Key Points: Considerations for White Plastisol Inks for Screen Printing
- White plastisol inks are the gold wellknown for opaque, crisp and sturdy white printing on all fabrics.
- Quality manufacturers like International Coatings and Wilflex provide specialized white inks for cotton, polyester and combined fabric, each with its own unique benefits.
- Low bleaching and coffee curing white inks deal with issues together with dye migration, cloth shrinkage or sizzling.
- Correct mesh rely, flash dryer utilization and priming strategies are vital for perfect white display screen printing.
- Use advocated temperatures and wash tests to make sure ok curing to avoid cracking and make sure longevity.
- Carefully follow adhesives to hold sign in accuracy and a excellent end on the pallet.
- Experiment with components and unique techniques to create precise white prints.
- Purchasing inks through the gallon, quart or pint relies upon for your production needs, however proper garage extends shelf lifestyles.
- Always alter your system to the cloth – cotton and polyester require unique strategies for quality results.
- Persistent testing, interest to detail, and willingness to test are the exceptional traits of a terrific screen printer.
- With the right approach, white ink is not scary. Invest in excellent inks, grasp the method, and each white screen print you produce will shine!
How to thin out white plastisol screen printing ink
Screen printing thrives on vibrant, crisp prints—and nothing is extra technically tough or visually critical than nailing the white ink in your designs. Whether you’re a hobbyist experimenting for your first t-shirt, or a seasoned expert looking to up your recreation, expertise білі пластизольні фарби, its remedy manner, and its software is vital for jaw-dropping outcomes. This article is a comprehensive guide that dives deep into the technological know-how and artwork of white plastisol ink for screen print. From low bleed solutions for poly blends to hints for accomplishing the suitable opaque white display screen print on both cotton and polyester, we’re overlaying it all. If you want your prints to pop with the great white possible, this manual is well worth analyzing: it offers answers to your largest ink questions, professional hints, comparisons of the first-class white plastisol inks, and realistic troubleshooting advice you’ll use in each print consultation.
Контур
- What is Plastisol Ink and Why Is It Essential for Print?
- Why Is White Plastisol Ink So Challenging Yet Important in Screen Printing?
- How Does the Curing Process Affect White Ink Print Quality?
- What Makes the Best White Plastisol Ink?
- How to Print Opaque White Ink on Cotton Shirts?
- How to Achieve Low Bleed White Ink on Polyester and Blends?
- How Much Ink Do You Really Need: Gallon vs Quart vs Pint?
- What Is the Role of Mesh, Flash, and Underbase in a Perfect Print?
- How to Prevent Dye Migration and Cracking in White Screen Prints?
- What Is the Best Way to Set Up Your Pallet and Manage Tack for Premier Results?
1.What is Plastisol Ink and Why Is It Essential for Print?
Plastisol ink is the spine of present day screen printing, prized for its versatility and colourful, opaque coverage. Unlike water-based totally alternatives, plastisol inks are made from PVC particles suspended in a plasticizer, this means that they don’t dry out in the display, providing you with more working time with out clogging mesh. These inks continue to be creamy and manageable till uncovered to excessive heat, in which they fuse into the material fibers in the course of the treatment stage.
For the ones obsessed on printing, plastisol is the default screen printing ink for both guide and automatic presses. It offers steady outcomes, making it easy to print sharp photographs and bold colorations—specially essential when generating complex designs or t-shirts with multi-coloration separations. Additionally, plastisol is to be had in many formulas, consisting of non-phthalate plastisol options, assembly regulatory and safety requirements international.
A key benefit of plastisol is its ability to produce excessive opacity prints—even on dark clothes—without bleeding or fading. Superior hiding power makes these inks especially ideal for white screen prints, in which attaining a shiny, stable white stands as an indicator of professional-best clothing.
2.Why Is White Plastisol Ink So Challenging Yet Important in Screen Printing?
Printing a sturdy white plastisol ink layer is the closing take a look at for any display printer, as white is the most visually scrutinized colour and the toughest to best. On darkish shirts, having a actually opaque white print requires a nicely-formulated ink that sits smooth and shiny atop the material, developing the critical under-base for different colored inks.
Yet, the challenges are great. White ink has a tendency to be thicker, with higher viscosity in comparison to other plastisols, that could make it difficult to attain each insurance and a gentle hand (which means the ink would not sense heavy at the blouse). If now not treated nicely, it could additionally crack after washing or fail to cure absolutely, which ends up in fading and durability problems. Getting a vivid white with one stroke is also difficult because white’s reflective features can disclose imperfections inside the print like no different coloration can.
Despite those difficulties, studying white display screen print is critical. A best white ink layer now not best complements the vibrancy and lifespan of your pictures however additionally signals the skill of the screen printer. For stores aiming to offer premium display screen printing services, understanding of white ink chemistry, managing, and cure strategies is a have to-have.
