Master screen printing with the perfect squeegee. Explore alternatives, best practices, and how to choose the ideal tool for your project.
Whether you’re a hobbyist or a pro, the squeegee is your gateway to vibrant, precise prints. Understand its mechanics, respect its role, and let it transform your screen printing journey.
The Essential Role of the Screen Printing Tool: A Comprehensive Guide
Screen printing is a dynamic fusion of artistry and technical precision, and at the core of this craft lies a critical tool: the squeegee. This unassuming instrument is the unsung hero of every print, responsible for transferring ink through a mesh screen and onto substrates with accuracy and vibrancy. Whether you’re printing T-shirts, posters, or industrial components, the squeegee is indispensable. For beginners, mastering its use is foundational; for experts, it’s the key to consistency and quality. In this guide, we’ll explore how this tool works, its optimal usage, alternatives, and the science that makes it irreplaceable.
Anatomy of the Tool: Design Meets Function
A squeegee is more than just a blade—it’s a precision-engineered instrument. Composed of a handle (often aluminum or wood) and a replaceable polyurethane or silicone blade, its design prioritizes control and durability. The blade’s durometer (hardness) varies: softer blades (60–70 Shore A) adapt to textured surfaces like fabric, while harder blades (75–90 Shore A) deliver sharp details on flat materials like paper or metal.
The edge profile of the squeegee also impacts results. A square edge maximizes ink deposition for bold graphics, while a rounded edge minimizes buildup for fine lines. Adjustable handles on professional-grade tools allow printers to fine-tune pressure distribution, ensuring even ink transfer across large screens. Whether printing a mural or a micro-detailed logo, selecting the right squeegee is the first step to success.
Mastering the Angle: The Science Behind Technique
A critical factor in screen printing is the angle of the squeegee during ink application. The widely recommended range of 60–75 degrees isn’t arbitrary—it’s rooted in fluid dynamics. A shallower angle (closer to 60 degrees) increases the blade’s contact with the screen, forcing more ink through the mesh. However, too shallow an angle risks ink flooding, causing smudges. Conversely, a steeper angle (75+ degrees) reduces ink flow, ideal for intricate designs but requiring meticulous pressure control to avoid uneven coverage.
Variables like ink viscosity, mesh count, and substrate texture influence the optimal angle. For example, a 65-degree angle with the tool might suit plastisol ink on a 110-mesh T-shirt screen, while a 70-degree angle works better for water-based ink on a 230-mesh poster screen. Seasoned printers develop an intuitive feel for adjusting the squeegee mid-print, compensating for environmental factors like humidity or screen tension.
When to Improvise: Alternatives to the Tool
While the squeegee is ideal, improvisation is sometimes necessary. Can a credit card replace this tool? Temporarily, yes—for small DIY projects. However, cards lack the flexibility and edge precision of a true squeegee, often leading to uneven pressure or stencil damage. Slightly better alternatives include plastic scrapers or putty knives, which offer more control but still fall short for complex or high-volume jobs.
These substitutes are best for prototyping or single-use prints. For instance, a hobbyist making a dozen stickers might manage with a scraper, but a professional relying on the tool for 500 shirts would never risk inconsistent results with makeshift instruments.
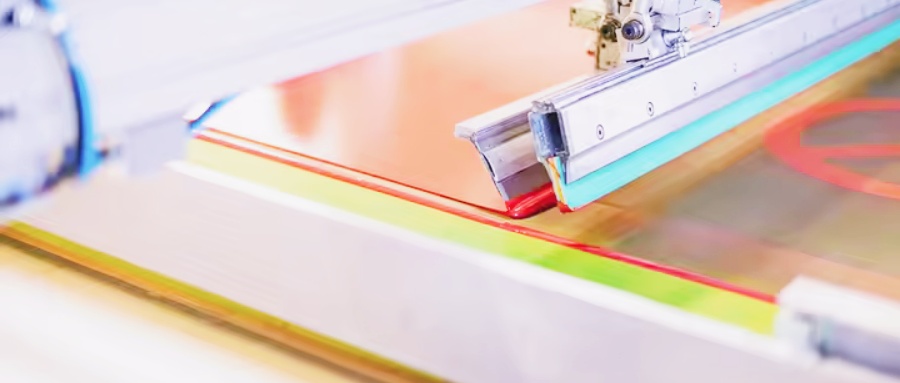
Material Matters: Why Composition Counts
The blade material of the squeegee directly impacts performance. Polyurethane is the industry standard due to its chemical resistance and durability. It maintains a sharp edge through thousands of prints and withstands harsh solvents. Silicone blades, though less common, excel with UV-curable inks due to their non-stick properties.
Blade hardness also affects ink behavior. A soft squeegee conforms to fabrics, ideal for thick inks like metallics. Hard blades excel with thin, fast-drying inks, providing rigidity for crisp lines. Some printers even use dual-durometer blades, combining soft cores for flexibility with hard exteriors for detail.
Troubleshooting Common Issues
Even with a high-quality squeegee, challenges arise. Streaking often signals a worn blade or uneven pressure—replacing the blade or adjusting the handle’s tilt can help. Ink bleeding under the stencil? The tool’s angle might be too shallow, or pressure too heavy. Conversely, pinholes or patchy coverage may indicate a steep angle or insufficient pressure.
Environmental factors also play a role. Humidity thins water-based inks, requiring a steeper angle. Cold temperatures thicken plastisol, demanding a softer blade to avoid screen damage. Documenting adjustments for different conditions builds a reliable workflow.
Automation vs. Hand Printing: The Tool’s Evolution
In industrial settings, manual squeegees have evolved into automated systems with pneumatic blades. These machines ensure robotic precision for high-volume runs. Yet the principles remain unchanged—angle, pressure, and blade integrity still dictate quality. Some hybrid systems allow manual tweaks to automated tools, blending efficiency with artisanal control.
Conclusion: Elevate Your Craft with the Right Tool
The squeegee is more than a tool—it’s the bridge between creativity and execution. From selecting the right durometer to troubleshooting angle-related flaws, mastery of this instrument separates amateurs from professionals. While temporary substitutes exist, investing in quality blades and refining technique unlocks unparalleled results. As screen printing embraces new inks and technologies, the squeegee remains timeless, proving that even in a digital age, hands-on craftsmanship reigns supreme.
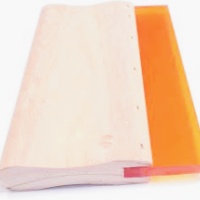