In Summary: Key Takeaways for Superior White Screen Printing
- Use High Volume Plastisols: Always pick a excessive quality milky white plastisol ink for ambitious, vibrant results.
- Master Curing: Proper curing (correct temperature and dwell time) is essential for lengthy-lasting print effects.
- POLYESTER LOW BLEED: Polyester and polyester/cotton blends require low bleed for satisfactory effects – decreasing migration and bleed.
- Careful Mixing and Handling: Mixing, loading and storing may have a widespread impact on ink first-rate and print consequences.
- Test prints: Perform wash tests to make sure prints rise up to real wear and tear.
- Trusted manufacturers depend: Invest in reputable, relied on brands for consistent performance across all substrate kinds.
- Perfect the method: Screen length, squeegee angle and flash curing all have an effect on final opacity and coverage.
- Stay bendy: Adapt your approach to materials which includes cotton, polyester, blends and wool to maximize the benefits of white inks.
- Troubleshoot intelligently: Fine-song all manner variables to deal with problems including cracking, dulling or dye migration.
- NEVER STOP LEARNING: The best display screen printers are continuously trying out new inks, strategies and products for advanced consequences.
- By gaining knowledge of white plastisol inks and perfecting every step of the process from blending to curing, you will raise every shirt, print and display to honestly professional great.
How to make white plastisol ink smooth on shirt
White ink, plastisol ink, and the secrets behind a bold, opaque display screen print—if you’re obsessed on display printing or run a print keep, you understand these aren’t simply product buzzwords. Understanding the way to work with ağ plastizol mürəkkəbi can transform your prints from common to jaw-droppingly colourful. Whether you’re a pro printer or a shop newbie, this article will raise your white screen printing recreation, assisting you avoid common pitfalls like dye migration, susceptible coverage on darkish shirts, and undercured prints. Stick with us—you’ll discover ways to select, mix, and treatment the fine white plastisol ink, as well as find out depended on brands, top rate tips, and critical troubleshooting. Reading this manual is your shortcut to expert, crack-resistant, shiny white print inks that turn first-time customers into unswerving fanatics.
Məqalənin xülasəsi
- What Makes White Ink Essential in Screen Print Projects?
- Understanding Plastisol Ink—Why Do Printers Prefer It?
- Demystifying White Plastisol Ink: Key Properties Explained
- How Does Curing Affect White Plastisol Ink Performance?
- What is Low Bleed White Ink, and When Should You Use It?
- Tips for Printing White Ink on Cotton and Poly Shirts
- Secrets to Achieving Perfect Opacity and High Coverage
- Mixing and Handling: Getting the Most from Your Ink Gallon
- Top Trusted Brands for White Screen Printing Inks
- Troubleshooting White Ink: Solving Common Print Issues
- Conclusion: Key Takeaways for White Screen Printing Excelle
1. What Makes White Ink Essential in Screen Print Projects?
Let’s be honest—there’s nothing quite as hanging as a crisp, vibrant white print in opposition to a ambitious material color. White ink is the hero of screen print stores, essential for both underbase layers that make hues pop and stand-alone prints that call for interest. Whether you’re after a pointy white logo or a basis for overlays, mastering white ink is non-negotiable.
Why is white so elaborate? Unlike a few colorations, white ink should be each highly opaque and bendy. Dye migration, bleed, and negative fiber coverage can make your prints appearance amateurish unless you use a purpose-formulated white plastisol ink. By understanding the position of white ink, you lay the basis for each a success display print undertaking.
Plus, the usage of white as an underbase on darker clothes like cotton or polyester shirts is what lets in all of your different colorations to really shine. Without a properly implemented white display screen print, you’ll discover hues dull and dead—some thing each display printer desires to keep away from. The secret to vibrant, lasting prints often starts (and now and again ends) along with your approach to white ink.
