Want your garb prints to jump off the shirt with formidable, jet-black ink that doesn’t fade, crack, or bleed? If you’ve ever puzzled how display printers get that rich, dependable black on garments, the solution is in one of the enterprise’s first-rate pals: black plastisol ink. This article unpacks the entirety you need to recognize approximately plastisol ink, particularly black plastisol types, and the important curing procedure that makes those prints last for the lengthy haul. Whether you’re just getting to know how to blend a creamy plastisol ink or troubleshooting why your prints crack, you’ll stroll away with seasoned guidelines and crucial solutions. Read on—your monitors (and your shirts) will thank you.
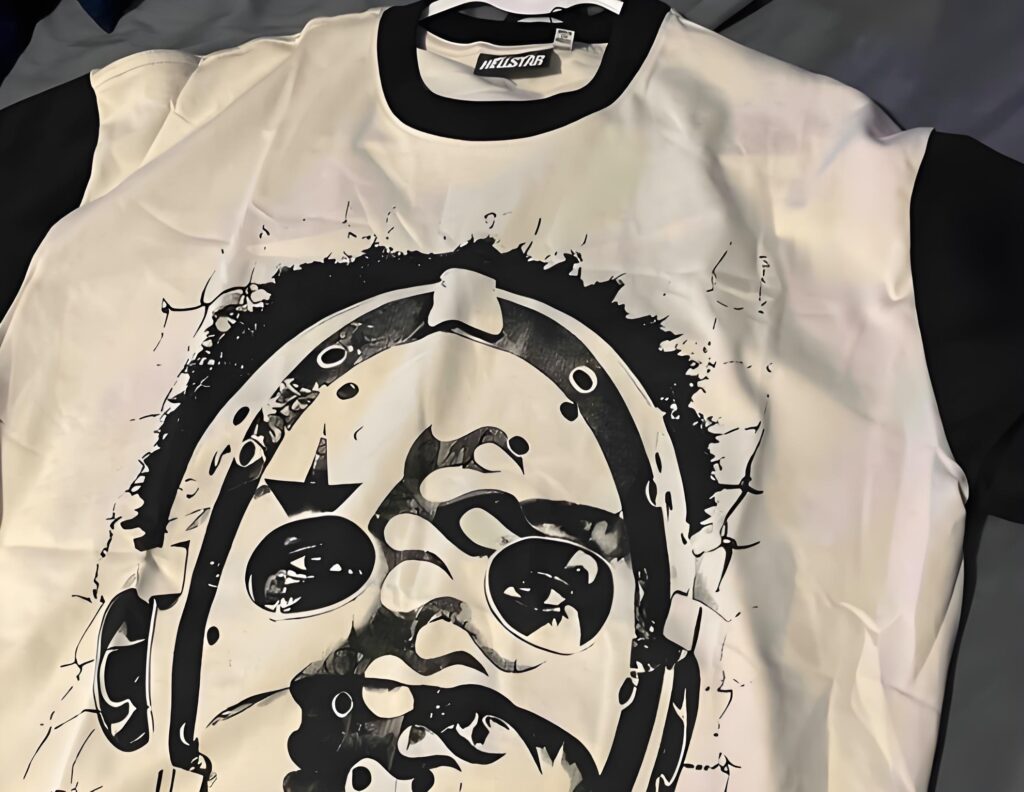
Table of Contents
1.What is Black Plastisol Ink and Why is it Essential for Screen Printers?
Black plastisol ink is one of the maximum generally used kinds of ink in the world of display screen printing. This opaque, creamy, and highly pigmented ink is designed to offer deep, constant black insurance on a extensive variety of fabrics. Unlike many water based totally inks, black plastisol ink sits atop the material fibers, ensuring splendid opacity—best for excessive-comparison images and formidable text.
Screen printers love plastisol ink for screen printing because it’s extraordinarily easy to print, works well with multiple display kinds and press setups, and grants colourful outcomes on each cotton and polyester blends. Its versatility makes it a pass-to for everything from fundamental t-shirts to fashion-forward poly/cotton blends, and its forgiving remedy window method even beginners can get pro results with a little practice.
Without black plastisol, reaching wealthy, lengthy-lasting blacks—free from ugly dye migration or bleed—could be so much more difficult. It remains the standard by way of which all different black display screen printing inks are judged.
2.Plastisol Ink Basics: Composition, Chemistry, and Types
At its core, plastisol ink is a suspension of PVC (polyvinyl chloride) particles in a plasticizer, which offers it its signature creamy texture and sturdy performance. The ink in no way “dries” at room temperature; as a substitute, it wishes to be cured at a particular temp to end up everlasting. That’s why you’ll often pay attention about “remedy plastisol” or “plastisol display screen” in shop communicate.
