Black Plastisol ink is the cornerstone of screen printing, offering deep opacity, bold coverage, and a premium finish.
Plastisol ink is particularly popular for its rich color, exceptional durability, and effortless application. This guide reveals expert strategies, advanced techniques, and pro tips to help you achieve flawless black prints.
Table of Contents
Unlocking the Full Potential of Black Plastisol Ink
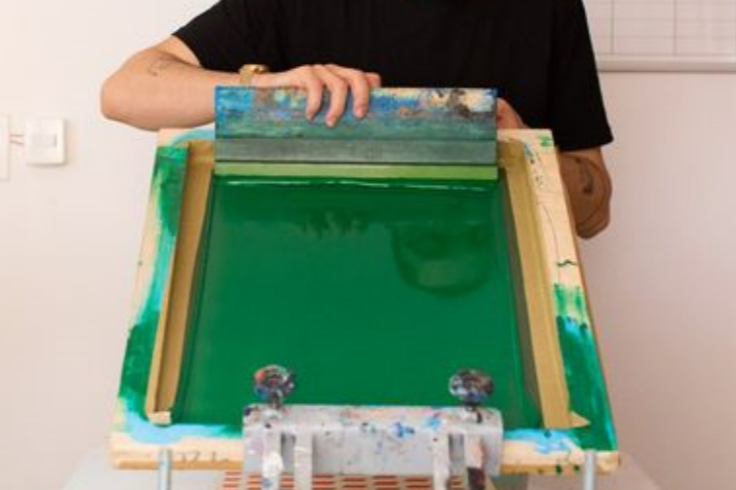
Achieving the perfect deep black print requires more than just ink—it takes skill, precision, and the right approach. Here’s how to maximize your results:
Expert Strategies for a Perfect Black Print:
- Opt for Ultra-High Opacity Ink: Use black inks with premium pigmentation to ensure dense, even coverage.
- Master the Art of Curing: Proper curing prevents cracking and enhances durability. Achieving the correct temperature is crucial to ensure the print doesn’t feel too stiff.
- Choose the Right Screen Mesh: A 110 to 230 mesh count ensures the best ink deposit for your design and helps achieve a balanced texture.
- Fine-Tune Your Squeegee Technique: Adjust pressure and angle for consistent ink distribution. Avoid too much pressure, which could cause unwanted ink buildup.
- Control Flash Drying Time: Over-flashing can lead to poor adhesion between layers, affecting print quality. Flash curing between ink layers can help improve opacity.
- Monitor Ink Layer Thickness: Excess ink can lead to a rubbery feel, while too little may reduce opacity. Finding the right balance is key to achieving crisp prints.
Mastering Black on Black: Techniques for a Bold Look
Printing black on black can be tricky, but with the right techniques, you can achieve sharp, high-contrast results. Here’s how to make your prints stand out:
- Maximize Opacity with High-Pigment Ink: Specialized black inks provide rich coverage on dark fabrics and make sure the black stands out against the black fabric.
- Use an Underbase for Contrast: A gray or discharge underbase helps the black ink pop, ensuring that the design doesn’t get lost on dark backgrounds.
- Enhance Depth with Double Printing: Printing two layers of black ink creates a richer, more defined look, providing both opacity and dimension to the design.
- Experiment with Matte and Gloss Finishes: Additives allow for custom visual effects. For example, a matte finish can provide a classic and sleek design, while a gloss finish offers a vibrant, eye-catching appearance.
- Try Puff Additives for a Raised Effect: Puff additives create a dimensional, standout design by raising the ink once cured.
- Use Highlight Techniques: Mixing in reflective or metallic elements can subtly differentiate the print. These highlights will catch light differently and give your design a distinctive look.
Precision Printing: Achieving Crisp, Detailed Black Designs
When printing intricate details with black ink, precision is key. Follow these essential steps for sharp, high-definition prints:
- Use a Fine Mesh Screen: A 200 to 305 mesh count preserves fine details, allowing for clear, crisp lines in complex designs.
- Optimize Ink Flow: Low-viscosity formulas prevent clogging and enhance clarity. Adjusting the ink consistency with an appropriate thinner ensures smooth flow.
- Avoid Ink Build-Up: Adjust stroke pressure to maintain a consistent print surface. Too much ink will result in excess thickness and loss of detail.
- Perfect Your Flash Drying Technique: Proper flash curing between layers keeps edges crisp and clean, preventing smudging or ink mixing.
- Use a Sharp Squeegee Blade: A fresh, sharp squeegee ensures precision in every pass. Using a dull blade can distort intricate designs.
- Apply Even Pressure: Uneven pressure can distort designs, affecting print consistency. Practice uniform pressure to avoid print inconsistencies.
Heat Transfers with Black Plastisol: A Versatile Printing Alternative
Plastisol ink isn’t limited to direct screen printing—it’s also perfect for heat transfers, offering flexibility and precision. The heat transfer process allows for larger volume production with the same quality results as direct prints.
Heat Transfer Process:
- Prepare and Mirror Your Artwork: Always ensure the artwork is mirrored before printing to ensure the correct orientation.
- Use the Right Transfer Paper: Use a high-quality transfer paper that allows for proper adhesion of the plastisol ink to the garment.
- Achieve Optimal Curing: Maintain consistent curing conditions for durable transfers. Ensure the ink is fully cured on the transfer paper before applying to garments.
- Apply with Precision: The correct heat and pressure settings ensure a long-lasting print. Adjust the pressure based on fabric type to avoid unwanted marks or fabric damage.
- Peel at the Right Time: Follow the recommended peel methods—hot, warm, or cold—for optimal results.
- Store Transfers Correctly: Keeping transfers in a dry, cool environment extends their usability and ensures they remain in perfect condition.
Why Black Plastisol Ink Stands Above the Rest
Black Plastisol ink offers a number of advantages over other types of inks, including:
- Unmatched Opacity: Deep, rich pigments that ensure standout prints, even on dark fabrics.
- Exceptional Durability: Resists fading and wear through multiple washes, making it perfect for long-lasting apparel and designs.
- Smooth and Effortless Application: The consistency of Plastisol ink makes it ideal for both beginners and professionals, providing smooth coverage with minimal effort.
- Versatility Across Fabrics: Works exceptionally well on cotton, polyester, and blended textiles, making it suitable for a wide range of garment types.
- Eco-Conscious Formulations: Low-VOC and phthalate-free inks ensure safety and sustainability for both the user and the environment.
- Consistent Batch Quality: Every batch is carefully tested for uniform color and performance, ensuring that every print is of the highest quality.
Boost Efficiency with Low-Cure Black Plastisol Ink
Low-cure Black Plastisol ink enhances productivity while reducing costs in the following ways:
- Accelerating Production: Cures at lower temperatures, reducing processing time and speeding up your workflow.
- Cutting Energy Costs: Requires less heat, which improves overall efficiency and lowers energy consumption.
- Delivering a Softer Feel: Lower curing temperatures result in a smoother, more comfortable print, ideal for clothing and wearable products.
- Reducing Fabric Scorching: Lower heat application protects delicate garments and prevents discoloration.
- Enhancing Ink Flexibility: Retains elasticity, preventing cracks or damage over time, especially after multiple washes.
Where to Find Premium Black Plastisol Ink
Searching for premium Black Plastisol ink suppliers? There are many industry-leading suppliers worldwide, providing custom formulations and expert assistance to meet your specific screen printing needs.
Whether you’re printing for a large-scale commercial project or a small boutique, choosing the right supplier is crucial to ensure quality results and consistent performance. It’s always worth considering customer reviews, industry reputation, and product consistency when selecting a supplier.
