Innehållsförteckning
Plastisol Ink: Essential Guide to Screen Printing Techniques and Benefits
Screen printing is one of the most popular methods for printing on textiles, and plastisol ink is the go-to choice for many professionals. Its durability, versatility, and ease of use make it the industry standard for printing on fabrics, particularly cotton and polyester. This guide explores the essential techniques, advantages, and best practices when working with plastisol ink to ensure high-quality prints.
Vad är Plastisol Ink?
Plastisol ink is a PVC-based ink, commonly used in plastisol inks for screen printing. that does not contain water or solvents, ensuring compatibility with plastisol screen printing. Unlike water-based inks, plastisol ink remains liquid until it is cured under heat, typically at temperatures around 320°F (160°C). This characteristic makes plastisol an excellent choice for screen printing, as it does not dry on screens and allows for easy manipulation during production.
Key Features of Plastisol Ink
- Does not dry until cured: Unlike water-based inks, plastisol stays wet until exposed to high temperatures, allowing for longer work times.
- Bright and opaque colors: Plastisol inks are highly pigmented, producing vibrant prints, even on dark fabrics.
- Excellent durability: Prints resist cracking, peeling, and fading over time, making them ideal for garments subjected to frequent washing.
- Layering capability: Plastisol inks can be stacked for multi-color designs without drying between layers.
- Easy to use: No special additives or handling requirements are needed for most applications.
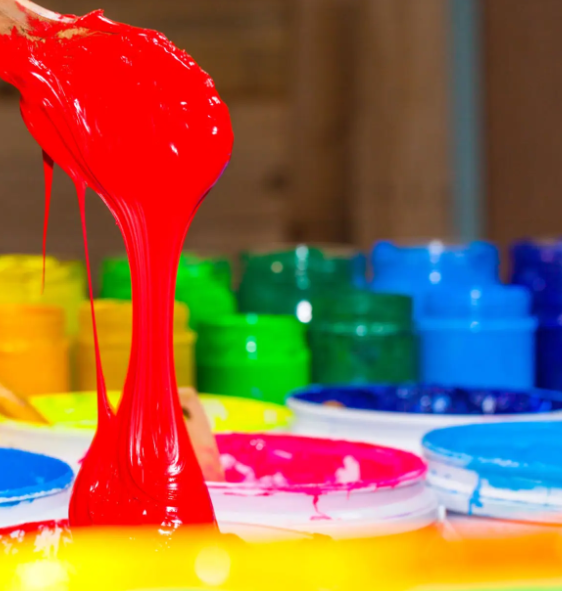
Techniques for Printing with Plastisol Ink
To achieve high-quality screen prints using plastisol ink, it’s important to master the essential techniques, including preparation, printing, and curing.
1. Preparing for Screen Printing
Choosing the Right Mesh Count
De maskantal of the screen determines how much ink is deposited onto the fabric. Lower mesh counts allow for heavier ink deposits, while higher mesh counts produce finer details.
- Lower mesh (86-110): Best for thick ink deposits, bold graphics, or specialty inks like puff, glitter, and white plastisol.
- Medium mesh (125-160): Ideal for standard plastisol printing, offering a balance between detail and ink coverage.
- Higher mesh (200-305): Used for fine details and halftone images.
Screen Coating and Exposure
- Coat the screen with a high-quality emulsion suitable for printing plastisol ink. that is compatible with plastisol ink.
- Ensure proper exposure time to create sharp stencil edges and prevent underexposure or overexposure.
- Proper drying and curing of the emulsion before printing is crucial to avoid breakdowns during printing.
2. Printing Process
Ink Application and Printing Technique
- Använd a medium to firm squeegee (typically 70 durometer) to push the ink through the screen.
- Print with a consistent pressure and angle (45°) to ensure even ink distribution.
- Flooding the screen with ink between prints prevents ink from drying in the mesh and helps with consistency.
