מהבסיס הלבן והקרחוני השאפתני לחולצת הלהקה האהובה עליכם ועד לשכבות הקרמיות והאטומות שגורמות לצבעים להבליט על חולצות כותנה ופוליאסטר, ההרפתקה של מציאת דיו פלסטיסול לבן איכותי שווה את תשומת ליבו של כל מדפיס. בין אם אתם עובדים על החולצה הראשונה שלכם או על ההדפס האלף שלכם, דיו ידע, פלסטיסול והאמנות של יצירת ההדפס הלבן המושלם הם מה שמבדיל חובב ממקצוען אמיתי. בסקירה מעמיקה זו, תגלו מדוע לימוד דיו לבן הוא תרופת הקסם להדפסים עזים, ייבוש יעיל ותוצאות מרהיבות על כל פריט לבוש. חגרו חזק - זה לא סתם "מדריך אחר". אנחנו חושפים את הרמזים, הסודות המדממים וטכניקות הערבוב האיכותיות שיעזרו לכם לשמור על הדפוס שלכם חלק והצבעים שלכם אמביציה יותר.
תוֹכֶן הָעִניָנִים
1. מה מייחד את דיו פלסטיסול להדפסת מסך לבנה?
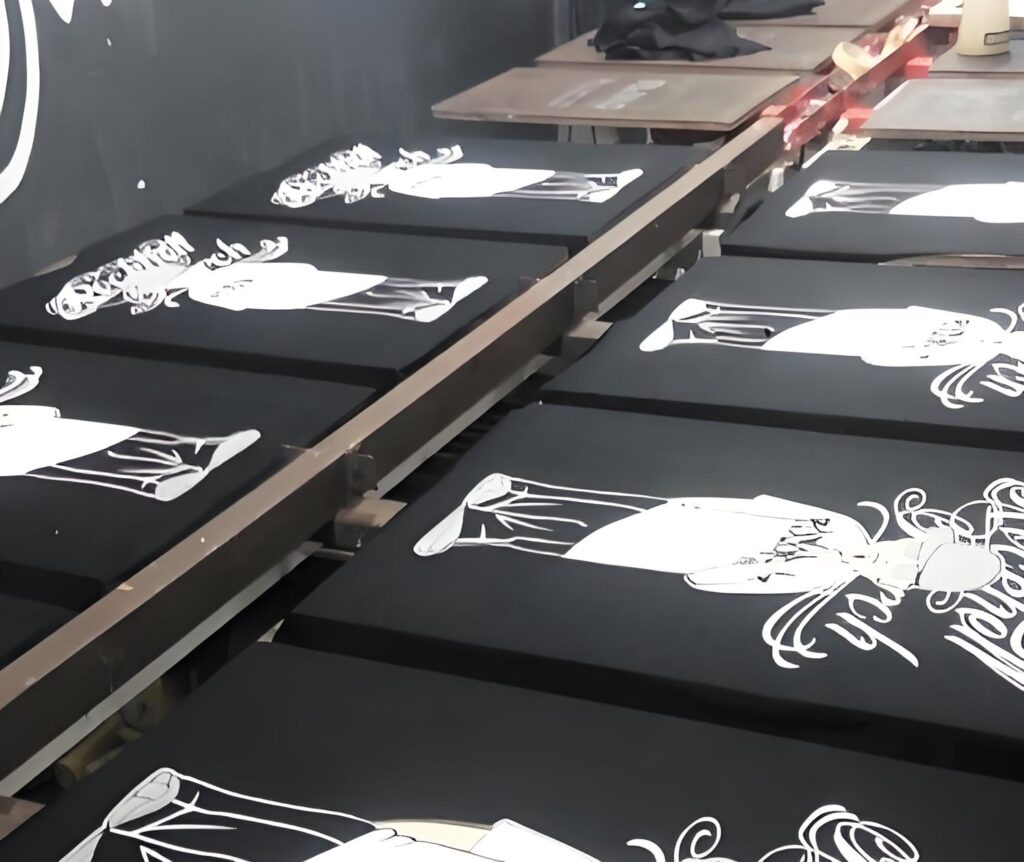
דיו פלסטיסול תופס מקום מיוחד בעולם הדפסת המסך. קבל/י סגור/י בניגוד לדיו על בסיס מים, דיו פלסטיסול הוא עדין, גמיש ומספק הגנה מעולה, במיוחד על בגדים כהים יותר שבהם אטימות בהירה ומוגברת חשובה. הרבגוניות שלו נובעת מטבעו הכימי המדויק: פלסטיסול עשוי מחלקיקי PVC התלויים בפלסטייזר, מה שאומר שהוא אינו מתייבש על המסך כמו אפשרויות על בסיס מים. המרקם הקרמי הזה הופך אותו למושלם להדפסות ארוכות, הדפסות מורכבות או שכבות, ומאפשר משטח נקי בעת הדפסה עם דיו פלסטיסול לבן.
