Bullet Point Summary – Key Takeaways
- White plastisol ink is vital for ambitious, opaque prints on darkish garments.
- Always choose the high-quality white plastisol ink to your material kind: cotton, polyester, blends.
- Mesh count, squeegee, and a easy, tacky pallet are critical for high print nice.
- Check for qualities like opacity, low bleed, and low cure whilst deciding on white ink.
- Avoid remedy issues by using the usage of a laser gun and following encouraged live times.
- Prevent dye migration and bleed with proper ink and appropriate dryer settings.
- Try print-flash-print for added opaque effects on difficult jobs.
- Pick pinnacle manufacturers like Wilflex, Monarch Color, or IC for reliability and overall performance.
- For a tender and creamy hand, stir ink well and test with reducers as wanted.
- With the right display printing ink, setup, and manner, every print can be a masterpiece!
By getting to know the art of white plastisol ink and clever display printing techniques, you could raise your garb emblem, delight your clients, and with a bit of luck pursue even the maximum stressful display screen printing initiatives. Happy printing!
Can you heat up white plastisol ink for screen printing?
Summary:
White plastisol ink is the powerhouse behind each formidable, bright display print you see on t-shirts, hoodies, and custom apparel. If you’ve ever wondered a way to get that ideal white print—soft and creamy in appearance but with unbeatable opacity—this newsletter is your cross-to useful resource. We’ll resolve what makes the first-class white plastisol ink stand out, the way to properly treatment your prints, and proportion insider suggestions which can supercharge your next display printing task. Whether you’re a pro display printer or new to print inks, this guide will equip you with actionable knowledge for excellent, durable white prints,
Outline
- What Is White Plastisol Ink and Why Is It So Popular for Screen Printing?
- How Does Plastisol Ink Work in Screen Print Projects?
- What Makes the Best White Plastisol Ink Stand Out?
- How to Choose the Right White Ink for Different Fabrics—Cotton, Polyester, and Blends
- What’s the Importance of Opacity, Bleed Resistance, and Low Cure in White Print Inks?
- Mesh Count, Squeegee, and Pallet: Getting Your Press Set Up for the Best Printing
- Step-by-Step: Achieving a Perfect White Screen Print
- Avoiding Common Issues: Dye Migration, Bleed, and Print Quality
- Comparing Top Brands: Wilflex, Monarch Color, IC, and More
- Pro Tips for Softer, Creamier, and More Durable White Prints
1.What Is White Plastisol Ink and Why Is It So Popular for Screen Printing?
White plastisol ink is the cornerstone of the display screen print industry and forms the muse for lots colourful designs, particularly when printing on dark fabrics. Unlike water-primarily based inks, plastisol ink sits on top of the substrate, giving a bold, opaque end result that’s seen even on deep black cotton garments. One of the most important reasons white plastisol ink is a cross-to is its high opacity—a crucial component when you want your design to definitely pop.
Screen printers love running with plastisol inks for screen printing because they’re equipped to use straight from the container and feature a creamy consistency. This approach less worry about blending ratios and more cognizance on achieving the fine printing results. Plus, white plastisol ink offers outstanding durability and wash fastness, ideal for t-shirts and clothes with the intention to take a beating.
When it comes to versatility, few inks fit white plastisol ink. Whether you’re tackling cotton clothes, polyester blends, or even heavier fabric, this ink performs. And as you’ll discover under, selecting proper ink is just the start of making high-impact white screen prints.
