In the realm of textile printing and graphic arts, understanding the intricacies of ink properties is crucial for achieving high-quality results. Among the various types of inks available, plastisol ink stands out due to its versatility, durability, and vibrant color reproduction. However, one common challenge faced by plastisol ink users is ink bleeding. This article delves into the relationship between ink viscosity and plastisol ink bleeding, exploring how managing these factors can significantly impact print quality. By the end, you’ll have a clearer understanding of how to maintain an optimal plastisol ink assortment stock, especially if you’re sourcing plastisol ink in Australia.
Understanding Plastisol Ink Bleeding
Plastisol ink bleeding occurs when the ink spreads uncontrollably beyond its intended boundaries on the substrate, resulting in blurred or overlapping images. This phenomenon can undermine the crispness and detail of your prints, making them look unprofessional. Plastisol ink bleeding is particularly problematic in multi-color prints, where overlapping ink layers can mix unintendedly, altering the desired color outcome.
Plastisol ink bleeding is influenced by several factors, with ink viscosity being a prominent one. Viscosity refers to the thickness or resistance of a fluid to flow. In the context of plastisol inks, viscosity affects how the ink behaves during application, drying, and final cure.
The Role of Ink Viscosity
Ink viscosity is a critical determinant of print quality, directly influencing ink transfer efficiency, dot gain, and, importantly, plastisol ink bleeding.
- Low Viscosity Inks: These inks flow more freely, which can lead to excessive spreading and plastisol ink bleeding. While they may be easier to apply, especially with fine details, the risk of bleeding increases, especially on porous or absorbent fabrics.
- High Viscosity Inks: Conversely, high-viscosity inks are thicker and less prone to spreading. They offer better control over ink placement, reducing the likelihood of plastisol ink bleeding. However, they can be more challenging to work with, requiring higher printing pressures or temperatures to ensure proper ink transfer.
Finding the right balance in ink viscosity is thus essential for minimizing plastisol ink bleeding while maintaining print quality and efficiency.
Managing Plastisol Ink Viscosity
Managing ink viscosity involves several strategies, from initial ink formulation to on-press adjustments. Here are some practical tips:
- Ink Selection: Choose inks specifically formulated for your printing needs. Manufacturers often offer a range of viscosities within their plastisol ink assortment stock. When sourcing plastisol ink in Australia, look for suppliers that provide detailed viscosity specifications and recommendations for different applications.
- Temperature Control: Ink viscosity is temperature-sensitive. Plastisol inks tend to thin as they warm up and thicken as they cool down. Maintaining consistent printing temperatures is crucial for achieving predictable ink behavior and minimizing plastisol ink bleeding.
- Additives: Using viscosity modifiers or thickeners can help adjust ink viscosity to the desired level. These additives should be carefully measured and mixed to avoid altering other ink properties like color or cure rate.
- Mixing and Storage: Proper mixing of ink batches ensures uniformity in viscosity. Store inks in cool, dry conditions to prevent premature viscosity changes.
Addressing Plastisol Ink Bleeding Specifically
Beyond managing viscosity, several additional measures can help mitigate plastisol ink bleeding:
- Substrate Preparation: Ensure the printing surface is clean, dry, and properly pretreated. Contaminants or excessive moisture can exacerbate ink bleeding.
- Print Settings: Adjust print head pressures, speeds, and gap settings to optimize ink transfer without causing excessive spreading.
- Drying and Curing: Adequate drying and curing are vital steps in preventing plastisol ink bleeding. Ensure that inks are fully dried before subsequent print passes or handling, and cure at the recommended temperatures and times.
- Ink Bundling: When storing or transporting plastisol ink bundles, take care to avoid temperature extremes and pressure points that could alter ink viscosity or cause leakage.
Case Study: Plastisol Ink Bleeding in Action
Consider a scenario where a printer in Australia is experiencing significant plastisol ink bleeding on polyester fabrics using a new batch of ink. After examining the ink’s viscosity, they discover it’s significantly lower than the previous batch. By adjusting the ink viscosity with a suitable thickener and recalibrating the print settings, they successfully reduce plastisol ink bleeding and restore print quality. This example underscores the importance of continuous monitoring and adjustment of ink properties.
Plastisol Ink Bubbling Up: A Related Issue
While plastisol ink bleeding is a primary concern, another issue worth mentioning is ink bubbling up. This occurs when ink trapped between layers of fabric expands during curing, causing bubbles or blisters on the surface. Proper ink viscosity and thorough substrate preparation can also help prevent ink bubbling up, further enhancing print quality.
Conclusion
In summary, the relationship between ink viscosity and plastisol ink bleeding is a complex yet manageable aspect of plastisol ink printing. By understanding and controlling ink viscosity, printers can significantly reduce the incidence of plastisol ink bleeding, leading to cleaner, more professional prints. Proper ink selection, temperature control, and the use of additives are essential strategies. Additionally, addressing substrate preparation, print settings, and curing practices contribute to minimizing plastisol ink bleeding. When sourcing plastisol ink in Australia, prioritize suppliers that offer a comprehensive plastisol ink assortment stock with detailed specifications and support. By adopting these practices, you’ll be well-equipped to handle the challenges of plastisol ink printing and deliver exceptional results.
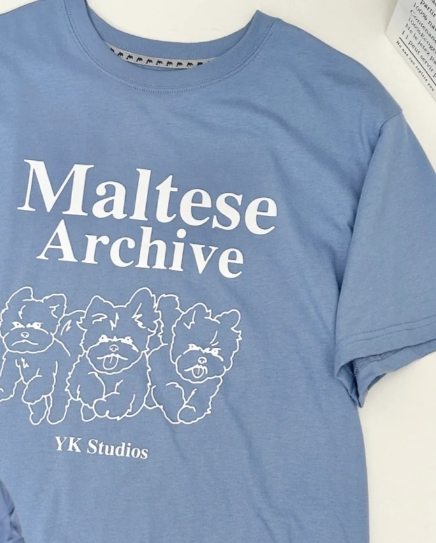