Key Takeaways: Mastering Ink, White Plastisol, and Screen Print Success
- White plastisol ink stays the enterprise preferred for ambitious, opaque outcomes on darkish fabrics.
- Ink selection—inclusive of top rate, low bleed, and high opacity alternatives—without delay affects print great and durability.
- Proper therapy with a laser gun, correct temperature, and longer dwell time is important to prevent crack, wash, or migration troubles.
- Matching ink traits to fabric (cotton, poly, mixture) and substrate guarantees coverage and vibrant results.
- Brands like Rutland supply top rate, creamy, smooth to work ink with relied on wash overall performance.
- Mesh, blend, and ink deposit depend; stability element and opacity for your specific software.
- Low therapy, non-phthalate, and DTF methods gift the next wave in garb print innovation, presenting flexibility for all clothes and garb wishes.
- Master those ideas and you may reap outstanding, resilient display screen print outcomes with each shirt—preserving your customers glad, your prints vivid, and your reputation for pleasant unshakeable
プラスチゾールの白インクが黄色く見えるのはなぜですか
概要:
Whether you’re a pro display screen printer or a curious newcomer, information the bits and bobs of ink choice—especially white plastisol ink—is important for high-impact, expert effects. This article unpacks the entirety you want to recognize approximately ink, print, and display print era, focusing on the specific challenges and exceptional practices for the use of white ink on dark clothes, low bleed desires for polyester, high opacity for bold prints, and the significance of proper cure to prevent dye migration, crack, and fading. Read on to unlock insider hints for colourful, long lasting, and smooth-hand display prints that stand out on any shirt or garb.
記事の概要
- What is White Plastisol Ink, and Why is it Essential for Screen Printing?
- How Does Ink Selection Affect Print Quality?
- Screen Print Secrets: Achieving Opaque, Bold Results on Cotton and Polyester
- Low Bleed and Dye Migration: Why They Matter for Polyester and Blends
- How to Correctly Cure White Plastisol Ink for Durability
- Exploring the Role of Mesh, Coverage, and Ink Deposit
- Premium and Trusted Brands: Comparing Rutland & Other Industry Leaders
- How to Mix, Flash, and Layer White Ink for Easy to Print Creations
- The Growing Trend: Low Cure, Flexible, and Non-Phthalate Ink Solutions
- Direct to Film and the Future of Apparel Decoration
1. 何ですか ホワイトプラスチゾルインク, and Why is it Essential for Screen Printing?
White plastisol ink stays the gold standard for display printers international, particularly in terms of reaching shiny, colourful prints on dark garments. Unlike water-primarily based ink, plastisol inks do not absorb into the cloth but as an alternative coat the fibers, turning in bold, opaque insurance that certainly pops on each cotton and polyester fabric. This belongings is mainly important for display print jobs where standout whites are non-negotiable1.
Opacity is essential in white plastisol inks. Without enough opacity, the underlying shirt color shows thru, main to stupid and disappointing consequences. A top class, excessive opacity white display screen print ink is formulated to make certain a creamy, clean to work consistency—making the print process greater constant, even for intricate artwork. The creaminess way it flows smoothly through mesh displays and lets in for thicker ink deposits while needed for full, vibrant insurance.