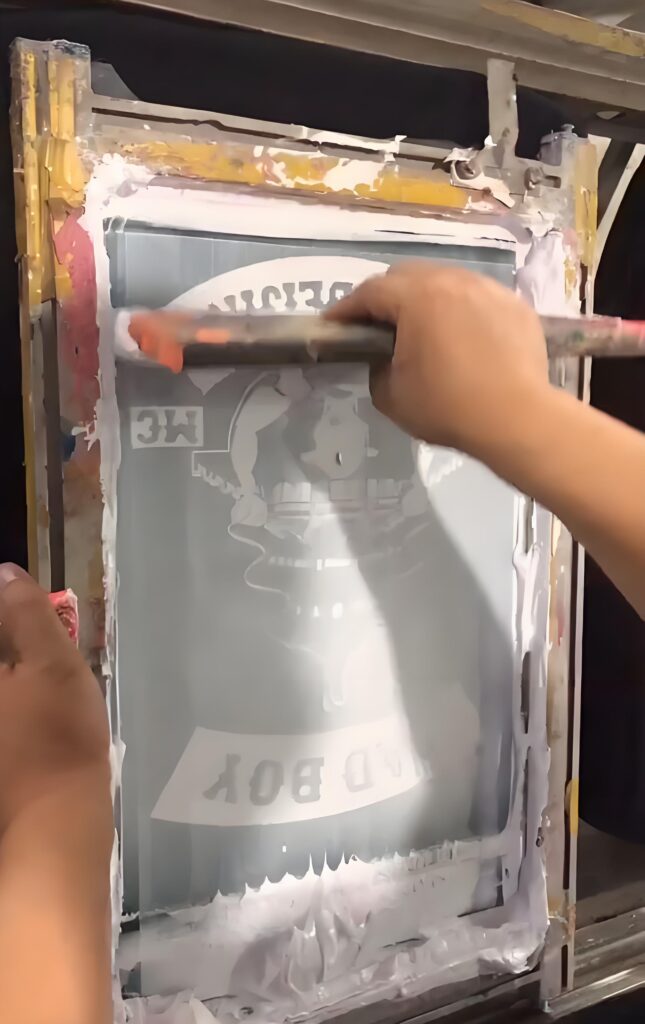
2.How Does Plastisol Ink Work in Screen Print Projects?
The magic of plastisol ink lies in how it healing procedures. Unlike water-primarily based print inks, plastisol will no longer dry until uncovered to heat—usually in a conveyor dryer or flash dryer at 320°F to 330°F, taking into consideration clean cleanup and long open instances on your mesh. The ink’s thick, creamy viscosity results in a barely raised, opaque print that sits atop your garment, offering a shiny white print even on the darkest fabrics.
What’s in particular appealing approximately working with plastisol is its compatibility with automation. Most automated display printers, whether using one hundred ten mesh or a lower mesh, find that plastisol inks are clean to print, forgiving of slower store speeds, and provide a reliable, regular ink deposit1. Automation additionally makes repeating results less difficult, whether you’re managing brief runs or lots of prints in a single job.
Ultimately, a successful screen print with plastisol ink depends heavily on right remedy. Failing to reach the essential reside time within the dryer can bring about problems related to wash durability, even as overheating can make the ink brittle. Using a laser gun to check ink temperature at the platen or conveyor belt will assist ensure you hit that curing candy spot whenever.
3.What Makes the Best White Plastisol Ink Stand Out?
Choosing the first-class white plastisol ink is all about balancing a smooth and creamy feel with excessive opacity and coffee bleed. Great ink for base whites is in particular formulated to withstand dye migration, provide super insurance, and maintain a soft hand while applied in one or strokes16. Look for a white plastisol ink that capabilities phrases like “low bleed,” “high opacity,” and “creamy consistency” at the label.
The best white plastisol ink can even deliver a nice matte finish—no longer a gloss—keeping your white prints looking fresh even after multiple washes1. Soft and creamy ink is easier to work via a lower mesh, so you’ll have fewer setup problems and higher consequences, particularly on huge print runs.
Opaque white inks stand apart because they permit for exquisite print exceptional on dark fabrics. Whether you’re creating a standout fashion line or coping with custom orders, excessive opacity guarantees your designs are sharp, bold, and expert.
4.How to Choose the Right White Ink for Different Fabrics—Cotton, Polyester, and Blends
Selecting the proper white ink means expertise your substrate. If you’re printing on a hundred% cotton, maximum widespread white plastisol inks will paintings superbly, supplying extremely good coverage and smooth utility. For polyester or poly-mixture clothes, however, dye migration is a real threat: the dye inside the garment can bleed up into your white print for the duration of curing, turning it pink or yellow.
