Plastisolimuste, as an important material in the printing industry, is widely used on various substrates such as T-shirts, balloons, and canvases. However, cracking in the ink is a common and frustrating problem during use. This article will delve into the causes of cracking in plastisol ink and provide comprehensive solutions focusing on the keyword “plastisol ink fix cracking”.
Sisällysluettelo
I. Yleiskatsaus plastisolimusteen halkeilusta
Halkeilu plastisolimusteessa tarkoittaa hienoja halkeamia, jotka syntyvät musteen pinnalle tai sisälle kovettumisen jälkeen. Nämä halkeamat eivät vaikuta ainoastaan painotuotteen ulkonäön laatuun, vaan voivat myös heikentää sen kestävyyttä ja markkina-arvoa. Siksi halkeilun syiden ymmärtäminen ja tehokkaiden ratkaisujen löytäminen on ratkaisevan tärkeää.
II. Plastisolimusteen halkeilun syiden analyysi
- Musteen formulaatioongelmiaMusteen koostumus on avaintekijä, joka vaikuttaa sen halkeilukykyyn. Jos musteen sisältämien komponenttien, kuten hartsien, pehmittimien ja pigmenttien suhteet ovat väärät tai jos käytetään sopimattomia lisäaineita, se voi johtaa musteen halkeilemiseen kovettumisprosessin aikana.
- Väärät kovettumisolosuhteetKovettumislämpötilalla ja -ajalla on suora vaikutus plastisolimusteen halkeilukykyyn. Jos kovettumislämpötila on liian alhainen tai kovettumisaika on liian lyhyt, muste ei ehkä koveta täysin, mikä johtaa liialliseen sisäiseen jännitykseen ja aiheuttaa halkeilua.
- Huono alustan yhteensopivuusEri substraateilla on erilainen adsorptiokyky ja yhteensopivuus plastisolimusteen kanssa. Jos muste ei ole hyvin yhteensopiva alustan kanssa, muste ei välttämättä kiinnity tiukasti alustaan kovettumisprosessin aikana, mikä johtaa halkeiluihin.
- Musteen väärä säilytys ja käyttöMusteen suorituskykyyn voivat vaikuttaa ympäristötekijät, kuten lämpötila ja kosteus varastoinnin ja käytön aikana. Pitkäaikainen altistuminen ilmalle voi johtaa hapettumiseen, mikä lisää myös halkeiluriskiä.
III. Ratkaisut plastisolimusteen halkeilemiseen
Käsitelläksemme plastisolimusteen halkeilua, voimme ehdottaa tehokkaita ratkaisuja seuraavista näkökohdista.
- Optimoi musteen koostumusBy adjusting the proportions of components such as resins, plasticizers, and pigments in the ink, or selecting more suitable additives, the flexibility and crack resistance of the ink can be improved. At the same time, ensure that the ink’s viscosity, drying speed, and curing performance meet printing requirements. Use our optimized plastisol ink formulation!
- Eri tarkoituksiin käytettävillä plastisolimusteilla voi olla erilaisia formulaatioita. Esimerkiksi T-paidan painovärit saattavat vaatia parempaa pesua ja pehmeyttä; kun taas ilmapallotulostuksen musteet saattavat tarvita vahvempaa tarttuvuutta ja joustavuutta. Siksi, kun valitset mustetta, valitse erityisten tulostustarpeiden perusteella. Custom Screen printing ink plastisol!
- Paranna kovettumisolosuhteitaSäätämällä kovettumislämpötilaa ja -aikaa voimme varmistaa, että muste reagoi täysin kovettumisprosessin aikana, mikä vähentää sisäistä jännitystä ja vähentää siten halkeiluriskiä. Harkitse lisäksi laitteiden, kuten kuumailmapistoolien tai infrapunalämmittimien käyttöä kovetustehokkuuden parantamiseksi.
- Paranna alustan yhteensopivuuttaKun valitset alustaa, varmista sen hyvä yhteensopivuus musteen kanssa. Jos alustan pinta on liian sileä tai karkea, voidaan suorittaa asianmukainen esikäsittely, kuten hionta tai pohjamaalaus, parantaakseen musteen tarttuvuutta ja kostuvuutta.