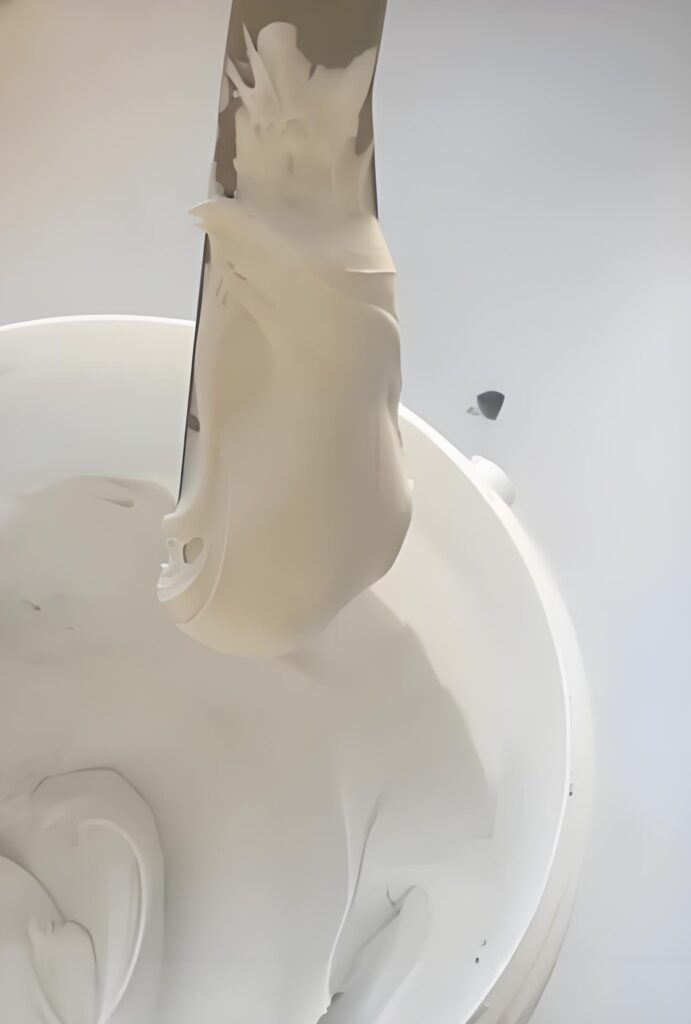
2.Understanding Plastisol Ink—Why Do Printers Prefer It?
Plastisol ink became the industry popular for a motive: it’s long lasting, smooth to paintings with, and flexible. Unlike water-based totally inks that soak into cloth, plastisol ink sits on pinnacle, forming a formidable, smooth layer after curing. This makes it best for reaching excessive-opacity consequences, particularly whilst printing white on dark shirts.
Another plus: plastisol is forgiving. You don’t should fear about the ink drying in the display screen, so that you get longer loading times and much less wasted cloth. For stores pumping out excessive-quantity orders, this indicates more constant manufacturing and fewer mishaps. It treatments thru heat as opposed to evaporation, taking into account smoother workflow and reliable results.
Most modern plastisol inks, along with ağ plastizol mürəkkəbi, are non-phthalate and safe for industrial use, meeting each safety and fine needs. Flexibility, top class smoothness, and creamy consistency make plastisol ink a favorite—no surprise so many trusted manufacturers consciousness their R&D on perfecting this type of screen printing ink.
3. Demystifying White Plastisol Ink: Key Properties Explained
Not all whites are created same. The best ağ plastizol mürəkkəbi boasts creamy viscosity, high opacity, and a balanced level of thickness. These residences make sure the ink covers even dark or colored fabrics, turning in that coveted colourful print whenever. But what’s definitely beneath the hood?
White plastisol ink have to face up to dye migration—a chemical response wherein cloth dye seeps into your ink layer, inflicting coloration shift or “bleeding.” Premium low bleed white variants are engineered for this unique motive, making them imperative for poly/cotton blends or a hundred% polyester shirts.
When evaluating a white ink, don’t forget viscosity (how thick or runny it’s far), hand sense (softness after curing), coverage, and flash properties. High opacity is a non-negotiable for display printers traumatic best white. Bonus factors for inks that offer decrease therapy temperatures to shield sensitive fabric and accelerate the production line.
