Βασικά Συμπεράσματα: Τα πιο σημαντικά πράγματα που πρέπει να θυμάστε
- Χρησιμοποιήστε φωσφορίζον μελάνι ή φωσφορίζον μελάνι πλαστιζόλης για μέγιστη ζωντάνια και ελκυστικές εκτυπώσεις.
- Να χρησιμοποιείτε πάντα μια αδιαφανή βάση από κάτω (συνήθως λευκή) όταν εκτυπώνετε σε σκούρα ρούχα για να βοηθήσετε στην ανάδειξη των φθοριζόντων χρωμάτων.
- Επιλέξτε το μελάνι σας για εκτύπωση οθόνης με βάση αποκλειστικά τον τύπο υφάσματος - βαμβάκι, πολυεστέρας, λινό, νάιλον ή ρεγιόν.
- Τα φθορίζοντα κίτρινα, πράσινα, ροζ, μπλε και πορτοκαλί χρώματα προσφέρουν τα πιο φωτεινά αποτελέσματα, ειδικά κάτω από υπεριώδη ακτινοβολία ή μαύρο φως.
- Σκληρύνετε το μελάνι πλαστιζόλης στη συνιστώμενη θερμοκρασία για βέλτιστη ανθεκτικότητα και αντοχή στο πλύσιμο.
- Μάρκες όπως το Speedball παρέχουν αξιόπιστα, πολύχρωμα και καθαρά στη χρήση μελάνια εκτύπωσης οθόνης.
- Ισορροπήστε το λείο χέρι και την αδιαφάνεια χρησιμοποιώντας τον σωστό αριθμό ματιών και τεχνικές αραίωσης για άνετες, φορετές εκτυπώσεις.
- Πραγματοποιείτε τακτικούς ελέγχους σχετικά με την κάλυψη, την ανθεκτικότητα στο πλύσιμο και τη ζωντάνια πριν από την πλήρη παραγωγή.
- Παρακολουθήστε για προβλήματα με τη μετανάστευση χρωστικής κατά την εκτύπωση σε πολυεστέρα ή μείγματα.
- Αποφύγετε τα συνηθισμένα λάθη προετοιμάζοντας σωστά τις οθόνες και ακολουθώντας όλες τις συμβουλές σκλήρυνσης και χρήσης μελανιού.
Με τις σωστές επιλογές μελανιού και τεχνικές, τα έργα φθορίζουσας μεταξοτυπίας σας μπορούν να επιτύχουν επαγγελματικά, εντυπωσιακά αποτελέσματα κάθε φορά!
Το φθορίζον μελάνι φέρνει επανάσταση στον κόσμο της μεταξοτυπίας, κάνοντας τις εκτυπώσεις πιο ζωντανές και ελκυστικές από ποτέ. Είτε παράγετε εντυπωσιακά μπλουζάκια, αφίσες νέον είτε πινακίδες υψηλής ορατότητας, η εξειδίκευση στο φθορίζον μελάνι και το μελάνι πλαστιζόλης είναι ζωτικής σημασίας για κάθε μεταξοτυπία που θέλει να προσφέρει έντονα, μακράς διαρκείας αποτελέσματα. Σε αυτήν την περιεκτική ανάρτηση ιστολογίου, θα ανακαλύψετε όλα όσα πρέπει να γνωρίζετε για τη φθορίζουσα μεταξοτυπία, από την επιλογή μελανιού έως τη σκλήρυνση και πώς να επιτύχετε ασυναγώνιστη ζωντάνια χρωμάτων, κάλυψη και απαλό χέρι σε μια σειρά υφασμάτων. Μείνετε μαζί μας για να διασφαλίσετε ότι το επόμενο έργο εκτύπωσης θα ξεχωρίσει!
