Table of Contents
A Comprehensive Guide to Using Plastisol Ink in Various Industries
Plastisol ink is a popular choice for printing on clothes, cars, signs, and more. But if you use it wrong, your designs might crack, fade, or wash off. This guide will show you how to use plastisol ink the right way. Let’s get started!
What is Plastisol Ink?
Plastisol ink is made from two main ingredients:
- PVC resin (a type of plastic).
- Plasticizers (oily liquids that make the ink soft and workable).
Why do people love plastisol ink?
- It doesn’t dry until you heat it. This means it won’t clog your screens.
- It makes bright colors that pop, even on dark fabrics.
- It stays strong and doesn’t fade after washing.
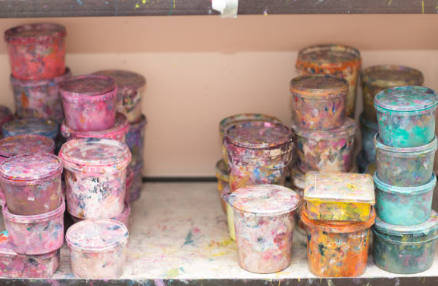
How Plastisol Ink is Used in Different Industries
1. Clothing and Apparel
Best fabrics: Cotton, polyester, and blends. Tips for success:
- Use soft-hand ink for comfortable t-shirts.
- Use high-density ink for thick logos (like sports jerseys).
- Example: Big brands like Gildan use plastisol ink for millions of shirts.
2. Automotive and Manufacturing
Common uses: Dashboard labels, wire coatings, and machine tags. Key tips:
- The ink must handle high heat (over 300°F).
- Use adhesion promoters to make it stick to metal or plastic.
- Follow safety rules like UL and ASTM standards.
3. Signs and Packaging
Best materials: PVC banners, corrugated plastic, and Tyvek®. Make it last longer:
- Add UV-resistant chemicals to fight sun damage.
- Use thicker layers of ink for outdoor signs.
4. Promotional Products
How to print: Use heat transfers for mugs, phone cases, and keychains. Avoid cracks: Cure at lower temperatures on curved surfaces.
Step-by-Step Guide to Using Plastisol Ink
1. Prepare Your Tools
Choose the right screen:
- 110-160 mesh count for small details.
- 60-86 mesh count for thick ink layers. Clean your material: Wipe surfaces with rubbing alcohol first.
2. Printing Tips
Fix thin ink: Add curable reducer (like Wilflex additives). Stop ink bleeding: Keep the screen slightly raised off the fabric.
3. Curing the Ink
Perfect cure: Heat the ink to 320°F–330°F for 60–90 seconds. Check the temperature: Use a laser thermometer for accuracy. Too hot? Ink becomes brittle. Too cold? Ink washes off.
Fixing Common Problems
Problem | Quick Fix |
---|---|
Pinholes | Clean the screen and tighten the mesh. |
Ink won’t stick | Use an adhesion promoter. |
Cracking | Let the ink cool slowly after curing. |
Fading after wash | Test prints using AATCC standards. |
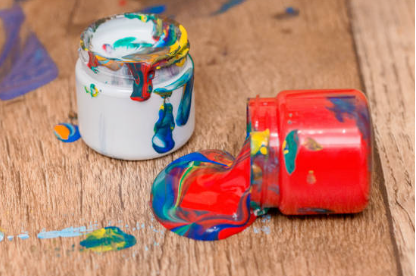
Eco-Friendly and Safe Options
Safer inks: Try phthalate-free brands like Matsui Evolve® or Ryonet EcoLine. Workplace safety: Follow OSHA guidelines and read safety data sheets (SDS). Reduce waste: Recycle cured ink scraps instead of throwing them away.
New Trends in Plastisol Ink
- Hybrid Inks Mix plastisol with water-based ink for a softer feel.
- Conductive Inks Print circuits on car parts for smart surfaces.
- Eco-Plasticizers Use plant-based formulas made from soy or castor oil.
Frequently Asked Questions
Can plastisol ink be used on nylon?
Yes! Use adhesion promoters first to help it stick.
Final Thoughts
Plastisol ink is perfect for creating tough, vibrant prints on clothes, cars, signs, and more. Always cure at 320°F–330°F, choose the right screen mesh count, and try eco-friendly inks like Ryonet EcoLine for safer projects.
Need help? Download a free plastisol curing cheat sheet here.