Modern polyester inks and coffee-bleed formulations are particularly designed to save you those issues. Always test your plastisol ink for compatibility with “polyester,” “low bleed,” or “high opacity” on the label. Test prints on new substrates are crucial, specially in case you’re switching among cotton clothes and synthetic blends.
Remember, using the right ink for your specific garment kind saves time and reduces wasted materials for the duration of production. For intense cases, don’t forget the usage of a blocker underbase or specialised poly white inks designed through pinnacle manufacturers like Wilflex, Monarch Color, or International Coatings.
5.What’s the Importance of Opacity, Bleed Resistance, and Low Cure in White Print Inks?
Opacity is critical for white plastisol ink—with out it, prints on darkish fabric will look faded and unattractive. High opacity white ink guarantees your designs remain crisp, even against deep reds, navies, and blacks. The term “bleed resistance” refers to how properly the ink prevents dyes from migrating from the garment into the ink layer for the duration of the curing technique.
Low remedy inks are a recreation changer, particularly with current synthetic substrates. They allow you to completely therapy the ink at lower temperatures, decreasing the threat of dye migration and bleed. These particularly formulated inks are perfect for custom jobs on polyester or poly-combo clothing, wherein higher dryer heat may want to motive more issues than it solves.
A awareness on these qualities ensures no longer best great-searching prints but also dependable overall performance within the wash—key for clients worrying durability and toughness from their custom tees.
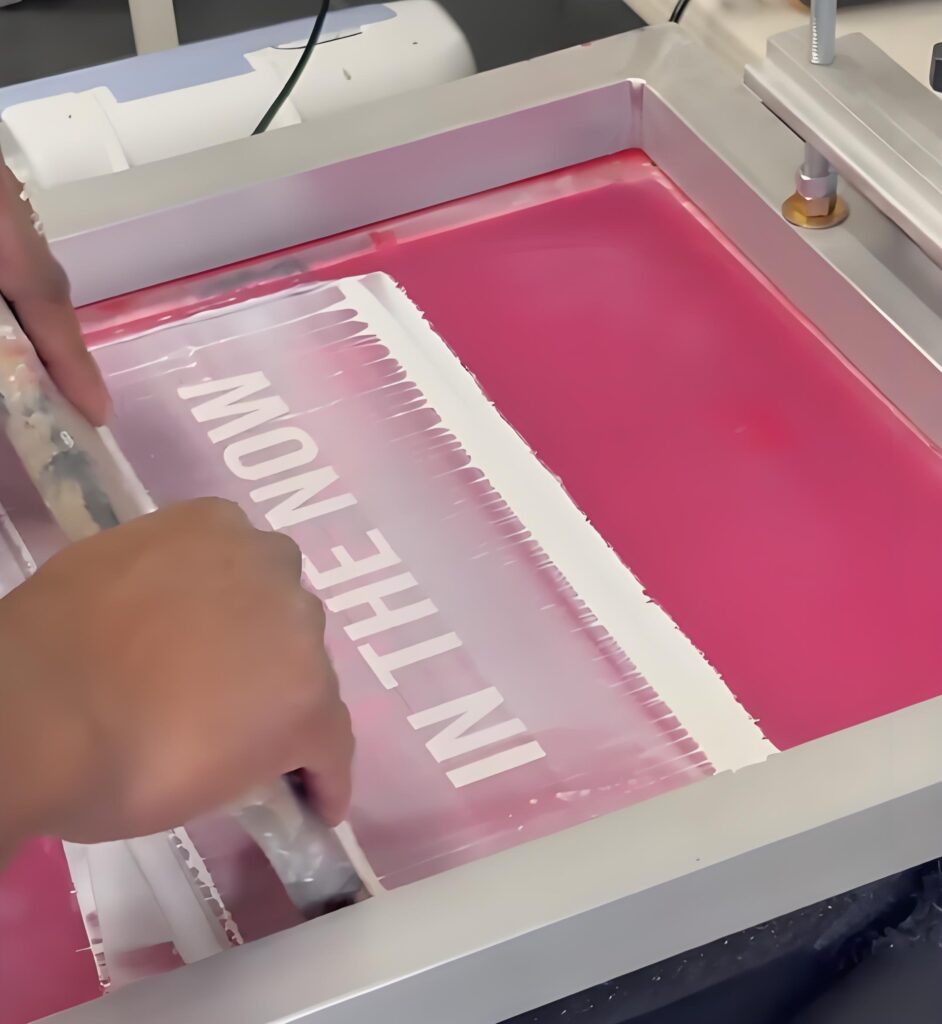
6.Mesh Count, Squeegee, and Pallet: Getting Your Press Set Up for the Best Printing
Before you even crack open your plastisol ink, make certain your press is configured for achievement. Mesh count is critical—decrease mesh like one hundred ten mesh permits greater ink to deposit at the blouse, that is ideal for thick, opaque white ink on dark clothes. Higher mesh counts (inclusive of 230 mesh) paintings for finer information however require thinner ink and can reduce opacity.
