When it comes to printing on leather, durability and quality are paramount. Among the various ink options available, plastisol ink stands out for its vibrant colors, flexibility, and resilience. This article delves into the durability of printing on leather with plastisol ink, exploring its application, benefits, and considerations. By understanding how this process works, you can make informed decisions about your leather printing needs.
The Basics of Plastisol Ink
Plastisol ink is a suspension of plastic particles in a liquid carrier. When heated, these particles coalesce, forming a smooth, durable finish. This type of ink is widely used in screen printing, particularly for fabrics and, increasingly, for leather goods. Plastisol ink’s unique properties make it an ideal choice for printing on leather with plastisol ink, offering a combination of durability, vibrancy, and versatility.
Application Techniques: Pressing with Plastisol Inks
One of the key aspects of using plastisol ink on leather is the application process. Pressed with plastisol inks, the ink is forced through a screen mesh onto the leather surface. This method ensures even coverage and deep penetration into the leather’s pores, enhancing durability. The pressing action also helps the ink adhere better to the leather, minimizing the risk of cracking or peeling over time.
Pricing on One Stroke Ink Plastisol can vary depending on factors such as ink color, quantity, and brand. However, the investment in high-quality plastisol ink is worth it for the long-lasting results it delivers. When shopping for ink, look for primary plastisol ink packs that offer a wide range of colors, including white, which is essential for creating vibrant prints on darker leather surfaces.
The Benefits of Printing on Leather with Plastisol Ink
Vibrant Colors and Design Versatility
Plastisol ink is renowned for its vibrant color reproduction. Whether you’re aiming for bold, primary hues or intricate, detailed designs, plastisol ink delivers. This makes it an excellent choice for printing on leather with plastisol ink, where the ability to showcase intricate designs and vibrant colors is crucial. The ink’s opacity also allows for better color coverage, especially when printing white or other light colors on dark leather backgrounds using printing white plastisol ink.
Durability and Flexibility
Durability is a hallmark of plastisol ink. Once heated and set, the ink forms a flexible, plastic-like layer that is resistant to cracking, fading, and wear. This resilience makes it perfect for leather, which can undergo significant stress and wear over time. Plastisol ink’s flexibility ensures that prints remain intact and look great, even on leather items that are frequently bent or stretched.
Environmental Considerations
While traditional screen printing inks may contain harmful chemicals, many modern plastisol inks are formulated to be more environmentally friendly. This shift towards eco-conscious manufacturing practices makes printing on leather with plastisol ink a more sustainable option. Look for inks with low VOC (Volatile Organic Compounds) emissions and those that are compliant with environmental regulations to minimize your ecological footprint.
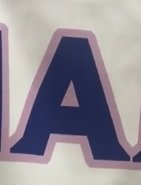
Challenges and Considerations
Despite its many advantages, printing on leather with plastisol ink comes with its own set of challenges and complexities that require careful consideration. While plastisol ink is known for its durability, vibrant color reproduction, and ability to adhere well to various surfaces, leather presents unique difficulties due to its texture, flexibility, and natural oils. Achieving a consistent print on leather often requires specialized techniques, precise temperature control, and the use of appropriate primers or additives to ensure proper adhesion. Additionally, the risk of cracking or peeling increases if the ink layer is too thick or if the leather is subjected to frequent bending or stretching. Environmental factors, such as humidity and heat, can also impact the curing process, making it essential to adjust settings accordingly. Lastly, the natural variability in leather types—ranging from full-grain to synthetic—can significantly affect the print outcome, necessitating thorough testing and preparation for each specific project.
By addressing these challenges with proper planning and expertise, the benefits of plastisol ink can be fully leveraged to create stunning and long-lasting designs on leather surfaces.
Leather Type and Preparation
Different types of leather respond differently to plastisol ink. Smooth, finished leathers may require special pretreatment to ensure the ink adheres properly. In contrast, more porous leathers like suede may absorb the ink more readily but may also require sealing to protect the print. Proper leather preparation, including cleaning and priming, is crucial for achieving optimal results.
Ink Viscosity and Drying
Plastisol ink’s viscosity, or thickness, can affect its application and final appearance. Too thick, and the ink may not flow through the screen evenly; too thin, and it may not adhere well to the leather. Adjusting the ink’s viscosity and ensuring proper drying conditions are essential for achieving a high-quality print.
Curing Process
The curing process is critical in determining the durability of printing on leather with plastisol ink. The ink must be heated to the correct temperature for a sufficient amount of time to ensure it fully coalesces and forms a durable, flexible finish. Inadequate curing can result in prints that are prone to cracking, fading, or peeling.
Practical Applications and Case Studies
To illustrate the durability and versatility of printing on leather with plastisol ink, let’s look at a few practical applications and case studies:
Custom Leather Goods
Custom leather goods, such as wallets, handbags, and belts, often feature intricate designs and branding. Plastisol ink’s ability to produce vibrant, detailed prints makes it an ideal choice for these applications. The durability of the ink ensures that the prints remain clear and vibrant, even with regular use and wear.
Automotive Interiors
The automotive industry frequently uses leather for seating, dashboards, and door panels. Plastisol ink’s resilience and flexibility make it suitable for printing logos, branding, and decorative patterns on these surfaces. The ink’s ability to withstand exposure to sunlight, heat, and cold makes it a reliable choice for automotive interiors.
Fashion Accessories
Fashion accessories like shoes, jackets, and hats often incorporate leather elements. Plastisol ink allows designers to create unique, eye-catching prints that stand out and hold up well to the rigors of daily wear.
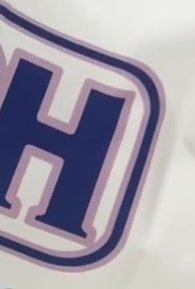
Conclusion
In summary, printing on leather with plastisol ink offers a combination of durability, vibrancy, and versatility that is unmatched by other ink types. With proper application techniques, ink selection, and leather preparation, plastisol ink can produce stunning, long-lasting prints on leather goods. Whether you’re a custom leather goods manufacturer, automotive interior designer, or fashion accessory creator, plastisol ink can elevate your products with stunning visual appeal and robust durability.