הקסם של פלסטיסול עבור חבילות דיו לבן בא לידי ביטוי באטימות שלו. דיו לבן לרוב רוצה להיות שאפתני וקרמי ככל האפשר, ולהופיע כבסיס כדי שצבעי פיגמנט אחרים יישארו אמיתיים ללא קשר לצבע החולצה. בין אם אתם עובדים עם דיו איכותי או עם שילוב זול יותר, קבלת השכבה הלבנה והצפופה תלויה בתכונות הספציפיות של דיו פלסטיסול ובזהירות שאתם נוקטים בעת יישומו.
2. מדוע דיו פלסטיסול לבן נחשב חיוני עבור מדפסות מסך?
אם תיצרו קשר עם מדפיסי מסך מנוסים, הם יגידו לכם שהגעה להדפס לבן איכותי ויפה היא המבחן הסופי של מיומנות ואמנות. דיו פלסטיסול לבן אינו סתם עוד גוון; הוא הבסיס. הוא מספק זוהר לכל סוגי הדיו השונים המונחים מעליו. כשעושים זאת נכון, אדומים אדומים יותר, כחולים נועזים יותר, ואפילו שילובים מורכבים נשמעים נכונים, הודות לבסיס המושלם הזה.
להדפסת מסך על בדים כהים, דיו לבן מציע אטימות שאין שני לה וחסימה קלה. מערכת הדיו הנכונה מבטיחה הדפסים מבריקים, ולא עוד מלוכלכים. וזה לא רק מראה חיצוני - דיו לבן עדין מציע עמידות בפני דליפות, חיוני במיוחד על בגדי פוליאסטר ומעורבים הנוטים לנדידת צבעים. דיו פלסטיסול לבן אמין בתוכך
3. כיצד משפיעה טמפרטורת הייבוש על תוצאות הדיו הלבן?
ריפוי הוא ללא ספק חשוב לשמירה על העמידות, עמידות השטיפה והחיוניות של הדפסי דיו הפלסטיסול שלכם. דיו פלסטיסול לבן דורש בדרך כלל טמפרטורת ריפוי מסוימת - בדרך כלל בין 320°F ל-330°F - כדי לאחות לחלוטין את ה-PVC והפלסטייזר. ריפוי יתר עלול לגרום לשטיפה או להתקלף של הדיו; ריפוי יתר עלול לגרום לשריפת החולצה או לבעיות דימום.
כאשר עובדים עם תערובות פוליאסטר או פולי, הטמפרטורה חשובה אף יותר. בדים אלה יכולים לשחרר צבעים בטמפרטורות גבוהות, מה שמוביל לנדידת צבע. חלק מדיו הפלסטיסול הלבן האיכותי מיועד לטמפרטורה נמוכה או להבהבה קצרה, מה שמאפשר למדפסות מסך להפחית את טמפרטורת הטיפול, למזער את הסיכון ולהבטיח תוצאות נהדרות על כל חומר. תמיד יש לבדוק את הוראות היצרן, ולבדוק את זמן ההבהבה והשהייה כדי להשיג את ההדפס הלבן הקרחוני הטוב והעמיד ביותר.
4. האם המצע שלך חשוב? הדפסה על כותנה, פוליאסטר ובדים מעורבים
אף בגד אינו זהה - וגם לא תגובותיו לדיו. כותנה נותרה הבד הסלחני והידוע ביותר למשימות הדפסת מסך, המאפשר לדיו פלסטיסול לבן להימרח בקלות עם סיכון מינימלי לדימום. הסיבים סופגים בנוחות את הדיו, מה שמביא למגע עדין וגוון חזק ואטום.