Περίγραμμα άρθρου
- Τι κάνει το φθορίζον μελάνι τόσο ξεχωριστό στην εκτύπωση μεταξοτυπίας;
- Πώς συγκρίνεται το μελάνι Plastisol με τα μελάνια με βάση το νερό και τα φθορίζοντα μελάνια;
- Φθορίζον κίτρινο, πράσινο, ροζ και μπλε: Πώς αποδίδουν οι νέον αποχρώσεις;
- Επιλογή του σωστού μελανιού για μεταξοτυπία: Συμβουλές και κόλπα
- Η σημασία της αδιαφάνειας και της κάλυψης μελανιού για φωτεινές εκτυπώσεις
- Βέλτιστες πρακτικές για τη σκλήρυνση μελανιού Plastisol και φθοριζόντων μελανιών
- Speedball και άλλες κορυφαίες μάρκες: Ποια μελάνια ξεχωρίζουν;
- Πώς να πετύχετε απαλά και αδιαφανή αποτελέσματα με φθορίζον μελάνι πλαστισόλης
- Φθορίζουσα Μεταξοτυπία σε Βαμβάκι, Πολυεστέρα και Άλλα Υφάσματα
- Συνηθισμένα λάθη που πρέπει να αποφεύγετε με τη μεταξοτυπία με φθορίζον μελάνι
1. Τι κάνει το φθορίζον μελάνι τόσο ξεχωριστό στην εκτύπωση μεταξοτυπίας;
Το φθορίζον μελάνι έχει σχεδιαστεί για να κάνει τα σχέδια εκτύπωσης να ξεχωρίζουν πραγματικά, είτε σε μπλουζάκια, αφίσες είτε σε υφασμάτινα πανό. Αυτά τα μελάνια χρησιμοποιούν ειδικές φόρμουλες βαφής για να αντανακλούν το μαύρο και το υπεριώδες φως, δημιουργώντας ένα λαμπερό εφέ που δεν περνάει απαρατήρητο. Το φθορίζον μελάνι μεταξοτυπίας είναι ιδανικό για μπλουζάκια και ρούχα που προορίζονται να ξεχωρίζουν, ειδικά για εκδηλώσεις, αθλητικές ομάδες ή προωθητικές ενέργειες που απαιτούν υψηλή ορατότητα.
Σε σύγκριση με το τυπικό μελάνι μεταξοτυπίας, το φθορίζον μελάνι προσφέρει μια απαράμιλλη ζωντάνια στις εκτυπώσεις. Η μοναδική του σύνθεση συχνά περιλαμβάνει φωτεινότερες χρωστικές ουσίες που δίνουν στις εκτυπώσεις μια «νέον» εμφάνιση, και ακόμη και υπό κανονικό φωτισμό, αυτά τα χρώματα φαίνονται πιο έντονα και κορεσμένα. Αυτό καθιστά το φθορίζον μελάνι ιδανικό για σχέδια όπου απαιτείται υψηλή οπτική επίδραση και ζωντάνια χρωμάτων.
Εκτός από την εμφάνισή του, το φθορίζον μελάνι χρησιμοποιείται συχνά σε τεχνικές ανάμειξης για τη δημιουργία προσαρμοσμένων αποχρώσεων ή εφέ διαβάθμισης. Οι εκτυπωτές οθόνης εκτιμούν την ευελιξία του τόσο σε χειροκίνητες όσο και σε αυτόματες διαμορφώσεις, καθιστώντας το βασικό στοιχείο των σύγχρονων προμηθειών μεταξοτυπίας.
2. Πώς συγκρίνεται το μελάνι Plastisol με τα μελάνια με βάση το νερό και τα φθορίζοντα μελάνια;
Το μελάνι Plastisol είναι ένα από τα αγαπημένα μεταξύ των μεταξοτυπικών εκτυπωτών για την κρεμώδη υφή του, την εξαιρετική κάλυψη, την ανθεκτικότητα και το χρονικό περιθώριο σκλήρυνσης που επιτρέπει την εύκολη σκλήρυνση. Το μελάνι Plastisol, που έχει σχεδιαστεί ειδικά για μεταξοτυπία, βασίζεται στο PVC και κάθεται πάνω από τις ίνες του υφάσματος αντί να απορροφάται, πράγμα που σημαίνει ότι μπορεί να προσφέρει εξαιρετική αδιαφάνεια, ειδικά σε σκούρα ρούχα ή μαύρα πουκάμισα.
Συγκριτικά, τα μελάνια με βάση το νερό προσφέρουν μια απαλή αίσθηση στο χέρι (μαλακό χέρι) και είναι ιδανικά για vintage ή ελαφριά μπλουζάκια, αλλά μπορεί να δυσκολεύονται να φτάσουν τη ζωντάνια και την κάλυψη του μελανιού πλαστιζόλης - ειδικά κατά την εκτύπωση με φθορίζοντα χρώματα. Το φθορίζον μελάνι με βάση το νερό είναι κατάλληλο για ανοιχτόχρωμα υφάσματα ή όταν επιθυμείται ένα απαλό, αναπνεύσιμο φινίρισμα, αλλά μπορεί να μην έχει την έντονη ζωντάνια στα σκούρα ρούχα.
