Understanding the dynamics of plastisol ink in various conditions is crucial for achieving optimal printing results. Among the myriad factors influencing plastisol ink performance, temperature plays a pivotal role, particularly in determining the plastisol ink cure time. This article delves into the intricate relationship between temperature and plastisol ink cure time, exploring how it impacts other vital aspects such as plastisol ink coverage, texture creation, crocking resistance, and the use of curable reducers.
Introduction: The Importance of Plastisol Ink Cure Time
Plastisol ink cure time refers to the duration required for the ink to fully solidify and bond with the fabric after application. Proper curing ensures that the ink maintains its vibrancy, durability, and washability. Temperature fluctuations can significantly alter this cure time, affecting both the efficiency of the printing process and the quality of the final product. Ensuring optimal cure time is thus a balance between various factors, including ink formulation, application technique, and, importantly, environmental temperature.
Temperature and the Plastisol Ink Curing Process
Plastisol ink cure time is heavily dependent on the ambient and substrate temperatures during the curing process. Plastisol inks are thermoplastic suspensions of pigments and resins in a liquid plasticizer. When heated, the plasticizer evaporates, allowing the solid particles to fuse and form a durable film on the fabric.
- Ambient Temperature Influence The surrounding temperature affects the rate of evaporation of the plasticizer, thereby influencing the plastisol ink cure time. Higher ambient temperatures accelerate the evaporation process, reducing cure time. Conversely, cooler temperatures slow down evaporation, prolonging cure time. It’s crucial to maintain a consistent ambient temperature within the recommended range (typically between 275°F to 325°F or 135°C to 163°C) to ensure uniform and efficient curing.
- Substrate Temperature Interaction The temperature of the fabric or substrate also plays a significant role. Preheating the substrate can drastically reduce plastisol ink cure time by ensuring that the ink reaches its curing temperature sooner. Preheated substrates allow for quicker evaporation of the plasticizer and fusion of ink particles, leading to faster solidification.
Plastisol Ink Coverage and Temperature
Achieving even and consistent plastisol ink coverage is another critical aspect influenced by temperature. Proper ink coverage is essential for vibrant colors and crisp details. Temperature affects ink viscosity, which in turn impacts how evenly the ink spreads across the fabric.
- Viscosity Changes As temperature increases, the viscosity of plastisol ink decreases, making it flow more freely. This can lead to better coverage, but if not controlled, it might result in ink bleeding or spreading beyond desired boundaries. Conversely, cooler temperatures increase viscosity, making the ink thicker and harder to spread evenly. Maintaining an optimal temperature ensures the ink has the right viscosity for even coverage without compromising detail.
- Curing and Coverage Interaction Efficient plastisol ink cure time is crucial for maintaining consistent coverage. If the ink is not fully cured, it may re-soften during subsequent handling or washing, causing the ink to migrate and disrupt the coverage. Temperature control ensures that the ink cures properly, locking in the coverage achieved during application.
Creating Textures with Plastisol Ink and Temperature Management
Plastisol inks are renowned for their ability to create a wide variety of textures, from smooth and flat to raised and three-dimensional. Temperature plays a key role in texture creation, impacting both the application and curing stages.
- Application Techniques Higher temperatures during application can cause the ink to spread more rapidly, making it easier to achieve certain textures like marbling or blending. Lower temperatures allow for more control over ink placement, suitable for creating precise, raised textures.
- Curing and Texture Development The plastisol ink cure time and temperature also affect the final texture. Proper curing at the correct temperature ensures that the ink solidifies with the intended texture. Under-curing can lead to soft, unstable textures, while over-curing can cause the ink to crack or lose its defined shape.
Crocking Resistance and Temperature
Crocking refers to the transfer of ink from the printed fabric to another surface, such as skin or another fabric. Temperature plays a significant role in developing crocking resistance.
- Curing and Adhesion Adequate plastisol ink cure time at the correct temperature ensures strong adhesion of the ink to the fabric fibers. Properly cured ink forms a durable bond, minimizing the risk of crocking. Incomplete curing can result in weak adhesion, making the ink prone to transfer.
- Temperature and Ink Formulation Formulating plastisol inks with crocking resistance additives can further enhance durability. However, these additives require specific curing temperatures to activate and function effectively. Maintaining the recommended temperature ensures optimal performance of these additives.
Using Plastisol Ink Curable Reducers and Temperature
Curable reducers are additives used to adjust the viscosity of plastisol inks without compromising their curability. Temperature affects how these reducers interact with the ink.
- Reducer Efficiency The effectiveness of curable reducers in modifying ink viscosity is temperature-dependent. At higher temperatures, reducers work more rapidly, thinning the ink more quickly. Lower temperatures slow down the reducer’s action, allowing for more control over viscosity adjustments.
- Curing Considerations When using reducers, it’s essential to consider their impact on plastisol ink cure time. Some reducers may require adjustments in curing temperature or time to ensure proper ink solidification. Maintaining accurate temperature control ensures that the ink cures correctly, even when reducers are used.
Conclusion: Balancing Temperature for Optimal Plastisol Ink Cure Time
In summary, temperature is a critical factor influencing plastisol ink cure time, as well as other important aspects such as coverage, texture creation, crocking resistance, and the use of curable reducers. Proper temperature management ensures efficient curing, leading to high-quality prints with vibrant colors, durable textures, and minimal crocking.
To achieve optimal results, printers must monitor and control both ambient and substrate temperatures, using preheating techniques and maintaining consistent curing temperatures. Additionally, understanding how temperature affects ink viscosity, texture development, and reducer efficiency allows for finer adjustments to the printing process.
In essence, balancing temperature is key to mastering the art of plastisol ink printing, ensuring that plastisol ink cure time is neither too long nor too short, but just right for exceptional print quality.
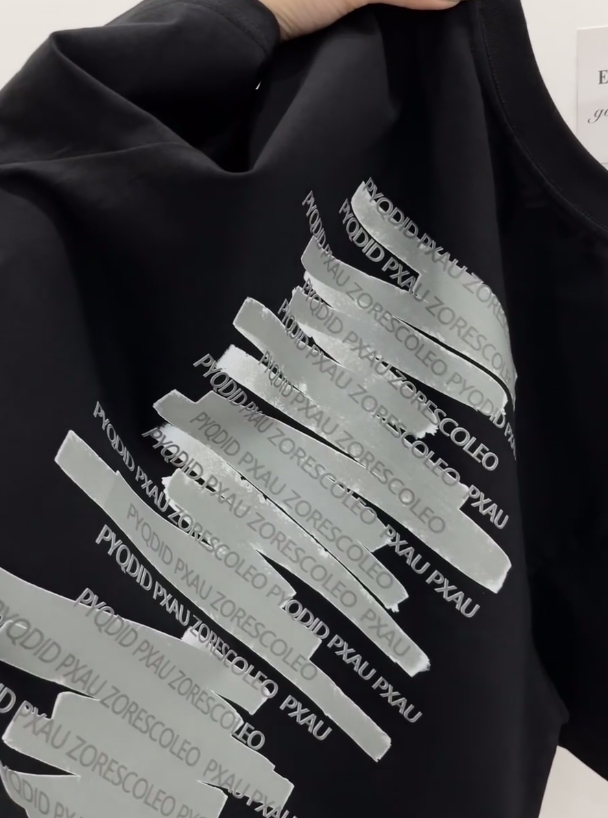