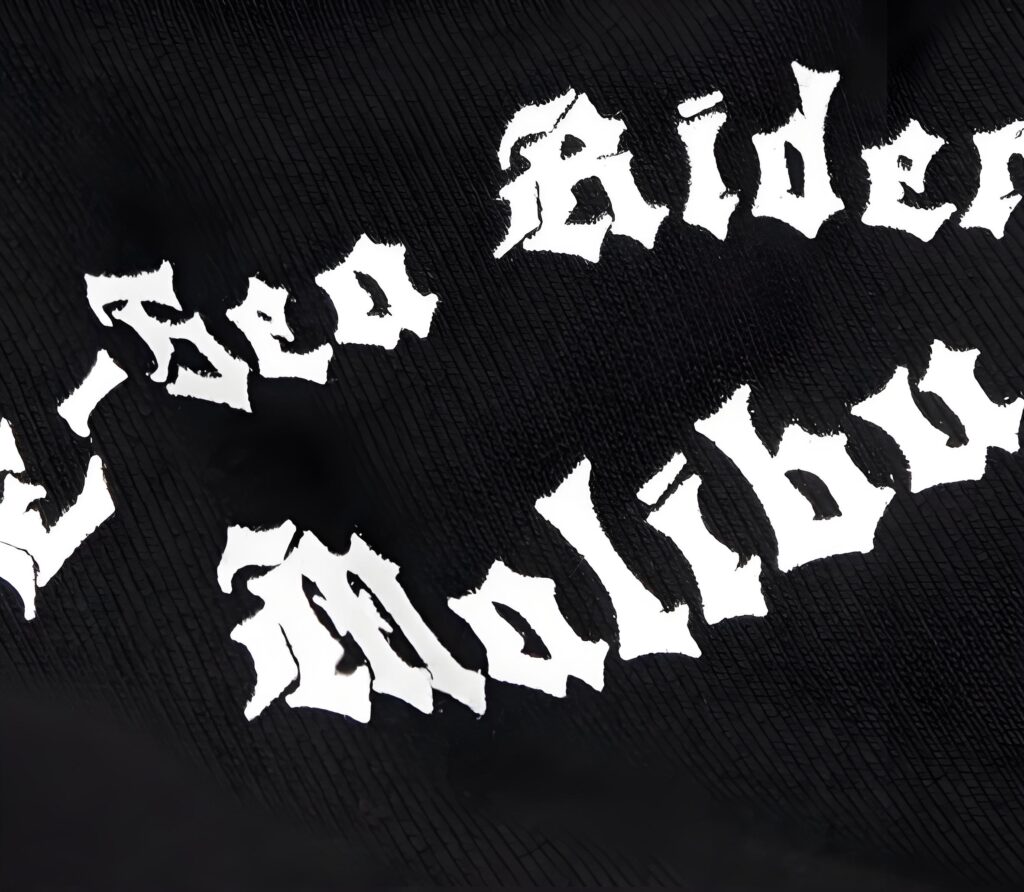
2.How Does Ink Selection Affect Print Quality?
Every print tells a tale—beginning together with your ink choice. The proper ink can imply the distinction between a flat, diminished result and a ambitious piece of clothing that grabs attention with each put on. White ink mainly affords challenges; it need to continue to be starkly opaque but bendy sufficient for smooth hand consequences on both cotton and polyester shirts.
Low bleed ink is essential while running with poly or poly combination substrates, as it prevents bleeding and dye migration which could destroy crisp white prints. Opting for thicker ink can also decorate sturdiness and resistance to crack and wash put on, supplied your dryer and cure temperatures are on factor. Trusted brands like Rutland offer a range of top class, non-phthalate print inks for nearly any garment type, giving display screen printers the flexibility to tackle cotton, blends, and fleece hopefully.
3.Screen Print Secrets: Achieving Opaque, Bold Results on Cotton and Polyester
Screen print era has superior dramatically, but getting colourful, opaque white on each cotton and polyester remains a undertaking that demands proper technique and ink selection. White ink ought to be sufficiently opaque to dam out even the boldest shirt dyes, yet easy to print in order that coverage is steady without clogging the screen or leaving rough, heavy patches.
A creamy ink texture ensures that the ink flows smoothly at the screen and without difficulty penetrates the mesh, ensuing in a soft hand even after more than one washes. Cotton shirts commonly take in ink easily, but polyester and blends require cautious interest to coverage and bleed. Flashing between layers, the use of a premium low bleed ink, and ensuring your print is cured white with the best dwell time inside the dryer prevent dye migration and guarantee lasting, vibrant results.
4. Low Bleed and Dye Migration: Why They Matter for Polyester and Blends
Low bleed is a buzzword you’ll pay attention frequently in the screen print enterprise, and for properly purpose. Polyester and mixed fabric generally tend to release dye at some point of printing—specially if therapy ink temperatures are too high. This dye can migrate into the white plastisol ink, inflicting ugly discoloration that undermines the print’s effect.
Using a committed low bleed ink specifically formulated for poly (frequently referred to as “poly ink”) is the frontline defense against dye migration. Flash techniques, mixed with a longer reside time and accurate curing temp, help seal the fibers and lock in ambitious, opaque white coverage no matter the substrate. Look for relied on brands that offer motive-constructed alternatives for poly—a ought to for premium garb and sportswear.
