The Advantages and Limitations of Plastisol Ink in Screen Printing
In the printing industry, Plastisol Ink stands out for its unique properties and wide range of applications. Particularly in screen printing, Plastisol Ink has become a top choice among suppliers and printers due to its exceptional printing results and stability. This article delves into the advantages and limitations of Plastisol Ink in screen printing.
Basic Characteristics of Plastisol Ink
Appearance and Composition
Plastisol Ink, also known as plasticizer-containing ink or oil-based paste, is a non-solvent-based ink. It appears as a paste, consisting primarily of resin (without solvents or water), pigments, and other additives. With a solid content of up to 100%, this ink exhibits thixotropy, meaning it is thick at rest but becomes thinner when stirred. This characteristic enables it to maintain good flowability and adhesion during the printing process.
Application and Curing
Plastisol Ink is suitable for both manual and mechanical printing, capable of producing various special effects such as color blocking, flat, three-dimensional right angles, rounded corners, stone, and bark textures. Importantly, this ink does not dry at room temperature and requires heating to 150°C-180°C for 1-3 minutes to cure completely. After curing, the ink is elastic, with a surface that does not powder, ensuring the durability and aesthetics of the printed product.
Advantages of Plastisol Ink in Screen Printing
Exceptional Printing Results
High Color Fidelity: Plastisol Ink boasts high color fidelity, accurately reproducing colors from design drafts, resulting in vivid and realistic prints. This feature is particularly suitable for applications requiring high color accuracy, such as color-separated character prints.
Elasticity and Feel: With fine resin particles, Plastisol Ink offers excellent elasticity and a soft touch after printing, surpassing traditional rubber-based inks in comfort. This characteristic makes it popular in high-end apparel printing, especially for sportswear, casual wear, and other textiles requiring good wearability.
Strong Adhesion: After curing at high temperatures, Plastisol Ink adheres firmly to the substrate, withstanding wet washing up to level 5 and dry rubbing up to level 4, ensuring prints remain vibrant even after multiple washes and frictions.
Cost and Efficiency
Low Plate-Making Costs: Compared to other printing methods, screen printing has relatively low plate-making costs, providing more options for small and medium-sized enterprises. Combined with Plastisol Ink, it ensures printing quality while controlling costs.
Simple Printing Process: Screen printing is straightforward and convenient, enabling quick responses to time-sensitive or small-quantity orders for apparel printing, meeting the demands of rapidly changing markets.
Diversity and Innovation
Versatile Applications: Plastisol Ink is not limited to T-shirts, cultural shirts, and advertising shirts. It can also be combined with special pastes to create discharge prints, penetration prints, foil stamping, flocking, thick plate prints, silicone prints, and more, adding creativity and value to printed products.
Environmental Protection and Sustainability: Some eco-friendly Plastisol Inks comply with international textile environmental standards, balancing market demands with environmental protection and sustainable development.
Limitations of Plastisol Ink in Screen Printing
Printing Speed
Compared to other highly automated printing methods, screen printing has a relatively low printing speed. This limits its application in large-scale production, especially when fast delivery is crucial.
Printing Precision
Screen printing produces relatively coarse lines, making it difficult to print very fine patterns. For applications requiring extreme precision, such as precision instrument labels or high-resolution graphics, it may not be the best choice.
Mesh Durability
Screen printing meshes have relatively low durability, prone to wear or clogging with increased printing cycles, affecting print quality. Regular inspections and mesh replacements are necessary, increasing maintenance costs and operational complexity.
Selection and Pricing of Plastisol Ink
Selection Tips
When selecting Plastisol Ink, consider the following:
- Brand and Quality: Choose reputable brands and reliable Plastisol Inks to ensure printing results and durability.
- Environmental Friendliness: With growing environmental awareness, prioritize eco-friendly Plastisol Inks that meet market demands and environmental standards.
- Applicability: Select the appropriate Plastisol Ink type and color based on specific printing needs and substrate characteristics.
Pricing Factors
Plastisol Ink prices vary by brand, quality, color, and purchase volume. Generally, renowned brands and higher-quality Plastisol Inks are pricier but offer better printing results and durability. Additionally, larger purchase volumes often lead to lower unit prices.
The Importance of Plastisol Ink Mixing System
The Plastisol Ink Mixing System is crucial for ensuring uniform ink mixing and stable use. Automated stirring and mixing systems maintain consistent ink performance and effects during printing, enhancing print quality and reducing manual operation difficulties and costs. Therefore, when selecting and using Plastisol Ink, it is essential to pair it with a high-quality Mixing System.
Conclusion
In conclusion, Plastisol Ink offers significant advantages and some limitations in screen printing. Its exceptional printing results, strong adhesion, and versatile applications make it a top choice for many printers and suppliers. However, its relatively low printing speed and precision, as well as mesh durability issues, require attention and solutions in application. By adopting reasonable selection and usage strategies and pairing it with a high-quality Mixing System, the advantages of Plastisol Ink can be maximized while overcoming its limitations.
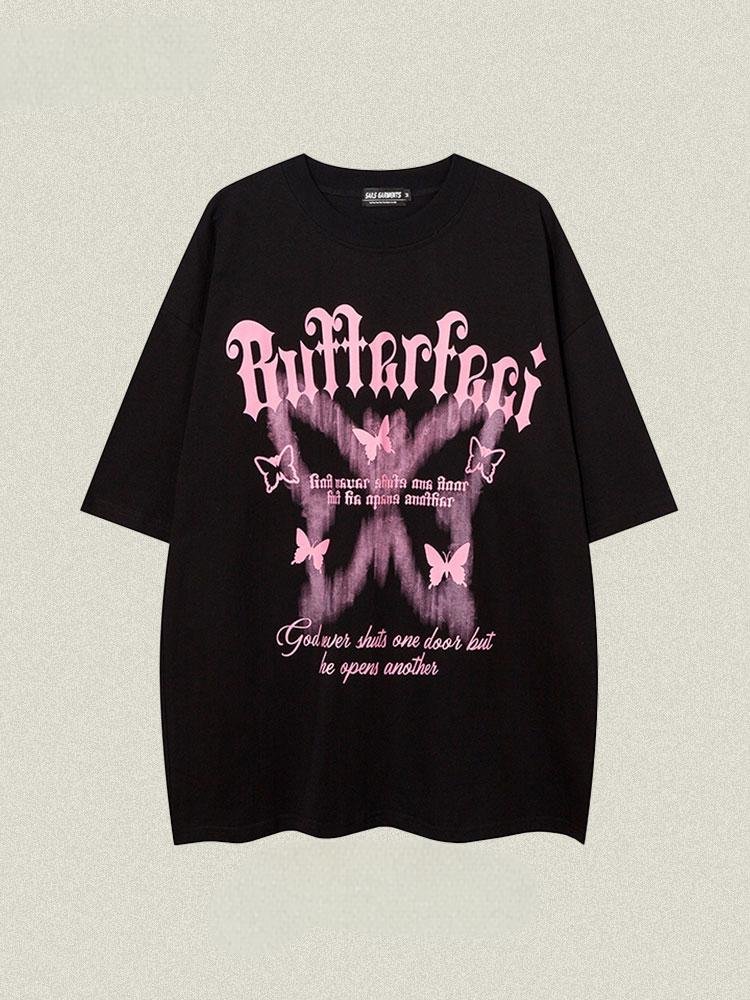