Bullet Point Summary: Key Takeaways for Screen Print Success
- Screen printing inks, in particular plastisol and white plastisol ink, offer creamy, opaque, clean to print answers for ambitious prints.
- The proper cure temperature and dryer stay time are critical for lasting, crack-unfastened prints—affirm with a wash test.
- Low bleed inks are critical for polyester and poly/cotton blends to save you dye migration and unwanted bleeding.
- Mesh choice and right white display screen coating ensure most opacity and crisp, ambitious designs.
- Choose ink sizes (gallon, 5 gallon, pint) in line with your keep’s workflow to save you waste and keep freshness.
- Trusted brands like Rutland and their mixing structures assist make certain consistent, top class outcomes over the long run.
- Always test, mix, and stir your inks for most advantageous creamy consistency and deposit on each substrate.
- Monitor and regulate your dryers and curing temps with gear like a laser gun for perfect whenever.
- Stay on pinnacle of advances—reflective, fluorescent, and coffee-temperature treatment plastisols are increasing what’s feasible for screen printers.
- Whether manual or automated, the important thing to memorable, lasting prints is pairing the right ink with the proper procedure—each time!
By mastering ink, print, screen print, and cure, you’re prepared to supply bold, colourful, washer-friendly designs that satisfaction each you and your clients, on every garment and every run.
Mastering Ink for Print: Everything You Need to Know About Screen Print, White Plastisol Ink, and the Perfect Cure
When it comes to handing over premium effects inside the global of display screen print, few substances remember extra than choosing the right ink—especially white plastisol ink. Whether you’re a seasoned print shop veteran or simply dipping your feet into the world of display printing, information the entirety from low bleed generation to curing temperature and gallon to five gallon field alternatives will set you aside. This blog dives deep into ink, print, screen, white displays, and treatment options, unlocking the secrets at the back of colourful, opaque, and lengthy-lasting display screen printing plastisols. Read on for arms-on recommendation, relied on manufacturers, and shop-examined tips for standout prints that undergo the wash!
Article Outline
- What Makes Screen Print Ink Different? A Look at Print Inks and Screen Printing Plastisol
- Why Is White Plastisol Ink a Staple for Every Print Shop?
- How Do You Achieve Maximum Opacity and a Bold White Ink Print?
- The Science of Cure: What Temperature Is Needed to Cure White Plastisol Ink?
- Low Bleed Ink: How to Print on Poly and Polyester Without Dye Migration
- Choosing the Right Ink for Cotton, Poly, and Blends
- Gallons, Five-Gallons, and Pints: Sizing Ink for Your Shop’s Needs
- Mixing System and Rutland Premier: Why Trusted Brands Matter
- Perfecting White Screen Coating and Mesh Selection
- Tips for Achieving Consistent Results in Your Screen Print Shop
1. What Makes Screen Print Ink Different?
A Look at Print Inks and Screen Printing Plastisol
Screen printing is particular due to its use of mainly-formulated inks that supply colourful, formidable outcomes unequalled via other printing techniques. Unlike water-based totally alternatives, plastisol ink—specially plastisol display printing ink—gives both sturdiness and a creamy texture that’s smooth to work with for big orders and complex designs. Most print stores depend on these print inks for their advanced coverage and opacity, mainly when printing on dark fabrics or creating bright, stable designs.
What simply units display screen printing plastisol apart is its ability to put down a thicker ink deposit, ensuring that even the maximum specified designs don’t crack, fade, or wash out fast. The end result? Wash-resistant prints and garments that look and experience top rate, wash after wash. On top of that, non-phthalate formulations and low bleed ink options come up with peace of thoughts for safety and overall performance in each manual and automatic display printing programs.
