Innehållsförteckning
Screen Printing Guide: En steg-för-steg-utforskning av trycktekniker
Välkommen till vår Guide för screentryck. Denna guide är gjord Denna guide är till för att förbereda en skärm för screentryck. du som vill lära dig screentryck. I enkla ord visar vi hur du trycker på skjortor, papper och mer. Du kommer att lära dig vilka verktyg du behöver, hur du förbereder din skärm och hur du skriver ut som ett proffs. Vi använder enkla ord och tydliga listor. Låt oss börja!
Visste du att en bra skärmåtervinning kan hjälpa till vid screentryck? Screentryckmarknaden växer med 4.5% per år. Fler trycker nu hemma och i små butiker.
1. Introduktion
Screentryck låter dig skriva ut många färger på en skjorta eller papper. Du kan använda plastisol bläck, Vattenbaserat bläck föredras i många screentrycktekniker för dess miljöfördelar.eller till och med att använda UV-ljus för att härda emulsionen. utsläpp bläck. Denna guide är till för att förbereda en skärm för att sprida emulsionen jämnt på nätskärmen. DIYers, konstnärer, och småföretagare.
- Lära sig varje steg i att göra en skärm.
- Fixera fel som bläckblödning.
- Spara pengar med rätt verktyg och tekniker.
Vi delar tips, tricks och smarta sätt att få det bästa trycket.
2. Viktiga screentryckmaterial och verktyg
Först behöver du verktyg. Här är vår lista:
- Skärmar:
- Du behöver en skärm med rätt maskantal.
- Ett lägre maskantal är bra: En bra screenskrivare vet att vikten av registreringsmärken är avgörande i screentryckprocessen för att säkerställa korrekt justering av färger. för korrekta utskrifter. för flytande bläck och en högre räkning för detalj.
- Skrapar:
- Dessa är gummiverktyg som hjälper till att sprida bläck.
- Bläck:
- Plastisol bläck är tjock och ljus.
- Vattenbaserat bläck är miljövänligt, speciellt när man använder vattenbaserat bläck vid screentryck.
- Utsläpp bläck ändra färgen på tyget.
- Emulsion:
- Detta är en ljuskänslig vätska som hjälper till att göra din bild på skärmen.
- Filmpositiva och transparenta ark:
- Dessa hjälper dig att överföra din design.
- Valfria verktyg: En bra screentryckare kan använda ytterligare verktyg för att förbättra screentryckstekniken.
- Exponeringsenhet: Hjälper ljuset att fungera bra.
- Scoop Coater: används för att skapa en stencil för screentryck. Ger ett slätt emulsionsskikt.
- Registreringssystem: Hjälper till att anpassa dina färger.
Dricks: Det finns startpaket som kostar under $500. Många småföretag började hemma med dessa kit.
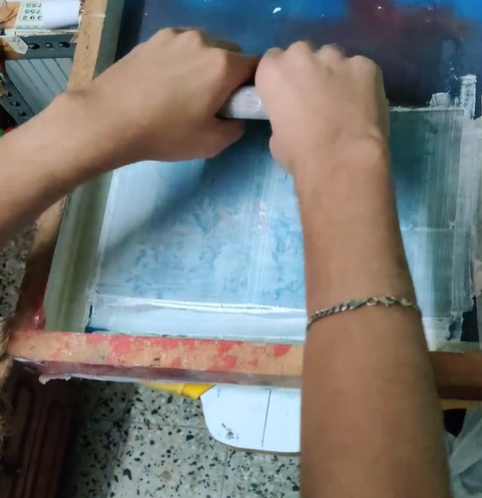
3. Förbereda ditt konstverk för screentryck
Din design måste vara rensa och upptagen. Följ dessa enkla steg:
- Välj din fil:
- Använd a vektor fil från Adobe Illustrator eller liknande verktyg.
- Hög upplösning:
- Se till att din design är åtminstone 300 DPI.
- Färgseparation:
- Varje färg behöver sin egen skärm.
