Conclusion
Using silkscreen ink for fabric offers endless possibilities for creating vibrant, long-lasting prints on textiles. By mastering the techniques and tips outlined in this guide, you can elevate your Silk Screen Printing projects, whether you’re using plastisol screen printing ink, water-based screen printing ink, or specialty inks like reflective screen printing ink. Remember to experiment, test your prints, and continuously refine your techniques to achieve the best results.
Silkscreen Ink for Fabric: Techniques and Tips
Silkscreen printing, also known as Silk Screen Printing, has been a trusted method for creating stunning designs on fabrics for decades. Whether you’re printing t-shirts, tote bags, or specialty items, using silkscreen ink for fabric is one of the most versatile and efficient ways to achieve vibrant, durable prints. But to get the best results, it’s important to understand the different techniques, types of inks, and tips to ensure a successful print every time.
In this comprehensive guide, we’ll explore the various methods of Silk Screen Printing, the types of silkscreen ink for fabric, and expert tips for achieving top-quality prints. Whether you’re a beginner or an experienced printer, this guide will provide valuable insights to take your fabric printing to the next level.
Understanding Silkscreen Ink for Fabric
Silkscreen ink for fabric is specifically designed to adhere to textile fibers, ensuring that the prints are durable, vibrant, and long-lasting. Unlike paper or plastic, fabric presents a unique challenge because it is flexible and absorbent. To achieve consistent, high-quality results, using the right type of silk screen printing ink is essential.
1. Plastisol Screen Printing Ink
Plastisol screen printing ink is one of the most popular options for printing on fabric. It offers vivid colors and excellent opacity, making it suitable for printing on both light and dark garments. Plastisol ink does not dry unless heat-cured, which makes it easier to work with during the printing process. This ink sits on top of the fabric, giving it a slightly raised texture, which many printers prefer.
When using plastisol screen printing ink, it’s important to cure the ink properly by heating it to around 320°F (160°C). This ensures the ink bonds well to the fabric, making it resistant to washing and wear.
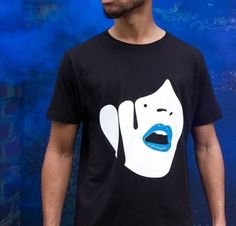
2. Water-Based Screen Printing Ink
Water-based screen printing ink is another popular option for fabric printing. Unlike plastisol, this ink penetrates the fibers of the fabric, creating a softer finish that feels lighter on the garment. It is especially popular for printing on lighter-colored fabrics.
One of the main advantages of water-based screen printing ink is its eco-friendliness. Many printers prefer it because it contains fewer harmful chemicals and creates less environmental impact. However, water-based ink screen printing requires careful attention during the drying process, as it dries more quickly on screens and needs to be fully air-cured or heat-set to prevent smudging or fading.
3. Specialty Inks
For those looking to create unique effects, there are a variety of specialty silkscreen ink for fabric options available, including:
- Reflective screen printing ink: Adds a reflective finish to the print, making it visible in low light.
- Puff ink screen printing: Creates a raised, 3D effect when heat-cured.
- Glow in the dark screen printing ink: Absorbs light and glows in dark settings.
Each of these specialty inks can be layered with silkscreen ink for fabric to create custom designs with added texture and visual impact.
Techniques for Using Silkscreen Ink for Fabric
To achieve the best results when using silkscreen ink for fabric, it’s crucial to master the right techniques. From selecting the right mesh size to curing the ink properly, each step can make a big difference in the final outcome.
1. Choosing the Right Screen Mesh
The mesh size of the screen plays a key role in how the silk screen printing ink is deposited on the fabric. The higher the mesh count, the finer the print, while a lower mesh count allows more ink to pass through, which is useful for printing on thicker fabrics or when using specialty inks like puff ink for screen printing.
For most fabric ink screen printing projects, a mesh size of 110 to 160 is ideal for plastisol screen printing ink, while higher mesh counts (180-230) are better for water-based screen printing ink or detailed designs.
2. Pre-Treating the Fabric
Before printing, it’s essential to pre-treat the fabric. This can involve washing the fabric to remove any oils, chemicals, or residues that could interfere with ink adhesion. Pre-treating the fabric also helps to prevent shrinkage, ensuring that the print stays true to size after washing.