The squeegee you operate—its durometer and whether or not you push or pull—additionally shapes the ink deposit. A medium durometer squeegee typically gives the great consequences with white plastisol ink, delivering enough strain for a smooth, even print. Don’t neglect the importance of an excellent, tacky pallet or platen: it holds your shirt regular and guarantees your registration stays crisp from shirt to blouse.
Finally, make sure your emulsion and display mesh are like minded with the ink viscosity. Thicker inks carry out differently depending on mesh and display screen anxiety, so tweak your setup to in shape your preferred white print ink for consistency in each run.
7.Step-by-Step: Achieving a Perfect White Screen Print
Ready to get printing? Start with a nicely tensioned lower mesh (like a hundred and ten mesh), load your creamy, soft and creamy white plastisol ink onto the display, and flood the screen for even insurance. Place your blouse at the pallet, and use a pointy squeegee angle to put down a stable, opaque print.
If you want extra opacity, attempt the print-flash-print method. This way printing one layer of ink, flashing it in brief below a dryer or heat lamp, then printing a 2nd layer on top. This method fights dye migration and ensures a great white print even on darkish-colored shirts.
Don’t bypass therapy! Using a laser gun, degree the ink floor temperature on the belt of your conveyor dryer or on the platen if flashing. Hit the producer’s encouraged live time and temperature to fasten for your design with out risking under- or over-curing your print inks.
8.Avoiding Common Issues: Dye Migration, Bleed, and Print Quality
Every display screen printer faces print first-class setbacks sooner or later. For white ink, the biggest enemies are dye migration and bleed—particularly important whilst printing on poly or dark-colored cotton. If you notice colors moving in your print after curing, it’s probably an difficulty with therapy temperature or ink choice.
Low remedy and coffee bleed plastisol whites are formulated to combat these troubles. Always talk to excellent practices with your dryer, and in no way let garments sit down in direct daylight after printing, as this will also inspire dye migration. Use right ink reducer for tweaking viscosity if you come upon demanding situations with thicker ink.
Consistent ink deposit, correct emulsion, and careful mesh choice maintain print high-quality excessive and decrease remodel. Sometimes, clearly cleaning your mesh or tweaking your squeegee angle can dramatically enhance your results, leading to first-rate matte end and fewer rejects.
9.Comparing Top Brands: Wilflex, Monarch Color, IC, and More
The enterprise is filled with top-tier ink manufacturers. Wilflex, Monarch Color, and International Coatings (IC) all offer non-phthalate, opaque, and occasional bleed options with terrific reviews from printers international. Each organisation has a slightly one of a kind white: some provide softer, greater matte finishes, while others specialize in ultra-high opacity or low cure overall performance.
Wilflex, as an example, is understood for its easy, gentle and creamy whites which might be easy to work, even for novices. Monarch Color promises highly excessive opacity appropriate for the hardest jobs, whilst IC focuses on area of expertise whites for unusual materials and custom Pantone matches.