פוליאסטר, לעומת זאת, ידוע לשמצה בנדידת צבעים. הסיבים המלאכותיים וסוגי הצבע הייחודיים בחולצות פוליאסטר מרמזים שחום יכול להפעיל את הצבע, ולגרום לו "לדמם" לתוך הדיו הלבן ולהקהות את בהירותו. תערובות כמו חולצות 50/50 משלבות את האתגרים, ולכן השימוש באפשרויות דימום נמוך או לבן פוליאסטר הוא המפתח לתוצאות באיכות גבוהה. מדפסות תצוגה חכמות בוחרות את הדיו וההגדרות שלהן בהתבסס על תכולת הבד כדי למקסם את שביעות הרצון בהדפסה ולהפחית הפתעות.
5. כיצד לערבב וליצור דיו לבן אטום ודיו בהיר
ערבוב דיו פלסטיסול לבן מדויק הוא גם טכנולוגיה וגם אמנות. הדיו הלבן הנעים משתמש באיזון זהיר של עומס פיגמנט, חומר פלסטייזר וחומרי מילוי כדי להשיג מרקם שאפתני, אטום וקרמי שנמרח בקלות אך מכסה לחלוטין. אם אתם משתמשים במערכת ערבוב דיו, הקפידו על יחסים ספציפיים עבור בסיס, פיגמנט ותערובת כדי למנוע הדפסה דקה או גירית.
עבור רוב האטימות על חולצות כהות, מדפיסים מומחים מסתמכים על ניסוח אטימות גבוה ולפעמים מכפילים שכבת בסיס כדי לחסוך בתצוגה. המטרה היא לבן קרחוני ועז שלא יאבד את זוהרו לאחר הבהוב או ייבוש. אם ברצונך לכוונן את הצמיגות, השתמש במרכיבים מומלצים והחזק הערות כדי להעתיק את ההצלחה שלך בפרויקטים עתידיים.
6. שיטות עבודה מומלצות למניעת נדידת דימום וצבע
דליפת צבע ונדידת צבע יכולים בקלות לחבל בהדפס לבן יפהפה - במיוחד על פוליאסטר ודיו מעורב. הסיבה לכך היא חום: כאשר החולצה מגיעה לטמפרטורת הייבוש, סיבים צבועים עלולים לשחרר צבע (בדרך כלל אדום, כחול כהה או שחור), אשר עובר לדיו הלבן שלך. כדי להילחם בכך, השתמשו בדיו עם דליפת צבע נמוכה והימנעו מלהבה יתר על המידה.
מדפיסי משי בוחרים לעתים קרובות בתערובות דיו פלסטיסול לבן פרימיום המסומנות כדלות דיו, המנוסחות במיוחד עבור סיבים סינתטיים. הגדרת מכונת דפוס נכונה עם טמפרטורות פלסטיסול נמוכות יותר עם הבזק והקשייה, כמו גם הבזק מהיר בין שכבות, יכולים לעשות את כל ההבדל. ניטור זמן השהייה, ניקוי קבוע של משי הדפוס ושמירה על קרירות אזורי מכונת הדפוס עוזרים לשמור על הדפסים לבנים קרחוניים מודגשים ונקיים.
7. מה ההבדל בין דיו דל דימום, דיו מהיר ודיו לבן רגיל?
אין "מידה אחת מתאימה לכולם" בכל הנוגע לדיו פלסטיסול לבן. דיו לבן רגיל מספק אטימות מעולה והוא אידיאלי עבור רוב חולצות הכותנה. דיו בעל דימום נמוך, לעומת זאת, מעוצב עם כימיה מיוחדת לחסימת נדידת צבע - חובה עבור פוליאסטר ותערובות שבהן עמידות בפני דימום היא קריטית.
צבעי דיו לבנים מהירים נועדו להיווצר במהירות תחת חום נמוך, מה שמפחית את הסיכון לחריכה של בדים עדינים או להפעלת צבעים. עבור הדפסה בנפח גדול או בעת הדפסה על מספר סוגי בגדים בו זמנית, השקעה בגלון או שניים מכל דיו לבן מיוחד מאפשרת למדפסות משי להתמודד עם פרויקטים מגוונים בביטחון.