- Registreringsmärken: väsentligt för att anpassa designen under screentryck.
- Hjälp dig att rada upp varje färg korrekt.
- Programvarutips:
- Använda Inkscape gratis eller Photoshop om du vill.
Genom att göra dessa kommer din konst att se ut bra på din skärm.
4. Steg-för-steg-skärmförberedelser
Följ dessa tydliga steg för att förbereda din skärm:
A. Beläggning av skärmen
- Applicera emulsion:
- Använd a scoop bestrykare för att fördela emulsionen jämnt.
- Torka emulsionen:
- Hitta en värma, mörkt område.
- Vänta tills det är torrt.
- Håll utkik efter bubblor:
- om du ser bubblor, låt skärmen torka igen.
B. Exponera skärmen
- Placera ditt konstverk:
- Lägg din film positivt på skärmen.
- Ljusexponering:
- Använd rätt ljus för din emulsion.
- Justera exponeringstiden. Ny teknik som CTS (dator-till-skärm) kan hjälpa till att påskynda detta.
- Tvätta ur:
- Använd vatten för att tvätta och ta bort emulsionen.
- Din design kommer att visas som tydliga områden.
Genom att följa dessa steg är din skärm redo för utskrift!
5. Utskriftsprocess: Tekniker för felfria resultat
Nu är det dags att skriva ut. Gör dessa steg:
A. Ställ in din skärm
- Placera skärmen:
- Se till att skärmen är på rätt plats.
- Rikta in skärmen:
- Kontrollera din registreringsmärken.
- Testutskrift:
- Gör ett provutskrift för att se om allt är i sin ordning, särskilt när du använder en UV-skrivare.
B. Bläckapplikation
- Översvämningsstroke:
- Täck skärmen med bläck före utskriften.
- Print Stroke: tekniken som används för att applicera bläck genom stencilen på underlaget.
- Använd ett fast, smidigt tryck.
- Håll i skrapa i en liten vinkel.
- Bläcklager:
- Om du skriver ut många färger, låt ett lager torka innan du lägger till ett annat.
- Använda underbastekniker om det behövs.
C. Härdning
- Välj en metod:
- Använd a värmepress eller a transportörstork.
- Tid och temperatur:
- Följ instruktionerna på din bläck.
- Plastisol bläck behöver mer värme än vattenbaserat bläck.
Påminnelse: Med UV-härdande bläck, får du snabb härdning och mindre spill.
6. Felsökning av vanliga screentrycksproblem
Ibland går saker inte som planerat. Här är korrigeringar för vanliga problem:
- Bläckblödning:
- Problem: Bläck går utanför designen.
- Fixera: Kontrollera ditt maskantal och avstånd från kontakten.
- Faktum: 45% av nybörjare ansikte bläck blödning.
- Spökbilder:
- Problem: Svaga dubbletter av bilder visas.
- Fixera: Rengör skärmen direkt efter utskrift.
- Ojämnt bläck: Detta kan inträffa under screentryckningsprocessen om schablonen inte är korrekt justerad.
- Problem: Bläck sprids inte jämnt.
- Fixera: Justera ditt sugskrapa tryck.
- Skärm igensättning:
- Problem: Bläck täpper till och slutar flöda.
- Fixera: Rengör skärmen och använd en bra avfettningsmedel.
Använd dessa tips för att göra din konst ren och snygg.
7. Avancerade tekniker för professionella resultat
För den som vill ha mer än bara enkla tryck, här är några Avancerade tekniker:
- Specialeffekter:
- Glitter eller metallbläck: Lägg till en glänsande look.
- Folieöverföringar: Ge ett unikt sken.
- Högdensitetsutskrifter: Skapa en 3D-effekt.
- Simulerad processutskrift:
- Blanda färger för att skapa realistiska bilder.
- Urladdningsutskrift:
- En metod som är bra för mjuka, vintagelooker.
- Även känd som miljövänligt screentryck.
