured finish, plastisol puff ink undergoes a unique transformation during the curing process. The secret lies in its formulation and the way it reacts to heat.
Plastisol inks are generally composed of a resin, plasticizers, pigments, and other additives. In the case of plastisol puff ink, the formulation includes specific ingredients that promote the expansion and raising of the ink during curing. This results in the distinctive 3D effect that sets plastisol puff ink apart.
The Curing Process: From Flat to 3D
The transformation of plastisol puff ink from a flat, printed layer to a raised, 3D texture occurs during the curing process. Here’s a step-by-step breakdown of what happens:
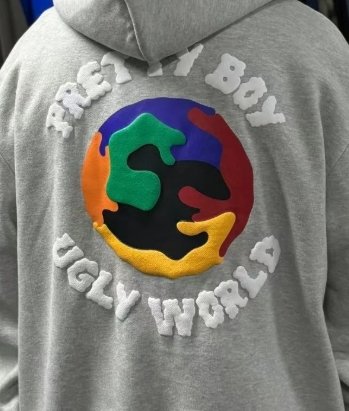
- Printing: The ink is applied to the substrate using a screen printing machine. The thickness of the applied ink layer will determine the ultimate height of the raised effect.
- Drying: After printing, the ink needs to dry partially. This can be done at room temperature or with the assistance of fans or heaters. The drying stage helps to remove excess moisture and prepare the ink for the curing process.
- Curing: The substrate with the printed ink is then subjected to heat, typically in a conveyor dryer or oven. During this stage, the plastisol puff ink undergoes a chemical reaction known as crosslinking. The heat causes the resin particles to soften, expand, and fuse together, forming a strong, cohesive layer.
- Expansion: As the ink cures, it expands and rises above the substrate surface. The unique formulation of plastisol puff ink ensures that this expansion is significant enough to create a noticeable 3D effect.
- Cooling: Once the curing process is complete, the ink cools and solidifies, locking in the raised texture.
Factors Influencing the 3D Effect
Several factors can impact the final appearance and quality of the raised, 3D effect achieved with plastisol puff ink:
- Ink Formulation: The specific ingredients and proportions used in the ink formulation play a crucial role. Different manufacturers may use varying recipes, which can affect the final texture and appearance.
- Printing Technique: The way the ink is applied can also influence the outcome. Factors such as screen mesh count, ink viscosity, and printing pressure can affect the thickness and uniformity of the applied ink layer.
- Curing Conditions: Temperature, dwell time, and conveyor speed in the dryer or oven are critical. Incorrect curing conditions can result in an underdeveloped or overcooked 3D effect.
- Substrate Type: The material being printed on can also affect the final result. Different fabrics and substrates have varying absorption rates and heat tolerance levels, which can impact the ink’s ability to expand and adhere properly.
Handling and Troubleshooting Plastisol Puff Ink
Working with plastisol puff ink can present some unique challenges. Here are some tips for handling and troubleshooting common issues:
- Proper Mixing: Ensure that the ink is thoroughly mixed before use to avoid settling and separation of ingredients.
- Clean Screens: Keep your screens clean and free of debris to prevent clogging and ensure smooth ink flow.
- Storage Conditions: Store plastisol puff ink in a cool, dry place to prevent premature curing and maintain its quality.
- Troubleshooting: If the ink fails to achieve the desired 3D effect, check your curing conditions, ink formulation, and printing technique. Adjust accordingly to optimize the result.
Plastisol Puff Ink vs. Other Ink Types
While plastisol puff ink offers unique advantages, it’s important to consider its suitability for your specific project needs compared to other ink types:
- Plastisol Process Inks: These inks are designed for high-volume production and offer excellent opacity and coverage. However, they typically do not produce a raised effect.
- Plastisol PMS Ink Formula: PMS (Pantone Matching System) inks are formulated to match specific colors accurately. While some PMS ink formulas are available in plastisol versions, they generally do not offer the same raised texture as plastisol puff ink.
- Plastisol Ink Remover: If you need to remove plastisol ink from a substrate, special removers are available. These removers are formulated to break down the ink’s chemical bonds, allowing it to be easily wiped or washed away. Note that plastisol puff ink may require a different remover or removal technique due to its raised texture.
- Plastisol PMS Ink Formula for 9140: Specific PMS ink formulas are designed for use with certain printing machines or processes, such as the 9140 model. Ensure compatibility with your equipment and project requirements when selecting a plastisol PMS ink formula.
Real-World Applications of Plastisol Puff Ink
Plastisol puff ink’s unique raised effect makes it ideal for a wide range of applications, including:
- Apparel and Textiles: Create eye-catching graphics and designs on T-shirts, hoodies, and other fabrics.
- Signage and Banners: Add depth and dimension to promotional materials and signage.
- Product Decoration: Enhance the visual appeal of toys, phone cases, and other products with raised textures.
- Custom Artwork: Create unique, one-of-a-kind pieces with a striking 3D effect.
Conclusion
Plastisol puff ink’s ability to achieve a unique raised, 3D effect makes it a standout choice for screen printers and designers. By understanding the formulation, curing process, and factors influencing the final texture, you can harness the full potential of this versatile ink type. Whether you’re working on a small-scale custom project or a high-volume production run, plastisol puff ink offers endless creative possibilities. With its distinctive appearance and durability, it’s no wonder that plastisol puff ink is a favorite among professionals in the screen printing industry.