Το φθορίζον μελάνι πλαστισόλης συνδυάζει πολλά πλεονεκτήματα: τη ζωντάνια των φθοριζόντων χρωμάτων, τις πιο παχύρρευστες και αδιαφανείς ιδιότητες του πλαστισόλης και την ανθεκτικότητα σε πολλαπλά πλυσίματα. Όταν συνδυάζεται με το σωστό πλέγμα και γαλάκτωμα, προσφέρει εκτυπώσεις που είναι ζωντανές και μακράς διαρκείας. Για έργα μεταξοτυπίας που απαιτούν τόσο χρώμα όσο και ανθεκτικότητα, το μελάνι πλαστισόλης (συμπεριλαμβανομένων των επιλογών φθορίζοντος μελανιού) είναι συχνά η πρώτη επιλογή.
3. Φθορίζον κίτρινο, πράσινο, ροζ και μπλε: Πώς αποδίδουν οι νέον αποχρώσεις;
Το φθορίζον κίτρινο, το φθορίζον πράσινο, το φθορίζον κόκκινο και το φθορίζον μπλε είναι μερικές από τις πιο δημοφιλείς αποχρώσεις στην μεταξοτυπία. Κάθε μία από αυτές προσδίδει μια υπέροχη «φωτεινότητα» και μπορεί να χρησιμοποιηθεί ως κύριο χρώμα ή σε συνδυασμό για πολύχρωμες, δυναμικές εκτυπώσεις. Για παράδειγμα, το φθορίζον κίτρινο είναι ιδιαίτερα έντονο σε σκούρα ρούχα, ενώ το φθορίζον πορφυρό και το φθορίζον πράσινο υπερέχουν για σχέδια για διαγωνισμούς ή streetwear.
Αυτά τα νέον γυαλιά ηλίου έχουν σχεδιαστεί για μέγιστη αντανάκλαση του φωτός, βελτιώνοντας τη ζωντάνια κάτω από τα συνηθισμένα και τα UV φωτιστικά. Για καλύτερα αποτελέσματα, εκτυπώστε αυτά τα μελάνια σε λευκά ή ανοιχτόχρωμα στρώματα κάτω από τη βάση για να βεβαιωθείτε ότι τα χρώματά τους παραμένουν ζωντανά. Η άμεση εφαρμογή φθορίζοντος μπλε σε σκούρα πουκάμισα χωρίς αδιαφανή βάση μπορεί επίσης να μειώσει τη ζωντάνια, επειδή τα φθορίζοντα μελάνια μπορεί μερικές φορές να είναι μόλις ορατά.
Τα συστατικά του φθορίζοντος μελανιού συχνά υπαγορεύουν την ασφάλεια και την αδιαφάνειά του. Ορισμένες μάρκες δημιουργούν παχύτερες, αδιαφανείς παραλλαγές των γυαλιών ηλίου νέον, ειδικά για εκτύπωση σε δύσκολα υφάσματα ή σκούρα ρούχα. Η κατανόηση του τρόπου με τον οποίο λειτουργεί κάθε χρώμα - και του εάν απαιτείται μια βάση από κάτω ή ένα μοναδικό γαλάκτωμα - θα βοηθήσει τους εκτυπωτές οθόνης να επιτύχουν σταθερά, αξιοσημείωτα αποτελέσματα.
4. Επιλογή του σωστού μελανιού για μεταξοτυπία: Συμβουλές και κόλπα
Δεν είναι όλα τα μελάνια εκτύπωσης ίδια και η επιλογή του κατάλληλου μελανιού για την συγκεκριμένη επιχείρησή σας εξαρτάται από πολλούς παράγοντες. Λάβετε υπόψη τον τύπο του υφάσματος - όπως βαμβάκι, πολυεστέρα, νάιλον, λινό ή ρεγιόν - καθώς τα διαφορετικά μελάνια προσκολλώνται και επεξεργάζονται σε εξαιρετικές τιμές. Για παράδειγμα, το μελάνι πλαστιζόλης μπορεί να είναι πολύ κατάλληλο για βαμβάκι και μείγματα, ωστόσο μπορεί να απαιτεί εξαρτήματα για πολυεστέρα 100% λόγω πιθανής μετανάστευσης χρωστικών.