4. How Does Curing Affect White Plastisol Ink Performance?
Curing might sound technical, but in practice, it’s one of the maximum essential steps for any display printer. Plastisol ink doesn’t dry within the air—alternatively, it calls for unique temperature and live time in a dryer to nicely set. The best white plastisol ink will specify a remedy temperature (frequently around 320°F/160°C), but modern low therapy and lower remedy inks may additionally set at temps as low as 260°F/127°C.
Getting this wrong can spell catastrophe: undercured ink cracks, fails the wash take a look at, or peels after some cycles. Too a lot warmth or a longer reside time, but, can also scorch the garment or motive shrinkage. Investing in a right conveyor dryer guarantees even curing across your ink deposit, but usually check thoroughly—opacity and adhesion must pass before that blouse hits your order line.
Advance tip: “flash” curing among layers (e.G., laying down a base white before hues) continues multicolor prints sharp and prevents ink migration. For stores aiming for the softest hand and flexible finish, experimenting with decrease therapy temp whites or rapid-treatment formulation is a top notch manner to stage up your display printing projects.
5. What is Low Bleed White Ink, and When Should You Use It?
Bleeding—one of the most dreaded phrases within the display screen printing global! Low bleed white plastisol ink is particularly formulated to reduce dye migration, that is in particular rampant with poly/cotton blends or polyester fabrics. When dye molecules are heated at some stage in curing, they could “migrate” into the ink layer, giving your crisp whites a pinkish or grayish tinge.
Choosing a low bleed ink is essential while printing on athletic put on, poly blends, or fleece gadgets. You’ll frequently see those categorised as “poly white” or “top class low bleed,” and they work fantastic as each underbase and stand-alone whites. Don’t forget about to preserve curing temperature low to lessen the danger similarly—sometimes the pleasant white for poly is likewise a decrease cure ink.
Proper use of low bleed white ink means fewer ruined shirts, happier clients, and less pressure on your shop. If you’re suffering with migration, ensure to change to a depended on low bleed system before your subsequent order.
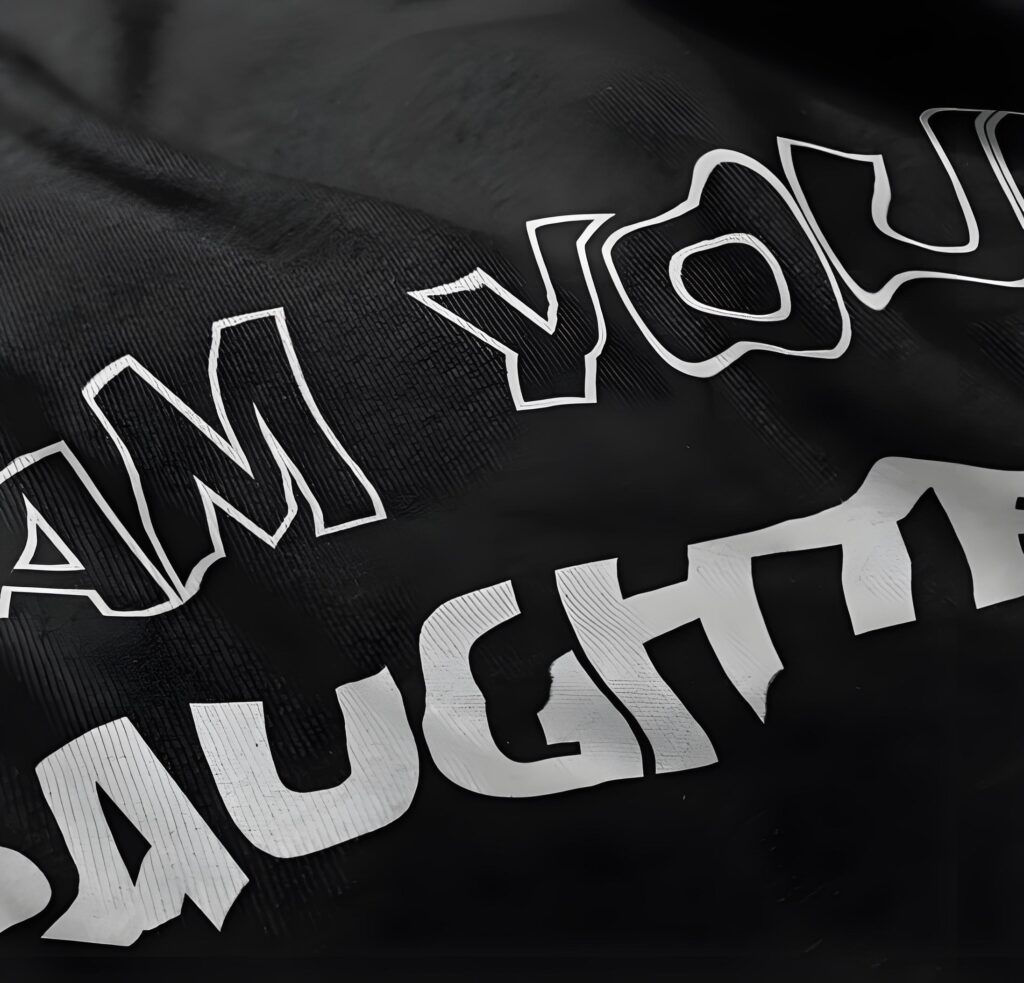
6.Tips for Printing White Ink on Cotton and Poly Shirts
Printing on cotton is typically trustworthy—high-opacity white plastisol ink effortlessly covers darker fibers, and general remedy temps do the trick. Cotton is much less liable to dye migration, so reaching vibrant white works on most shirts. However, don’t forget about mesh size and manual method; a thicker ink deposit and correct loading method improve each opacity and coverage.
