Key Takeaway: Essentials for Low Bleed White Plastisol Inks for Polymers and Blends
- Selecting Low Bleed White Inks for Polymers and Polymer Blends: Critical to stopping dye migration and avoiding bleed disasters on synthetic fabrics.
- Formulation Matters: Look for high coverage, creamy consistency inks designed for low bleed performance.
- Curing is critical: Always use the correct temperature and dwell time to properly blend the ink while minimizing the risk of dye migration.
- Test before high volume production: Each substrate and mixture may react differently; always pre-test for opacity, blotch resistance and durability.
- Mix and handle inks correctly: Mix inks thoroughly before use and use additives carefully for smooth print flow.
- Choose the right equipment and mesh: Optimize mesh count and press settings for the ink and garment type selected.
- Be careful with additives: Use reducers or softeners only when necessary, remember they reduce impermeability.
- Beware of sticking and flashing problems: Adjust techniques and timing to avoid sticking and pilling during production.
- Document the process: Track what works (and doesn’t work) on each substrate for efficient, consistent results.
- STAY INFORMED AND ADAPTABLE: Printing techniques and apparel materials are always evolving – keep learning, testing and improving your game.
With these insights, you can take screen printing to the next level – even the toughest polyester fabrics and darkest garments are no match for well-formulated, low-bleed white plastisol inks and knowledgeable decorators.
Unlock the Secrets of Opaque, Low Bleed White Plastisol Ink for Superior Polyester and Blend Printing
Are you suffering with bleeding colorations, stupid prints, or bad coverage whilst printing on polyester and poly blends? Dive into the world of low bleed white plastisol ink—your answer for colourful, opaque, and durable prints on even the trickiest fabric. This article is vital analyzing for print shops, garb decorators, and display screen printing lovers trying to master the artwork of printing brilliant whites on tough substrates. Here, you’ll discover why ink desire subjects, the way to achieve excessive opacity, and how to keep away from high priced errors like dye migration.
مخطط المقال
- What Makes Low Bleed White Plastisol Ink Essential for Screen Printing on Polyester?
- How Does Ink Chemistry Tackle Dye Migration and Bleed on Poly Fabrics?
- Why Is Opaque White Ink a Game-Changer for Printing on Dark Garments?
- Which Printing Equipment and Mesh Are Best for Low Bleed White Inks?
- Can You Print Low Bleed White on Cotton and Blends—Or Just Poly?
- How Do Cure Temperature and Dwell Time Influence Bleed Resistance?
- How to Achieve Creamy Consistency and Smooth Flow with White Plastisol Ink
- What Additives and Reducers Are Safe—And Which Lower Bleed Resistance?
- Tips to Avoid Tack, Sticking, and Flash Issues on Press
- Why Should You Always Test and Adjust for Each Substrate?
1. What Makes Low Bleed White Plastisol Ink Essential for Screen Printing on Polyester?
When it involves garb decoration, ink overall performance is the whole thing. Low bleed white plastisol ink is formulated particularly for printing on polyester and poly blends, where dye migration and bleeding can wreck prints. Its purpose? To act as a barrier, blocking dyes in poly cloth from staining your crisp, white ink and retaining your artwork vibrant and smooth.
Unlike wellknown plastisol, low bleed ink includes houses that face up to dye migration, making it vital for high-opacity prints on difficult substrates. If you are printing on dark fabric or any garment containing synthetic fibers, low bleed white plastisol ink must constantly be your first preference. This uniqueness ink ensures your prints pop and remain long lasting—even after more than one washes.
Polyester and poly blends are infamous for bleeding, and normal inks simply cannot deal with the venture. The precise chemistry in low bleed inks is your insurance coverage for pristine results whenever.