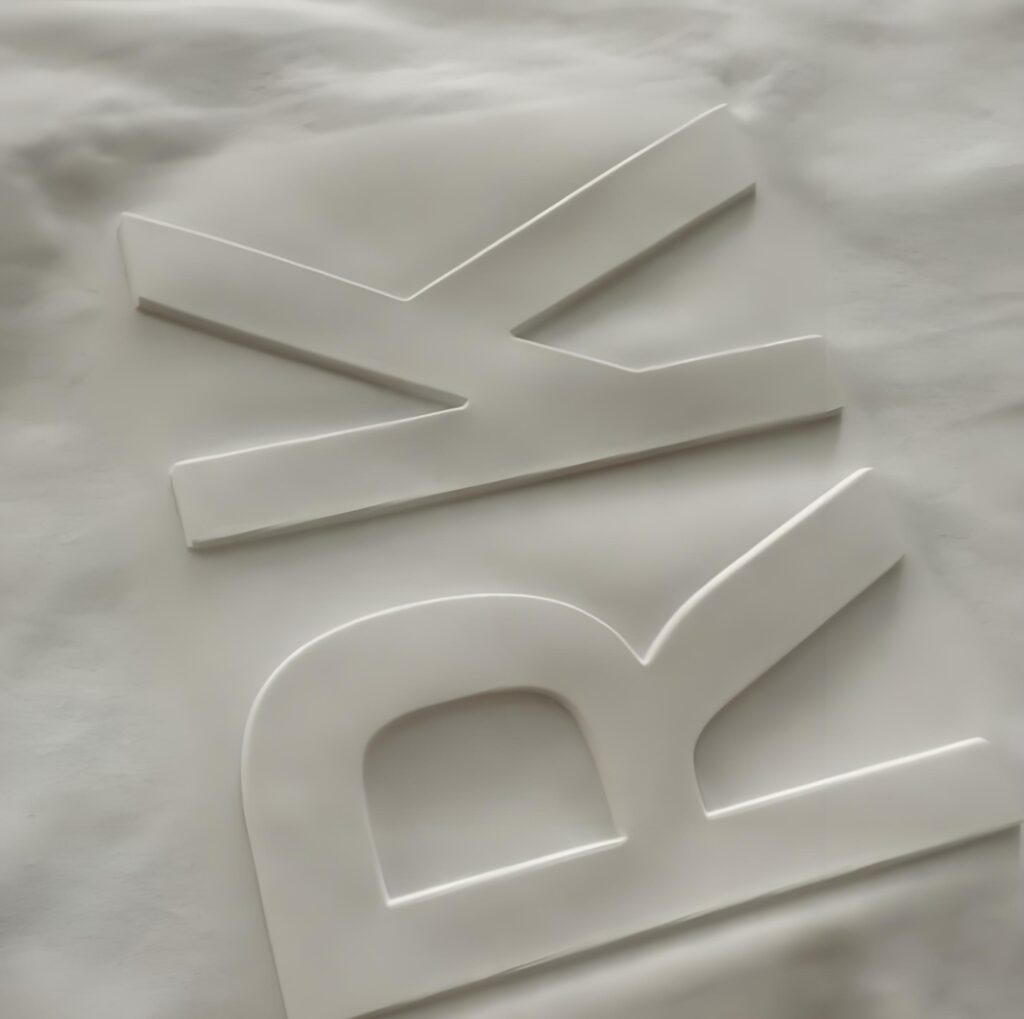
2.Why Is White Plastisol Ink a Staple for Every Print Shop?
If you ask any screen printers which ink they use maximum, the solution is normally white plastisol ink. This ink is the industry’s workhorse, prized for its capacity to supply near-ideal bases—often referred to as a white display screen—that make hues pop on shirts, hoodies, and fleece. The nice white ink is creamy, clean to print, and boasts excessive opacity for general coverage over each light and dark fabrics.
Shop owners love white plastisol ink as it therapies to a soft hand and resists dye migration and bleeding, even on tricky substrates like polyester blends. This makes it a long way greater flexible and forgiving than fashionable inks, letting you figure with cotton, poly, blends, and extra—all while lowering the danger of scorch or dye migration at higher remedy temperatures.
