In the world of screen printing, achieving the perfect balance between ingredients is crucial for outstanding results. One such critical aspect is understanding the ideal ratio of plastisol ink to cured reducer. This article delves deep into the intricacies of this ratio, offering insights that can revolutionize your printing process. By the end, you’ll have a comprehensive understanding of how to optimize your plastisol ink usage with the right amount of reducer, ensuring the best possible outcomes. Let’s dive into the specifics, starting with the fundamental question: What is the ideal ratio of plastisol ink to cured reducer for optimal printing results?
The Importance of the Plastisol Ink to Cured Reducer Ratio
Plastisol ink is a versatile and popular choice for screen printing due to its durability, vibrant colors, and ability to adhere to various fabrics. However, to achieve these benefits, the ink must be properly mixed with a reducer before the curing process. The reducer plays a vital role in thinning the ink, making it easier to print and ensuring a smooth, even application.
The ideal ratio of plastisol ink to cured reducer can vary depending on several factors, including the specific type of ink you’re using, the desired print effect, and the fabric you’re printing on. However, getting this ratio wrong can lead to a host of problems, such as poor ink adhesion, fading colors, and even ink cracking after curing. That’s why it’s essential to understand the importance of this ratio and how to achieve the perfect mix.
Tips for Mixing Plastisol Ink with Cured Reducer
When mixing plastisol ink with a reducer, there are a few key tips to remember to ensure optimal results:
- Start with a Small Batch: It’s always a good idea to start with a small batch of ink and reducer when experimenting with new ratios. This allows you to test the mixture without wasting a lot of ink.
- Use High-Quality Ingredients: Investing in high-quality plastisol ink and reducer is essential for achieving the best possible print results. Cheaper alternatives may not mix well or may produce inferior prints.
- Measure Precisely: Using accurate measurements is crucial when mixing plastisol ink and reducer. Even small deviations in the ratio can significantly impact the final print.
- Mix Thoroughly: Once you’ve combined the ink and reducer, mix them thoroughly to ensure an even consistency. This will help prevent streaking or pooling during the printing process.
- Test on Scrap Fabric: Before printing on your final fabric, test the mixture on a scrap piece of material. This will allow you to check for any potential issues, such as ink bleeding or poor adhesion.
Understanding Plastisol Ink Toxicity
Before we dive further into the ratio of plastisol ink to cured reducer, it’s important to address a common concern: the toxicity of plastisol ink. While plastisol ink is generally considered safe for use in screen printing, it can pose some risks if not handled properly.
Plastisol ink contains PVC (polyvinyl chloride) resin, plasticizers, and pigments. When heated during the curing process, these components can release volatile organic compounds (VOCs) and other potentially harmful substances. Therefore, it’s essential to work in a well-ventilated area and to wear appropriate protective gear, such as gloves and a respirator, when handling and printing with plastisol ink.
The Role of Plastisol Ink Transfers and Pails
When it comes to plastisol ink, transfers and pails are two essential components of the printing process. Plastisol ink transfers allow you to print detailed designs onto fabrics using a heat press. They are a popular choice for creating custom t-shirts, hoodies, and other garments.
Plastisol ink pails, on the other hand, are large containers used to store and transport the ink. These pails come in various sizes, depending on your printing needs. When choosing a pail, look for one that is made from durable materials and has a tight-fitting lid to prevent spills and evaporation.
Tulco, a leading manufacturer of printing supplies, offers a wide range of plastisol ink pails and transfers. Their products are known for their high quality and reliability, making them an excellent choice for professional screen printers.
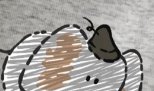
Adjusting the Ratio for Different Printing Needs
As mentioned earlier, the ideal ratio of plastisol ink to cured reducer can vary depending on your specific printing needs. Here are some guidelines to help you adjust the ratio for different applications:
- Fabric Type: Different fabrics require different ink consistencies. For example, thicker fabrics may require a thicker ink mixture, while thinner fabrics may benefit from a thinner mixture.
- Print Effect: The desired print effect also plays a role in determining the ink-to-reducer ratio. For example, if you want a soft hand feel on the printed fabric, you may need to use a higher ratio of reducer. On the other hand, if you want a more durable print, you may need to use less reducer.
- Ink Brand and Type: Different brands and types of plastisol ink have varying viscosities and curing properties. Be sure to consult the manufacturer’s instructions for the specific ink you’re using to determine the optimal ratio.
Common Issues and Troubleshooting
Even with the best intentions, issues can arise when mixing and printing with plastisol ink and reducer. Here are some common problems and troubleshooting tips:
- Ink Cracking: If the ink cracks after curing, it may be due to too much reducer or not enough ink. Try reducing the amount of reducer or increasing the amount of ink in your mixture.
- Poor Adhesion: If the ink doesn’t adhere well to the fabric, it may be due to a poor ink-to-reducer ratio, contaminated ink, or incorrect curing temperatures. Check your ratio, ensure your ink is fresh, and adjust your curing temperatures as needed.
- Fading Colors: Fading colors can be caused by too much reducer, incorrect curing temperatures, or exposure to UV light. Try adjusting your ratio, ensuring proper curing, and storing your prints in a cool, dark place.
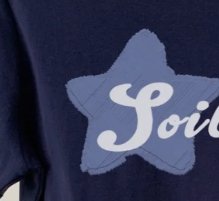
Conclusion
Achieving the ideal ratio of plastisol ink to cured reducer is essential for optimal printing results. By following the tips outlined in this article, you can ensure that your ink mixture is perfect for your specific printing needs. Remember to always use high-quality ingredients, measure precisely, and test on scrap fabric before printing on your final material.
In summary, the ideal ratio of plastisol ink to cured reducer depends on various factors, including fabric type, print effect, and ink brand. By adjusting the ratio to suit your needs and troubleshooting common issues, you can achieve outstanding print results with plastisol ink.