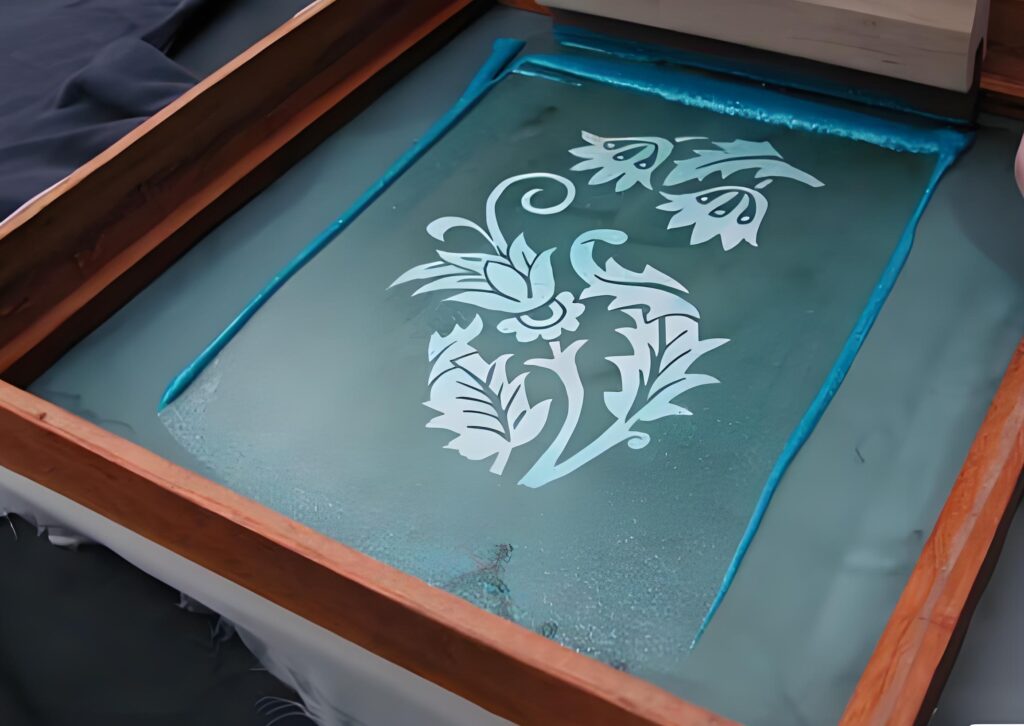
2. How Does Ink Chemistry Tackle Dye Migration and Bleed on Poly Fabrics?
You may marvel what offers low bleed white plastisol ink its magic. The mystery lies in its formulation—engineered mainly to create a bodily block against dye migration, the process where cloth dye seeps into the ink film after printing and curing.
Low bleed white carries uniqueness components that growth bleed resistance and enhance opacity. These substances work through forming a tighter, greater impervious ink layer atop the material. This is critical in view that polyester garb and poly blends are specially prone to dye migration—reds, mainly scarlet reds, and other deep colours love to bleed into lighter ink deposits.
Understanding the connection between ink chemistry, treatment temperature, and dwell time is essential. Cure too warm and you risk unlocking latent fabric dyes; too cool and your plastisol ink might also never nicely fuse, ensuing in negative adhesion and sturdiness.
3. Why Is Opaque White Ink a Game-Changer for Printing on Dark Garments?
Opacity is one in all the biggest demanding situations in display screen printing, in particular whilst operating with dark clothes or substrates. Standard white plastisol frequently falls quick, leading to stupid, faded prints. High-opacity, low bleed white ink is specifically formulated to put down a thick, colourful layer that visually “blocks out” the darkness under.
This is specifically critical while printing as a stand-alone white or the use of an underbase for multi-colour prints. The creamy, excessive pigment method in modern lb white plastisol ink ensures your whites continue to be shiny and immune to the bleed of underlying dyes—a necessity for any serious display screen printing keep.
Moreover, excessive-opacity inks lessen the number of print strokes required, boosting productiveness whether or not you’re printing manually or on automatic presses. The end result? Reliable, sharp, and professional-looking prints every time.
4. Which Printing Equipment and Mesh Are Best for Low Bleed White Inks?
Your preference of printing gadget and mesh could make or destroy a print run with low bleed white inks. For pleasant effects, pair your ink with a suitable mesh depend (normally 86-156) that lets in for a enormous ink deposit at the same time as preserving image detail.
Both guide and automated presses work superbly with lb white plastisol ink, however computerized presses shine when consistency and speed are important. If you’re strolling excessive-volume prints or producing sportswear, investing in computerized presses approach higher manage over ink deposit, squeegee strain, or even live time.
No be counted your setup, always stir the ink previous to printing. This guarantees a creamy consistency and enables avoid clogs or choppy opacity, which is mainly vital when printing on textured poly blends.
5. Can You Print Low Bleed White on Cotton and Blends—Or Just Poly?
بينما low bleed white plastisol ink is designed with polyester in mind, its versatility extends to cotton and blends, too. Many print stores use it as a accepted white across poly, cotton, and poly/cotton blends to simplify production.