- Musteen oikea säilytys ja käyttöMustetta tulee suojata ympäristötekijöiltä, kuten lämpötilalta ja kosteudelta, säilytyksen ja käytön aikana. Ennen käyttöä se on sekoitettava perusteellisesti, jotta vältetään pitkäaikaisesta ilmalle altistumisesta johtuva hapettuminen. Tarkista lisäksi säännöllisesti musteen laatu varmistaaksesi, että se täyttää tulostusvaatimukset.
- Jos muste tuntuu käytön aikana karkealta, se voi johtua musteen sisältämistä suurista tai epätasaisesti jakautuneista pigmenttihiukkasista. Tässä tapauksessa mustetta voidaan parantaa suodattamalla se tai säätämällä dispergointiaineen määrää sen sileyden ja tasaisuuden parantamiseksi.
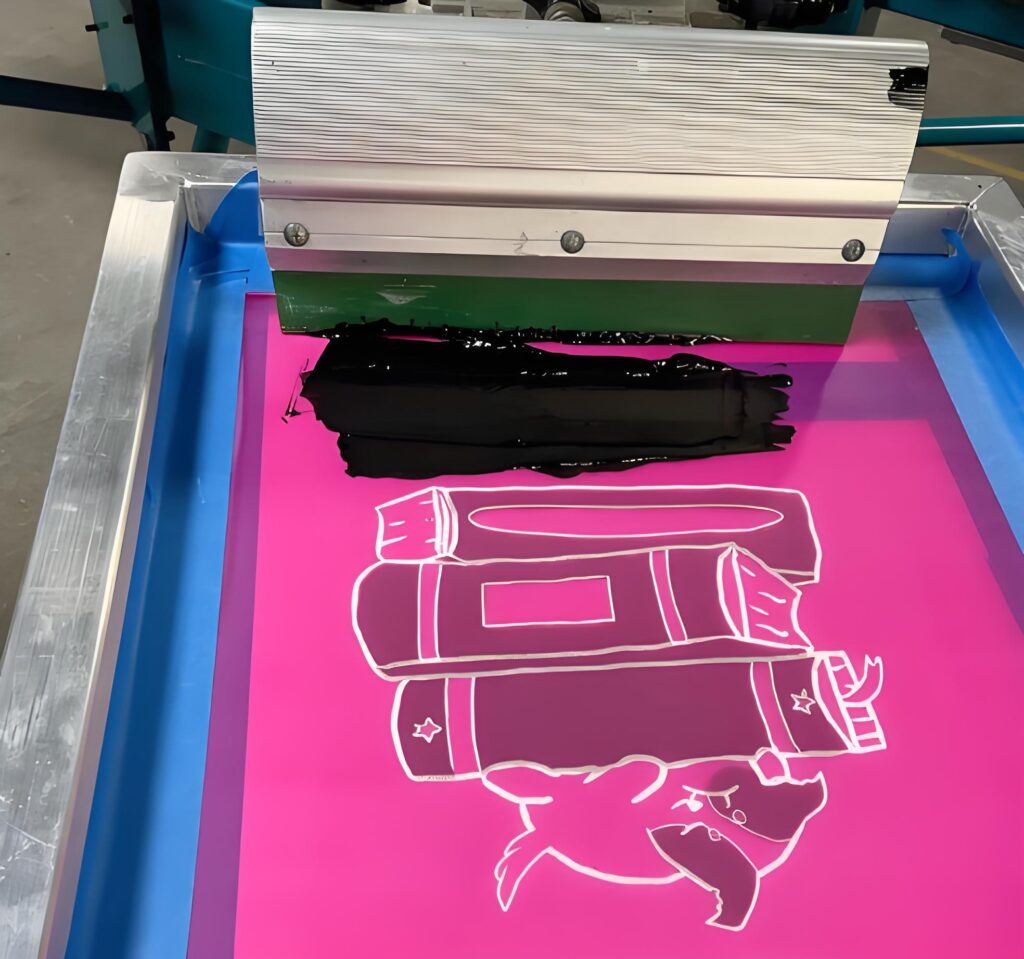
IV. Yksityiskohtaiset ratkaisut, jotka keskittyvät "Plastisol Ink Fix Cracking"
Käsitelläksemme plastisolimusteen halkeilua, tässä on joitain erityisiä ratkaisuja, jotka pyörivät painopisteavainsanan "plastisolimusteen korjaaminen halkeilun" ympärillä.