5.How to Correctly Cure ホワイトプラスチゾルインク for Durability
Curing white plastisol ink is greater artwork than technological know-how. Conventional plastisol inks require a treatment temperature of around 320°F, but lower cure or low remedy formulation exist for tough substances. Using a flash dryer or conveyor dryer, warmth ought to be frivolously disbursed to fully therapy ink in the course of the complete ink deposit, not just the surface.
Using a laser gun helps guarantee that the temperature on the ink layer—not just the dryer’s air—is reaching the essential treatment temp. Under-cured ink will crack, wash away, or fail a wash take a look at, while over-curing can damage the garment or cause migration. Always test special fabrics, preserve longer live time for thicker ink deposits, and confirm a flexible, tender hand put up-treatment.
6.Exploring the Role of Mesh, Coverage, and Ink Deposit
Mesh choice without delay impacts your print quality and efficiency while screening white ink. A excellent mesh gives better detail for artwork but can limit ink deposit, making it tough to obtain high opacity on dark substrates. Conversely, a decrease mesh count lets in for a thicker ink deposit and more colourful whites.
Coverage matters: a good, ambitious lay down approach fewer passes and extra constant results. Optimize your press settings—squeegee pressure, perspective, and pace—to obtain creamy, clean to print insurance together with your premium white ink. Use a white display as an underbase for other colorations when printing on darkish shirts, ensuring brightness and vibrancy inside the completed print.
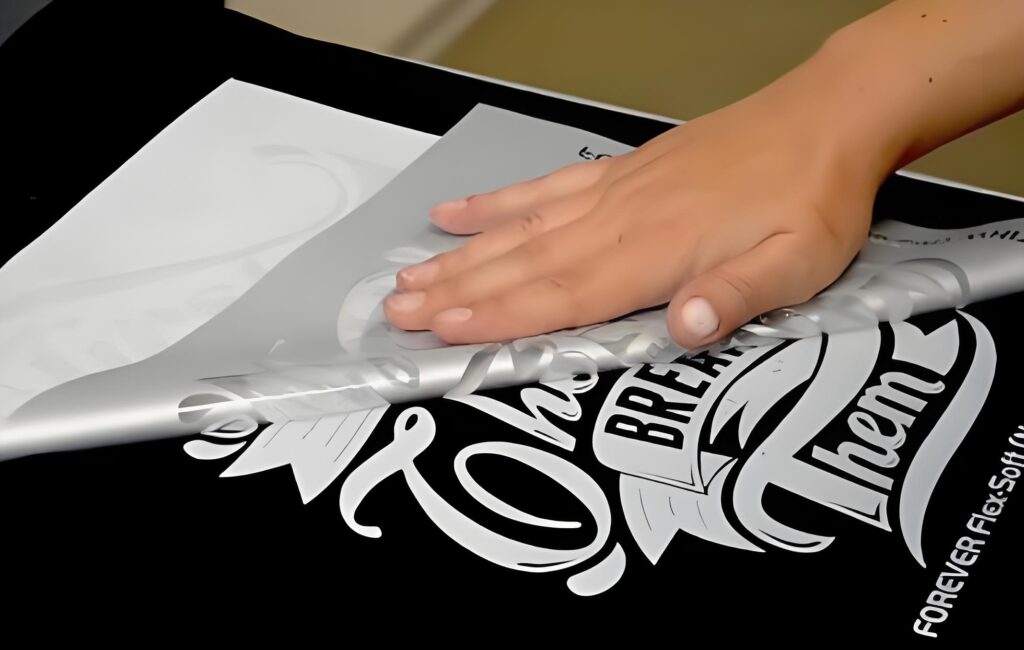
7.Premium and Trusted Brands: Comparing Rutland & Other Industry Leaders
When print performance and consistency matter, using premium ink brands is non-negotiable. Rutland is a leader in the field, offering industry-trusted white plastisol ink options for nearly every application, from high opacity cotton whites to low bleed solutions for tricky poly blends.
