Mixing screen printing ink is an essential skill for any print shop, allowing for a wide range of colors and effects without the need for a vast inventory of pre-mixed inks. Whether you’re working with plastisol inks, water-based inks, or specialty inks, understanding how to mix them can help you achieve the exact shades and tones required for your projects. This guide will walk you through the basics of mixing screen printing ink, offer tips for avoiding common pitfalls, and explore the types of colors you can create.
Why Mix Screen Printing Ink?
There are many reasons why you might want to mix screen printing ink in your shop. Sometimes, a job may call for a color that you don’t typically stock, or you might have a one-time project requiring a unique shade. Mixing inks allows you to create these colors on-demand without ordering custom inks, which can save time and reduce costs.
Additionally, mixing screen printing inks can help you reclaim leftover ink by combining it to create new, usable colors. This approach not only maximizes your ink inventory but also reduces waste.
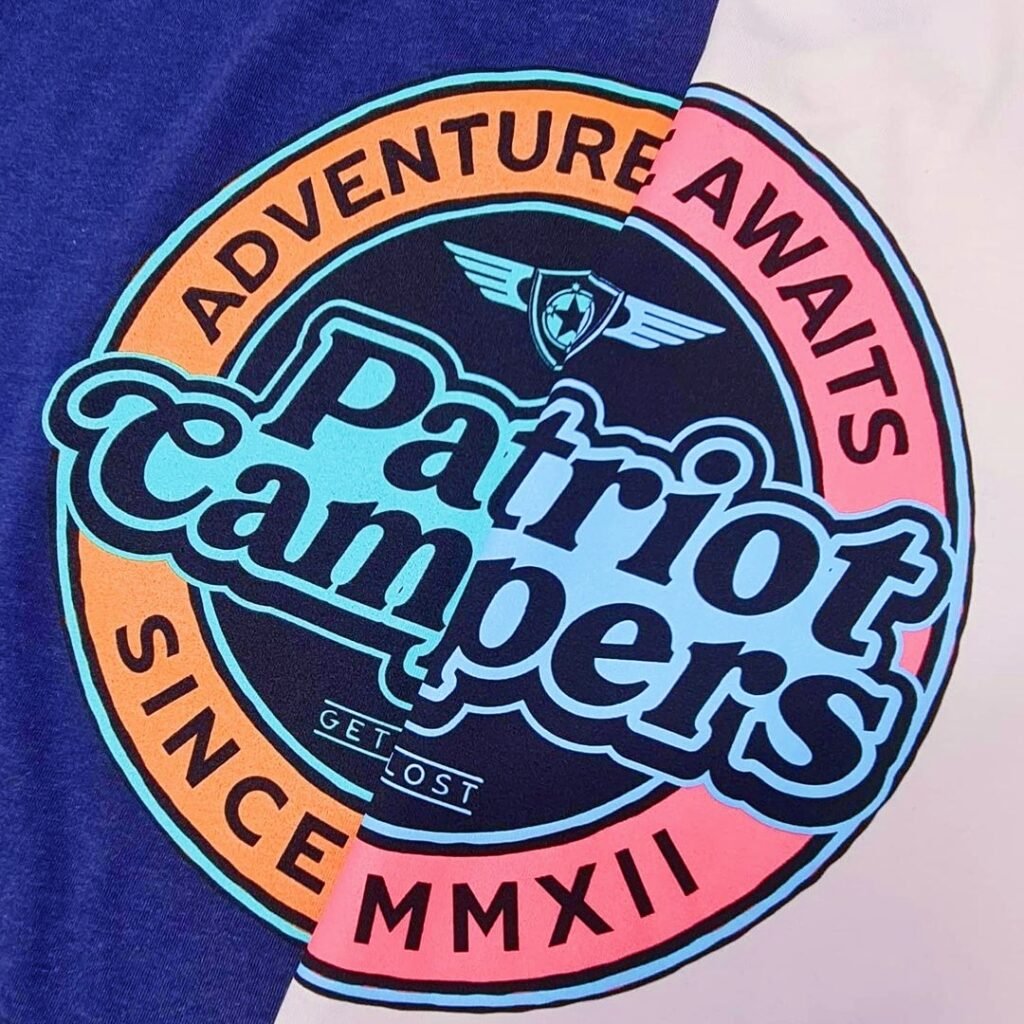
Understanding the Basics of Ink Mixing
Before diving into the process of mixing screen printing ink, it’s important to understand the basics of color theory. Plastisol ink, ink plastisol, and screen printing paint all follow the principles of subtractive color mixing. The primary colors in this system are red, yellow, and blue. By mixing these colors, you can create a wide range of secondary and tertiary colors.
- Primary Colors: Red, Yellow, Blue
- Secondary Colors: Orange (Red + Yellow), Green (Yellow + Blue), Purple (Blue + Red)
- Tertiary Colors: Created by mixing primary and secondary colors (e.g., Red + Green = Brown)
By using these principles, you can mix plastisol screen printing ink to create nearly any color you need.
Tools Needed for Mixing Screen Printing Ink
Before you start mixing screen printing ink, gather the necessary tools to ensure accuracy and consistency:
- Mixing Sticks: For stirring and combining inks.
