Conclusion & Quick Tips: Takeaways for Best Soft Hand Screen Printing Results
- Use soft hand base liberally with your standard plastisol inks for a dramatically softer print feel.
- Employ curable reducer, soft hand additive, and extender to further thin and soften ink deposits.
- For best results and minimal color loss, use a higher mesh and a soft (70 durometer) squeegee.
- Test prints on your actual garment type and use a heat press to finish for extra smoothness if desired.
- Balance opacity and softness: underbase when printing on dark garments, but don’t overdo ink layers.
- Remember to adjust pigment load; less pigment means softer, more flexible prints.
- Don’t neglect curing: test for proper cure after modifying any ink formula.
- Achieve the softest, vintage, or fashion soft effect by layering lightly and using premium soft bases.
- Comparison: Soft plastisol offers a forgiving, vibrant, and soft result compared to water-based ink, but each has its place.
- Always experiment, tune your process, and let your clients feel the difference!
- With these principles, your next soft hand print can rival any vintage tee or fashion boutique shirt—ensuring your clients get the softest, most impressive results from every screen printing project!
Ready to up your screen printing supply game? Start experimenting with soft bases, curable reducers, and see just how soft you can make your next run—your customers will love the buttery soft hand!
How to make м'які пластизольні чорнила
Short Summary and Why This Article Matters:
Have you ever touched an aired top and been so impressed by how light and soft it feels that it’s as if the ink isn’t even there? This fantastic “soft touch” print is not magic – it’s the result of a perfect combination of smart ink alternatives, smooth feel substrates, curing reducers, and knowledge of touchscreen printing. This booklet provides an in-depth look at everything you’ll want to know about how to make fabulous soft plastisol ink prints, how to use smooth feel substrates, and how to use a selection of additives to give your prints the smooth feel your business demands. Whether you’re a printing novice or a veteran, these guidelines will help you enhance the recreation of your display printing supply and get the softest, most abrasion-resistant results. Read on to analyze the professionals’ secrets, unusual pitfalls, and how to produce prints that customers will love!
Структура статті
- What Makes an Ink “Soft”? Defining Soft Hand in Screen Printing
- Plastisol Ink Basics: Why Plastisol Dominates Modern Screen Printing
- How Does Soft Plastisol Ink Transform Your Print?
- Additives Explained: Extender, Curable Reducer, and Soft Hand Additive
- What’s the Role of Mesh and Squeegee in Achieving a Soft Hand?
- Mixing Inks for Maximum Softness: Pigment Loads, Binders, and Tips
- Soft vs. Opaque: Managing Opacity When Printing Soft
- Specialty Soft Prints: Vintage Prints, Buttery Soft, and Fashion Soft
- Soft Plastisol vs. Water-Based and Discharge Inks: Pros and Cons
- Troubleshooting: Common Mistakes and How to Get the Softest Soft Hand Prints
1. What Makes an Ink “Soft”? Defining Soft Hand in Screen Printing
The “tender hand” is that coveted, slightly-there experience you observe whilst you run your fingers over a freshly revealed garment and the ink appears to soften into the cloth. In the context of display screen printing, “tender hand” actually refers to the softness of the very last print—how little you feel the ink film sitting atop the shirt. Everyone from excessive-fashion manufacturers to custom t-blouse stores chases after this effect as it increases the garment’s comfort and perceived first-class.
Achieving a soft hand print more often than not depends on the type of ink, the way the ink is prepared, and the gadget used. Details like gentle hand base, curable reducer, and better mesh counts could make all of the difference. Going after a smooth hand isn’t just about luxurious; for many forms of clothes, mainly lightweight tees, smooth prints are anticipated and might set your paintings other than competition.
If you care approximately repeat clients and beating out heavily produced plastisol prints with that regular heavy ink feel, getting to know to supply a soft hand print is a game-changer on your display screen printing business!