Η τεχνική λογισμικού (χειροκίνητη ή ηλεκτρονική), η χρήση πλέγματος στην οθόνη σας και τα επιθυμητά χαρακτηριστικά μελανιού (όπως απαλό χέρι, αδιαφάνεια ή ασφάλεια) μπορεί επίσης να επηρεάσουν την προτίμησή σας. Τα μελάνια με βάση το νερό μπορεί να είναι ιδανικά για ελαφριά, αναπνεύσιμα μπλουζάκια, ενώ το μελάνι πλαστιζόλης είναι καλύτερο για ανθεκτικές, ζωντανές εκτυπώσεις σε ένα πολύ ευρύτερο φάσμα τύπων ενδυμάτων.
Πάντα να δοκιμάζετε ένα σετ μελανιών πριν ξεκινήσετε μια μαζική παραγωγή. Είναι σημαντικό να ελέγχετε πώς το φθορίζον μελάνι ή το κίτρινο πλαστιζόλ σας επεξεργάζεται, πλένεται και φαίνεται κάτω από μοναδικά φωτιστικά. Η κατοχή εξαιρετικών εξαρτημάτων μεταξοτυπίας, συμπεριλαμβανομένου αξιόπιστου μελανιού για μεταξοτυπία και κατάλληλου γαλακτώματος, θα σας προετοιμάσει για την επιτυχία.
5. Η σημασία της αδιαφάνειας και της κάλυψης μελανιού για φωτεινές εκτυπώσεις
Η αδιαφάνεια αναφέρεται στο πόσο καλά καλύπτει το μελάνι το ύφασμα ή τα προηγούμενα στρώματα μελανιού, κάτι που είναι ιδιαίτερα σημαντικό κατά την εκτύπωση με φθορίζοντα χρώματα σε σκούρα ρούχα. Η ανεπαρκής αδιαφάνεια μπορεί να προκαλέσει θαμπές, ξεθωριασμένες εκτυπώσεις που δεν δημιουργούν αποτέλεσμα - ένα κύριο πρόβλημα για την εκτύπωση με φθορίζουσα οθόνη.
Τα πιο παχιά μελάνια και αυτά που έχουν σχεδιαστεί ειδικά για «αδιαφανή» κάλυψη είναι κρίσιμα όταν εργάζεστε με πολύχρωμα γυαλιά ηλίου όπως το φωσφορίζον κίτρινο ή το φωσφορίζον πορτοκαλί. Ορισμένες τεχνικές περιλαμβάνουν την εκτύπωση μιας αδιαφανούς λευκής βάσης πριν από τη χρήση φωσφορίζοντος μελανιού. Αυτή η τεχνική βοηθά τις νέον αποχρώσεις να διατηρούν τη φωτεινότητά τους και διασφαλίζει ότι η εκτύπωση ξεχωρίζει, ακόμα και σε μαύρα πουκάμισα ή σκούρα ρούχα.
Πρέπει να μετρηθεί το σωστό πλέγμα οθόνης (συνήθως 100-156 για μελάνι φθορισμού πλαστιζόλης) αναμεμειγμένο με τη σωστή τάση οθόνης και ένα κατάλληλο στρώμα γαλακτώματος μπορεί να αυξήσει σημαντικά την αδιαφάνεια. Πάντα να πειραματίζεστε με τις αναλογίες ανάμειξης σε περίπτωση που θέλετε να δημιουργήσετε προσαρμοσμένα νέον σκιάδια ηλίου, βεβαιώνοντας ότι το τελευταίο μελάνι λειτουργεί καλά για την επιλεγμένη σας χρήση.
6. Βέλτιστες πρακτικές για τη σκλήρυνση μελανιού πλαστισόλης και Φθορίζοντα μελάνια
Η σκλήρυνση είναι ο τρόπος με τον οποίο το μελάνι πλαστισόλης στερεοποιείται και γίνεται μόνιμο στο ένδυμα. Το σωστά σκληρυμένο μελάνι προσφέρει εξαιρετική αντοχή στο πλύσιμο, ανθεκτικότητα και διατηρεί τη ζωντάνια του με την πάροδο των ετών. Το μελάνι πλαστισόλης συνήθως επεξεργάζεται σε θερμοκρασία περίπου 320°F (160°C), αλλά φροντίστε να ελέγξετε τις συμβουλές του κατασκευαστή, ειδικά για τις παραλλαγές φθορίζουσας μελάνης, καθώς μερικές μπορεί επίσης να απαιτούν ελάχιστα ειδικές θερμοκρασίες σκλήρυνσης.