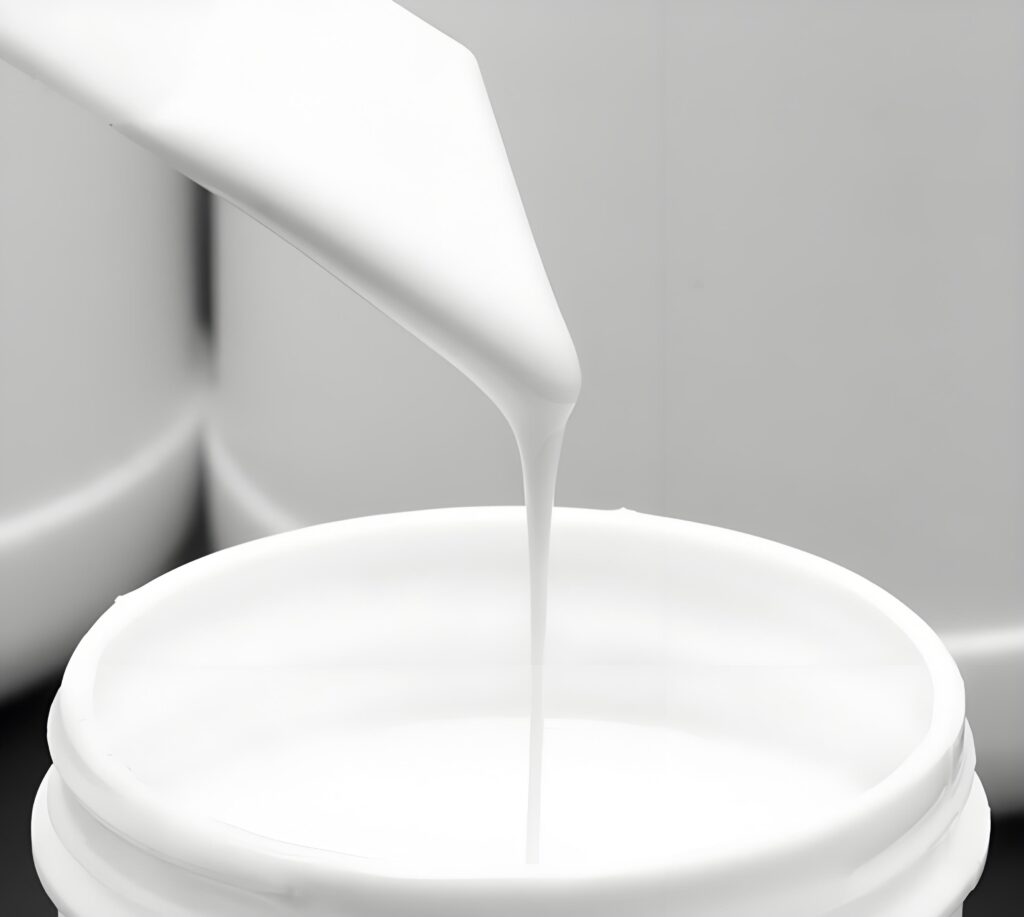
3.How Does the Curing Process Affect White Ink Print Quality?
A crucial step in screen print success is the therapy: the system where plastisol ink transforms from a creamy, unset paste to a stable, long lasting print. For білі пластизольні фарби, accomplishing a full cure is even extra crucial, as incomplete fusion results in negative adhesion, washout, and a print that can crack or peel.
White ink normally has a higher pigment load, which insulates the lower layers from warmth and makes it more difficult for the entire deposit to attain the best remedy temperature—usually between 320°F and 330°F (160°C to a hundred sixty five°C). Use of a conveyor dryer or flash unit guarantees even heating and thorough fusion with the cloth fibers. Always test using a wash take a look at to verify ink durability and that the therapy system has completed.
Modern improvements—like low therapy white plastisols—allow curing at temperatures as low as 260°F, which is mainly beneficial while printing on polyester or combination fabrics at risk of dye migration. Lower cure temps lessen the risk of activating cloth dyes, maintaining both print exceptional and the garment itself.
4.What Makes the Best White Plastisol Ink?
Selecting the pleasant білі пластизольні фарби is prime, whether you’re shopping for by means of the quart, pint, or gallon. The pinnacle white inks are engineered for superior opacity, tremendous coverage, and easy consistency. Brands like International Coatings and Wilflex are famend for his or her top class plastisol formulations, offering standout overall performance for both cotton white (optimized for cotton shirts) and poly white (especially designed for polyester).
