How to Ensure Plastisol Ink Doesn't Clog Screen Mesh During Screen Printing?
In the realm of screen printing, Plastisol Ink is highly favored for its vibrant colors, excellent opacity, and durability against washing and wear. However, ensuring that Plastisol Ink does not clog the screen mesh during the printing process poses a significant challenge for every printer. This article delves into effective strategies to prevent such clogging, highlighting the unique characteristics of Plastisol Ink, its comparison with water-based ink, specific products like Wilflex Plastisol Ink, and practical operational tips.
I. Understanding the Fundamental Characteristics of Plastisol Ink
Plastisol Ink is a PVC (Polyvinyl Chloride) resin-based ink that remains liquid at room temperature and transforms into a flexible, durable plastic film upon heating. Its high viscosity, while contributing to exceptional printing results, also increases the risk of mesh clogging. Understanding and mastering these characteristics is the first step towards prevention.
II. Comparing Plastisol Ink with Water-Based Ink
Plastisol vs Water-Based Ink: Compared to water-based ink, Plastisol Ink excels in color saturation, opacity, and weather resistance. However, its higher viscosity and solid content make it more prone to depositing in screen mesh and causing clogging. Therefore, selecting the right ink based on specific printing needs and product characteristics is crucial.
III. Choosing the Right Plastisol Ink Product
Wilflex Plastisol Ink, a renowned brand in the market, boasts stable performance, a wide range of colors, and superior printing effects. Choosing high-quality Plastisol Ink products like Wilflex can help reduce the risk of mesh clogging to a certain extent.
IV. Specific Measures to Prevent Clogging
1. Thorough Mesh Cleaning
Before each printing session and when changing colors, ensure the screen mesh is thoroughly cleaned to keep it unobstructed. Use specialized cleaners and tools to remove residual ink and impurities.
2. Controlling Ink Viscosity
Adjust the ink’s dilution ratio or use professional thinners to maintain Plastisol Ink’s viscosity within an optimal range. Excessively high viscosity increases the risk of clogging, while too low can compromise printing quality.
3. Even Ink Application
During printing, ensure even ink distribution on the screen mesh to prevent localized thickening that can lead to clogging. Utilize appropriate squeegee angles and pressures to optimize ink transfer efficiency.
4. Regular Equipment Maintenance
Maintain the printing equipment in good condition by regularly inspecting and replacing worn-out parts such as squeegees and screens. Additionally, control the printing environment’s temperature and humidity to minimize ink drying too quickly, which can cause clogging.
V. Emergency Handling of Clogging
Upon discovering clogged mesh, immediately stop printing and address the issue appropriately. Use fine needles or compressed air to clear clogged mesh holes or soak and rinse with specialized cleaners.
VI. Conclusion
Ensuring Plastisol Ink does not clog screen mesh during screen printing requires printers to adopt a multi-faceted approach, including selecting suitable ink products, mastering correct operational methods, regularly maintaining equipment, and promptly addressing clogging issues. By implementing these comprehensive strategies, printers can effectively reduce the risk of clogging, enhancing printing efficiency and quality.
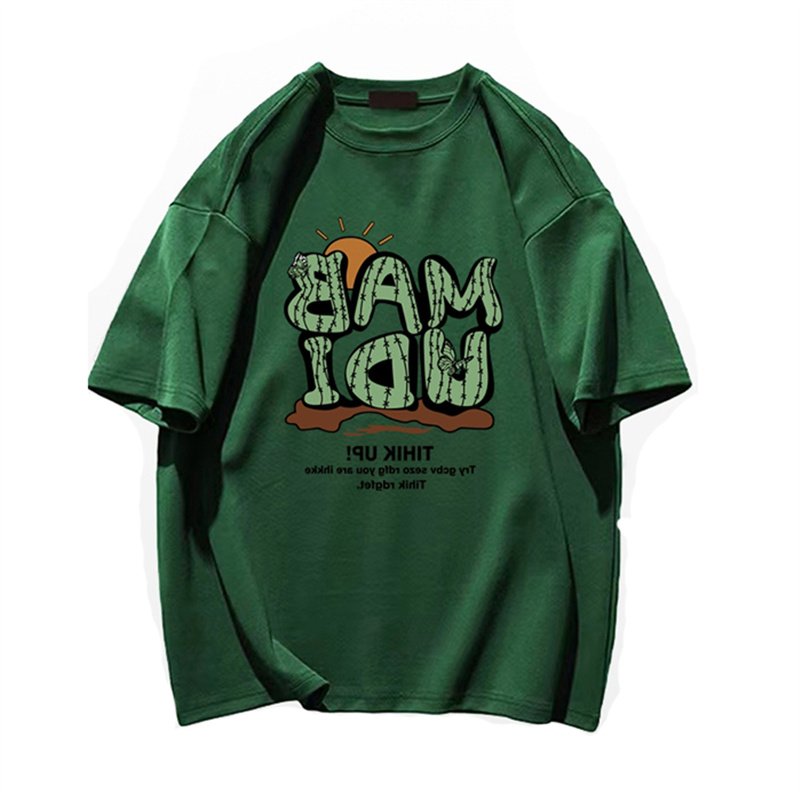