- Käytä halkeamia kestäviä pehmittimiäSopivien määrien halkeilua kestävien pehmittimien lisääminen musteeseen voi parantaa merkittävästi sen joustavuutta ja halkeilunkestävyyttä. Nämä pehmittimet voivat sitoutua tiukasti hartsimolekyyleihin, mikä vähentää musteen sisäistä jännitystä ja vähentää siten halkeiluriskiä.
- Kun esimerkiksi tulostat T-paitoja ja muste halkeilee, yritä lisätä musteeseen sopiva määrä halkeamia kestäviä pehmitteitä ja säädä tulostusprosessin parametreja, kuten tulostusnopeuden vähentäminen ja kovettumisajan pidentäminen, jotta tulostustulos paranee. Harkitse samalla sellaisten merkkien tai mallien käyttöä, jotka kestävät paremmin halkeamia.
- Säädä tulostusprosessin parametrejaPainoprosessiparametreilla on myös tärkeä vaikutus plastisolimusteen murtumiskykyyn. Säätämällä parametreja, kuten tulostuspainetta, vetolastan kulmaa ja nopeutta, musteen siirtotehoa ja kovettumissuorituskykyä voidaan optimoida, mikä vähentää halkeiluriskiä.
- Ilmapalloja painettaessa tulee niiden ohuen ja muotoaan muuttavan materiaalin vuoksi kiinnittää erityistä huomiota painoprosessin parametrien säätämiseen. Esimerkiksi tulostuspaineen vähentäminen voi estää mustetta tunkeutumasta ilmapallon sisään ja aiheuttamasta halkeamia; samanaikaisesti kovettumisajan pidentäminen varmistaa, että muste kovettuu täysin ja kiinnittyy pallon pintaan.
- Paranna musteen ja alustan välistä liimauslujuuttaEsikäsittelymenetelmät, kuten pohjustus tai hionta, voivat parantaa musteen ja alustan välistä sidoslujuutta, mikä vähentää halkeiluriskiä. Lisäksi paremman tarttuvuuden omaavien mustemerkkien tai mallien valitseminen voi parantaa tulostustuloksia.
- Kankaalle tulostettaessa tulee niiden karkean ja huokoisen pinnan vuoksi kiinnittää erityistä huomiota musteen ja kankaan väliseen sidoslujuuteen. Pohjusteella voidaan täyttää kankaan pinnan huokoset ja lisätä sen kostuvuutta; samanaikaisesti paremman tarttuvuuden omaava musteen valinta varmistaa painotehosteen laadun.
- Huolla tulostuslaitteita säännöllisestiMyös painolaitteiston kunto vaikuttaa plastisolimusteen halkeilukykyyn. Laitteen voimakas kuluminen tai väärä säätö voi johtaa epätasaiseen musteen siirtoon tai huonoon kovettumiseen, mikä lisää halkeiluriskiä. Huolla ja huolla siksi tulostuslaitteita säännöllisesti varmistaaksesi, että ne ovat hyvässä toimintakunnossa.
- Painolaitteita huollettaessa tulee kiinnittää erityistä huomiota osien, kuten pyyhkimien, seulojen ja lämmittimien puhdistukseen ja säätöön. Lastat tulee pitää terävinä ja vaihtaa säännöllisesti; näytöt tulee puhdistaa perusteellisesti ja välttää naarmuuntumista; lämmittimien tulee säilyttää tasaiset lämpötilat ja välttää ylikuumenemista tai alikuumenemisongelmia. Huollamalla ja huoltamalla painolaitteita säännöllisesti, musteen siirtotehoa ja kovettumiskykyä voidaan hyödyntää täysimääräisesti, mikä vähentää halkeiluriskiä.
V. Päätelmät
Cracking in plastisol ink is a complex and common problem that needs to be addressed from multiple aspects such as ink formulation, curing conditions, substrate compatibility, and ink storage and use. By optimizing ink formulation, improving curing conditions, enhancing substrate compatibility, and properly storing and using ink, we can effectively reduce the risk of cracking in plastisol ink. At the same time, for specific printing needs and problem situations, HONG RUISHENG can also custom plastisol ink solutions to address the challenges of cracking in plastisol ink.