Mastering Silkscreen Ink for Fabric: A Beginner’s Guide
Silkscreen printing, also known as screen printing, is a versatile and rewarding technique for creating vibrant designs on fabric. In this guide, we’ll focus on silkscreen ink for fabric, giving you the knowledge you need to master this craft. Whether you’re using water-based or plastisol ink, this step-by-step tutorial will help you achieve beautiful and durable prints.
Choosing the Right Silkscreen Ink for Fabric
When selecting silkscreen ink for fabric, it’s essential to consider the type of material you’ll be printing on. For instance, plastisol ink is commonly used for fabrics like polyester and cotton blends due to its vibrancy and durability. On the other hand, water-based inks work well on natural fabrics like cotton and linen.
- Plastisol Ink: Ideal for synthetic fabrics, offering vibrant and long-lasting prints.
- Water-Based Ink: Best suited for natural fibers, providing a softer feel on garments.
Understanding the fabric you are working with will guide you in selecting the right silkscreen ink for fabric for your project.
Preparing Your Fabric for Screen Printing
Preparation is key to achieving a high-quality print. Here’s how to get started:
- Choose the right fabric: Ensure the fabric is suitable for screen printing, like cotton or polyester blends.
- Pre-wash your fabric: This removes any chemical finishes that might interfere with the ink’s adhesion.
- Iron your fabric: Smooth out any wrinkles to ensure even ink application.
Proper preparation ensures that the silkscreen ink for fabric adheres effectively and lasts longer.
Setting Up Your Screen and Stencil
Before you begin, create a stencil of your design. You can either cut your design into acetate or use a pre-made stencil. Secure it onto the silkscreen frame with tape, ensuring that the stencil lies flat with no gaps. This is crucial for precise application of silkscreen ink for fabric.
Position your prepared fabric on a flat surface, and ensure it’s taut to prevent any movement during printing.
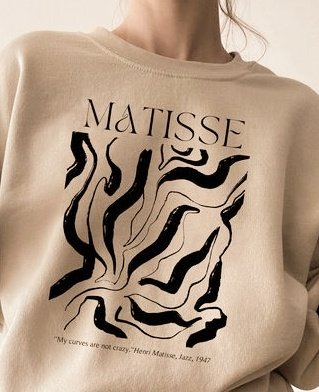
Applying Silkscreen Ink for Fabric: Step-by-Step Process
Now comes the fun part—printing your design!
- Apply the ink: Pour a small amount of silkscreen ink for fabric onto the screen. Spread it evenly across the stencil.
- Use the squeegee: Press the squeegee firmly across the screen to push the ink through the stencil onto the fabric.
- Dry the ink: Once your design is printed, allow it to dry completely before moving the fabric.
For those using plastisol ink, remember that it will need to be cured at high temperatures to bond with the fabric properly.
Curing Your Print
Curing the ink ensures your design stays on the fabric even after multiple washes. For silkscreen ink for fabric, especially plastisol ink, this step is vital. There are three common methods for curing your print:
- Heat Press: This is the most efficient method for curing plastisol prints.
- Household Iron: For smaller projects, you can use an iron to heat set the ink.
- Air Curing: Water-based inks can be left to dry naturally, though heat setting will make the design more durable.
Ensure you follow the manufacturer’s instructions when curing silkscreen ink for fabric to avoid damaging the print.
Troubleshooting Common Issues with Silkscreen Ink for Fabric
Despite best efforts, issues like cracking, fading, or improper adhesion can arise. Here’s how to troubleshoot these common problems with silkscreen ink for fabric:
- Cracking: Usually occurs with plastisol prints if the ink hasn’t been cured at the correct temperature. Ensure you’re following the proper curing process.
- Fading: Can be caused by insufficient curing. Check that the ink is thoroughly heat set before washing the garment.
- Improper Adhesion: Make sure the fabric is pre-treated and clean before applying silkscreen ink for fabric.
With these tips, you can avoid mishaps and achieve professional-quality results.
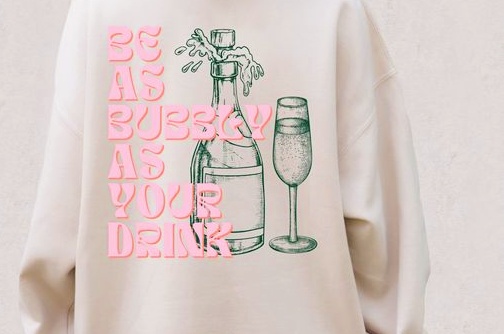
Conclusion
Mastering silkscreen ink for fabric takes time and practice, but with this guide, you’ll be well on your way to creating stunning designs. Whether you’re working with plastisol ink or water-based alternatives, these techniques will help ensure your prints are vibrant, durable, and professional.
Experiment with different fabrics, inks, and techniques, and soon, you’ll be producing custom creations that truly stand out.