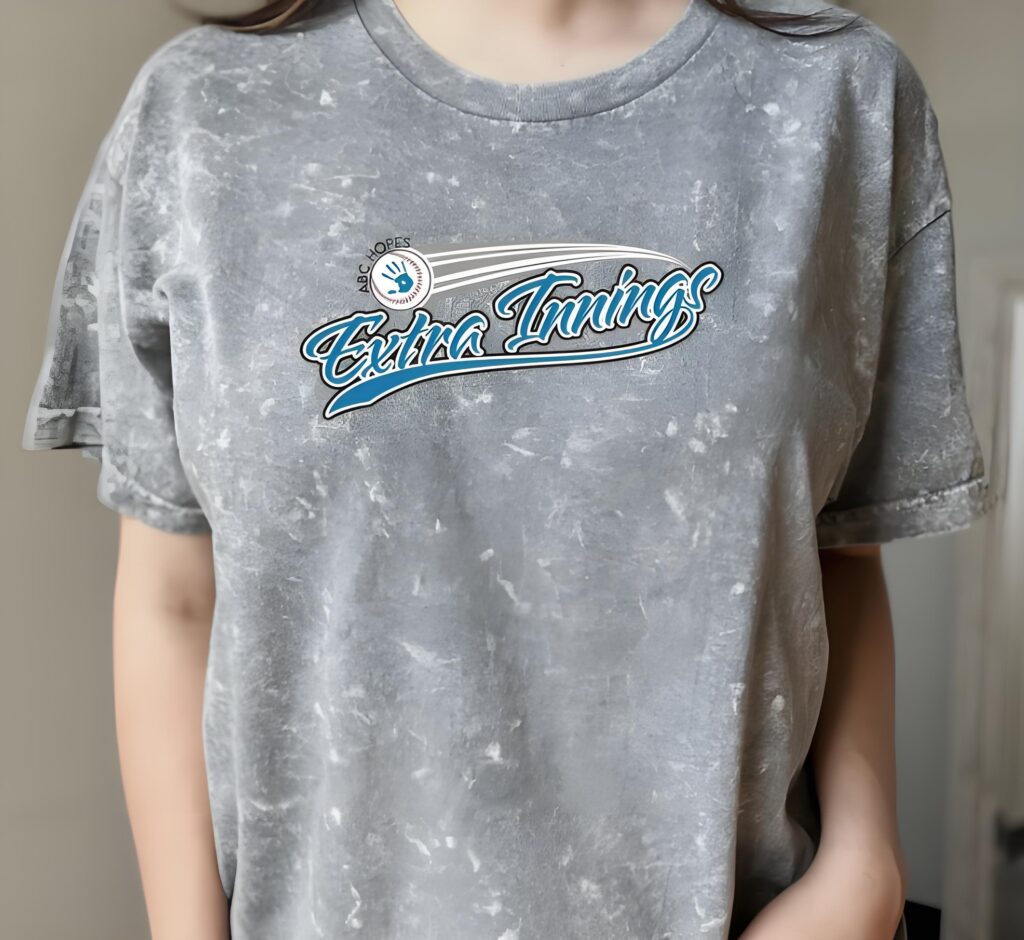
2.Plastisol Ink Basics: Why Plastisol Dominates Modern Screen Printing
Plastisol ink is, by a ways, the workhorse of the screen printing world. It’s preferred by means of printers global because of its consistency, coloration vibrancy, and ease of use. Unlike water-primarily based ink, plastisol does not dry inside the display, taking into consideration longer print periods and clean cleanup. But, in its everyday form, plastisol regularly yields a heavier, more plasticky touch, particularly in comparison to alternatives like water based totally or discharge ink.
That plastisol ink sense is generally thick, a little rubbery, and opaque—first-rate for bold, vivid designs, however no longer continually perfect while you want a softer, greater subtle finish. That’s wherein strategies for softening up your ink come into play. Whether you’re customizing sports uniforms or fashion tees, learning plastisol is crucial in case you need versatility to your print store.
Mixing plastisol with gentle hand base, extenders, or particular additives permits you to regulate ink viscosity, pliability, and, most significantly, the hand feel at the completed print. Armed with the proper screen printing deliver expertise, you may take widespread plastisol inks to gain a miles softer sense for your clothes.
3. Як це працює Soft Plastisol Ink Transform Your Print?
A soft hand base is a in particular formulated clean or semi-opaque base that, while blended with widespread plastisol ink, dramatically softens the final sense of the print. Soft hand base is blended with preferred plastisol inks to attain a “buttery smooth” hand, crucial for printers producing high style garments or replicating vintage prints.
This base may be used as an underbase or a aspect to your entire colour mix. By swapping out some of your ordinary plastisol with soft hand base for plastisol, you lessen ink buildup at the surface of the garment. The end result: a gentle, pliable print that’s a ways much less “plasticy” and lots more in keeping with water-based ink feels however with the durability of plastisol.
Crucially, gentle hand base isn’t just about softness; it could affect opacity as well. In a few cases, blending in loads of base will make an ink less opaque, so you’ll need to stability softness with insurance, specially on dark clothes. That stated, the payoff in comfort and excessive-style enchantment makes the use of a hand base for plastisol ink a recurring step for display screen printers generating excessive fashion appears.
