In the vibrant world of screen printing, red plastisol screen printing ink stands out as a staple for creating bold, eye-catching designs on various fabrics. Its rich hue and versatility make it a popular choice among designers and printers alike. But how durable is this vibrant ink when applied to different fabric types? This article delves into the durability of red plastisol screen printing ink, examining its performance across diverse materials and incorporating reviews of specific ink formulations like rapid cure plastisol ink, red 485 plastisol ink, red puff plastisol ink, and reducing white plastisol ink.
Understanding Red Plastisol Screen Printing Ink
Red plastisol screen printing ink is a type of ink formulated with a plastic suspension in a liquid carrier. It is known for its opacity, vibrancy, and durability. Unlike water-based inks, plastisol inks do not absorb into the fabric but sit on top, forming a slightly raised layer. This characteristic not only adds texture but also enhances the ink’s resistance to fading and wear.
Durability Across Fabric Types
The durability of red plastisol screen printing ink varies depending on the fabric it’s printed on. Different fabrics have unique properties that can affect the ink’s adhesion, flexibility, and longevity.
Cotton
Cotton is a versatile fabric that works well with red plastisol screen printing ink. The ink adheres well to cotton’s fibers, creating a durable print that can withstand frequent washing and wear. The ink’s plastic-like finish also adds a layer of protection, ensuring the print maintains its vibrancy over time.
Polyester
Polyester is another common fabric that pairs well with Red Plastisol Screen Printing Ink. The synthetic fibers of polyester provide a smooth surface for the ink to adhere to. However, it’s essential to use an ink formulation specifically designed for synthetic fabrics to ensure optimal durability. Rapid cure plastisol inks, which dry quickly and adhere well to synthetic materials, are ideal for polyester.
Nylon
Nylon is a durable fabric often used in athletic wear and outdoor clothing. When paired with red plastisol screen printing ink, it offers a robust printing surface. The ink’s flexibility allows it to move with the fabric, maintaining the integrity of the print even under stress. For best results, consider using an ink like Red Plastisol Screen Printing Ink, known for its excellent adhesion and durability on nylon.
Mixed Blends
Fabrics made from blends of cotton, polyester, and other fibers can be challenging to print on. The mix of fiber types can affect ink adhesion and durability. However, red plastisol screen printing ink, with its plastic-like properties, adapts well to these fabrics. Choosing an ink with good elastic properties, such as red puff plastisol ink, ensures the print retains its shape and color even when stretched.
Factors Affecting Durability
While the fabric type plays a significant role in the durability of red plastisol screen printing ink, other factors also come into play.
Pre-Treatment
Proper fabric pre-treatment is crucial for ink adhesion. Pre-treating fabrics with appropriate primers or binders ensures that the ink bonds well with the fabric fibers, enhancing durability.
Ink Formulation
The specific formulation of the Red Plastisol Screen Printing Ink can also affect durability. High-quality inks with good pigment dispersion and binder systems offer better resistance to fading, cracking, and wear. Reviews of various ink formulations, such as rapid cure plastisol inks, can provide valuable insights into their performance and durability.
Printing Technique
The printing technique used can also impact the durability of the ink. Ensuring proper ink deposition, pressure, and squeegee angle during the printing process helps in achieving an even, well-adhered print.
Post-Processing
Post-processing steps, such as drying and curing, are essential for ensuring the durability of the printed fabric. Proper drying removes excess moisture, while curing solidifies the ink, making it more resistant to wear and fading.
Specific Ink Formulations
Different formulations of red plastisol screen printing ink are designed to cater to a variety of printing needs, each offering unique benefits that can significantly enhance durability and performance. From standard inks to specialty blends, these formulations are tailored to meet the demands of specific applications, fabrics, and design requirements.
For instance, high-opacity Red Plastisol Screen Printing Ink are formulated to provide excellent coverage on dark fabrics, ensuring the vibrancy of the red color remains true and bold. These inks are ideal for creating striking designs that stand out, even on challenging backgrounds. On the other hand, low-bleed formulations are specifically engineered for use on synthetic fabrics like polyester, preventing dye migration and preserving the clarity of the red ink over time.
Specialty options, such as red puff plastisol inks, add a dimensional effect to designs while maintaining their durability through multiple washes and wear. Meanwhile, rapid cure formulations are perfect for high-speed production, offering quick drying and curing times without sacrificing the longevity of the prints.
In addition to durability, many modern formulations incorporate advanced features like improved stretchability for athletic and performance wear or enhanced adhesion for complex substrates such as nylon and blends. These innovations ensure that red plastisol screen printing inks not only deliver visually stunning results but also stand up to rigorous use in various environments.
By understanding the distinct advantages of each formulation, screen printers can select the ideal Red Plastisol Screen Printing Ink to meet their project’s specific needs, ensuring both quality and durability in every print.
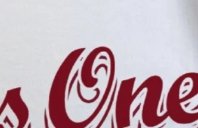
Rapid Cure Plastisol Ink
Rapid cure plastisol inks are a game-changer for screen printers operating in high-speed production environments where efficiency and turnaround time are critical. These specially formulated inks are designed to dry and cure significantly faster than traditional plastisol inks, reducing production times without compromising the quality of the final prints.