Move to poly or poly/cotton blends, and the strategy shifts. Here, white ink choice will become paramount: usually take hold of a low bleed white plastisol ink, opt for a decrease treatment temp if viable, and perform a flash underbase to save you migration. Polyester substrates can retain greater warmness, so a conveyor dryer with unique controls is your pleasant buddy.
For each cloth kinds, doing a wash test is wise. Only then can you assure your print survives the toughest laundry trials without fading, cracking, or flaking.
7. Secrets to Achieving Perfect Opacity and High Coverage
Perfect white opacity isn’t just about which ink you select; it’s also approximately approach. Start by means of selecting a excessive-opacity, creamy white plastisol ink designed for formidable coverage. Next, make certain your screens are prepped with the proper mesh rely—a slightly lower mesh lets through extra ink, growing deposit and brightness.
Don’t overlook to flash cure between layers, in particular whilst printing specified or multi-shade designs on colored or black shirts. Add a properly mixed underbase to make next print inks look colourful and proper to their pantone swatches.
Brands regularly advertise their white as “premium,” “opaque,” or “perfect white”—usually take a look at person reviews and perform your very own check print earlier than committing to a complete gallon. Crushing the coverage undertaking method extra go back business and rave evaluations in your print shop24.
8.Mixing and Handling: Getting the Most from Your Ink Gallon
Even the first-class white plastisol ink can underperform if mishandled. Start every consultation with thorough blending—pigments and binders can settle, so stirring your pint or gallon before loading your display screen prevents inconsistencies. Some thicker inks might also require a little thinning (use best additives endorsed through the producer to avoid ruining opacity).
Practice mild loading at the display screen with the right squeegee angle and pressure. If you’re the use of guide strategies, watch for ink buildup and keep the screen smooth—this ensures a creamy, flexible end without undesirable texture.
Lastly, continually store your ink in keeping with label commands. Too a good deal warmness or air publicity can smash viscosity and shorten shelf existence, turning a most advantageous product right into a print keep headache. An easy to work method saves time and decreases waste, particularly in excessive-stress manufacturing environments.