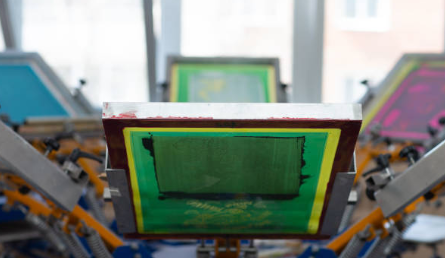
Underbase Printing for Dark Garments
When printing on dark-colored fabrics, a white or light-colored underbase is often required to make the colors pop. This involves:
- Printing a white underbase layer first.
- Flash-curing the underbase before applying additional colors.
- Printing the desired colors over the cured underbase.
3. Curing Plastisol Ink
Proper curing is essential for long-lasting prints. Plastisol ink must reach 320°F (160°C) to fully cure. If under-cured, prints will crack and wash out; if over-cured, the fabric may scorch, and the ink could become brittle.
Methods of Curing
- Conveyor Dryer: Ideal for large-scale production, providing consistent heat across the entire print.
- Flash Dryer: Used for spot curing and small-batch printing.
- Heat Press or Heat Gun: Can be used in small operations but requires careful temperature monitoring.
To ensure proper curing:
- Använd a temperature gun or heat probe to verify the ink reaches the correct temperature.
- Test the wash durability of prints made with white ink before mass production.
Benefits of Using Plastisol Ink
Plastisol ink offers numerous advantages, making it a preferred choice in the screen printing industry.
1. Superior Print Quality
Plastisol inks produce sharp, vibrant, och highly opaque prints. The ink sits on top of the fabric rather than soaking in, which results in a vibrant finish suitable for screen printing plastisol inks for screen printing. bold and bright färger.
2. Long Shelf Life and Easy Handling
Since plastisol ink does not air-dry, it has a long shelf life and can be stored without special precautions. It allows screen printers to work at their own pace without worrying about ink drying in the screen.
3. Versatility Across Fabrics
Plastisol ink is compatible with cotton, polyester, blends, and even non-textile surfaces when properly prepared. Special additives can be used to improve adhesion and elasticity for stretchable materials.
4. Special Effects and Additives
Plastisol ink can be customized using various additives and specialty inks:
- Puff Ink: Expands when cured, creating a raised texture.
- Glitter & Metallic Inks: Adds a shimmering effect to prints.
- Glow-in-the-Dark Ink: Absorbs light and glows in dark conditions, making it ideal for specialty screen printing ink.
- Stretch Additive: Enhances elasticity for athletic wear.
- Low Bleed Additive: Prevents dye migration when printing on polyester.
Common Challenges and Troubleshooting
Even experienced printers may face challenges when working with screen printing plastisol ink. Here are solutions to common issues:
Problem with the application of screen printing ink. | Cause | Solution |
---|---|---|
Ink cracking after washing | Under-curing or improper ink deposit | Ensure proper curing at 320°F and use the correct mesh count. |
Ink not adhering properly | Fabric treatment or ink type mismatch | Use proper pre-treatment or an adhesion additive. |
Ink too thick or stiff | Cold temperatures or old ink | Stir the ink well and warm it slightly before use. |
Dye migration (bleeding) can be problematic when using certain types of ink. | Printing on polyester fabrics | Use a low-bleed ink or a barrier underbase. |
Slutsats
Plastisol ink is a powerful and reliable choice for screen printing, offering durability, versatility, and ease of use. By mastering the right techniques—choosing the correct mesh count, using proper printing methods, ensuring adequate curing, and troubleshooting common issues—screen printers can produce high-quality, long-lasting prints. Whether you’re printing custom T-shirts, athletic wear, or promotional items, plastisol ink provides the best results for professional-grade screen printing.
By leveraging the benefits of plastisol ink and following best practices, you can elevate your screen printing projects to a professional level. Whether you’re a beginner or an experienced printer, understanding and perfecting plastisol ink techniques will help you achieve outstanding, durable, and visually appealing prints.