- CTS-system:
- De minskar inställningstiden med 40% och hjälp med att snabbt skapa skärmar.
Dessa metoder gör att ditt arbete sticker ut och kan användas i en liten butik eller av proffs.
8. Underhåll & Hållbarhet
Att ta hand om dina verktyg är mycket viktigt. Att göra detta bra sparar pengar och planeten.
A. Skärmåtervinning
- Rengör din skärm:
- Ta bort all emulsion med en remover.
- Använd rengöringsmedel som Saati Emulsion Remover.
- Återanvänd din skärm:
- En väl rengjord skärm kan användas 15 gånger.
- Dricks: Regelbunden rengöring stoppar fel i utskrifter.
B. Miljövänliga val
- Vattenbaserade bläck:
- De är mjukare och säkra för jorden.
- Deras användning ökade med 35% sedan 2020.
- Metoder med lågt avfall:
- Använda UV-härdande bläck för snabb härdning och mindre avfall, överväg att använda ett tråg för ditt vattenbaserade bläck.
Att ta hand om din utrustning hjälper dig att skriva ut snabbare och gör jorden till en bättre plats.
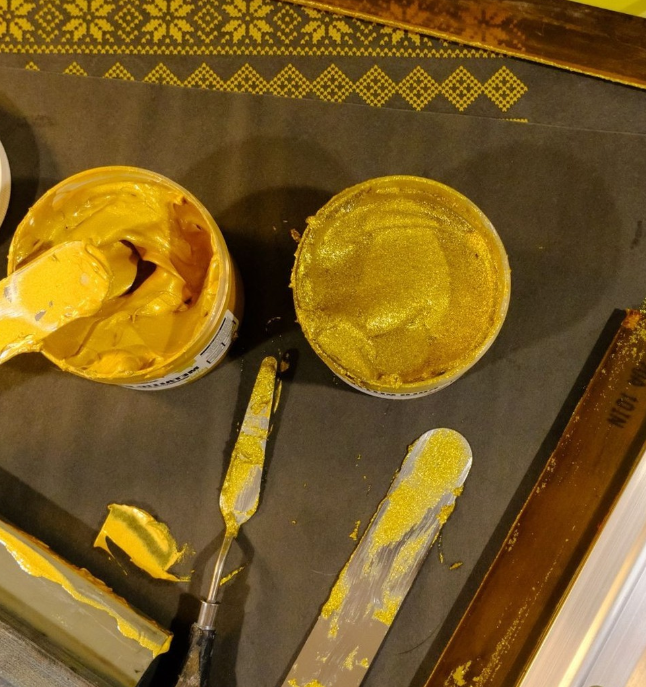
9. Vanliga frågor
Låt oss svara på några vanliga frågor:
Kan jag screentrycka hemma?
Ja! Många använder DIY screentryckssatser.
62% av småföretag startar hemma.
Vilket bläck är bäst för nybörjare?
Plastisol bläck är ljus och lätt att använda.
Vattenbaserat bläck är bra om du vill ha miljövänliga tryck.
Varför blöder mina utskrifter?
Bläckblödning kan bero på ett felaktigt maskantal.
Kontrollera dina kontaktlösa inställningar och använd våra felsökningstips.
Hur rengör jag min skärm?
Använd en remover som Saati Emulsion Remover.
Tvätta skärmen och låt den torka.
Vad är CTS?
CTS betyder Dator-till-skärm.
Det gör skärminställningar 40% snabbare.
Dessa vanliga frågor hjälper dig att lösa vanliga problem och lära dig snabbt.
10. Slutsats och nästa steg
Vi hoppas att den här guiden hjälper dig att lära dig screentryck. Du känner nu till stegen och ser hur många som älskar denna konst. Här är några nästa steg Den här guiden är till för dig: för att lära dig hur du förbereder en skärm för effektivt skärmtryck.
- Öva:
- Börja med enkla mönster.
