Screen print transfer paper is revolutionizing the screen printing industry, offering a solution for transferring designs onto fabrics and other materials.
What Is Transfer Paper and How Does It Work?
Transfer paper serves as the bridge between your artwork and the fabric. Instead of applying ink directly to the material, the design is first transferred to the paper and then moved to the fabric using heat and pressure. This method not only allows for more flexibility but also helps in producing designs with intricate details, sharp edges, and vibrant colors.
The process is simple yet effective:
- Design Creation: Start by designing your artwork digitally.
- Print to Paper: Print the design onto the transfer paper using screen printing inks (like plastisol or fabric ink).
- Cure the Ink: Partially cure the ink on the paper to ensure it’s ready for the transfer.
- Heat Press Transfer: Position the paper ink-side down on the fabric and apply heat and pressure with a heat press machine.
- Peel the Paper: Once cool, remove the paper, and your design will be perfectly transferred onto the fabric.
What Materials Can You Use Screen Print Transfer Paper With?
One of the major advantages of transfer paper is its versatility. Here are the materials commonly used with it:
- Cotton and Cotton Blends: Popular for garments like T-shirts and hoodies.
- Polyester: Works well for sportswear and athletic gear, especially with plastisol transfer paper.
- Canvas: Perfect for bags and promotional items.
- Hard Surfaces: Some transfer papers can be used on ceramics, metal, and wood for specialty projects.
As long as the material can withstand heat and pressure, screen print transfer paper can be used on it.
How to Maximize the Benefits of Transfer Paper in Screen Printing
To get the best results with screen print transfer paper, you need to follow a few best practices:
- Choose the Right Paper: Make sure the paper matches the type of ink and material you’re using, such as plastisol transfer paper for plastisol inks.
- Apply Ink Evenly: Ensure that the ink is applied smoothly and evenly on the transfer paper to avoid uneven prints.
- Cure the Ink Properly: Don’t over-cure the ink before transferring, as this can impact the final result.
- Correct Heat Press Settings: Temperature, pressure, and timing are key to ensuring a successful transfer. These settings may vary depending on the paper and material you’re using.
- Test First: Always test the process on a small batch before scaling up production to prevent mistakes.
What Are the Key Advantages of Using Transfer Paper?
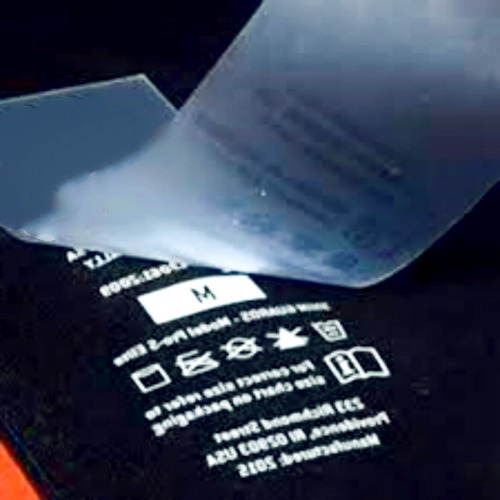
- Flexibility: You can prepare your designs ahead of time, allowing for on-demand printing. This is especially useful for custom or small batch orders.
- Precision: Transfer paper allows you to capture fine details, gradients, and intricate patterns with high accuracy, making it perfect for more complex designs.
- Portability: You can easily print your designs in one location and transfer them to different locations, making this method ideal for mobile operations.
- Reduced Waste: Since you can preprint the designs on paper, mistakes are less likely to affect the final product, helping reduce material waste.
- Cost-Effective for Small Orders: For smaller quantities, transfer paper is a more affordable option compared to setting up traditional screen printing.
- Durability: When done correctly, the transferred design is long-lasting and resistant to wear.
- Consistency: Once you’ve mastered the technique, transfer paper can deliver consistent results, making it a reliable option for professional printing.
Potential Drawbacks to Consider
While transfer paper offers numerous advantages, there are some challenges to keep in mind:
- Heat Sensitivity: Some fabrics may not handle the high temperatures needed for the transfer process, so make sure your material can withstand the heat.
- Durability Issues: If the transfer process is not executed correctly, the design may not last as long as a traditional screen print.
- Learning Curve: For beginners, getting the ink application, curing, and heat press settings just right can take some time and experimentation.
- Material Limitations: Heavily textured or delicate fabrics may not yield the best results with transfer paper.
- Higher Costs for Specialty Papers: Specialty transfer papers (like those for plastisol inks) can be pricier than traditional screen printing methods.
How Different Types of Transfer Paper Affect Your Design
The type of transfer paper you choose can impact the final look of your design:
- Plastisol Transfer Paper: Ideal for vibrant, long-lasting prints, especially for cotton and polyester fabrics.
- Cold Peel vs. Hot Peel Papers: Cold peel papers give a matte finish, while hot peel papers offer a glossy finish, so you can choose based on your desired outcome.
- Eco-Friendly Papers: For those looking for sustainable options, eco-friendly papers that work with water-based inks are a great choice.
- Specialty Halftone Papers: Designed for detailed and intricate designs, these papers allow for high-resolution transfers with sharp, crisp lines.
Conclusion
Screen print transfer paper has quickly become a must-have tool for screen printers. It provides a perfect blend of flexibility, precision, and ease, allowing for high-quality, custom prints on a variety of materials. Whether you’re working on T-shirts, hoodies, or promotional items, transfer paper offers a reliable way to create intricate, durable designs. While there are a few challenges to consider, such as heat sensitivity and learning curves, the benefits of this method far outweigh the drawbacks. By mastering the right techniques and choosing the right transfer paper, you can take your screen printing projects to the next level.
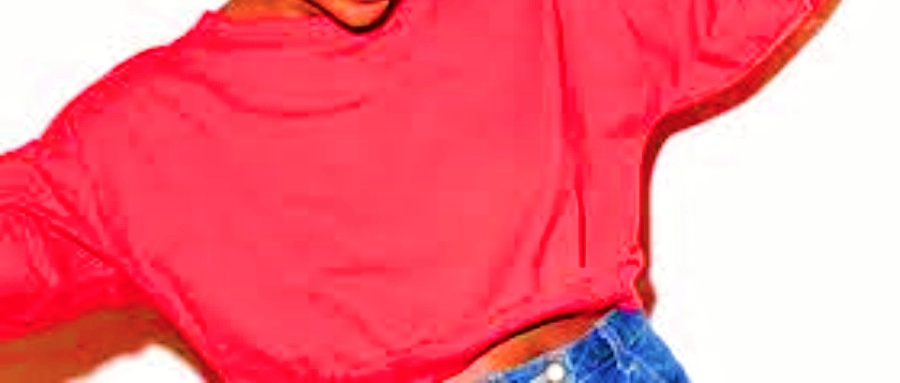