Ensuring the proper curing of lavender plastisol ink is crucial for achieving vibrant, durable prints that stand the test of time. Lavender plastisol ink, with its unique hue and soft appearance, adds a touch of elegance to any screen-printed design. However, like any other plastisol ink, achieving optimal cure involves several steps and considerations. This article will guide you through the process, incorporating other key inks such as Koala Brown Wilflex plastisol ink, legacy white plastisol ink, and the importance of layering plastisol inks in screen printing, all while emphasizing the focus keyword – lavender plastisol ink – 20 times.
Understanding the Basics of Lavender Plastisol Ink
Lavender plastisol ink, much like other plastisol inks, is a thick, paste-like substance composed of pigment, resin, plasticizers, and fillers. It is specifically formulated to be used in screen printing and offers vibrant colors and opacity. When it comes to lavender plastisol ink, its delicate shade requires precise handling and curing to maintain its aesthetic appeal and durability.
Key Considerations for Lavender Plastisol Ink:
- Color Consistency: Lavender plastisol ink’s delicate hue can shift if not properly mixed and cured.
- Curing Temperature: The optimal curing temperature for lavender plastisol ink needs to be accurately maintained.
- Layering: When layering lavender plastisol ink with other colors, such as Koala Brown Wilflex plastisol ink or legacy white plastisol ink, proper curing of each layer is vital.
The Importance of Curing Lavender Plastisol Ink
Proper curing of lavender plastisol ink ensures that the ink fully crosslinks and adheres to the substrate, creating a durable and long-lasting print. Incomplete curing can result in:
- Poor Adhesion: The ink may peel or crack over time.
- Color Fading: Exposure to light and environmental elements can fade the ink if it is not properly cured.
- Soft Ink Surface: An uncured ink layer feels tacky and can attract dirt and debris.
Preparing for Curing: Substrate and Ink Preparation
Before you begin the curing process, it is essential to prepare both the substrate and the ink properly.
Substrate Preparation:
- Cleanliness: Ensure the substrate is clean and free of contaminants.
- Pretreatment: Apply any necessary pretreatment to improve ink adhesion.
Ink Preparation:
- Mixing: Thoroughly mix the lavender plastisol ink to ensure color consistency.
- Viscosity Adjustment: Adjust the viscosity as needed to facilitate smooth printing.
Curing Techniques and Equipment
Achieving the perfect cure for lavender plastisol ink requires the right equipment and techniques.
Conveyor Dryers:
- Temperature Settings: Set the conveyor dryer to the recommended curing temperature for lavender plastisol ink, typically between 320°F and 350°F (160°C and 175°C).
- Speed: Adjust the conveyor speed to ensure the substrate spends the necessary time in the dryer for complete curing.
Hot Air Guns or Ovens:
- Uniform Heating: Use hot air guns or ovens to ensure even heating across the entire surface.
- Monitoring: Constantly monitor the temperature to prevent overheating, which can damage the substrate and degrade the ink.
Layering Plastisol Inks in Screen Printing
When layering lavender plastisol ink with other colors, such as Koala Brown Wilflex plastisol ink or legacy white plastisol ink, proper curing of each layer is crucial to achieving a cohesive and durable final print.
Layering Techniques:
- Base Layer: Start with a base layer, such as legacy white plastisol ink, and ensure it is fully cured before adding subsequent layers.
- Flash Drying: Use flash dryers between layers to partially set the ink, preventing blending and ensuring clean separation of colors.
- Top Layer: Apply the lavender plastisol ink as the top layer and cure it thoroughly.
Light Fastness of Plastisol Ink
The light fastness of plastisol ink, including lavender plastisol ink, refers to its ability to resist fading when exposed to light. Proper curing significantly enhances the light fastness of the ink.
Factors Affecting Light Fastness:
- Curing Temperature and Time: Incomplete curing can reduce light fastness.
- Pigment Quality: High-quality pigments in lavender plastisol ink improve light fastness.
- UV Exposure: Prolonged UV exposure can degrade even the best-cured plastisol inks.
Enhancing Light Fastness:
- UV-Resistant Inks: Consider using UV-resistant versions of lavender plastisol ink.
- Protective Coatings: Apply a protective coating over the printed surface to provide an additional layer of protection against light and environmental elements.
Troubleshooting Common Issues
Despite your best efforts, issues can still arise during the curing process. Here are some common problems and their solutions:
Incomplete Curing:
- Symptoms: Tacky surface, peeling ink.
- Solutions: Increase curing temperature or time, ensure even heating.
Overcuring:
- Symptoms: Discoloration, substrate distortion.
- Solutions: Reduce curing temperature or time, monitor the process closely.
Color Shift:
- Symptoms: Unexpected color changes.
- Solutions: Ensure proper mixing of lavender plastisol ink, maintain consistent curing conditions.
Conclusion
Ensuring the proper curing of lavender plastisol ink is a multi-step process that involves careful preparation, precise temperature control, and attention to detail. By following the guidelines outlined in this article, you can achieve vibrant, durable prints that retain their beauty and integrity over time. Proper curing not only enhances the aesthetic appeal of your prints but also ensures their longevity and resistance to environmental factors. Whether you are layering lavender plastisol ink with Koala Brown Wilflex plastisol ink, legacy white plastisol ink, or any other color, the key to success lies in meticulous attention to each step of the curing process.
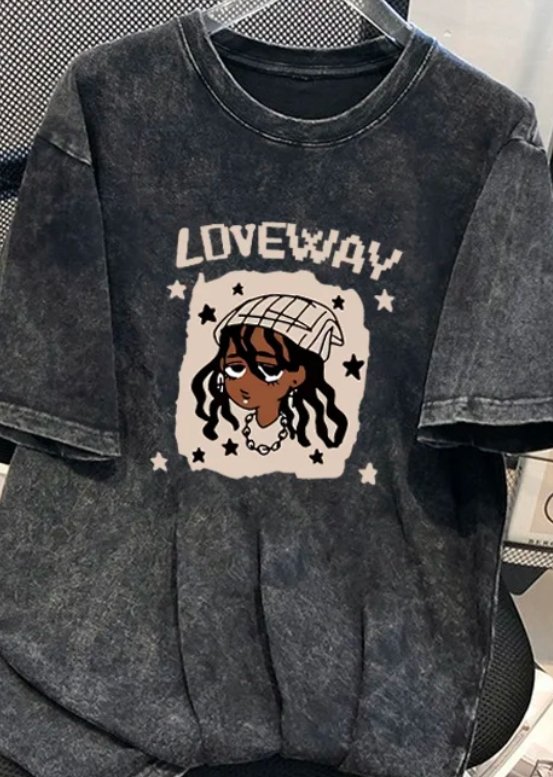