No be counted that you pick out, the key is selecting inks designed in your precise wishes and doing a few take a look at prints to verify overall performance for your clients’ garments.
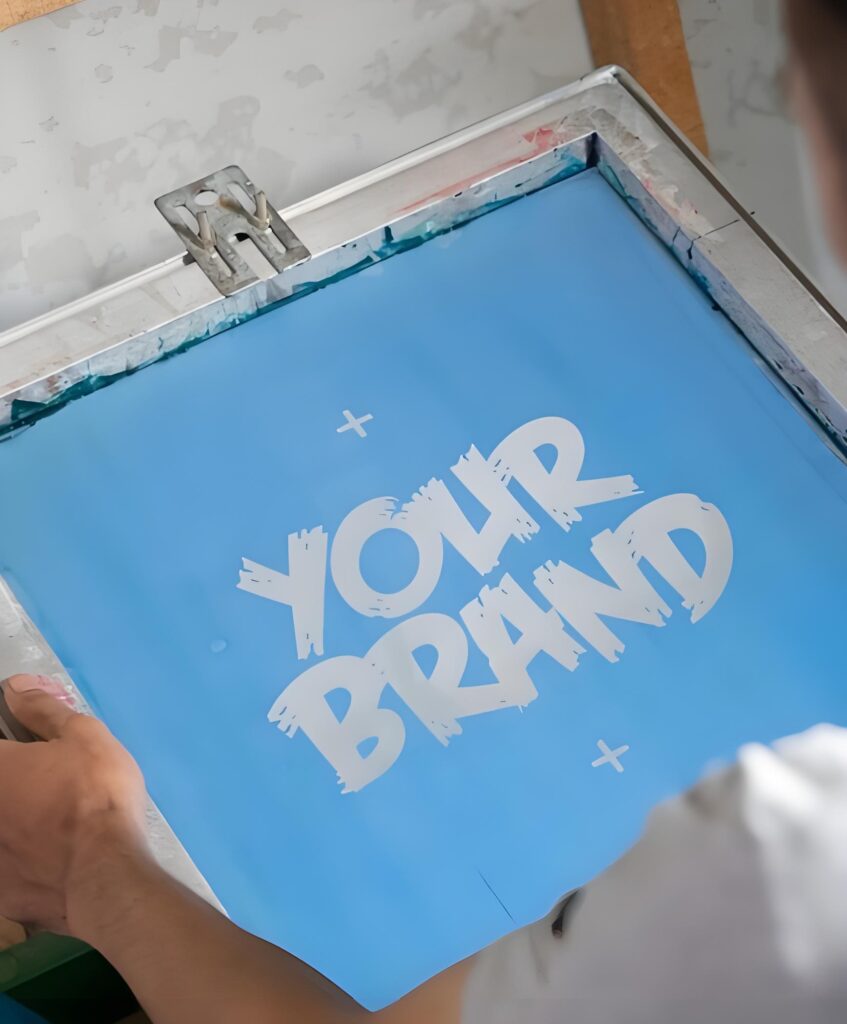
10.Pro Tips for Softer, Creamier, and More Durable White Prints
For the great printing experience, continually stir your ink thoroughly—even pre-blended, geared up to use plastisol inks gain from a quick mixture to make certain creamy consistency. If you’re trying to find more softness, remember adding a reducer carefully or use a specially formulated smooth hand white ink for cotton garments.
Never shortcut the therapy. Your dryer or flash temperature is crucial, so always use a laser gun and comply with producer steering to lock in wash-fast outcomes. For advanced sturdiness, pair low remedy white ink with poly and poly-blends, and use a excessive-opacity system for dark fabrics where vivid whites be counted most.
Work smart, no longer tough: prep your screens and mesh remember earlier, double-test your emulsion, and stay with right ink and top-tier brands. These little steps assure a amazing ink enjoy that leads to higher consumer delight and fewer complications for your store.