Trusted brands ensure that every gallon—whether in standard or 5 gallon buckets—provides reliability, creamy consistency, and compatibility with modern low cure and non-phthalate requirements. Top-tier inks also undergo rigorous wash test examination before release, so you enjoy peace of mind with every screen print job, from small-batch shirts to full apparel lines.
8.How to Mix, Flash, and Layer White Ink for Easy to Print Creations
Mixing white ink successfully guarantees that it stays creamy, clean to work, and provides both coverage and versatility. Always thoroughly blend ink within the bucket—even premium inks can settle over time—and stir vigorously for uniform texture and opacity.
Flashing among passes when laying down 白色プラスチゾルインク guarantees every layer builds up opacity without clogging the display screen or risking migration. Layering is especially useful on dark or ambitious-colored shirts: print a skinny underbase first, flash remedy, then lay down your top white. This approach locks inside the ink, imparting a flexible, tender hand and resistance to washing or cracking.
9. How to Mix, Flash, and Layer White Ink for Easy to Print Creations
Mixing white ink efficaciously ensures that it stays creamy, easy to work, and delivers each coverage and versatility. Always thoroughly mix ink in the bucket—even top class inks can settle over the years—and stir vigorously for uniform texture and opacity.
Flashing between passes whilst laying down white plastisol ink ensures each layer builds up opacity without clogging the screen or risking migration. Layering is specifically useful on darkish or formidable-colored shirts: print a skinny underbase first, flash remedy, then lay down your top white. This technique locks inside the ink, providing a bendy, tender hand and resistance to washing or cracking.
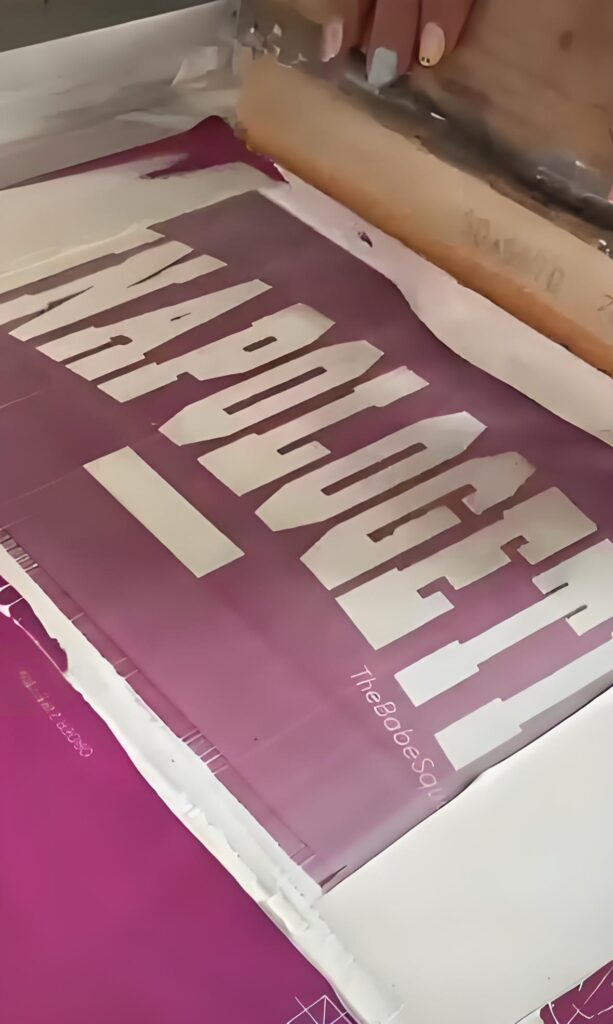
10. Direct to Film and the Future of Apparel Decoration
Direct to film (DTF) is changing the display screen print landscape. This contemporary generation makes use of print inks and adhesives to create colourful, bendy transfers that can be cured at low temperature and bonded to nearly any garment or material—including problematic poly and blends.
The mixture of traditional screen print talents and DTF generation opens new doors for clothing customization, allowing excessive-opacity ink and sharp insurance on garments formerly off-limits to conventional plastisol ink. This future-centered technique way printers can provide gentle hand, bold prints on the entirety from general cotton shirts to advanced activewear, maintaining them in advance of industry traits and consumer demand.