In the ever-evolving world of textile printing, innovation continues to push the boundaries of what’s possible. One such innovation is the advent of scented plastisol ink, which not only adds vibrant colors to fabrics but also introduces an olfactory dimension to the printed designs. The question on many minds, however, is whether scented plastisol ink can be effectively used on various fabrics and materials. This article delves into the intricacies of using scented plastisol ink, exploring its versatility, application techniques, and the nuances associated with different fabric types. By the end, you’ll have a comprehensive understanding of how to harness the power of scented plastisol ink for your screen printing needs.
Understanding Scented Plastisol Ink
Scented plastisol ink combines the durability and vibrancy of traditional plastisol ink with the added charm of aroma. Plastisol ink is a suspension of pigment in a plasticizer, which solidifies when heated. When infused with scent, it creates an engaging sensory experience that can significantly elevate the appeal of printed textiles. The key to successful application lies in understanding the ink’s composition and how it interacts with various fabric surfaces.
Compatibility with Different Fabrics
Scented plastisol ink’s versatility is one of its most appealing features. From cotton to polyester, from nylon to blends, this ink can be used on a wide range of fabrics. However, the success of the print heavily relies on proper preparation and technique.
1. Cotton Fabrics
Cotton is a popular choice for screen printing due to its absorbency and ability to hold ink well. When using scented plastisol ink on cotton, it’s crucial to ensure the fabric is pre-treated to enhance ink adherence. Proper drying and curing temperatures are also vital to prevent ink cracking or fading.
2. Synthetic Fabrics
Synthetic fabrics like polyester and nylon have a smoother surface, making ink adherence more challenging. However, advancements in ink formulations have made scented plastisol ink suitable for these materials. Special additives or primers may be required to ensure the ink bonds effectively. Once applied correctly, synthetic fabrics can showcase vibrant prints with long-lasting scent retention.
3. Blended Fabrics
Blends, especially cotton-polyester mixes, present a unique challenge. They combine the absorbency of cotton with the smoothness of polyester. When printing scented plastisol ink on blends, it’s essential to strike a balance between ink formulation and fabric preparation. Testing different ink-fabric combinations is recommended to achieve optimal results.
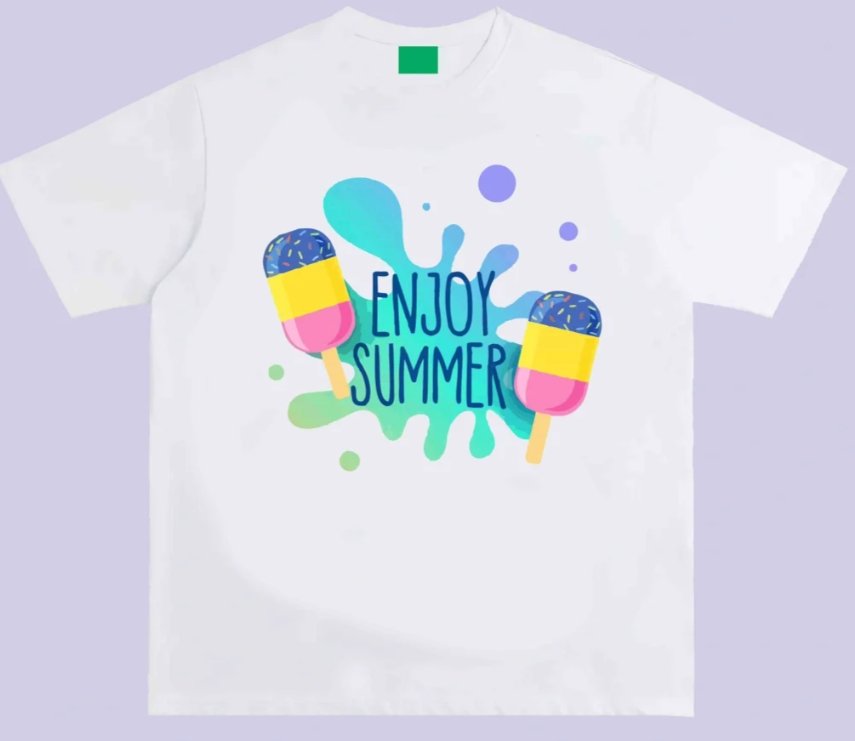
Screen Printing Techniques with Scented Plastisol Ink
Screen printing is a popular method for applying scented plastisol ink due to its precision and ability to handle large volumes efficiently. Here’s a closer look at the process:
1. Screen Print Plastisol Ink
Screen printing involves forcing ink through a stencil (or screen) onto the fabric. When using scented plastisol ink, the ink must be mixed thoroughly to ensure consistent scent distribution. Proper viscosity is crucial to prevent ink from clogging the screen or bleeding into the fabric.
