Using white plastisol ink on black t shirts is a go-to method for creating high-contrast, durable designs with a professional finish. The process requires a combination of the right materials, techniques, and tools to ensure crisp, vibrant results. Whether you’re crafting heat transfers for personal projects or commercial orders, this guide will walk you through the essentials, from preparing the transfer paper to mastering the heat press process.
THE TRANSFER PAPER
Transfer paper is the foundation of any successful heat transfer project. It acts as the medium for the ink and facilitates a smooth transfer onto the black t-shirt.
1. Choosing the Right Transfer Paper
- Hot Peel Transfer Paper: Provides a glossy finish and quick application.
- Cold Peel Transfer Paper: Offers a matte, durable finish, perfect for white plastisol ink on black t shirts.
Cold peel paper is preferred for its ability to create clean and long-lasting designs.
2. Preparing the Paper for Use
- Cut the transfer paper to fit your design.
- Secure it firmly onto the printing surface to prevent shifting during application.
Transfer paper ensures the ink adheres properly to the t-shirt, minimizing issues like the white plastisol ink crocking problem.
LEARN HOW TO SCREEN PRINT MULTI-COLOR PLASTISOL HEAT TRANSFERS
Adding multiple colors to your heat transfers involves precision and technique. However, the key to success is establishing a solid white underbase.
1. The Importance of a White Underbase
Printing a white underbase ensures that additional colors remain vibrant on the black fabric. Without it, colors can appear muted or uneven.
2. Aligning Colors with Registration Marks
- Use registration marks to align multiple screens accurately.
- Begin with the white underbase, followed by additional colors.
3. Layering Inks
Each layer of ink should be gel-cured (partially dried) before applying the next. This step prevents smudging and ensures clean, precise designs.
By mastering multi-color heat transfers, you can elevate your designs beyond simple white prints.
PRINTING
Printing is the core step where white plastisol ink is applied to the transfer paper. This stage requires careful handling to avoid issues like white plastisol ink cracking or uneven coverage.
1. Selecting High-Quality Ink
Choose high-opacity ink designed for dark fabrics. You can find reliable options like white plastisol ink for sale on platforms such as Amazon, which offer professional-grade inks for consistent results.
2. Applying the Ink
- Use a squeegee at a consistent angle and pressure to spread the ink evenly across the screen.
- Focus on achieving a smooth, even layer, especially for the white underbase.
3. Troubleshooting Common Problems
- Cracking Issues: Ensure the ink is properly cured to avoid cracking after application.
- Crocking Problems: Minimize crocking (ink transferring to other surfaces) by using the correct adhesion powder and curing techniques.
Printing correctly sets the stage for a flawless transfer to the black t-shirt.
LEARN HOW TO CHOOSE THE RIGHT MESH COUNT FOR THE JOB
The mesh count of your screen determines the level of detail and ink deposit in your design.
1. Understanding Mesh Counts
- Low Mesh Counts (110-160): Ideal for bold designs requiring heavy ink deposits, such as the white underbase for black t-shirts.
- High Mesh Counts (200-305): Best for fine details and multi-color prints.
2. Choosing the Best Mesh for White Plastisol Ink
For white plastisol ink on black t shirts, a mesh count of 110-156 is recommended for the underbase to ensure full opacity.
3. Testing for Best Results
Perform test prints to determine if your chosen mesh count provides adequate ink coverage and captures the desired level of detail.
Selecting the correct mesh count is critical to creating vibrant, high-quality transfers.
THE ADHESION POWDER
Adhesion powder is a vital step in creating heat transfers, as it helps the plastisol ink bond effectively to the t-shirt fabric.
1. Applying the Powder
After printing your design onto the transfer paper, apply a fine layer of adhesion powder over the wet ink.
- Gently shake off excess powder to avoid uneven application.
2. Benefits of Adhesion Powder
- Enhances ink adhesion to the fabric.
- Reduces the risk of peeling or lifting after heat pressing.
3. Curing the Powder
Partially cure (gel) the ink with the powder applied. This step ensures that the powder melts into the ink for a strong bond.
Using adhesion powder effectively ensures your designs will last, even after multiple washes.
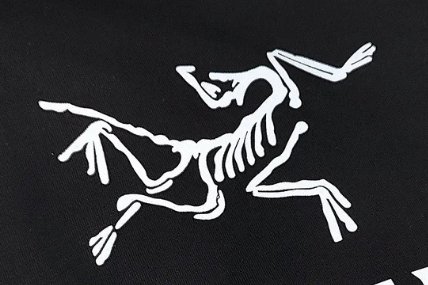
GELLING THE INK
Gelling is the process of partially curing the plastisol ink to prepare it for transfer. This step is crucial to avoid smudging or improper adhesion during heat pressing.
1. Partial Curing
Use a flash dryer or conveyor dryer to heat the ink until it reaches a gel-like consistency. This typically occurs at temperatures between 180-240°F.
2. Avoid Overcuring
Do not fully cure the ink at this stage, as this will make it impossible to transfer onto the t-shirt.
3. Testing the Gelled Ink
The ink should be dry to the touch but not fully set. Conduct a quick test to ensure the ink transfers cleanly.
Proper gelling is essential for achieving a smooth, professional transfer.
HEAT PRESSING
The heat pressing stage brings your design to life, transferring the ink from the paper to the black t-shirt.
1. Preparing the T-Shirt
- Preheat the t-shirt using the heat press to remove moisture and wrinkles.
- Position the transfer paper ink-side down on the desired location.
2. Pressing the Design
Set the heat press to the recommended temperature and time for white plastisol ink on black t shirts (typically 320°F for 10-15 seconds).
3. Removing the Transfer Paper
- For hot peel paper, remove immediately after pressing.
- For cold peel paper, allow the design to cool before peeling.
Heat pressing finalizes the transfer process, ensuring the ink adheres firmly to the fabric.
LEARN WHY A HEAT PRESS IS EVERY PRINTER’S SECRET TOOL
A heat press is an indispensable tool for screen printers, offering precision and consistency that other methods can’t match.
1. Benefits of a Heat Press
- Ensures even heat and pressure for flawless transfers.
- Reduces the risk of errors, such as uneven adhesion or incomplete curing.
2. Choosing the Right Heat Press
- Clamshell Press: Compact and easy to use.
- Swing-Away Press: Provides more space and flexibility for larger designs.
3. Maintenance and Care
Regularly clean the heat press platen to prevent ink residue from transferring onto t-shirts.
A quality heat press is a worthwhile investment for creating professional-grade heat transfers with white plastisol ink on black t shirts.
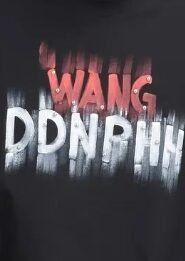
Conclusion
Creating custom heat transfers with white plastisol ink on black t shirts involves careful preparation, precise execution, and attention to detail. By following these steps—choosing the right transfer paper, mastering printing techniques, and using a heat press effectively—you can achieve durable, high-contrast designs that stand out on dark fabrics.
Addressing common issues like white plastisol ink cracking or crocking problems ensures long-lasting, professional-quality results. With practice and the right tools, you’ll master the art of creating custom heat transfers that elevate your screen printing projects.