If you’ve ever stared at a perfectly crisp white brand on a black blouse and puzzled, “How on the earth do display printers pull that off?”—you’re within the proper area. This manual will plunge deep into the world of white plastisol ink: what makes it vital for screen print, why getting that glacier white pop is trickier than you suspect, and tips on blending, printing, and curing for satisfactory results. Whether you’re a seasoned pro or just dipping your feet into plastisol display printing, you’ll find solutions to the hardest questions about ink, bleed, temperature, and greater. Dive in and discover a way to create bolder, brighter prints on any cloth—such as cussed cotton and polyester blends!
جدول المحتويات
1. What Makes حبر بلاستيسول أبيض Special in Screen Printing?
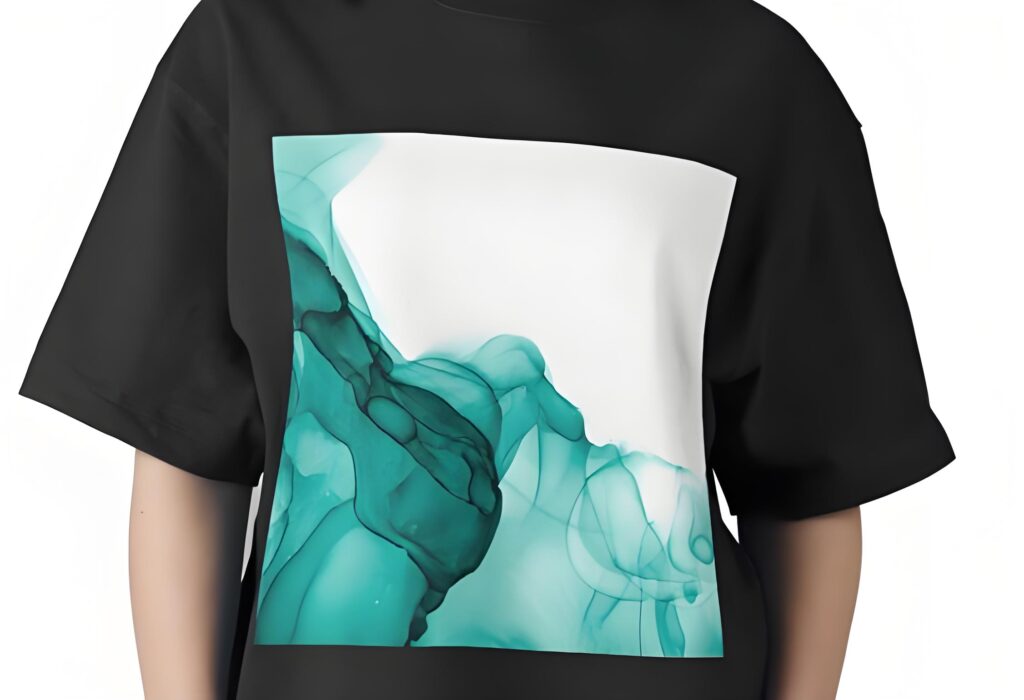
White plastisol ink is the unsung hero in the back of nearly every formidable layout you notice on a dark blouse. Unlike water-based ink, plastisol doesn’t dry by using evaporation; it without a doubt healing procedures whilst heated, forming a robust, flexible layer that sits on top of the cloth. For display printers aiming for a glacier white print, this indicates your ink needs simply the proper stability of opacity and smoothness.
Screen printers believe white plastisol ink because of its creamy consistency and excessive opacity. It stands up superbly on each cotton and polyester, making it a favorite for tough garments.
2. How Does Plastisol Ink Work on Fabric?
Plastisol ink doesn’t soak into the cloth’s fiber like a few screen printing ink; as an alternative, it stays close to the floor, turning in that ambitious, vibrant appearance. The chemistry of plastisol entails vinyl resin and plasticizer, which stay liquid until they hit their cure temperature—normally around 320°F (a hundred and sixty°C).This method plastisol inks are incredibly flexible and forgiving during printing. They won’t dry in the screen, so you get lots of press time and no clogged mesh. However, attaining clean, shiny results requires attention on your print setup—select the right mesh remember, preserve a fair squeegee stress, and ensure you’re flashing and curing successfully for each cotton and poly shirts.
3. What’s the Difference Between Opaque and Regular White Ink?
Not all white inks are created same. Opaque white plastisol ink is purposely formulated to be more thick and filled with pigment. If you’re trying to print white ink onto a black or deep-coloured shirt, excessive opacity is vital to hold historical past hues from showing via.
