If you’re a printer, graphic designer, or anyone involved in the textile and apparel industry, mastering the art of mixing and applying plastisol inks is crucial. Among the various shades and types of plastisol inks, opaque red plastisol ink stands out for its vibrancy and versatility. Whether you’re working on custom T-shirts, banners, or other promotional materials, knowing how to handle opaque red plastisol ink correctly can make a significant difference in the final product’s quality. In this comprehensive guide, we’ll explore the intricacies of mixing and applying opaque red plastisol ink, while also touching on related inks like opaque white plastisol ink, optilux reflective plastisol ink, orange glitter plastisol ink, and orange plastisol ink. Let’s dive in!
Understanding Opaque Red Plastisol Ink
Opaque red plastisol ink is renowned for its rich, bold color that covers well over various fabrics. Unlike transparent or translucent inks, opaque red plastisol ink ensures that the underlying fabric color doesn’t interfere with the printed design. This characteristic makes it ideal for creating striking graphics and detailed artwork.
Mixing Basics:
Before you start applying opaque red plastisol ink, it’s crucial to mix it properly. Ensuring an even consistency ensures a smooth printing process and superior results. Here’s a step-by-step guide to mixing opaque red plastisol ink:
- Preparation:
- Wear gloves to protect your hands from the ink.
- Ensure your workspace is clean and well-ventilated.
- Measuring:
- Use a scale to measure the exact amount of ink you need. This precision is vital for consistent color output.
- Mixing:
- Place the ink in a clean mixing container.
- Use a stirring paddle to mix thoroughly, ensuring there are no lumps or settled pigment.
- Consistency Check:
- The ink should have a thick, creamy consistency. If it’s too thin, you can add a thickening agent. If it’s too thick, you can mix in a small amount of reducer.
By carefully following these steps, you’ll have perfectly mixed opaque red plastisol ink ready for application.
Applying Opaque Red Plastisol Ink
Now that your ink is ready, it’s time to apply it. The application process involves several crucial steps, from screen preparation to printing. Let’s break it down:
- Screen Preparation:
- Ensure your screen is clean and free of any debris.
- Coat the screen with a proper emulsion and let it dry completely.
- Burn your design onto the screen using a stencil or film positive.
- Setting Up the Printer:
- Adjust your printing press to the correct settings for plastisol ink.
- Ensure that the off-contact distance (the gap between the screen and the fabric) is appropriate to prevent ink from spreading unevenly.
- Loading the Ink:
- Pour the mixed opaque red plastisol ink into the screen’s ink tray.
- Use a squeegee to spread the ink evenly across the screen’s surface.
- Printing:
- Place your fabric on the printing bed, ensuring it’s properly tensioned and aligned.
- Make a test print to check for any issues.
- Once satisfied, print your design in one smooth, even stroke with the squeegee.
- Drying and Curing:
- Allow the printed fabric to dry completely. This can take several hours, depending on the thickness of the ink and the ambient temperature.
- Once dry, cure the ink in a heat press at the recommended temperature and time. This step ensures the ink adheres properly to the fabric and is durable against washing and wear.
By meticulously following these steps, you’ll achieve crisp, vibrant prints using opaque red plastisol ink.
Using Complementary Inks: Enhancing Your Designs
While opaque red plastisol ink is a standout choice, sometimes incorporating other colors and types of inks can elevate your designs to new heights. Here’s how you can use opaque white plastisol ink, optilux reflective plastisol ink, orange glitter plastisol ink, and orange plastisol ink in conjunction with opaque red plastisol ink:
- Opaque White Plastisol Ink:
- Use opaque white plastisol ink as a base layer to ensure your red ink stands out against darker fabrics. This undercoat provides a clean, blank canvas for your red ink designs.
- Optilux Reflective Plastisol Ink:
- Incorporate optilux reflective plastisol ink to add a safety or visibility element to your designs. Reflective ink is especially useful for sportswear, safety vests, and other garments that need to be highly visible in low-light conditions.
- Orange Glitter Plastisol Ink:
- Add a sparkly, festive touch to your designs with orange glitter plastisol ink. Perfect for promotional materials, party wear, and children’s clothing, glitter ink catches the light and adds a playful dimension to your artwork.
- Orange Plastisol Ink:
- Use orange plastisol ink to create color gradients, highlights, or complementary designs that enhance your red ink prints. Orange pairs well with red, creating a warm, inviting palette that’s sure to attract attention.
Troubleshooting Common Issues
Even with careful preparation and application, issues can arise. Here are some common problems and their solutions:
- Ink Drying Too Slowly:
- Increase the drying temperature or use a fan to circulate air.
- Ink Cracking After Curing:
- Ensure the ink is fully dried before curing. Adjust the curing temperature and time if necessary.
- Poor Coverage:
- Check the ink consistency and mix it more thoroughly. Consider using an additional layer of ink if necessary.
By anticipating and addressing these issues, you can ensure your prints are of the highest quality.
Conclusion
Mastering the art of mixing and applying opaque red plastisol ink takes practice and precision. By following the steps outlined in this guide, you’ll be able to achieve vibrant, durable prints that stand out. Incorporating complementary inks like opaque white, optilux reflective, orange glitter, and orange plastisol inks can further elevate your designs, creating unique and eye-catching artwork. With patience, attention to detail, and the right tools, you’ll transform your printing projects into professional-grade creations that leave a lasting impression.
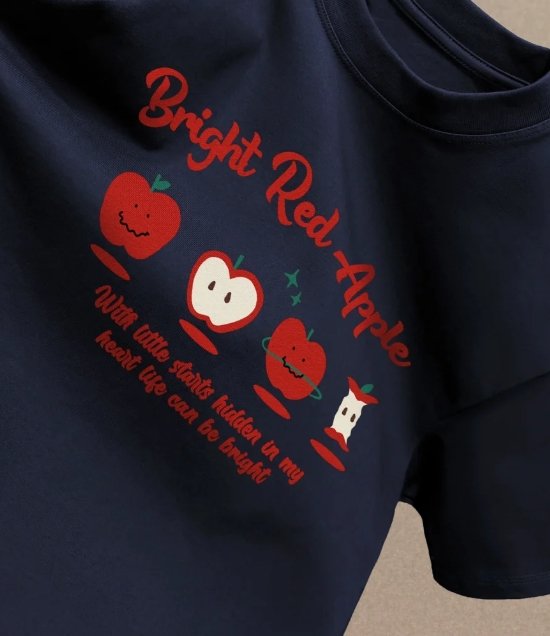