3.How Do You Achieve Maximum Opacity and a Bold White Ink Print?
Getting a formidable, vibrant white ink print calls for more than simply slapping any white plastisol ink on the display screen. The key lies in a aggregate of high-opacity white ink, controlled ink deposit, and precise mesh choice. Thicker ink with a creamy consistency lays down a denser layer, making sure the blouse’s original coloration doesn’t display via.
For the brightest print, it often makes sense to do a -bypass print or comprise a flash between layers, permitting every bypass to semi-remedy earlier than the next is implemented. This method creates a ambitious, reflective surface that actually sticks out. Remember, excessive opacity isn’t pretty much look; it additionally covers capability dye migration from polyester fibers, in particular whilst running with low bleed or top rate whites.
4.The Science of Cure: What Temperature Is Needed to Cure White Plastisol Ink?
Curing ink is the single most critical step in screen print success. If you beneath-cure, your print will crack or wash out; over-remedy, and you hazard scorching or negative the garment. The industry preferred for therapy temperature is generally 320°F (160°C), though a few low therapy and occasional-temperature therapy plastisol inks are engineered to treatment at just 260°F–280°F.
Getting the therapy right manner balancing ink chemistry, dryer settings, and shirt/material type. Using a laser gun to test surface temperature of the ink because it exits the dryer is a store vital. Longer reside time or a better temperature therapy can be needed for thick ink deposits or fleece, while lighter fabrics and occasional cure inks benefit from quicker, lower-temperature treatment options. Always take a look at with a wash test to verify which you’ve cured the ink absolutely and carried out a smooth hand, crack-loose end.
5.Low Bleed Ink: How to Print on Poly and Polyester Without Dye Migration
Printing on polyester or blends offers a infamous challenge: dye migration. When exposed to heat during therapy, polyester dye can sublimate and bleed into the ink, turning vivid white into a dingy red or gray. The answer? Use low bleed ink, especially formulated to dam dye migration beneath the heat of the dryer.
Low bleed white plastisol ink capabilities additional blockading retailers and a higher opacity, helping to shape a barrier between the dye and the floor of the ink. That approach much less danger of bleeding and bolder, longer-lasting whites—even on hard substrates like poly fleece and athletic wear. Keeping your therapy temp as low as encouraged by using the ink manufacturer also helps, as decrease temperatures imply less opportunity for dye migration.
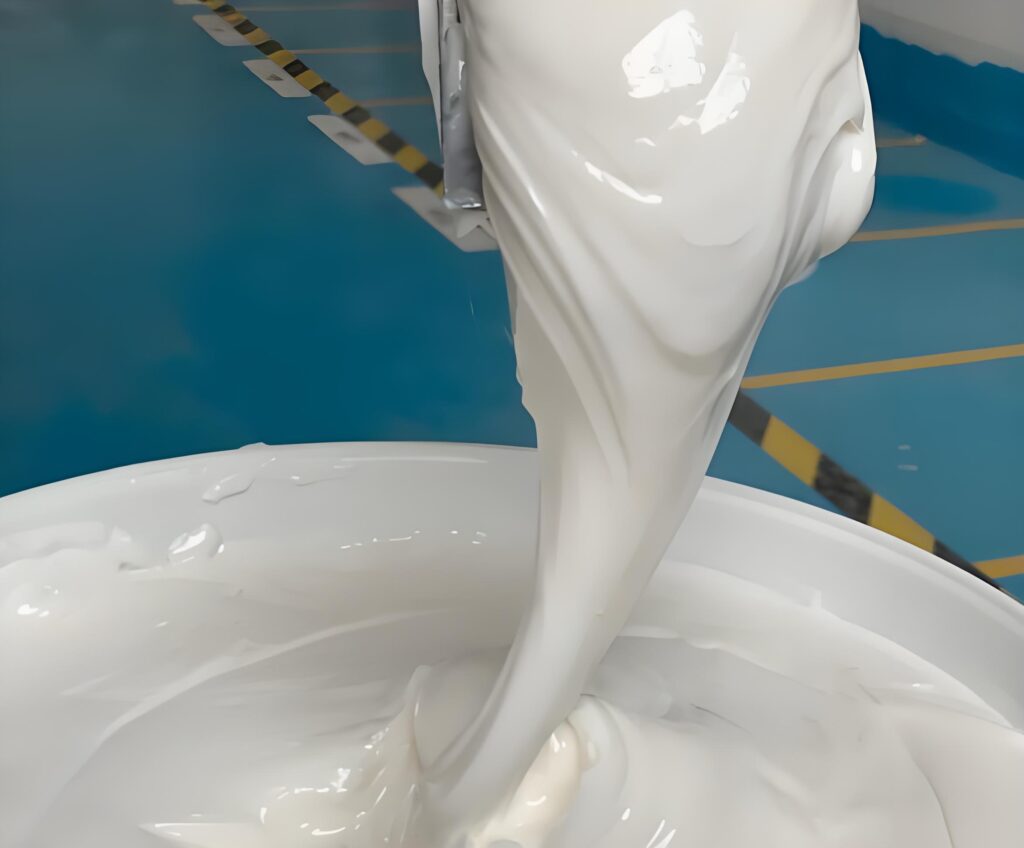