One of the standout features of rapid cure plastisol inks is their excellent adhesion to a wide range of fabrics, including synthetic materials such as polyester, nylon, and blends. This makes them an ideal choice for printing on sportswear, performance gear, and other synthetic garments that demand durability and precision. The inks create a strong bond with the fabric, ensuring that the prints stay intact even with frequent use, washing, and exposure to environmental elements.
In addition to their speed and adhesion properties, rapid cure plastisol inks produce vibrant, high-opacity prints that retain their color intensity over time. The quick-curing nature of these inks is particularly advantageous for busy print shops or large-scale production runs, as it enables faster handling and minimizes the risk of smudging or imperfections during the curing process.
Moreover, rapid cure plastisol inks are versatile, allowing for excellent results in both single-color and multi-color printing applications. They are compatible with various curing methods, including flash dryers, conveyor dryers, and heat presses, making them adaptable to different production setups.
For printers looking to boost efficiency while maintaining superior print quality, rapid cure plastisol inks provide the perfect balance of speed, durability, and vibrant results. With proper handling and curing techniques, these inks can help streamline workflows and deliver exceptional prints that meet the demands of both the production team and end customers.
Red Plastisol Screen Printing Ink
Red Plastisol Screen Printing Ink is highly regarded for its bright, eye-catching hue and exceptional performance on nylon and other synthetic fabrics. This ink stands out for its ability to deliver vivid, long-lasting prints that maintain their brilliance even under demanding conditions. Whether used for athletic wear, outdoor gear, or promotional items, Red Plastisol Screen Printing Ink is a reliable choice for projects that require both visual appeal and durability.
One of the key features of Red 485 plastisol ink is its high pigment load, which ensures bold and vibrant prints with excellent opacity. This means that even on dark or heavily textured synthetic fabrics, the red color remains intense and true to its intended shade. This characteristic makes it an ideal solution for designs that need to pop against challenging backgrounds.
In addition to its vibrant color, Red 485 plastisol ink offers outstanding durability. It adheres firmly to synthetic fabrics, resisting cracking, peeling, and fading over time, even with repeated washing and exposure to the elements. This makes it a preferred choice for creating high-quality prints on items like sports jerseys, jackets, bags, and other nylon-based products.
To maximize the performance of Red 485 plastisol ink, proper preparation and curing are essential. Pre-treating synthetic fabrics to improve adhesion and ensuring the ink reaches the correct curing temperature will help achieve optimal results. By combining these techniques with this premium ink, screen printers can produce stunning, durable prints that stand out in any application.

Red Puff Plastisol Ink
Red puff plastisol ink is a dynamic and innovative choice for screen printers looking to add a unique texture and visual interest to their designs. Unlike standard inks, puff plastisol ink creates a distinctive raised, puffy effect when cured, giving prints a three-dimensional quality that stands out. This added dimension can transform simple designs into eye-catching statements, making it an ideal option for custom apparel, branding, and promotional items.
The specialized formulation of red puff plastisol ink not only provides this engaging texture but also ensures durability. The ink adheres firmly to fabrics and retains its vibrant red color and raised effect even after repeated washing and wearing. This makes it suitable for a variety of applications, from casual wear and sportswear to children’s clothing and fashion-forward designs.
Additionally, red puff plastisol ink can be used creatively to enhance specific elements of a design, such as text, logos, or decorative patterns. By combining it with other inks or techniques, printers can achieve a layered and multidimensional look that sets their creations apart.
For optimal results, proper curing techniques are crucial. The ink needs to reach the correct temperature during the curing process to fully expand and achieve its signature puff effect. With the right tools, attention to detail, and high-quality ink, red puff plastisol ink offers endless possibilities for creating textured, durable, and visually striking prints.
Reducing White Plastisol Ink
When printing on darker fabrics, using a reduced white plastisol ink as an underbase is a highly effective technique to enhance the vibrancy of red plastisol ink. This underbase acts as a primer, creating a bright, neutral surface for the red ink to sit on, ensuring the final print appears vivid and true to its intended color. Without this step, darker fabric colors can dull the red ink, reducing its impact and clarity.
By applying a thin, even layer of reduced white plastisol ink, you can achieve better color consistency and improved opacity, particularly when working with intricate designs or logos that demand sharp, vibrant details. This technique is especially useful in screen printing applications where bold, eye-catching visuals are essential, such as branding, sportswear, or promotional merchandise.
Moreover, the underbase layer also contributes to the overall durability of the print, as it helps the red plastisol ink adhere more effectively to the fabric. The combination of a proper underbase and high-quality red plastisol ink ensures that your prints not only stand out visually but also withstand regular wear and washing, maintaining their brightness over time.
Conclusion
Red plastisol screen printing ink offers exceptional durability across various fabric types, provided the right ink formulation, fabric pre-treatment, printing technique, and post-processing steps are followed. Reviews of specific ink formulations, such as rapid cure plastisol ink, red 485 plastisol ink, red puff plastisol ink, and reducing white plastisol ink, provide valuable insights into their performance and suitability for different applications. By understanding these factors, printers can ensure that their red plastisol prints remain vibrant and durable, enhancing the overall quality of their printed products.