8. כיצד לבחור את הרשת הנכונה ואת הגדרת המכונה להדפסות בצבע לבן קרחון
ספירת רשתות ותצורת מכונת הדפוס הן הגיבורים הלא מוכרים מאחורי תוצאות הדפסת משי מתקדמות. רשת גסה יותר (86-110 חוטים לאינץ') מאפשרת ליותר דיו לעבור, אידיאלית לשכבות דיו פלסטיזול לבן עבות, קרמיות ובעלות אטימות גבוהה. רשת דקה יותר שמורה לפרטים או ליישומים קלים יותר אך עלולה לפגוע באטימות מסוימת.
יש להגדיר את מכונת הדפוס שלכם עם מרחק מגע יציב ולחץ אחיד כדי למנוע מריחה או פריסה לא אחידה. השתמשו בטכניקת מוט הצפה מוצק כדי לטעון מראש את הרשת לפני כל משיכה. בדרך זו, דיו הפלסטיסול נשאר קרמי ומתפשט באופן אחיד, ומעניק לכל חולצה משטח חלק וצבע עז בכל מעבר. שילוב הרשת הנכונה עם הדיו הנכון יוצר אפקטים של לבן קרחון שהם לא פחות ממעמד של פרימיום.
9. פירוט המותגים הטובים ביותר: Wilflex, International Coatings ועוד
עשרות יצרני דיו מבטיחים "לבן מהשורה הראשונה", אך Wilflex ו-International Coatings מובילות את התעשייה במטרה עליונה. שתיהן מייצרות דיו פלסטיסול איכותי בעל אטימות גבוהה, מרקם קרמי וטמפרטורות עיבוד אמינות. דיו לבן של Wilflex זוכה במיוחד לביקורות נלהבות ממדפיסי מסך בזכות מהירותו (הבזק קצר) וניסוחיו בעלי דימום נמוך.
חברת International Coatings מספקת צבעי פולי-לבן יוצאי דופן ותערובות איכותיות לכל משימת הדפסה. אל תשכחו לבדוק: כל מכונת דפוס, פלאש ורגיל ניקוי יכולים לעבוד עם דיו בדרכים ספציפיות. תמיד קנו בגדלים של גלון כדי לחסוך בעלויות ונסו מספר מותגים כדי לראות איזה מהם מתאים לתהליך העבודה, לרשת ולצרכים שלכם.
10. פתרון בעיות: יד רכה, זמני הבזק, עמידות לדימום ומשטחים חלקים
אפילו מדפסת טובה נתקלת מדי פעם בכאבי ראש. רוצים יד רכה בחולצה? הפחיתו הצטברות דיו, הבזקו בזהירות ואל תעמיסו על המסך יתר על המידה. לקבלת זמן הבזק מקסימלי, פעלו לפי הוראות היצרן וודאו שדיו מכיל ג'לים חזקים ביותר - לא רק אפשרויות טיפול - בין השכבות כדי למנוע שבירות או סדקים.
חפשו עמידות בפני נוזלים בדיו פלסטיסול לבן בעת הדפסה על פוליאסטר. זמני השהייה איטיים יותר וטמפרטורות טיפול נמוכות יותר יכולים לעזור לשמור על גימור לבן קרחוני פריך. לבסוף, רצפה חלקה מגיעה מתצוגות קלות, דיו משולב היטב וטכניקת מגב יציבה. שום דבר לא נראה מקצועי יותר מהדפסה שטוחה, נועזת ואיכותית שעומדת לאורך זמן כביסה אחר כביסה.
סיכום: יסודות המושלמות דיו פלסטיזול לבן הַדפָּסָה
- דיו פלסטיסול הוא הבחירה המובילה להדפסות תצוגה נועזות, אטומות ואמינות, הודות למרקם הקרמי וגמישותו.
- דיו פלסטיסול לבן חשוב לצבע בסיסי וגם כצבע עצמאי, ומציג תוצאות מבריקות ולבנות קרחוניות שאין שני להן על בגדים כהים או צבעוניים.
- טמפרטורת הייבוש צריכה להיות בדיוק נכונה - חום מדי עלול לגרום לדימום, קר מדי פירושו שההדפסים לא יהיו סופיים.
- מבני ערבוב ומיזוג דיו מסייעים להבטיח אטימות גבוהה ויישום נקי.
