In the vast world of screen printing, process black plastisol ink stands out as a reliable and versatile choice for creating bold, durable prints. Whether you’re a seasoned professional or a newcomer to the industry, understanding the formulation process of process black plastisol ink is crucial to achieving high-quality results. This article delves into the intricacies of how process black plastisol ink is made, its unique properties, and why it remains a popular choice among printers. By the end, you’ll have a comprehensive understanding of this remarkable ink, including its formulation, benefits, and comparison to water-based inks.
The Basics of Process Black Plastisol Ink
Process black plastisol ink is a type of ink used primarily in screen printing. It’s composed of plastic particles suspended in a liquid carrier, which, when heated, fuses together to form a smooth, durable print. Unlike water-based inks, plastisol inks don’t dry through evaporation; they undergo a chemical change when exposed to heat, making them ideal for applications that require fade and scratch resistance. Process black plastisol ink, specifically, is known for its rich, consistent black color that can produce sharp, detailed prints per gallon of plastisol ink.
The Formulation Process
The formulation of process black plastisol ink involves several critical steps, each contributing to the ink’s final properties.
1. Pigment Selection
The first step in formulating process black plastisol ink is selecting the right pigment. Pigments are the colorants that give the ink its characteristic black hue. For process black plastisol ink, high-quality carbon black pigments are often used due to their strong color intensity and lightfastness. The pigments are meticulously blended to ensure consistent coverage and color saturation in prints per gallon of plastisol ink.
2. Resin and Plasticizer Addition
Next, resins and plasticizers are added to the pigment mixture. Resins act as binders, holding the pigment particles together and adhering them to the substrate. Plasticizers, on the other hand, improve the flexibility and workability of the ink. Together, these components form the core of the plastisol ink, allowing it to flow smoothly through the screen and fuse into a durable print when heated.
3. Liquid Carrier Incorporation
The pigment, resin, and plasticizer mixture is then suspended in a liquid carrier, typically a solvent or water-based solution. This liquid carrier keeps the solid components in suspension, allowing the ink to maintain a uniform consistency. The choice of liquid carrier can affect the ink’s viscosity, drying time, and overall performance.
4. Milling and Mixing
Once all components are combined, the mixture undergoes a milling process to ensure the pigments are evenly dispersed throughout the liquid carrier. This step is crucial for achieving consistent color and print quality. After milling, the ink is mixed thoroughly to blend all components evenly, creating a homogeneous mixture ready for use.
5. Quality Control
Finally, the formulated ink undergoes rigorous quality control testing. This includes checks for viscosity, color consistency, and printability. Only inks that meet strict quality standards are approved for use, ensuring that every gallon of process black plastisol ink produces high-quality prints.
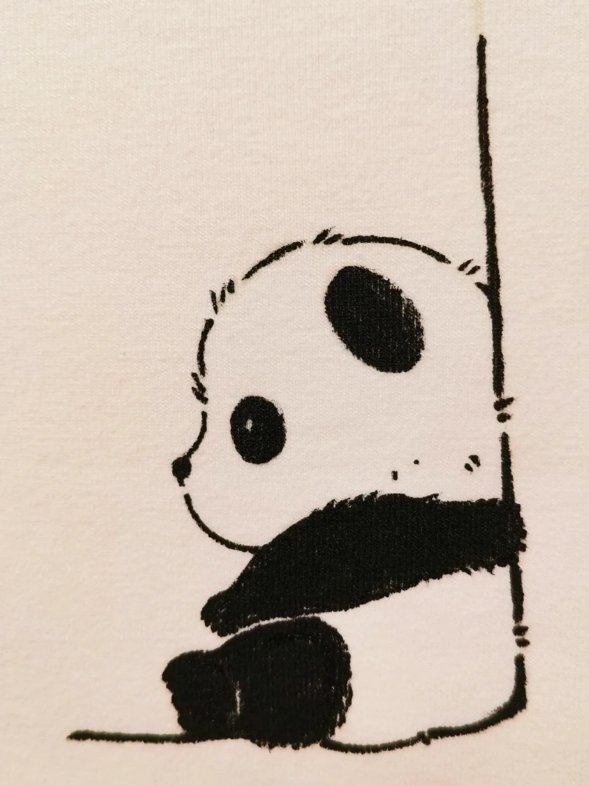
Benefits of Process Black Plastisol Ink
Process black plastisol ink offers numerous advantages over other types of inks, making it a popular choice for screen printers.
1. Durability
One of the most significant benefits of process black plastisol ink is its durability. Due to its plastic-based composition, plastisol inks are highly resistant to fading, scratching, and wear. This makes them ideal for applications that require long-lasting prints, such as signage, apparel, and promotional materials.
2. Vibrant Color
Process black plastisol ink produces rich, consistent black colors that are unmatched by other types of inks. The high-quality pigments used in its formulation ensure sharp, detailed prints with excellent color saturation.
3. Versatility
Plastisol inks are versatile and can be used on a wide range of substrates, including fabrics, plastics, metals, and paper. This versatility makes process black plastisol ink a go-to choice for printers working with diverse materials.
Comparison: Pros and Cons of Water-Based vs. Plastisol Inks
While process black plastisol ink offers many benefits, it’s essential to understand the differences between water-based and plastisol inks to make informed decisions about which type of ink is best for your needs.
Pros of Water-Based Inks:
- Environmentally Friendly: Water-based inks are more environmentally friendly than plastisol inks, as they contain fewer volatile organic compounds (VOCs) and can be disposed of more easily.
- Faster Drying: Water-based inks dry quickly through evaporation, allowing for faster production times.
Cons of Water-Based Inks:
- Durability: Water-based inks are less durable than plastisol inks, prone to fading and wear over time.
- Limited Color Range: Water-based inks may not offer the same vibrant color range as plastisol inks, particularly in dark shades like black.
Pros of Plastisol Inks:
- Durability: Plastisol inks, including process black plastisol ink, are highly durable, resistant to fading, scratching, and wear.
- Vibrant Color: Plastisol inks offer a wide range of vibrant colors, including rich black shades.
Cons of Plastisol Inks:
- Environmental Impact: Plastisol inks contain higher levels of VOCs and require special disposal methods to minimize environmental impact.
- Slower Drying: Plastisol inks dry through a chemical process that requires heat, making production times slower than with water-based inks.
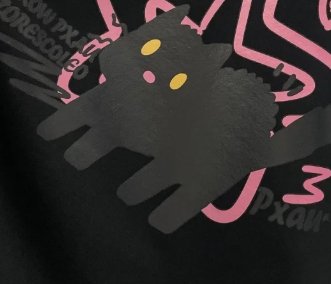
Proper Disposal of Plastisol Ink
Given the environmental concerns associated with plastisol inks, proper disposal is crucial. Unlike water-based inks, which can be disposed of down the drain with minimal impact, plastisol inks require special handling. Used plastisol ink should be collected in sealed containers and disposed of according to local regulations. Many printers opt for recycling services that can repurpose the ink components or safely dispose of them in environmentally friendly ways.
Conclusion
Understanding the formulation process of process black plastisol ink is essential for achieving high-quality prints that meet your clients’ needs. From pigment selection to quality control, each step in the formulation process contributes to the ink’s unique properties and benefits. While water-based inks offer environmental advantages and faster drying times, plastisol inks, including process black plastisol ink, stand out for their durability and vibrant color. With proper disposal practices, plastisol inks can be used responsibly, minimizing their environmental impact. By choosing the right ink for your projects, you can ensure that your prints are not only beautiful but also long-lasting.