6.Choosing the Right Ink for Cotton, Poly, and Blends
Each material responds otherwise to ink, cure, and usual printing technique. Cotton is absorbent and responds properly to maximum preferred plastisol inks, turning in a bold, colourful end with dependable wash durability. Polyester, especially the more moderen overall performance blends, typically needs low bleed or low treatment plastisol to prevent bleeding and make sure most opacity.
For blends, it’s all about stability: choose inks especially classified as “poly/cotton mixture well suited” or use a mixing device like Rutland’s finest line to create a custom system. This compatibility ensures the ink bonds to each fiber, coping with each natural cotton and synthetic polyester, and reduces troubles like dye migration, cracking, and sizzling.
Each material responds otherwise to ink, cure, and usual printing technique. Cotton is absorbent and responds properly to maximum preferred plastisol inks, turning in a bold, colourful end with dependable wash durability. Polyester, especially the more moderen overall performance blends, typically needs low bleed or low treatment plastisol to prevent bleeding and make sure most opacity.
7.Gallons, Five-Gallons, and Pints: Sizing Ink for Your Shop’s Needs
Ink bins are available in each size, from pint samplers to large 5 gallon buckets ideal for high-volume stores. Your choice depends on your output—small-scale print jobs or prototyping may simplest demand a quart or pint, while a bustling print save churning out loads of prints in step with day will fast go through gallons.
Premium manufacturers like Rutland offer white plastisol ink in without difficulty resealable gallon and 5 gallon boxes to hold your save strolling smoothly. Storing ink properly guarantees consistent coverage, clean to work consistency, and no premature drying or contamination. Invest in sizes based totally for your workflow to minimize waste and maintain print quality excessive.
8.Mixing System and Rutland Premier: Why Trusted Brands Matter
When you need steady outcomes and vibrant, reliable color matching, using a relied on emblem’s mixing system is vital. Brands like Rutland are enterprise leaders, presenting each pre-mixed and customizable structures for white ink and a spectrum of other colorings. The most beneficial strains generally characteristic high opacity, low remedy alternatives, and work well throughout cotton, poly, and blends.
A nicely-designed blending device helps you to create custom whites for specific applications—whether or not you need more low bleed for artificial fibers or a general explore for cotton shirts. Trusted manufacturers also spend money on top rate non-phthalate formulations, supplying you with safety, performance, and compliance all in one formidable ink box.