For poly blends, this ink offers the bleed resistance of area of expertise poly ink with the gentle hand and brightness desired for cotton prints. However, constantly check in your genuine mixture—fabric range, and some may additionally gain from a distinct white ink designed mainly for all-material performance.
When handling nylon or particular blends, test in case your ink is rated for adhesion on the ones substrates. Some require special components or maybe a separate stand-on my own ink for premiere tack and durability.
6. How Do Cure Temperature and Dwell Time Influence Bleed Resistance?
Curing is one of the maximum critical stages in accomplishing bleed resistance with any plastisol ink, specifically low-bleed formulations. The “treatment” refers back to the fusing of ink to the fabric, generally in a conveyor dryer. For low bleed white ink, temperatures usually variety from 270°F to 320°F with suitable live time, ensuring sturdy adhesion without overheating the substrate.
Over-curing can cause dyes in polyester to sublimate, leading to dye migration and ruining your print. Under-curing will bring about ink that doesn’t fuse well—hurting durability or even washability.
Dwell time varies by dryer model, material weight, and layer thickness. Some low therapy white inks are formulated for even lower temperatures, lowering the hazard of dye migration further. Always pre-test your conditions and use temperature strips or probes for verification.
7. How to Achieve Creamy Consistency and Smooth Flow with White Plastisol Ink
Achieving the right creamy consistency in your ink is vital for high-opacity prints with maximum smoothness. Plastisol inks, in particular high-opacity and coffee bleed types, may be thick out of the bucket. Stir the ink previous to printing—this warms and loosens the components, making sure it flows properly via the mesh.
A creamy ink minimizes squeegee strain required on press, which facilitates lessen print facet elevate and unwanted tackiness. If additional go with the flow or softness is needed, reducers and components may be used—however use caution! Adding any reducer or additive can decrease the bleed resistance, potentially making the ink less effective at blockading dyes.
Balance is prime: prioritize consistency and creamy handling, however don’t over-skinny your ink otherwise you threat compromising print opacity and bleed manipulate.
