Learn how to optimize your screen printing process with an emulsion calculator. This guide covers how to calculate the right amount of emulsion.
tips for different screen sizes and mesh counts, and the importance of the emulsion-sensitizer ratio for high-quality prints.
Tabla de contenido
1. Unlocking the Potential of the Emulsion Calculator to Enhance Serigrafía
Screen printing demands precision, especially when applying emulsion for plastisol ink. If the emulsion isn’t applied correctly, the final print quality can be compromised. The emulsion calculator is an innovative tool that removes the uncertainty from the equation, helping you calculate the precise amount of emulsion required based on the screen size, mesh count, and coating technique. Whether you’re just starting or are a seasoned expert, mastering this tool can elevate both your print quality and process efficiency.
In this guide, we’ll walk you through how the emulsion calculator works, share tips for calculating and measuring emulsion for screen printing, and address common questions such as, “How much emulsion do I need?” and “What’s the proper way to calculate emulsion?”
2. Accurately Estimating the Right Amount of Emulsion for Successful Screen Printing
Getting the correct amount of primary emulsion is key to achieving excellent screen printing results. The primary emulsion is the first layer applied to the screen, and it must be thick enough to create a durable stencil, but not so thick that it affects print quality.
When estimating the right amount of emulsion, there are a few important factors to consider:
- Número de mallas: Finer mesh counts, like 230, need less emulsion compared to lower counts such as 110.
- Screen Size: Larger screens, like 24×36 inches, will require more emulsion than smaller screens, like 12×16 inches.
- Coating Technique: Whether you’re using a scoop coater or applying the emulsion manually will impact how much is needed.
By taking these factors into account, the emulsion calculator can guide you precisely to the amount required, eliminating any guesswork.
3. How Much Emulsion is Enough? Finding the Right Quantity
One of the most frequent concerns in screen printing is determining how much emulsion is enough. Applying too much can lead to excessive exposure times and sloppy prints, while applying too little can result in weak stencil formation and poor-quality prints. Several factors influence the amount needed:
- Mesh Size: Larger mesh screens, like 160 mesh, will need less emulsion than coarser ones, like 110 mesh.
- Coating Method: Using a scoop coater generally requires less emulsion and provides an even coat, while hand-coating often requires more emulsion.
- Number of Coats: Typically, two coats are applied—one to the front and one to the back, each requiring the right thickness to form a solid stencil.
An emulsion calculator helps you accurately estimate the right amount of emulsion based on your specific setup, optimizing your printing process.
4. The Essential Formula for Measuring Emulsion Correctly
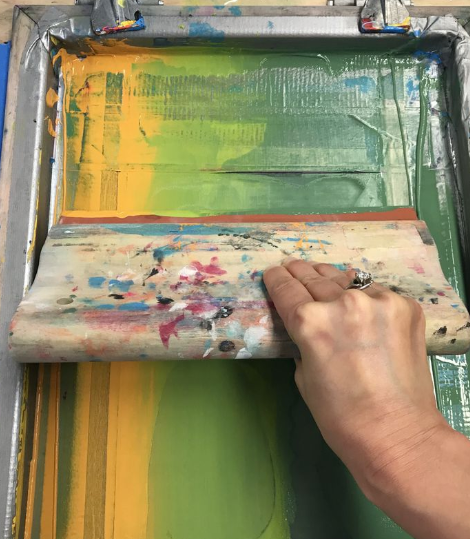
Properly measuring emulsion is essential for producing high-quality prints. The process becomes simpler when you follow a systematic approach:
- Screen Size: Larger screens, such as 24″x36″, will need more emulsion, while smaller screens, like 12″x16″, need less.
- Número de mallas: Higher mesh counts (e.g., 230 mesh) require less emulsion than lower mesh counts (e.g., 110 mesh).
- Coating Method: The method you use to apply the emulsion impacts the amount needed.
By inputting these details into the emulsion calculator, you’ll receive an exact measurement, saving time and materials while avoiding the trial-and-error method that can lead to waste.
5. The Importance of the Emulsion-Sensitizer Ratio
The ratio of emulsion to sensitizer is a crucial element in achieving the best results with your screen printing emulsion. This ratio refers to the blend of emulsion and sensitizer, which makes the emulsion light-sensitive for exposure.
There are two common ratios:
- 1:1 Ratio: Equal parts of emulsion and sensitizer.
- 2:1 Ratio: Two parts emulsion to one part sensitizer.
The correct ratio ensures optimal exposure times and stencil strength. Too much sensitizer can result in overexposure, while too little can cause underexposure. The emulsion calculator can assist in determining the right amount of sensitizer needed based on the emulsion you’re using, ensuring a perfectly balanced mixture.
6. Reliable Methods for Determining Emulsion Requirements in Screen Printing
There are several methods available to help you determine the right amount of emulsion for your screen printing. Below are the most reliable techniques:
- Trial and Error: This involves experimenting with different amounts of emulsion and testing the results. While it works, it can be time-consuming and wasteful.
- Manufacturer Recommendations: Many emulsion manufacturers provide charts that estimate the amount of emulsion needed based on mesh count and screen size. While useful, these are less precise than personalized calculations.
- Emulsion Calculator: The most accurate and efficient method is to use an emulsion calculator. By entering the screen size, mesh count, and coating method, you can get the exact amount of emulsion required, ensuring consistent and high-quality prints.
Though trial and error may be occasionally used, relying on an emulsion calculator is the best way to ensure accurate measurements and prevent wastage.
This version has been rewritten with a new style and vocabulary while keeping the essential points intact. Let me know if you’d like further adjustments!
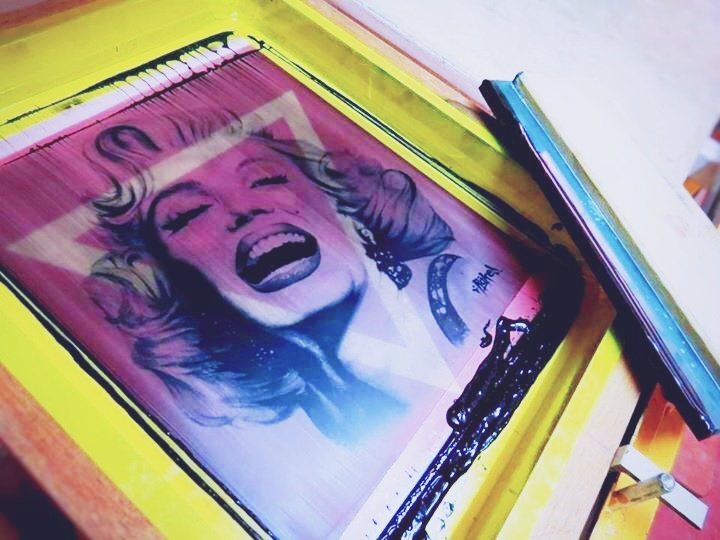