4. Additives Explained: Extender, Curable Reducer, and Soft Hand Additive
Achieving that smooth hand sense isn’t simplest about the base. Sometimes, you need an extender, a curable reducer, or a dedicated tender hand additive to reach the preferred impact. Here’s a quick rundown of each:
- Extender: Think of this as a clean ink with out pigment. It “extends” your coloured plastisol ink, making it less focused and thinner, which equals a softer sense to the print and enables you print well on lightweight clothes.
- Curable Reducer: This additive reduces plastisol ink’s viscosity, making it easier to push thru a finer mesh and thin out the deposit at the garment. Lowering viscosity equals softer resins, much less movie construct-up, and consequently, a softer print. Just pay attention: too much curable reducer may also have an effect on proper therapy and durability of your finished print.
- Soft Hand Additive: This is a strong point additive designed in particular for attaining tender hand prints. Often, it’s a chemical blend that, while delivered to conventional plastisol inks, offers a soft, almost “style tender” result—perfect for display screen printers looking to offer the softest options available on the market.
All three methods play well with tender hand base and can be adjusted in proportions depending on your cloth, mesh be counted, favored impact, and process requirements.
5. What’s the Role of Mesh and Squeegee in Achieving a Soft Hand?
The mesh you operate to your screen printing method is a huge component in accomplishing smooth hand prints. High mesh counts—suppose 230 and above—allow for thinner layers of ink to be published. When the use of a smooth hand base, curable reducer, or extender, a finer mesh ensures the final print isn’t cakey or heavy.
Pairing a high mesh rely with a softer, 70 durometer squeegee would deposit just sufficient ink for vibrancy while retaining the completed print soft and bendy. The details here depend: the mixture of mesh and squeegee could make an ink experience dramatically softer or heavier, regardless of how it appears at the garment.
If you’re aiming for the softest results, always recollect mesh counts, squeegee hardness, and even the off-contact. Finer mesh and softer squeegee method less ink, and less ink approach a softer hand!
6.Mixing Inks for Maximum Softness: Pigment Loads, Binders, and Tips
Mixing your inks for maximum softness is each an artwork and a science. Start by means of reducing pigment load while viable. Heavy pigment makes an ink extra opaque but also will increase its stiffness at the shirt. Sometimes, replacing a part of your colour with extender is the important thing—your whites may turn out to be much less opaque, but brightness and comfort growth.
The binder in plastisol ink—the resin that carries the pigment—additionally impacts softness. Some producers promote soft plastisol ink formulated with more pliable resins, so maintain your eyes out for these to your display printing supply hunts.
Key tips: Always stir thoroughly, mix small test batches when the use of new gentle bases or components, and check the final print for each colour and hand. If you want antique prints with a smooth hand feel, use a greater obvious blend and layer lightly—you’ll mimic the appearance and sense of these first-rate-worn, nicely-cherished shirts customers crave.
7. Soft vs. Opaque: Managing Opacity When Printing Soft
Balancing opacity and softness is a elaborate venture for printers. The softer the print, often the more transparent your ink film. When printing on darkish garments, you can need to lay down an underbase of white ink to reinforce coloration vibrancy with out sacrificing the tender hand.
A tender hand base is blended with popular colors to minimize film thickness, however doing so may additionally result in a final print that is less opaque. For exceptional results and minimum shade shift, use an underbase just thick sufficient to pop your pinnacle hues—don’t overdo it. In reality, a clean base or extender can now and again be used as an underbase for softer, antique-like outcomes.
Remember, your purpose is the perfect balance: a print gentle sufficient to satisfaction, but still vivid enough to electrify. With exercise, your prints will strike that candy spot.