A top white ink strikes a balance: it should be opaque sufficient for a vivid print in a single or strokes, yet creamy and easy to print via medium-to-high mesh counts. Leading options are non-phthalate, low-bleed, and produce a nice matte finish. For printing on difficult materials, look for features like low bleed, which prevents dyes from leaching thru the ink, and more advantageous elasticity to stop the print from cracking.
Some formulation include low remedy additive, enabling the ink to remedy at decrease temperatures—ideal for touchy fabric and blended clothes. Testing out one of a kind whites and walking side-via-side trials will screen which works incredible in your workflow and garment choice.
5.How to Print Opaque White Ink on Cotton Shirts?
Printing on cotton is arguably the most forgiving, but specialists nonetheless chase that flawless opaque white. Start by choosing a remarkable cotton white ink recognized for advanced insurance and softness on the completed shirt. Utilize the proper mesh be counted—commonly round 110 to 156 for white plastisol ink—which permits a generous ink deposit whilst protecting pleasant info.
Apply a coat of white ink with even, consistent squeegee pressure, keeping in thoughts whether or not you’ll push or pull primarily based on your style or press. Often, a single skip is sufficient with a high-opacity ink, however a few print shops will use strokes for extra brightness or to outshine that colored underbase.
Cure the print thoroughly the use of both a conveyor dryer or flash unit, making sure the ink fuses with the cotton fibers and survives the all-crucial wash check. The end result? A stunning, vibrant white print that’s smooth to touch and durable wash after wash.
6.How to Achieve Low Bleed White Ink on Polyester and Blends?
Polyester and mix fabric complicate screen printing with their notorious dye migration issue, in which garment dyes tour into the freshly published white ink, turning it pinkish or yellow. The solution? Specialized poly white and occasional bleed ink formulations, designed to block or decrease dye migration during the curing process.
When printing on poly shirts or blends, pick out a white plastisol ink classified “low bleed”—those have blockers to stop dye and often therapy at decrease temperatures (like 260°F in place of 320°F). This decrease therapy no longer only reduces dye migration however also protects heat-sensitive fabrics from harm.
For more safety, apply a flash among layers or use a “migration blocker” underbase. Always confirm your ink’s overall performance with a hard wash test; it’s the best way to guarantee the print remains vibrant white at the completed garment.
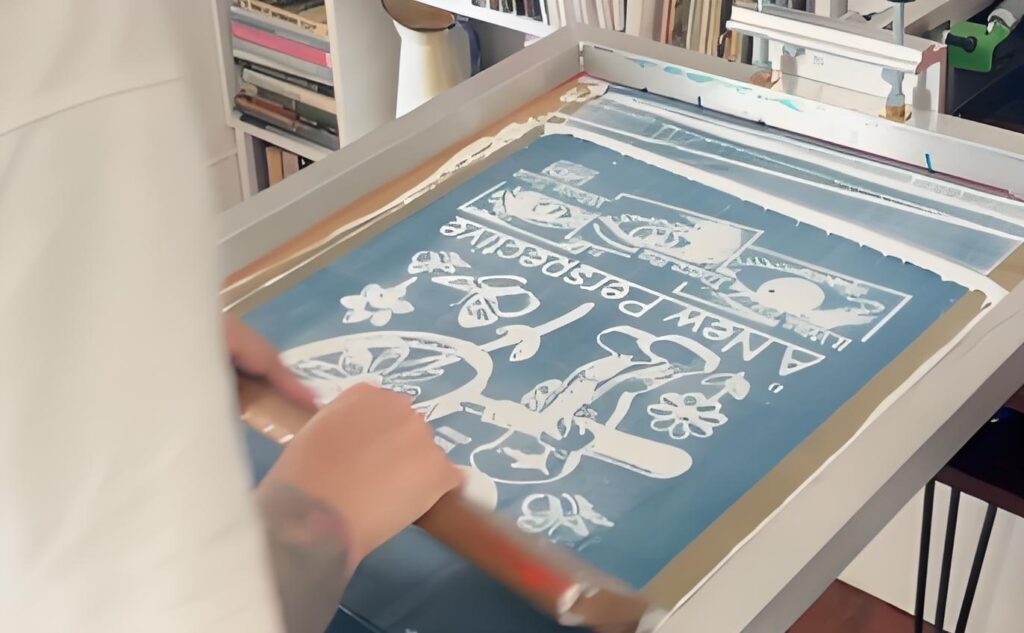
7.How Much Ink Do You Really Need: Gallon vs Quart vs Pint?
Ink sizing comes all the way down to your manufacturing scale and frequency. Larger shops frequently purchase gallon packing containers of white plastisol ink to preserve up with bulk orders, even as small-scale or strong point printers may additionally choose quart or pint sizes—specifically whilst checking out extraordinary manufacturers or batches. Remember, plastisol ink has an extended shelf existence, maintaining its creamy consistency for months or maybe years if saved well.