- Prova olika bläck som plastisol, vattenbaserad, och ansvarsfrihet.
- Gå med i grupper:
- Det finns många onlinegrupper och forum.
- Läs mer:
- Leta efter verkstäder som kan minska ditt fel med 50%.
Lycka till med tryckningen!
Ytterligare resurser
- Besök våra länkar för Miljövänlig screentryck:
Med hjälp av dessa länkar kan du kolla in fler miljövänliga produkter.
Nyckeltermer och vad de betyder
Nedan följer en enkel lista med viktiga termer:
- Tillbehör för screentryck: Verktygen för screentryck.
- Gör-det-själv screentryckssats: Ett kit för hemmabruk.
- Skrapa: Ett verktyg för att sprida bläck.
- Plastisol bläck: Ett tjockt bläck som ger klara färger.
- Vattenbaserat bläck: Ett säkert bläck för jorden.
- Urladdningsutskrift: Ett sätt att skriva ut som tar bort färg.
- CTS (dator-till-skärm): Ett tekniskt verktyg för att påskynda skärmtillverkning.
- Adobe Illustrator: Ett designverktyg för konst.
- Speedball: Ett märke av tillbehör för screentryck.
- HERR: Ett varumärke känt för utskriftsutrustning.
Ha dessa villkor i åtanke när du arbetar med ditt projekt. De hjälper dig att följa stegen med lätthet.
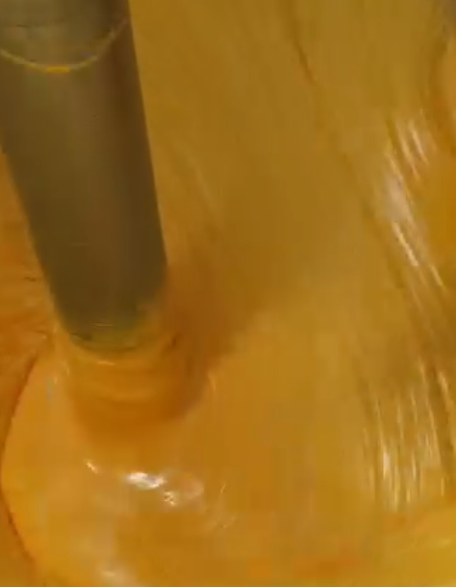
Steg-för-steg sammanfattning
Låt oss granska de viktigaste stegen en gång till:
- Samla in verktyg:
- Skaffa skärmar, bläck, skrapor, emulsions- och filmpositiv.
- Förbered din design:
- Använd en vektorfil, hög upplösning och skapa registreringsmärken.
- Förbered din skärm:
- Belägg, torka, exponera och tvätta ur skärmen.
- Skriv ut din design:
- Ställ in din utskriftsstation, använd flood- och tryckdragen och härda utskriften direkt på substratet.
- Felsökning:
- Lös problem som bläckblödning, spökbilder och ojämnt bläck.
- Avancerade alternativ:
- Prova specialeffekter, simulerad processutskrift eller urladdningsutskrift.
- Underhåll dina verktyg:
- Ta tillbaka dina skärmar och välj miljövänliga metoder.
- Läs mer:
- Gå med i workshops och gemenskaper för fler tips.
Slutliga tankar
I den här guiden visade vi dig hur du gör screentryck. Vi höll våra ord enkel. Vi använde listor för att visa dig stegen i screentryckningsprocessen. Vi använde till och med en tabell med fakta. Nu vet du grunderna från början till slut. Screentryck är roligt och en växande färdighet. Du kan göra konst, sälja skjortor eller starta ett litet företag!
Kom ihåg att övning är viktigt. Ju mer du skriver ut, desto bättre blir du. Använd våra tips för att åtgärda dina misstag. Lär dig av misstag och snart kommer du att skriva ut med lätthet. Och oroa dig inte om du stöter på problem. Det finns många onlinegemenskaper och resurser som kan hjälpa dig.
Lycka till med tryckningen och ha kul!