Types consist of trendy plastisol, low bleed, non-phthalate options (which might be more secure for the environment), and strong point inks for dark garments or polyester fabrics. Each mixture is tailored for a particular substrate, ensuring you’re included whether you’re printing on cotton, poly, or uncommon substances.
One of the coolest matters about plastisol ink is its compatibility with shade mixing structures—meaning custom shades, including Pantone-matched blacks and blends, are absolutely feasible.
3. How Does Black Plastisol Ink Compare to Water Based Ink?
Screen printers frequently debate plastisol ink for display screen printing as opposed to water based ink. Plastisol inks are praised for their high opacity, creamy consistency, and reliable curing. Water based ink, then again, soaks into cloth for a softer sense, but it’s a lot more reliant on fiber activation and might war to be fully opaque—specially for black prints or on dark garments.
Plastisol inks paintings higher with quite a few mesh counts and screen types, at the same time as water bases every now and then require excessive mesh and more finesse. For companies selling shirts by using the gallon or print stores striving for consistency, black plastisol ink’s smooth-to-print houses and forgiving cure variety make it the winner—particularly whilst you’re aiming for bold, wealthy black on any fabric.
4. Choosing the Right Screen and Mesh for Plastisol Inks
The screen you pick out is essential for purchasing perfect effects with black plastisol or any plastisol ink. Lower mesh displays allow extra ink via, perfect for heavy, opaque prints, while better mesh counts are suitable for great detail or smooth hand designs.
For ambitious black plastisol prints, many printers settle round a 110 mesh display screen; it moves a balance between ink deposit and detail. That said, your material matters too! Printing on polyester fabric? Opt for a mesh that helps save you dye migration. Emulsion thickness (like a solid direct emulsion) influences the stencil facet and universal picture sharpness. Spending time on coating and prepping your monitors pays off—crisp stencils imply crisp prints.
5.How Do You Mix and Prep Black Plastisol Ink for Printing?
When you open a clean 1 gallon or five gallon bucket of plastisol ink, you’ll be aware it’s thicker than many display printing inks. A thorough blend is important for even pigment dispersion and the creamy consistency wanted for clean squeegee movement.
Some black plastisol inks come geared up to print, whilst others may require you to combination in components for low remedy or low temperature printing. It’s additionally not unusual to have a colour mixing system for pantone matching and area of expertise jobs. Always preserve the plasticizer balanced so you don’t come to be with too much tack, and keep away from exposing your ink to direct daylight, that could degrade the pigment.
6.Press Setup: Manual vs. Automatic for Optimum Prints
Screen printer setups range widely, from the house garage single-head manual press to the whole-scale automatic plastisol press in a expert keep. Black plastisol ink plays well in both scenarios thanks to its solid open time and steady printability.
Manual presses require a constant hand and careful squeegee use, however they’re forgiving for small batch runs. Automatics convey pace and repeatability—plus better manage over flash and print-flash-print steps for thick black layers or wet-on-moist printing. Adjust your off-contact, screen anxiety, and platen temp for max effects regardless of platform.
7.Understanding Curing: Why Does Plastisol Ink Need to Cure?
Unlike water based ink, plastisol ink handiest bonds to cloth after it’s heated to its cure temp—normally round 320°F (one hundred sixty°C), although low-temperature ink formulation are getting commonplace. The curing manner transforms the creamy paste right into a tough, bendy plastic that gained’t wash out, crack, or peel the temperature.
8. How to Set Correct Cure Temp and Dwell Time
The proper cure temp ensures the plastisol screen print direct bonds to your blouse for long-lasting effects. Most plastisol inks want a minimum temperature of 320°F, but decrease treatment inks exist for warmth-touchy polyester or blends. Always use a thermometer (or pyrometer) to verify that each the surface and ink film are accomplishing cure temp, not just the air inside the dryer.
Dwell time can range by thickness; a heavier coat needs longer treatment. Test your manner! Stretch the cured print—if it cracks, your cure’s off. If the print peels, boom warmth or time. This interest to detail units execs apart from hobbyists.
9. Preventing Bleed, Dye Migration, and Other Common Issues
Polyester fabric convey unique headaches like dye migration and bleed, wherein the dye from the blouse wicks into the black plastisol or other screen printing ink, spoiling the crisp black finish. Prevent this the use of a low bleed or high opacity black plastisol ink, particularly designed for poly and blends.