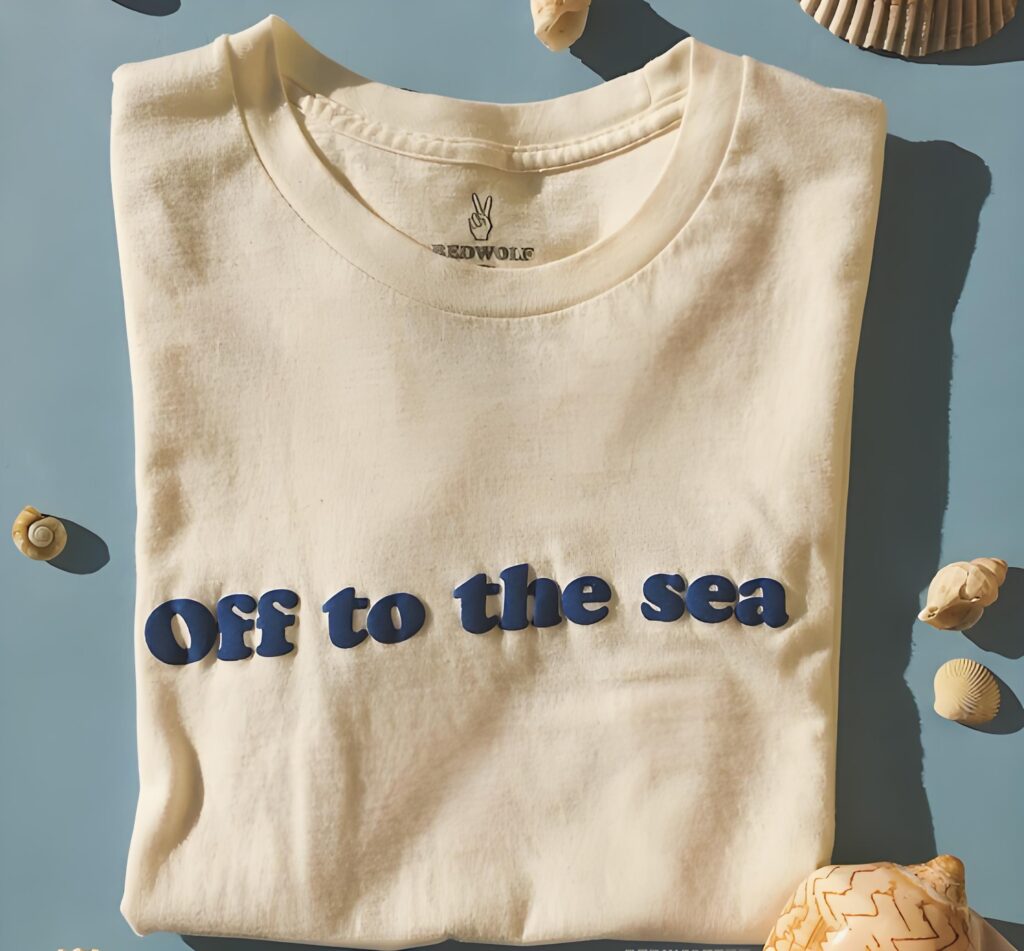
8.Specialty Soft Prints: Vintage Prints, Buttery Soft, and Fashion Soft
Want to copy the ones extremely soft, “barely-there” prints visible on vintage concert tees or high-style manufacturers? Soft plastisol prints dominate this area! The technique typically includes the use of a specialized smooth base, decreased pigment, finer mesh, and on occasion even completing with a warmth press for additonal softness.
“Fashion smooth” isn’t only a buzzword. Printers generating high style garments frequently depend upon the softest feasible plastisol ink formulas, usually the usage of a mix of gentle hand base, curable reducer, and general pigment. The consequences: lightweight, buttery tender prints that customers like to put on.
To truly nail this, test. Vintage prints, for instance, may use a 320 mesh, more clear base, and only a contact of pigment—a technique that showcases each mastery of ink blending and a nuanced technique to device.
9. Soft Plastisol vs. Water-Based and Discharge Inks: Pros and Cons
Let’s compare the heavy hitters for soft prints: smooth plastisol ink and water-primarily based ink or discharge ink. Water-based and discharge inks evidently penetrate the garment, yielding the softest prints possible—now and again indistinguishable from the blouse itself. However, they require extra technical understanding, specific curing/cure situations, and further vigilance to keep away from ink drying in the screen.
soft hand plastisol ink brings the excellent of both worlds: the reliability and colourful colorings of plastisol, and—with the right additives and tender hand base—the softness and drapability you want for top rate garments. Plus, smooth plastisol prints are much less finicky with humidity, color shift, and curing, especially for printers without conveyor dryers.
For commercial and fashion programs, soft plastisol remains the move-to, especially when screen printers producing excessive style clothes want both durability and comfort.
10.Troubleshooting: Common Mistakes and How to Get the Softest Soft Hand Prints
Getting buttery tender results isn’t constantly honest. Here are commonplace troubles with fixes:
- Print Feels Too Thick/Stiff: Use greater smooth hand base or curable reducer, and growth mesh matter.
- Colors Look Dull or Washed Out: Try an underbase of white ink, or layer your top shade more than one times lightly.
- Ink Isn’t Curing Properly: Too a good deal gentle base or reducer can prevent right cure. Run wash assessments to make certain sturdiness.
- Ink Sits on Top of Fabric: Lower viscosity with a curable reducer or extender for deeper material penetration.
A tip: Always take a look at small. Different kinds of garments, mesh, and ink require adjustment. Don’t be afraid to tweak your formulation till you acquire that softest hand your customers want.