2. Using Screen Print Tape for Plastisol Ink
Screen print tape plays a vital role in maintaining the integrity of the stencil during printing. It acts as a barrier, preventing ink from leaking under the screen. When working with scented plastisol ink, ensure the tape is compatible with the ink’s chemistry to avoid any adverse reactions that could compromise print quality.
3. Screen Printed Transfers with Plastisol Inks
Screen printed transfers offer a flexible way to apply complex designs onto garments. For scented plastisol ink transfers, the ink must be applied in precise layers to maintain scent intensity and ensure the transfer adheres smoothly to the fabric. Proper curing is also essential to lock in the scent and prevent fading.
Achieving Optimal Ink Thickness
The thickness of the plastisol ink layer directly impacts the print’s quality, durability, and scent retention. Here’s how to get it right:
Screen Printing: How Thick Should Plastisol Ink Be?
The ideal ink thickness for screen printing with scented plastisol ink varies depending on the fabric, design complexity, and desired effect. Generally, a thicker ink layer provides better opacity and scent retention but may require longer drying and curing times. On the other hand, thinner ink layers are ideal for intricate designs, as they allow for more detail and faster drying. Testing different ink thicknesses on scrap fabric is the best way to determine the optimal setting for your specific needs.
Maintaining Scent Intensity
Maintaining the scent intensity of printed fabrics is crucial for ensuring customer satisfaction. Here are some tips to help retain the scent:
- Quality Ink: Choose high-quality scented plastisol ink from reputable suppliers.
- Proper Storage: Store ink in a cool, dry place away from direct sunlight to prevent scent degradation.
- Curing Temperature: Ensure the curing temperature is within the manufacturer’s recommended range to lock in the scent effectively.
- Fabric Choice: Some fabrics retain scent better than others. Testing different fabrics can help identify the best options for your projects.
Case Studies and Real-World Applications
Examining real-world applications of scented plastisol ink provides insights into its effectiveness and versatility. From personalized apparel and promotional items to home textiles and beyond, scented plastisol ink has found its way into various industries. Here are a few notable examples:
- Apparel Industry: Custom T-shirts, athletic wear, and uniforms benefit from scented plastisol ink’s durability and appealing aroma.
- Promotional Items: Branded merchandise, such as tote bags and aprons, can be made more engaging with scented prints.
- Home Textiles: Bedding, towels, and curtains can be enhanced with calming or invigorating scents, creating a more immersive sensory experience.
Addressing Challenges and Troubleshooting
While scented plastisol ink offers numerous benefits, it can also present some challenges. Here’s how to troubleshoot common issues:
- Ink Cracking: Ensure the fabric is properly pre-treated and avoid over-stretching during printing.
- Scent Fade: Use high-quality ink, cure at the recommended temperature, and store printed items in a scent-preserving environment.
- Ink Bleeding: Adjust the ink’s viscosity and ensure the screen is clean and properly tensioned.
Conclusion
In conclusion, scented plastisol ink is a versatile and innovative printing medium that can be used on a wide range of fabrics and materials. By understanding its composition, selecting the right application techniques, and addressing potential challenges, you can create stunning, sensory-rich prints that captivate and engage your audience. Whether you’re a seasoned professional or a budding entrepreneur, scented plastisol ink offers a unique way to elevate your textile printing projects to new heights.
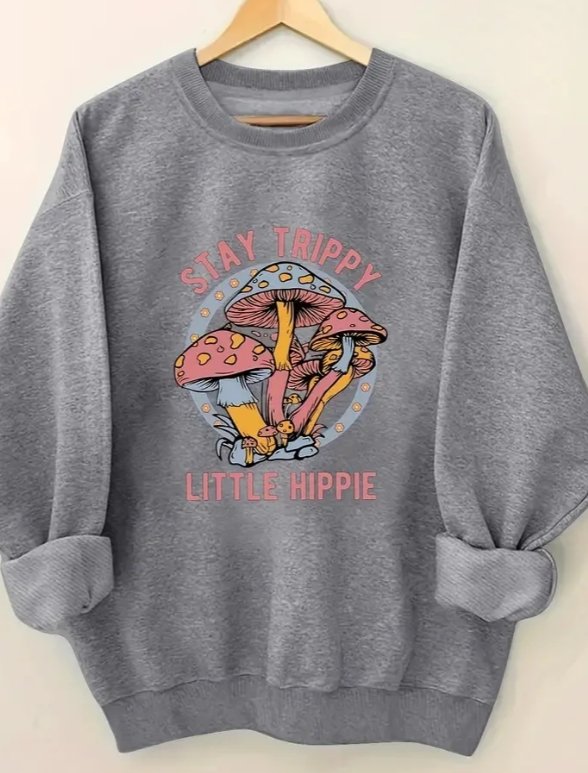