Flash between layers if wished for extraordinary opaque prints, but don’t overheat or you can scorch or crack the print. Stencil edges ought to be sharp (stencil and emulsion pleasant is prime) and ink via screen print ought to be thick enough for opacity, thin sufficient for smooth hand.
10. Tips for a Soft Hand, Opaque Coverage, and High Opacity Prints
Everyone wishes a display print that feels exact—in industry terms, a “soft hand”—but still indicates deep, smooth black. Achieve this balance with the aid of choosing the right mesh remember, optimizing your squeegee method, and the usage of a creamy ink system. Specialty excessive opacity or “bleed blocker” black plastisol types are perfect for opaque, low-bleed outcomes.
Try print-flash-print for extra formidable blacks (in particular on coloured or poly clothes), however be cautious of constructing up too thick a layer, which loses softness and makes the blouse sense heavy
Summary: Your Fast Track to Plastisol Screen Printing Success
Here’s what to consider as you’re taking your black plastisol screen printing to the subsequent level:
- Black plastisol ink can provide ambitious, opaque, and sturdy consequences for almost any cloth or display printing setup.
- Always pick the right mesh and prep your screens nicely—coating and emulsion depend.
- Mix your plastisol ink very well for creamy, regular prints.
- Set your remedy temp and reside time cautiously—improper curing results in cracks, peeling, or fading.
- Use low bleed, high opacity, or distinctiveness black plastisol ink for polyester, poly-blends, or hard fabrics.
- “Flash” among prints for extra opacity, but avoid over-curing.
- Clean up with ink degradent and press wash; keep inks faraway from daylight.
- Troubleshoot cracking, bleeding, or scorching by using checking cure parameters, mesh, and stencil setup.
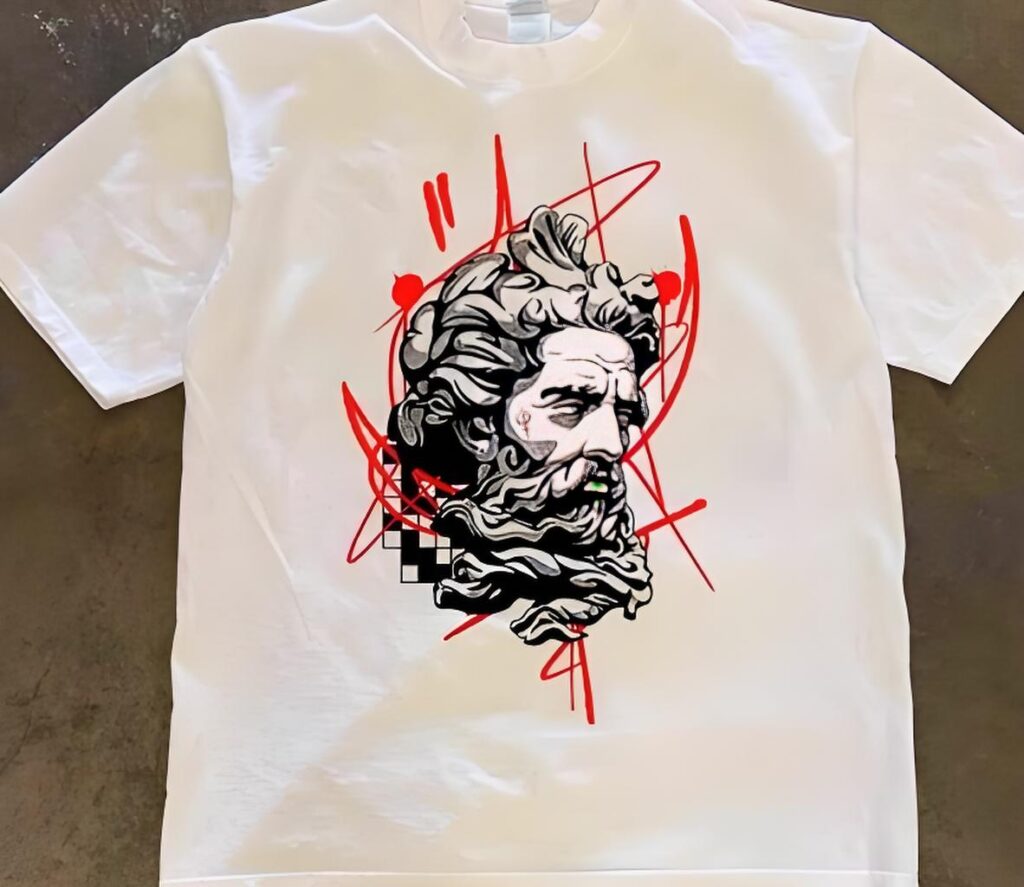