In some cases, especially when using water based screen printing ink, applying a fabric softener can help the ink penetrate the fibers more effectively, creating a softer print.
3. Layering Multiple Colors
When working with multiple colors in Silk Screen Printing, layering the inks correctly is critical. You should flash cure each layer before applying the next to prevent the colors from blending or smudging. This is particularly important when using specialty inks like glow in the dark screen printing ink or reflective screen printing ink. Flash curing involves briefly heating the ink to set it without fully curing it, allowing for crisp, clean layers.
4. Curing the Ink
Curing is one of the most important steps in the screen printing process. Whether you’re using plastisol screen printing ink, water-based screen printing ink, or specialty inks, proper curing ensures that the print will be durable and withstand repeated washing. For plastisol ink, use a heat press or conveyor dryer to reach the appropriate temperature for curing. For water-based screen printing ink, air drying followed by heat setting is typically required to lock in the print.
Tips for Achieving the Best Results with Silkscreen Ink for Fabric
Here are some expert tips to help you get the best results when working with silkscreen ink for fabric:
1. Keep Your Screens Clean
Maintaining clean screens is essential for achieving sharp, high-quality prints. Ink can build up on the screen over time, especially with water-based screen printing ink, which dries quickly. Be sure to clean your screens regularly to prevent dried ink from clogging the mesh.
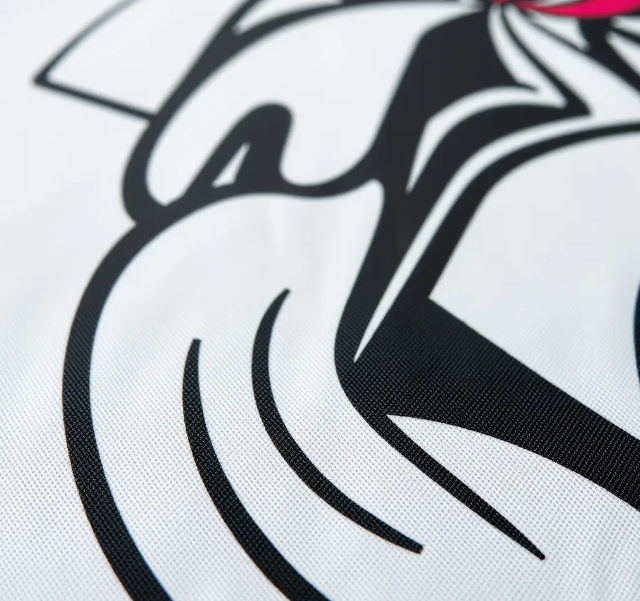
2. Use the Right Squeegee Pressure
Applying the right amount of pressure when pulling the squeegee across the screen is critical for even ink distribution. Too much pressure can cause the ink to bleed, while too little pressure may result in incomplete prints. Practice applying consistent pressure to achieve smooth, even prints.
3. Experiment with Specialty Inks
Don’t be afraid to experiment with specialty inks like reflective screen printing ink or puff ink screen printing to create unique textures and effects. Specialty inks can be combined with regular silkscreen ink for fabric to add dimension to your designs. For example, adding a layer of glow in the dark screen printing ink on top of your design can make it stand out in both daylight and dark environments.
4. Test Your Prints
Before printing your entire batch, always test your design on a sample fabric. This allows you to check for any issues with ink adhesion, color consistency, or curing. Testing is especially important when using a combination of inks, such as screen print ink for silicone wristbands and silkscreen ink for fabric.
Advanced Silkscreen Ink Techniques
For those looking to take their silkscreen ink for fabric techniques to the next level, consider trying the following advanced methods:
1. Discharge Ink Screen Printing
Discharge ink screen printing is a technique used to remove the dye from the fabric, leaving a soft, natural print. This method is ideal for creating vintage or faded designs. Discharge ink can be combined with other screen printing inks to add depth to your designs.
2. Layering Reflective Ink
Layering reflective screen printing ink on top of regular fabric screen printing ink can create prints that shine brightly when exposed to light. This technique is commonly used for safety apparel, outdoor gear, and fashion items designed for night-time visibility.
3. Metallic Effects with Gold Inks
If you’re looking to add a luxurious touch to your prints, try using metallic gold screen printing ink. This ink provides a shiny, reflective finish that catches the light, making your designs stand out.