In comparison, normal white plastisol ink may be softer but can appear slightly translucent on darker fabric. For the brightest white display screen prints, display printers frequently attain for “excessive opacity,” “premium,” or “nice white” formulas from manufacturers like Wilflex and International Coatings. The right desire relies upon to your garment, favored hand feel, and the complexity of your printing tasks.
4. The Best White Plastisol Ink Options: How Do You Pick?
With dozens of alternatives available on the market, selecting the great white ink can sense overwhelming. To make your decision, think about fabric type (cotton, poly, or mixture), the demanding situations of bleed, your press setup, and your store’s workflow.
For all-motive prints on cotton shirts, many printers start with “normal” or mid-tier opaque options. Polyester and blends demand low bleed plastisol ink with excessive bleed resistance. Gallon sizes make feel for big print runs; don’t forget quick flash or low therapy white inks for temperature-sensitive garments. Leading choices like Wilflex Poly White and Glacier White offer depended on overall performance and colourful shade on even the boldest fabric.
5.How to Mix White Plastisol Ink for Maximum Opacity?
Mixing could make or wreck your final print. For high opacity, constantly stir your ink very well before loading it onto the display screen. This guarantees pigment dispersion and gives you buttery, creamy consistency for a clean surface.
In contrast, regular white plastisol ink may be softer but can appear slightly translucent on darker fabrics. For the brightest white screen prints, screen printers often reach for “high opacity,” “premium,” or “best white” formulas from brands like Wilflex and International Coatings. The right choice depends on your garment, desired hand feel, and the complexity of your printing projects.
Advanced screen printers sometimes create “ink mixing systems,” blending different types of white plastisol ink for a custom balance of opacity, body, and bleed resistance. Just remember: adjusting your mix too much can impact cure temperature and ink performance. Conduct swatch tests on the actual fabric before launching into big printing projects to guarantee you’ll get the glacier white, bright finish you crave.
6. Beating Dye Migration and Bleed: Tips for Cotton, Poly, and Blends
If you’re printing on polyester or blends, dye migration is the ghost haunting each shop. This method the garment’s dye can creep via your stunning white plastisol ink, turning it purple or gray. The trick? Use low bleed or poly white ink in particular formulated for polyester and blends.
Pre-test your print with the aid of flashing and absolutely curing on leftover cloth. If you notice dye migration, transfer to a top class low bleed or non-phthalate plastisol ink. Keeping your remedy temperature as low as viable—and watching live time in the dryer—enables keep shades formidable.
7. Perfecting Your Underbase: Does the “Best White” Exist?
In complicated display print jobs, an underbase is your mystery weapon—particularly on darkish fabric. Use a layer of white plastisol ink as your foundation. The underbase need to be easy and opaque, giving subsequent color layers a impartial, vibrant “canvas.”
But is there really a “best white” for each printer? It relies upon on your mesh, press speed, and material kind. Wilflex Glacier White and International Coatings Ultra White are crowd favorites for their creamy sense and constant effects. The pleasant white is the only that fits your workflow and gives each opacity and clean printability.8. How to Cure Plastisol for Lasting, Bright Prints
Getting the therapy right is critical whilst working with plastisol ink. If you underneath-cure, the ink will crack and wash out. Over-treatment, and the ink can flip brittle or even yellow, killing your glacier white.
Cure plastisol consistent with the producer’s endorsed temperature—often round 320°F. Don’t trust your conveyor dryer blindly; always check with a laser thermometer or donut probe to make certain the ink movie, now not simply the air, hits remedy temp. For top class outcomes, take note of both reside time and consistent dryer settings.
8. Quick Flash, Dwell Time, and Flash Temperature: What Matters for White Ink?
White plastisol ink often desires a “quick flash” among layers to lock in opacity and save you colour blending or bleed. A speedy flash dries the ink’s surface (no longer fully therapies) so you can print a couple of shades or build a thicker underbase.
Ideal flash temperature is just excessive enough to gel the ink—normally 220°F to 250°F on cotton, slightly decrease for poly to limit dye migration. Too plenty live time dangers sizzling your cloth or inflicting bleed. Exceeding the right temp can undermine your formidable, opaque print through making the ink rubbery or much less bendy.
9. Pro Tools, Brands, and Mixing Systems for Screen Printers
Mastering white plastisol ink calls for dependable equipment: excessive-anxiety mesh screens, sharp squeegees, and precise presses. Investing in quality gallon containers of screen printing ink ensures consistency, even as set up brands like Wilflex offer time-examined formulation with excessive opacity and occasional bleed.