9.Perfecting White Screen Coating and Mesh Selection
A ideal white screen starts with the right coating and mesh depend. Coating your display correctly guarantees that your white plastisol ink forms a crisp stencil, allowing for smooth to print operation and sharp, formidable designs. Mesh be counted influences ink deposit: a lower mesh (85–110) permits more ink thru for additonal opacity, while better mesh counts (156–230) are ideal for detailed designs wherein a softer hand is favored.
Pay careful attention to mesh anxiety, emulsion thickness, and drying so your white ink sits atop the fibers, no longer sinking into the fabric. The result? The ultimate soft hand print, complete insurance, and fascinating opacity for any garment.
10.Tips for Achieving Consistent Results in Your Screen Print Shop
No depend how superior your print shop, consistency is prime. Always stir your ink earlier than each use to ensure creamy consistency, and hold your dryer calibrated for goal temperature cure. Run frequent wash checks to capture any curing troubles before a process is going out the door.
Train your team inside the fundamentals—ink choice for cloth kind, proper display screen setup, flash curing among passes, and normal device upkeep. Invest in top rate, low bleed, and coffee therapy inks in which needed, and continually maintain a record of a hit settings for future reference. Consistent method equals constantly colourful monitors and happy customers.
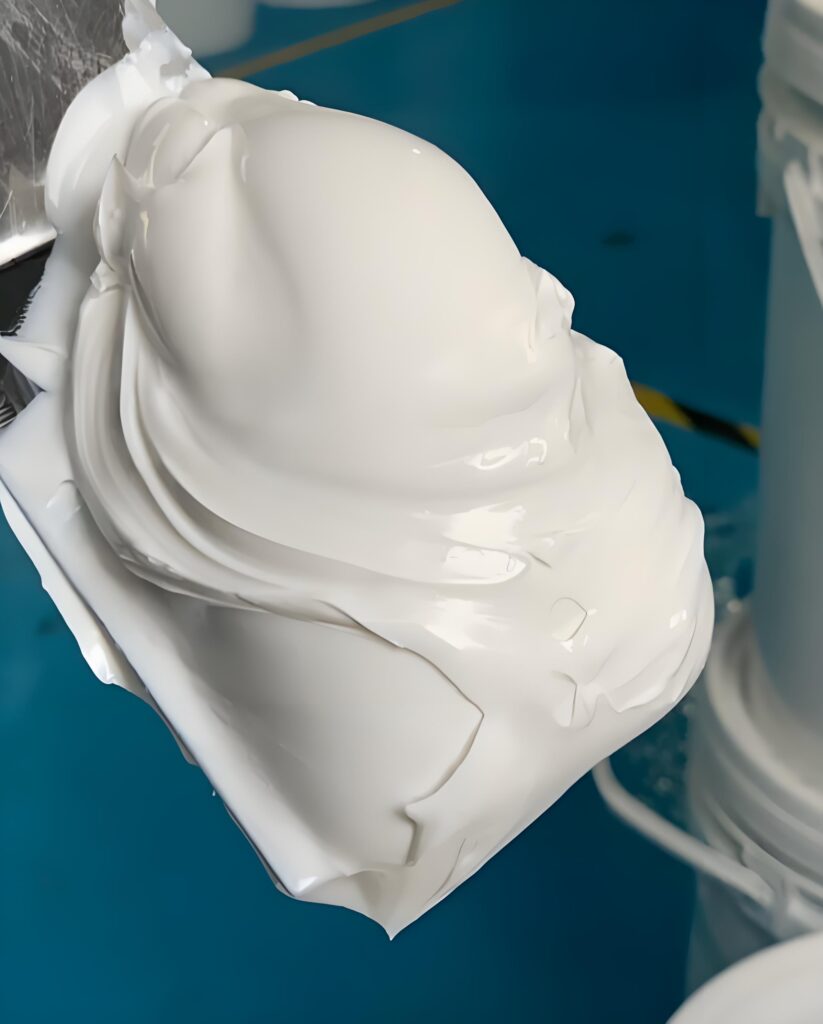