In the world of textile printing, plastisol ink has become a staple due to its vibrant colors, flexibility, and durability. However, achieving optimal durability in plastisol ink can be challenging, especially when numerous factors can compromise its longevity. Understanding these factors is crucial for suppliers and printers alike to ensure the highest quality prints. This article delves into the key aspects that reduce plastisol ink durability, focusing on plastisol ink dispensers, plastisol ink drop, plastisol ink dye migration, and the environment. By the end, you’ll have a comprehensive understanding of how to mitigate these issues and enhance the durability of your plastisol ink.
The Importance of Plastisol Ink Durability
Plastisol ink durability is paramount for ensuring that prints maintain their vibrancy, resistance to wear and tear, and overall quality over time. Whether used in garments, signage, or promotional materials, the ability of plastisol ink to withstand everyday use is a defining characteristic of its appeal. When durability is compromised, prints can fade, crack, or show signs of wear, reducing their aesthetic appeal and functionality. This not only impacts the reputation of the printer but also affects the satisfaction of the end-consumer.
Factors Affecting Plastisol Ink Durability
1. Quality of Plastisol Ink Dispensers
Plastisol ink dispensers are the tools that deliver ink onto the fabric or substrate. The precision and consistency of these dispensers play a significant role in the durability of the final print. Poor-quality dispensers can lead to inconsistent ink deposition, causing areas of the print to be thicker or thinner than intended. This inconsistency can result in uneven wear, where thicker areas may crack or peel off, reducing the overall durability of the print.
- Improper Calibration: If the plastisol ink dispenser is not properly calibrated, it can lead to over-dispensing or under-dispensing of ink. Over-dispensing can cause ink pooling, which can affect the drying process and result in cracking. Under-dispensing, on the other hand, can lead to weak color intensity and poor adhesion to the fabric.
- Wear and Tear: Over time, plastisol ink dispensers undergo wear and tear, especially if they are not maintained properly. Worn-out parts can lead to ink leakage, inconsistent drops, and poor print quality. Regular maintenance and timely replacements of worn-out components are essential to ensure the longevity and accuracy of the dispenser.
2. Plastisol Ink Drop Consistency
The consistency of the plastisol ink drop is another critical factor affecting durability. An even and controlled drop ensures that the ink is evenly distributed across the fabric, promoting uniform drying and curing.
- Ink Viscosity: The viscosity of plastisol ink must be carefully managed to achieve consistent drops. Ink that is too thick can clog nozzles, leading to inconsistent drops and poor print quality. Ink that is too thin may not adhere well to the fabric, resulting in fading and wear over time.
- Nozzle Size and Type: The size and type of nozzles used in the plastisol ink dispenser also impact drop consistency. Smaller nozzles can produce finer details but may be prone to clogging. Larger nozzles can handle thicker inks but may not be suitable for intricate designs. Choosing the right nozzle for the specific application and ink viscosity is crucial.
3. Plastisol Ink Dye Migration
Dye migration is a common issue in textile printing, where dyes from the ink migrate within the fabric over time. This can lead to color bleeding, fading, and a general reduction in print durability.
- Fabric Composition: The composition of the fabric plays a significant role in dye migration. Natural fibers like cotton tend to absorb more ink and are more prone to dye migration compared to synthetic fibers like polyester. Blends of natural and synthetic fibers can also exhibit varying degrees of dye migration.
- Curing Process: Proper curing of plastisol ink can help mitigate dye migration. Curing involves exposing the printed fabric to heat, which causes the ink to set and bond with the fibers. Inadequate curing can lead to incomplete cross-linking of the ink components, allowing dyes to migrate more easily.
4. Environmental Factors
Environmental conditions, such as temperature, humidity, and exposure to UV light, can significantly impact the durability of plastisol ink.
- Temperature and Humidity: High temperatures and humidity can accelerate the breakdown of ink components, leading to fading and cracking. On the other hand, extreme cold can cause ink to become brittle, making it more susceptible to cracking and peeling.
- UV Exposure: Prolonged exposure to UV light can cause the dyes in plastisol ink to degrade, resulting in fading and loss of color vibrancy. UV stabilizers can be added to the ink formulation to help mitigate this effect, but they may not completely eliminate the issue.
Practical Tips for Enhancing Plastisol Ink Durability
- Use High-Quality Plastisol Ink Dispensers: Invest in reliable and well-maintained dispensers to ensure consistent and accurate ink deposition.
- Optimize Ink Viscosity: Regularly check and adjust the viscosity of your plastisol ink to ensure optimal drop consistency.
- Choose the Right Nozzle: Select nozzles that are compatible with your ink viscosity and the intricacy of your designs.
- Proper Fabric Preparation: Pretreat fabrics to enhance ink adhesion and reduce dye migration.
- Adequate Curing: Ensure that the printed fabric is exposed to the appropriate temperature and time during the curing process.
- Protect Against Environmental Factors: Store printed fabrics in cool, dry places and use UV-resistant coatings or finishes to protect against fading.
Conclusion
Plastisol ink durability is a multifaceted issue influenced by the quality of plastisol ink dispensers, consistency of ink drops, dye migration, and environmental factors. By understanding and addressing these factors, suppliers and printers can significantly enhance the durability of their prints. Investing in high-quality equipment, optimizing ink viscosity, proper fabric preparation, adequate curing, and protecting against environmental factors are essential steps towards achieving longer-lasting and more vibrant prints. Remember, the key to successful plastisol ink printing lies in attention to detail and a commitment to quality at every stage of the process.
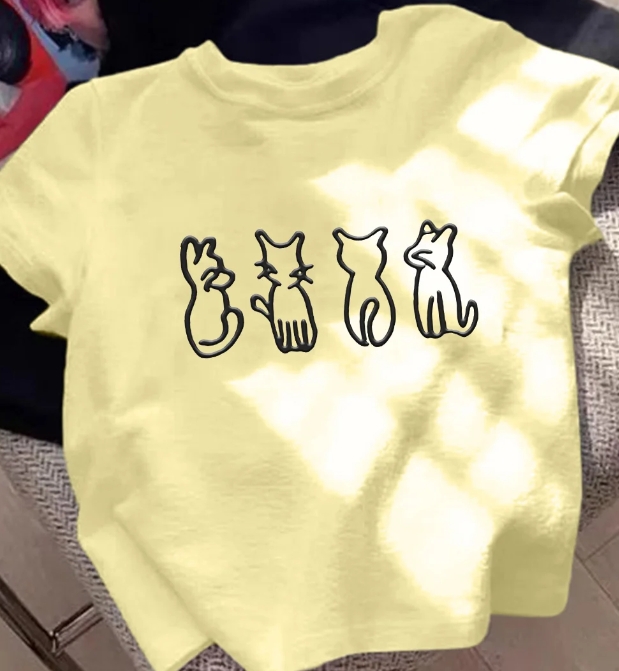