For domestic or starter groups, quarts or pints are a cost-effective manner to experiment with best white formulation. But for excessive-extent runs or for stores focusing on cotton or poly shirt printing, gallons are more fee-effective in the end and reduce downtime.
No remember the dimensions, always blend your ink well earlier than printing—this ensures the pigment and plasticizer continue to be combined for most useful opacity and overall performance on-screen.
8.What Is the Role of Mesh, Flash, and Underbase in a Perfect Print?
Mesh choice affects how a lot ink passes via to the material. For a thick, brilliant white print, use a lower mesh rely (one hundred ten–156), which deposits extra white plastisol ink in one stroke. Finer element paintings would possibly require better mesh, but assume to lose some opacity unless you double-stroke the print.
A flash unit is your secret weapon for multi-layer jobs. Flashing the print after the first underbase hardens the ink’s floor, so subsequent layers building up for max brightness and prevent colorations mixing. Using an under-base of white ink additionally sets the level for brilliant color prints—the white makes an ideal backdrop for Pantone suits and neons.
Mastering the balance of mesh, flash, and underbase steps is an artwork form—get it proper, and your white display prints will stick out from the group.
9.How to Prevent Dye Migration and Cracking in White Screen Prints?
Dye migration and cracking are the 2 primary threats to an excellent white print. Migration happens while polyester dyes move out of the cloth and into the freshly cured ink—resulting in stained or off-color whites. Low bleed ink formulations and coffee cure temperatures (the usage of specialized ink or additives) help mitigate migration’s results.
Cracking usually stems from over or below-curing, too thick an ink buildup, or terrible material stretch homes. Ensure ink movies aren’t excessively thick, and constantly observe the ink manufacturer’s encouraged cure time table—normally, 320°F for 1–2 minutes, but seek advice from your premium plastisol technical information for specifics.
A properly-cured, properly implemented white screen printing plastisol now not simplest appears vibrant but withstands repeated washes and heavy put on.
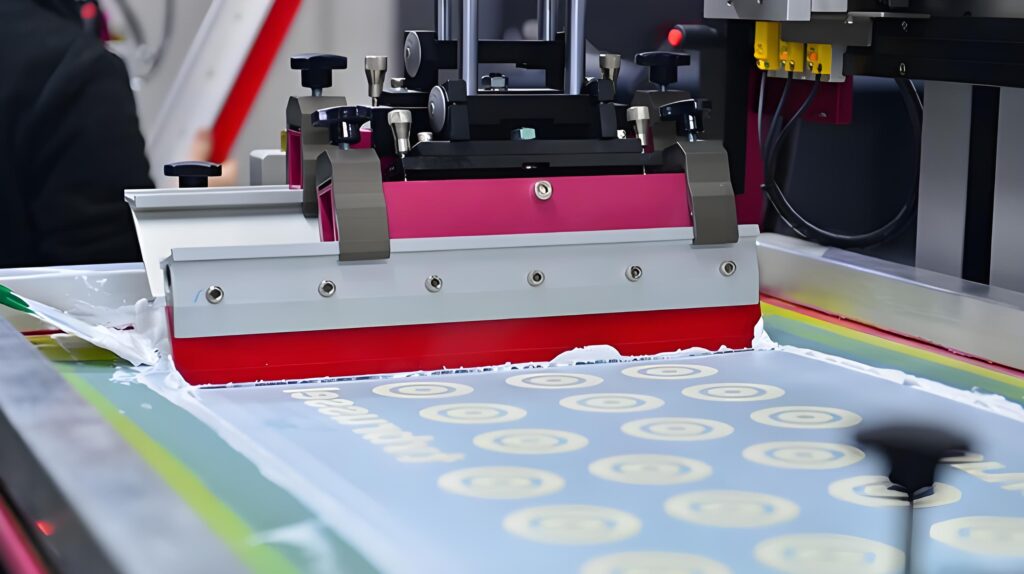
10.What Is the Best Way to Set Up Your Pallet and Manage Tack for Premier Results?
Proper pallet setup and preserving simply the proper tack in your surface are critical for printing multiple layers of ink without moving the shirt and ruining registration. Use a tack adhesive acceptable in your surroundings: water-primarily based for easy cleanup or spray adhesives for more potent stickiness in fast production settings.
Keep the pallet easy and most effective practice just sufficient tack to hold garments in region. Excessive tack can switch to the blouse or garble the fabric texture, at the same time as too little way shirts may additionally slide and lead to blurry prints. Periodically clean pallets between runs to avoid ink buildup, which could go away unwanted texture on the lower back of your shirts.
A properly-controlled pallet and tack approach no longer most effective improves registration and print quality however speeds up your workflow for most suitable, professional-grade outcomes.