- Scale: To measure ink quantities precisely, especially when following color mixing formulas.
- Color Charts: A reference guide for creating specific colors.
- Mixing Containers: Small, clean containers for mixing and storing custom ink blends.
- Ink Mixing Software: Some ink suppliers offer computerized mixing software for precise color matching.
Mixing Plastisol Inks
Plastisol inks are among the most commonly mixed inks in screen printing. They are versatile and can be easily blended to create a wide range of colors. When mixing plastisol inks, it’s crucial to follow some key guidelines to ensure you achieve the desired color and maintain the ink’s properties.
Step 1: Choose Your Base Colors
Start by selecting the base colors needed for your mix. If you want to create a specific shade, use primary colors and mix them in varying proportions. For example, to create purple, mix red and blue screen printing ink plastisol in equal parts. Adjust the ratio of each color to achieve the desired hue.
Step 2: Measure and Mix
Use a scale to measure the exact amount of each color to ensure consistency, especially if you need to replicate the color later. Place the base ink colors into your mixing container and use a mixing stick to blend the inks thoroughly. Be sure to mix slowly and evenly to avoid air bubbles and achieve a smooth, uniform color.
Step 3: Test and Adjust
After mixing, test the ink on a small fabric swatch to see how the color looks once printed and cured. Plastisol inks can appear different once they’re applied to fabric and cured, so this step is crucial. Adjust the mix as needed by adding more of a base color or a tinting base to lighten or darken the ink.
Creating Custom Colors
Mixing screen printing inks allows you to create an array of custom colors beyond the standard palette. Here are some common color mixes you can create:
- Pastel Shades: To create pastel colors, mix a small amount of color ink with a white plastisol base. Adding white will lighten the color and give it a softer appearance.
- Earth Tones: Combine primary and secondary colors to achieve earthy tones. For example, mix green and red to create a warm, natural brown.
- Bright and Vibrant Colors: Use primary colors at full strength or mix them with minimal amounts of other inks to maintain vibrancy.
Mixing Specialty Inks
In addition to standard plastisol inks, you can also mix specialty inks like water-based screen printing ink and silk screen printing ink. However, these inks have different properties that require special attention.
Water-Based Screen Printing Ink
Water-based screen printing ink is known for its soft feel on fabric. When mixing water-based inks, it’s important to remember that they can dry out quickly, so mix only the amount needed for the job at hand. Water-based inks can also be mixed with a retarder to extend their open time and improve their workability.
Specialty Plastisol Inks
Specialty plastisol screen printing ink, such as glow-in-the-dark or metallic inks, can also be mixed with other plastisol inks to create unique effects. However, mixing these specialty inks requires careful consideration of their properties to ensure they retain their special effects. For example, adding too much regular plastisol ink to metallic ink can diminish its reflective quality.
Tips for Successful Ink Mixing
- Mix in Small Batches: Start with small batches to avoid wasting ink if the color isn’t exactly right. You can always scale up the mix once you’re satisfied with the result.
- Document Your Mixes: Keep a record of the ratios and amounts used for each custom color mix. This documentation will make it easier to replicate the color for future projects.
- Use an Ink Mixing System: Some suppliers offer ink mixing systems with computerized software to help you achieve precise color matching. These systems can save time and improve accuracy.
- Avoid Over-Mixing: Over-mixing can introduce air bubbles into the ink, which can affect print quality. Mix the ink until it is uniform, but avoid excessive stirring.
Common Challenges in Mixing Screen Printing Ink
Mixing screen printing ink can be challenging, especially when trying to achieve a specific shade. Here are some common challenges and how to address them:
Achieving Consistent Colors
Consistency is key when mixing inks. Slight variations in the ratio of colors can lead to different shades. To maintain consistency, use precise measurements and follow your documented color recipes.
Avoiding Overuse of White
While adding white to ink for screen printing can create pastel shades, it’s easy to overdo it, resulting in an excessive amount of ink. To prevent this, always start with a base amount of white and gradually add color to achieve the desired shade.
Balancing Opacity
When mixing screen printing inks like plastisol, be mindful of the ink’s opacity. Adding too much color to an opaque base can affect the ink’s ability to cover dark fabrics. If you need to adjust the opacity, consider adding an opacity modifier designed for screen printing inks.
Using Mixed Ink in Production
Once you’ve mixed your screen printing ink, it’s ready for use in your print run. Test the ink on a sample fabric first to ensure it produces the desired color and texture. After printing, cure the ink properly, as curing affects the final appearance of the color, particularly with plastisol print inks.
Conclusion
Mixing screen printing ink is an invaluable skill for screen printers, offering flexibility in color creation and efficient use of ink supplies. Whether you’re working with plastisol inks, water-based inks, or specialty inks, understanding the basics of ink mixing and following best practices will help you achieve consistent, vibrant colors for your projects.
From creating custom shades to reclaiming leftover ink, mixing inks can enhance your screen printing capabilities and allow you to cater to a broader range of client requests. With practice and attention to detail, you can master the art of mixing screen printing ink to produce stunning, professional results.