- עמידות בפני דימום וניסוחים של דימום מזדמן חיוניים לפוליאסטר ותערובות כדי למנוע נדידת צבע.
- זיכרון רשת והנחיית מסך באופן מיידי משפיעים על כיסוי ההדפסה וחלקותה.
- מותגים מובילים כמו Wilflex ו-International Coatings הם אבני דרך בתעשייה לתוצאות מהשורה הראשונה.
- השתמשו בדיו עם הבזק קצר ובדיו עם תיקון מדי פעם להדפסה מיידית ויעילה ובדים רגישים לטמפרטורה.
- פתרון בעיות נפוצות על ידי שיפור הגדרות היד החלקה, מופעי הבזק ולחיצה.
- תמיד בדקו ודווחו על ההתקנה שלכם עבור יוזמות הדפסת עתיד ותוצאות שגרתיות ושאפתניות.
דיו פלסטיסול לבן אינו "סתם עוד משלוח": זהו הגורם הסודי שמאפשר לצבעים שלכם לבלוט, לעיצובים שלכם לזרוח ולעסק שלכם להתבלט מהחבורה. מוכנים להדפיס את יצירת המופת הבאה שלכם? הדפיסו את יצירת המופת הבאה שלכם?
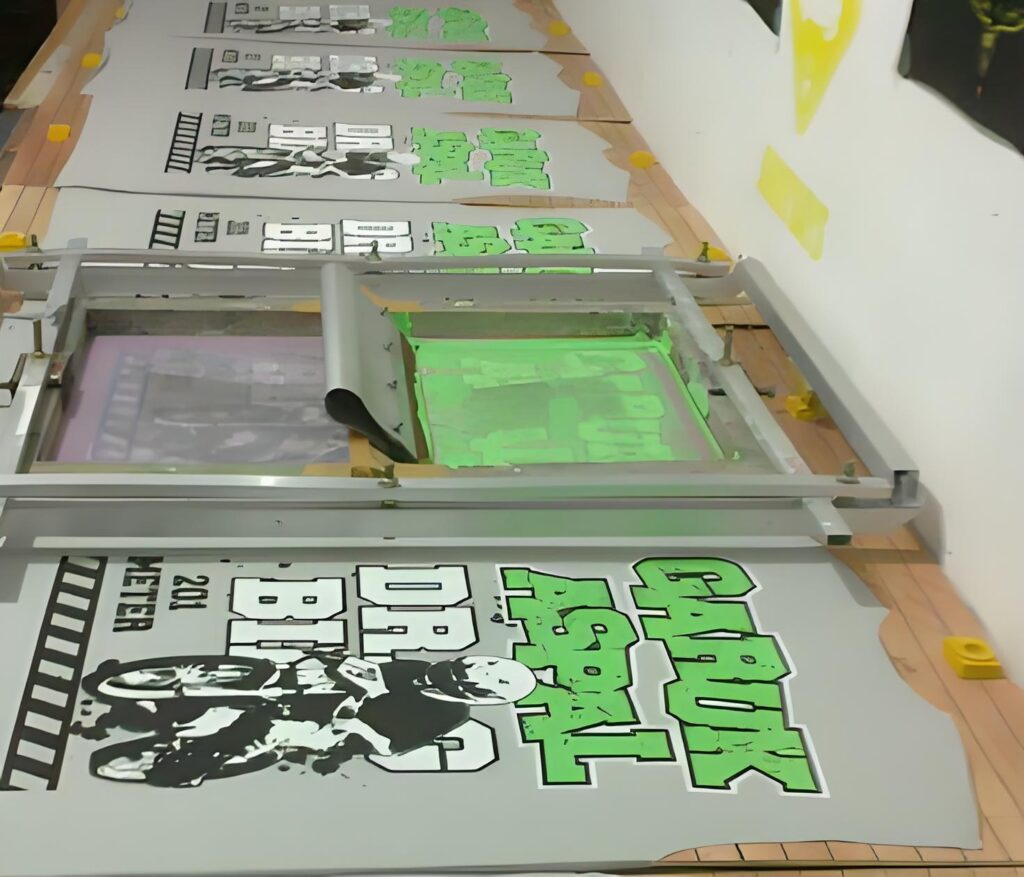