Εάν το μελάνι δεν σκληρυνθεί για αρκετό χρονικό διάστημα ή σε αρκετά υψηλή θερμοκρασία, οι εκτυπώσεις ενδέχεται επίσης να ραγίσουν, να ξεθωριάσουν ή να ξεθωριάσουν εκ των προτέρων. Από την άλλη πλευρά, η υπερθέρμανση μπορεί να κάψει το ύφασμα ή να υποβαθμίσει το μελάνι, επηρεάζοντας τόσο την εμπειρία όσο και την ανθεκτικότητα. Για τα ηλεκτρονικά καταστήματα, η διατήρηση σταθερών στροφών ιμάντα και σωστών ζωνών θερμότητας είναι το κλειδί. Για χειροκίνητες ρυθμίσεις, χρησιμοποιήστε ένα θερμόμετρο λέιζερ για να ελέγξετε ότι το μελάνι πλαστισόλης για την οθόνη φτάνει στην κατάλληλη θερμοκρασία καθαρισμού.
Πραγματοποιήστε έλεγχο τάνυσης και πλύση στην ολοκληρωμένη σας εκτύπωση για να βεβαιωθείτε ότι το μελάνι έχει σκληρυνθεί σωστά. Εάν η εκτύπωση ραγίσει ή ξεπλυθεί, επανεξετάστε τη διαδικασία σκλήρυνσης. Τα μελάνια φθορισμού για την εκτύπωση οθόνης μπορεί επίσης να φαίνονται σκληρυμένα στο πάτωμα, αλλά να είστε απαλά από κάτω, γι' αυτό ελέγχετε πάντα τα αποτελέσματα κάθε αγγίγματος και πλύσης.
7. Speedball και άλλες κορυφαίες μάρκες: Ποια μελάνια ξεχωρίζουν;
Η Speedball είναι ένα από τα πιο γνωστά ονόματα στα είδη μεταξοτυπίας, προσφέροντας μια γκάμα μελανιών, όπως τυπικά μελάνια με βάση το νερό, μελάνια πλαστιζόλης και φθορίζοντα μελάνια για μεταξοτυπία. Τα μελάνια τους είναι κατάλληλα τόσο για αρχάριους όσο και για έμπειρους εκτυπωτές μεταξοτυπίας, γνωστά για τη συνοχή, τη ζωντάνια και την ευκολία χρήσης.
Όταν επιλέγετε μελάνι μεταξοτυπίας ή συναρμολογείτε ένα σετ μελανιών, σκεφτείτε αν χρειάζεστε μη φθαλικές συνθέσεις, υψηλή αδιαφάνεια ή ταχύτερους χρόνους σκλήρυνσης. Πολλές κορυφαίες μάρκες προσφέρουν νέον ή φθορίζοντα χρώματα, επομένως συγκρίνετε κριτικές και δοκιμάστε τα προϊόντα τους πριν από μεγάλες παρτίδες. Τα φθορίζοντα πράσινα, κίτρινα ή ροζ χρώματα της Speedball είναι δημοφιλή τόσο για μπλουζάκια όσο και για αφίσες.
Επίσης, σκεφτείτε εξειδικευμένα μελάνια όπως το κίτρινο μελάνι plastisol ή συλλογές που διαθέτουν πολλαπλές αποχρώσεις νέον σε ένα σετ μελανιών. Υπάρχουν επίσης μελάνια plastisol σχεδιασμένα να παρέχουν «απαλή αίσθηση» για άνετα, ελαφριά πουκάμισα—μια εξαιρετική επιλογή όταν αναζητάτε τόσο απόδοση όσο και άνεση στο τελικό προϊόν.
8. Πώς να πετύχετε απαλά και αδιαφανή αποτελέσματα με φθορίζον μελάνι πλαστισόλης
Μια συνηθισμένη προσπάθεια στην εκτύπωση επίδειξης είναι η επίτευξη μέγιστης ζωντάνιας με ένα απαλό χέρι, που σημαίνει ότι η εκτύπωση είναι απαλή και εύκαμπτη αντί για παχιά ή ελαστική. Χρησιμοποιώντας τα συνηθισμένα μελάνια plastisol, είναι δυνατό να επιτευχθεί μια πιο βαριά εκτύπωση, κάτι που δεν είναι επιθυμητό για μοντέρνα μπλουζάκια που δίνουν προτεραιότητα στην άνεση.