9. Top Trusted Brands for White Screen Printing Inks
Investing in a relied on brand will pay huge dividends. Industry leaders offer low bleed, high-opacity, and coffee cure white plastisol ink tailored to the desires of each excessive-quantity shops and boutique printers. Look for reviews that point out “top class,” “smooth to paintings,” “works great,” and “smooth creamy” to gauge actual-world performance.
A few brands have a cult following for their white display screen printing products—whether it’s because of flexible end, formidable opacity, or reliable curing. When buying via the gallon or pint, always choose brands with sturdy customer service, clear documentation, and a history of standing behind their display printing ink5. This manner, each print—regardless of the substrate—promises a real optimal result.
10.Troubleshooting White Ink: Solving Common Print Issues
Struggling with crack-susceptible prints, bleeding, or opacity issues? Don’t panic—nearly every screen printer faces those headaches. Usually, the answer lies in revisiting your ink choice (are looking for a top class, opaque white), curing (verify temperature and conveyor dwell time), or method (optimize display screen mesh and squeegee perspective).
If prints are cracking, take a look at that your cure temp wasn’t too low and the ink nicely bonded with the fiber. Migration or bleeding signals it’s time for a low bleed method or reducing the remedy temp. Dull, thin prints may additionally want a thicker ink deposit or a brand new gallon of better-viscosity ink.
Performing a wash check on sample prints regularly ensures customers only get hold of top notch, lengthy-lasting products. Troubleshooting is straightforward when you have the know-how and persistence to deal with each variable
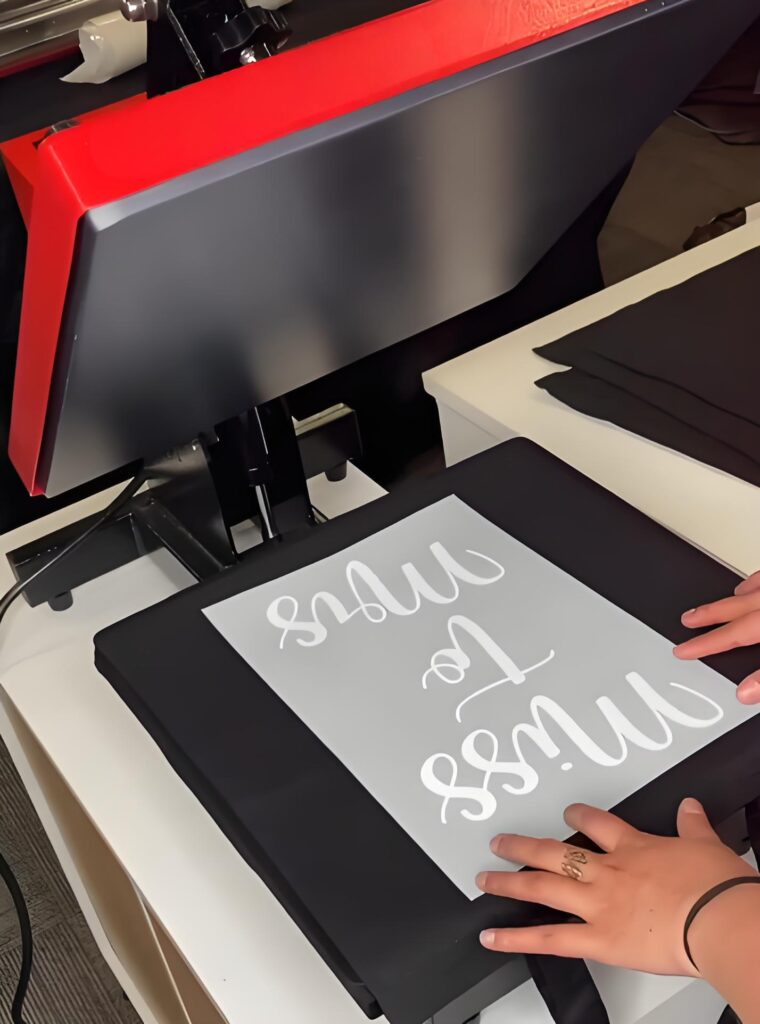