A strong ink blending machine—whether or not keep-bought or homemade—helps you to formulate custom sunglasses for premium printing projects, and batch mixing ensures each print is simply as ambitious and brilliant as the final. Top printers preserve detailed notes on mixes, temperature, and press setups to troubleshoot any troubles and continually refine their device[2]Bullet Point Summary: The Key Takeaways
White plastisol ink is the usual for formidable, vibrant display screen prints—specifically on darkish clothes.
- Their creamy consistency, flexibility, and opacity cause them to ideal for cotton, polyester, and blends.
- Opaque, premium, or “first-class white” formulas—like Wilflex and International Coatings options—offer maximal insurance and color brilliance.
- Always mix your white plastisol ink thoroughly to maximize opacity and a clean print floor.
- Beat dye migration with low bleed and poly white ink, and maintain your remedy temperature as little as possible on poly fabrics.
- Use a solid white underbase to make colours pop on complicated, multi-layer display prints.
- Watch your cure: too little or an excessive amount of warmth will destroy the print. Target 320°F and take a look at with a thermometer for accuracy.
- Flash among layers simply enough to gel the ink floor, however don’t overdo the dwell time.
- Invest in outstanding display screen, press, and ink blending structures for steady, professional results each time.
- Document your method—together with ink blending ratios, temperature, and garment notes—for repeatable, top class great in every job.
That’s it—your crash route in studying white plastisol ink for display screen print. Whether you’re chasing the brightest glacier white or truely seeking to beat those complex material challenges, those guidelines will set you up for fulfillment with each press of the squeegee.
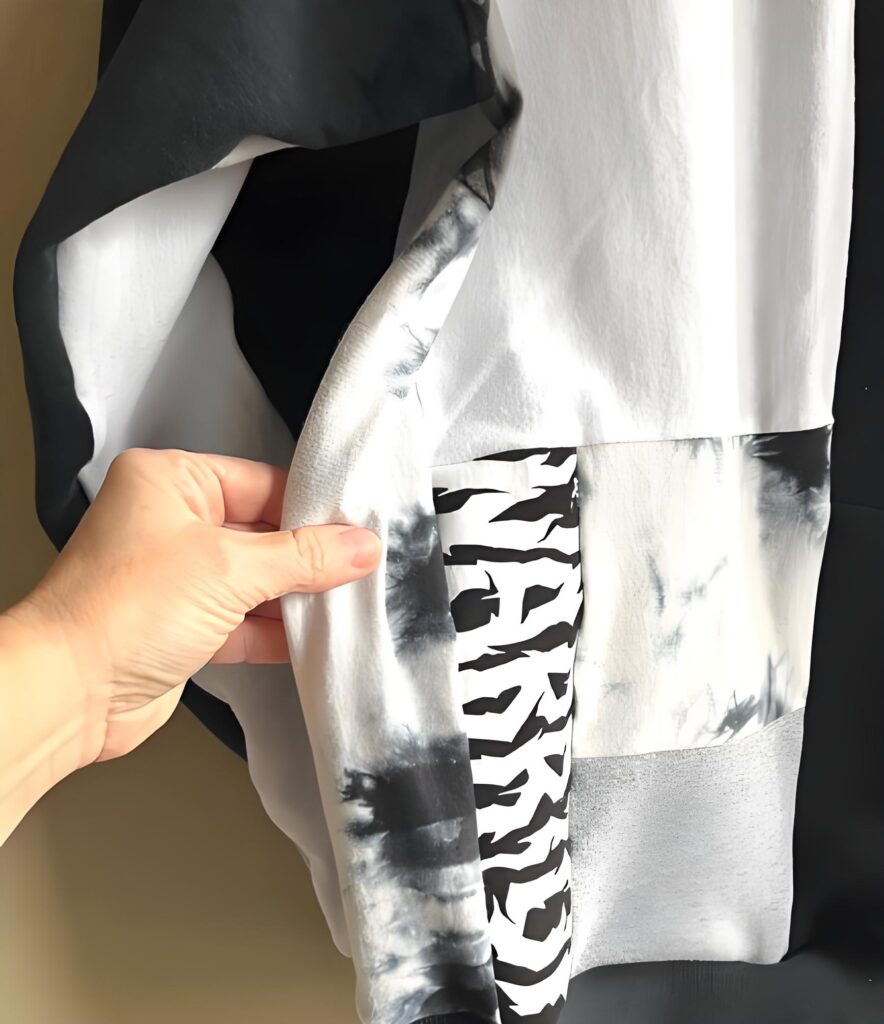