Για να πετύχετε αδιαφανή και απαλά αποτελέσματα στο χέρι, χρησιμοποιήστε κορυφαίας ποιότητας φθορίζον μελάνι πλαστιζόλης, το οποίο έχει σχεδιαστεί για κρεμώδη εφαρμογή. Η εκτύπωση με τον σωστό αριθμό ματιών (μείωση για πιο βαρύ μελάνι, καλύτερη για πιο απαλή εμπειρία) και ο πειραματισμός με αραιωτικά ή τροποποιητές μελανιού μπορούν να βοηθήσουν. Ορισμένοι εκτυπωτές "συνδυάζουν" μελάνια ή εκτυπώνουν λεπτότερα στρώματα σε περισσότερα από ένα περάσματα αντί για ένα παχύ στρώμα.
Ένα απαλό χέρι εμπνέεται επίσης από τη χρήση κάτω από τη βάση. Χρησιμοποιώντας την πιο λεπτή, αποτελεσματική αδιαφανή βάση και σωστή σκλήρυνση, μπορείτε να γλιτώσετε μια αίσθηση ακαμψίας, ενώ παράλληλα διασφαλίζετε ότι τα πολύχρωμα χρώματα της φθορίζουσας εκτύπωσης αναδεικνύονται. Αυτή η ισορροπία είναι ζωτικής σημασίας για φορετά, κομψά πουκάμισα και ρούχα.
9. Φθορίζουσα εκτύπωση μεταξοτυπίας σε βαμβάκι, πολυεστέρα και άλλα υφάσματα
Διαφορετικά υφάσματα μπορούν να επηρεάσουν τον τρόπο λειτουργίας του μελανιού και το πόσο πολύχρωμη ή μακράς διαρκείας μπορεί να είναι η ολοκληρωμένη σας εκτύπωση. Το βαμβάκι είναι το πιο απλό ύφασμα για μεταξοτυπία με μελάνι plastisol, καθώς επιτρέπει ισχυρή πρόσφυση και έντονα χρωματικά αποτελέσματα. Το μελάνι plastisol είναι ακόμη πιο αποτελεσματικό στο βαμβάκι χρησιμοποιώντας ένα κατάλληλο γαλάκτωμα και πλέγμα.
Ο πολυεστέρας, το νάιλον, το λινό και το ρεγιόν παρουσιάζουν πιο απαιτητικές καταστάσεις λόγω της μετανάστευσης της βαφής (κατά την οποία η βαφή του υφάσματος μπορεί να εισχωρήσει στο μελάνι) και των αποκλειστικών απαιτήσεων σκλήρυνσης. Το φθορίζον μελάνι για μεταξοτυπία σε πολυεστέρα μπορεί να απαιτεί μελάνι πλαστιζόλης χαμηλής επεξεργασίας ή την προσθήκη ενός μπλοκαρίσματος από κάτω για την αποφυγή ανεπιθύμητων χρωματικών μετατοπίσεων. Η εκτύπωση σε λινό ή ρεγιόν μπορεί επίσης να απαιτεί ακριβή πρόσθετα για να διασφαλιστεί ότι το μελάνι παραμένει εύκαμπτο και προσκολλάται αποτελεσματικά μετά τη σκλήρυνση.
Ανεξάρτητα από το ύφασμα, συνήθως πλύνετε, ελέγξτε και ελέγξτε για ζωντάνια και ανθεκτικότητα χρώματος. Συμβουλευτείτε τον προμηθευτή μελανιών μεταξοτυπίας για να βεβαιωθείτε ότι το καλύτερο προϊόν για το ύφασμά σας, ειδικά για εργασίες που χρησιμοποιούν σετ μελανιών νέον ή φθορισμού πλαστιζόλης σε τεχνικά ανθεκτικά ρούχα.
10. Συνηθισμένα λάθη που πρέπει να αποφεύγετε με το φθορίζον μελάνι μεταξοτυπίας
Ένα συνηθισμένο λάθος με την εκτύπωση με φθορίζουσα μεταξοτυπία είναι η παραμέληση της ανάγκης για αδιαφάνεια και στρώσεις βάσης, ειδικά σε σκούρα πουκάμισα. Η εκτύπωση μελανιού νέον βυσσινί ή φθορίζον κίτρινο ταυτόχρονα σε μαύρα ή σκούρα ρούχα καταλήγει σε μια άτονη εκτύπωση, επειδή η ημιδιαφάνεια του μελανιού θα επιτρέψει στην απόχρωση του υφάσματος να φαίνεται.