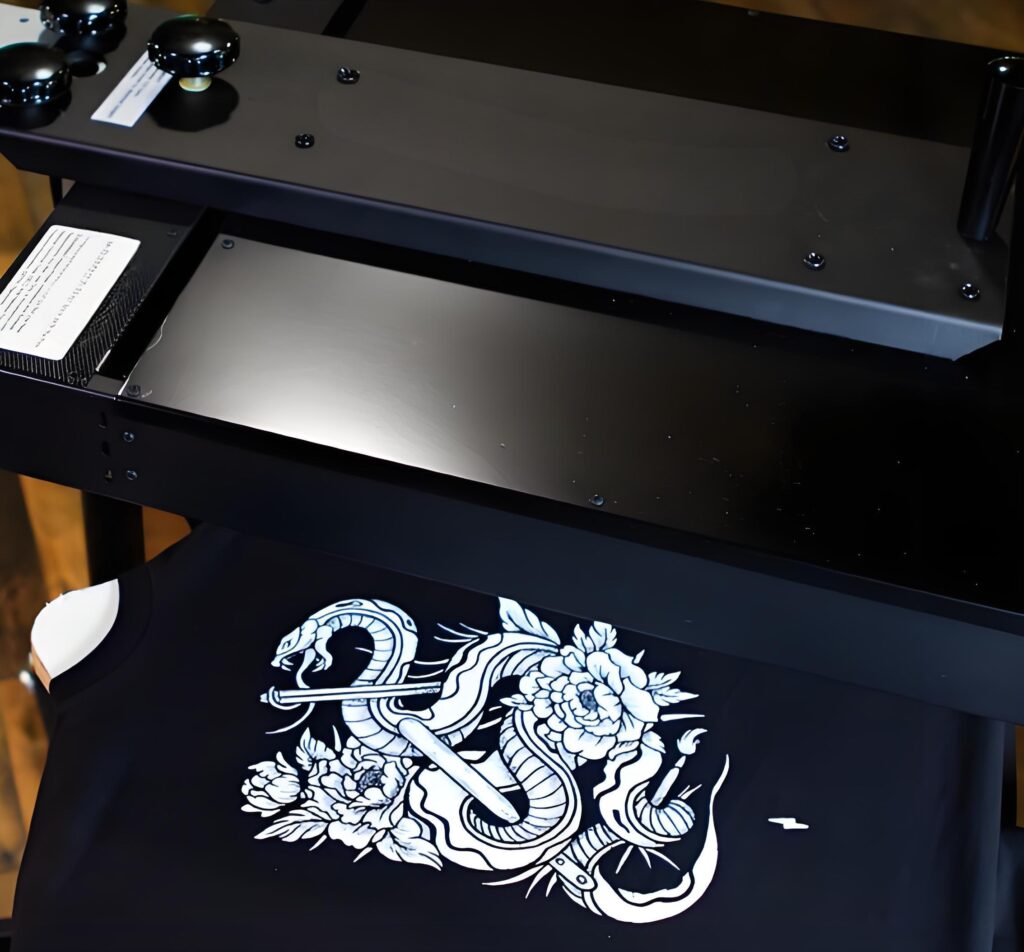
8. What Additives and Reducers Are Safe—And Which Lower Bleed Resistance?
Additives and reducers are popular in display screen printing for changing ink viscosity, improving drift, or softening hand feel. However, with low bleed white inks, the addition of reducers or other components can decrease the bleed resistance that makes these inks so valuable.
Before adding anything in your lb white plastisol ink, don’t forget the utility. If printing on dark fabrics or garments susceptible to dye migration, you need to preserve maximum block-out electricity. Additives can lower the bleed resistance—the very property you’re counting on for achievement.
If you ought to upload some thing, continually pre-check on the precise fabric, and preserve notes on effects. Many expert ink suppliers, like International Coatings, provide utilization tips for components, and suggest constantly testing for durability, opacity, and bleed resistance after change.
9. Tips to Avoid Tack, Sticking, and Flash Issues on Press
Dealing with cheesy prints, sticking monitors, or cussed flash times? These problems are more common with high-opacity, low bleed inks due to their thicker, stickier nature. To keep away from them, make certain your press is clean, monitors are tensioned, and you’re following proper stay and flash instances.
Fast flashing is another gain of present day lb white plastisol ink—it lets in you to treatment a skinny ink layer quick among colors with out overheating. But if the ink stays tacky, alter your flash temp and stay, or attempt a distinct underbase setup.
If you run into continual tack or sticking, take a look at in case your ink deposit is just too thick, your mesh is too nice, or if environmental elements (like humidity) are affecting drying.
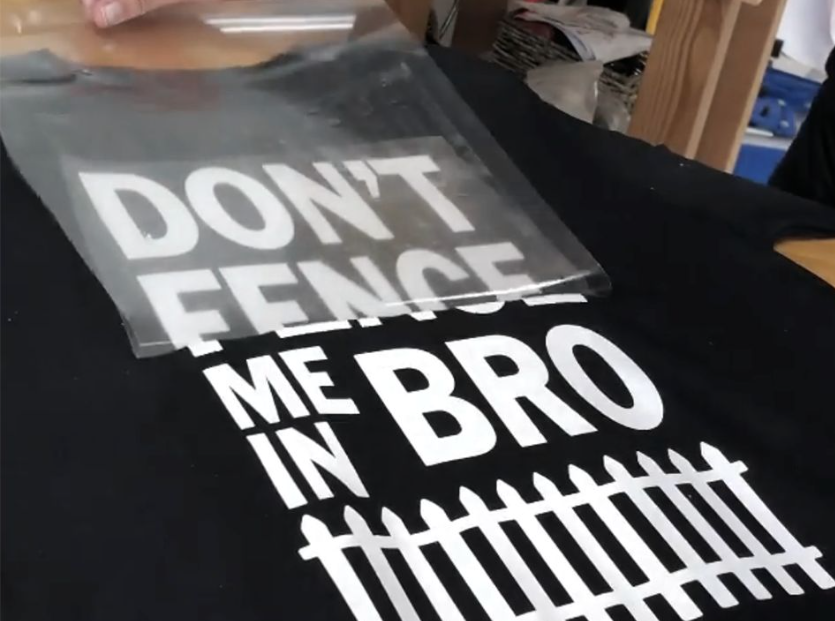
10. Why Should You Always Test and Adjust for Each Substrate?
No print runs—or fabric—are ever identical. Always check your ink and procedure on each unique substrate before diving into full manufacturing. Factors like garment colour, dye kind, and blend ratio all have an effect on how low bleed white plastisol ink behaves.
Pre-test poly blends, dark garments, and area of expertise fabric for adhesion, brightness, and bleed. Check your results after curing by way of looking at for any dye migration or changes in opacity. Adjust mesh, stay, or temp if needed for exceptional outcomes.
Remember, display printing is as a good deal art as technology. Keeping targeted notes and being organized to conform are signs of a top-tier print save.