Ένα άλλο πρόβλημα είναι οι ακατάλληλες θερμοκρασίες θεραπείας. Η πολύ λίγη θερμότητα μπορεί να οδηγήσει σε μελάνι που ξεπλένεται ή γίνεται κολλώδες, ενώ η υπερβολική θερμότητα μπορεί να κάψει το υλικό ή να σπάσει την εκτύπωση. Πάντα να ελέγχετε τον χρόνο θεραπείας και τη θερμοκρασία για κάθε μελάνι, ειδικά όταν εργάζεστε με έντονα φθορίζοντα χρώματα, τα οποία μπορεί επίσης να έχουν ειδικές απαιτήσεις από τα συμβατικά μελάνια plastisol.
Τέλος, η μη χρήση του καλύτερου αριθμού ματιών, γαλακτώματος ή τάσης εκτύπωσης μπορεί να προκαλέσει διαρροή, έλλειψη υλικού ή κακή ασφάλεια στις εκτυπώσεις σας. Ακολουθείτε πάντα τις καλές πρακτικές για την προετοιμασία της εκτύπωσης και πραγματοποιήστε μια δοκιμαστική εκτύπωση όταν χρησιμοποιείτε ένα ολοκαίνουργιο μελάνι για μεταξοτυπία, ειδικά εάν δημιουργείτε τον δικό σας συνδυασμό μελανιού φθορισμού και πλαστιζόλης.
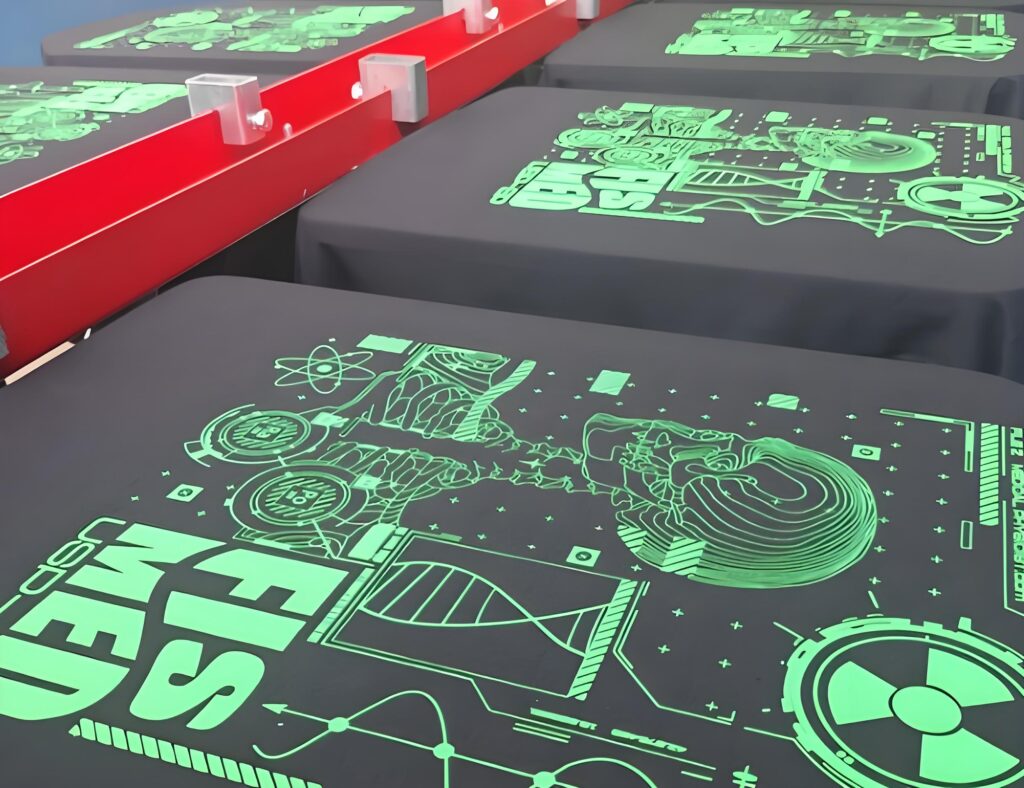