Key Takeaways: Plastisol & Screen Print Success
- Plastisol Ink offers unmatched durability, high opacity, and bold color on a wide range of garment fabrics.
- Proper cure temperature and dwell time are critical for lasting, wash-proof prints.
- Black plastisol ink delivers deep, vibrant, and bold results on both light and dark substrates.
- Meticulous screen prep (mesh, emulsion, ink deposit) ensures detail, coverage, and efficiency.
- Both manual and automatic presses benefit from plastisol’s forgiving nature and creamy consistency.
- Shop workflow—from ink mix to dryer—makes or breaks print production, so plan every step.
- International Coatings is a trusted brand for professional plastisol screen printing inks.
- Tackle common issues like bleed, opacity, and flashing with smart product selection and process contro.
- While water based ink has its niche, plastisol remains the best choice for vibrant, durable garment production.
- Stay current with trends and technology to keep your shop competitive and your prints looking world-class!
By mastering the art and science of plastisol ink, you unlock true potential for your screen print shop—one bold, beautiful print at a time
Mastering Plastisol Ink: The Ultimate Guide to Bold Screen Prints & Curing on Garments
Plastisol ink has revolutionized the world of display printing, handing over unequalled sturdiness, formidable and vibrant shades, and simplicity of use—making it the enterprise’s move-to alternative for garment printing. Whether you’re walking a bustling print shop, an bold startup, or tackling tasks right out of your garage, know-how plastisol, plastisol ink, and black plastisol ink will enhance your display print results and enterprise increase. This article dives deep into all things plastisol, demystifying curing temperatures, display prep, shop workflows, and more. If you want to raise your screen prints with creamy, opaque finishes and lengthy-lasting wash sturdiness, this is the guide for you.
Artikelöversikt
- What Is Plastisol? The Foundations of Screen Printing
- Plastisol Ink Explained: Why It’s the Industry Standard for Garment Printing
- How Does Black Plastisol Ink Boost Bold & Vibrant Prints?
- Cure Like a Pro: Achieving a Perfect Plastisol Ink Cure Every Time
- Screen Preparation: Mesh, Emulsion & Ink Deposits
- Tips for Screen Printers—Manual vs. Automatic Presses
- Inside the Shop: Optimizing Plastisol Ink Workflow and Production
- What Makes International Coatings a Leading Brand for Plastisol Screen Printing Inks?
- Troubleshooting: Bleed, Opacity, Flash, and Common Plastisol Ink Challenges
- Plastisol vs. Water Based Ink & Other Alternatives—Which is Best For Your Fabric?
1. What Is Plastisol? The Foundations of Screen Printing
Plastisol is a type of ink that’s primarily based on PVC particles suspended in a liquid plasticizer, growing a creamy, thick aggregate that doesn’t dry out at room temperature. This makes plastisol exceedingly smooth to print, even for novices, as it handiest sets when it reaches the proper cure temperature through publicity to heat.
Because plastisol ink doesn’t air-dry, you get unlimited open time for your displays. This is critical for guide shops or absolutely everyone mastering the ropes, as errors may be constant with out fear of the ink placing mid-production. Whether you’re printing t-shirts, hoodies, or athletic gear, plastisol’s versatility ensures it performs nicely across cotton and polyester blends, adhering to material fibers for an instantaneous, ambitious end.
The end result? Prints with a smooth hand feel, high opacity, and longer-lasting sturdiness—even after countless washes. With its resistance to ink degradent and its potential to preserve vibrancy, plastisol is the heartbeat of professional display print stores anywhere.
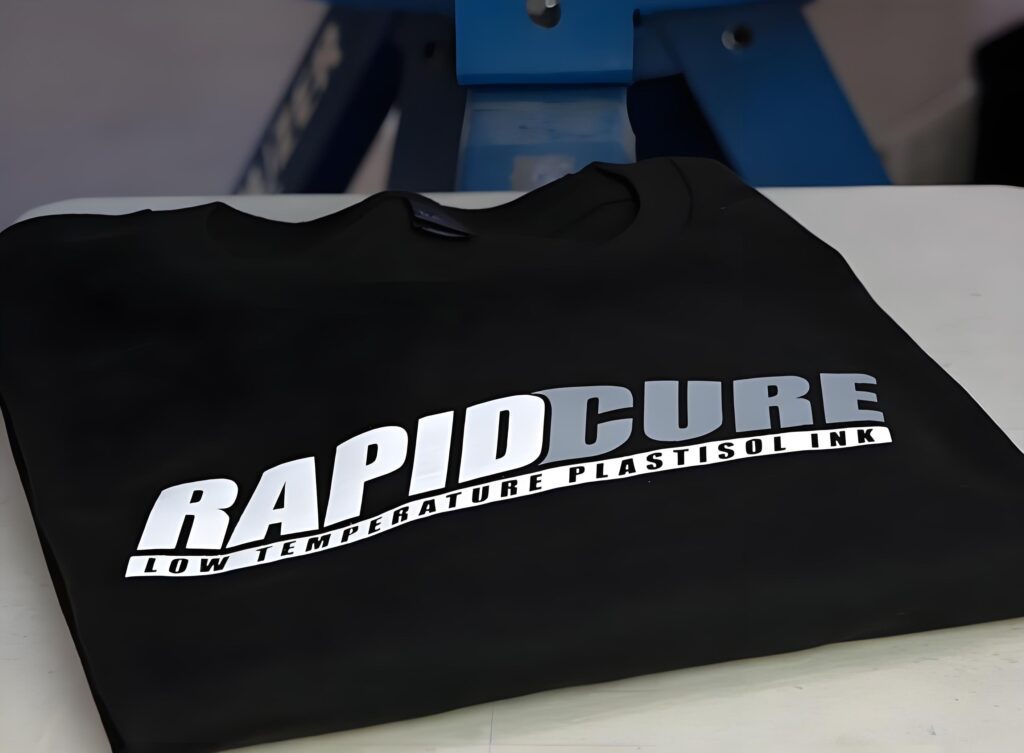
2.Plastisol Ink Explained: Why It’s the Industry Standard for Garment Printing
Plastisol ink stands other than other screen printing inks for a bunch of motives. Its thick, creamy consistency allows for an easy to print technique, whether you’re the usage of manual or computerized presses23. “Easy to print” isn’t simply enterprise jargon—it manner fewer misprints, smoother runs, and much less strain approximately your ink drying inside the middle of a complicated activity.
What truly sets plastisol ink aside is its high opacity and potential to supply formidable and colourful shades, regardless of the substrate or garment shade beneath. Whether you’re doing direct printing on darkish shirts or mild fabric, plastisol guarantees the shade pops. For custom garments and branded apparel, this makes an substantial distinction in quality perception.
Another massive gain? Unlike water primarily based ink, plastisol does no longer require unique coping with or quick screen clearing. That method more time printing, less time disturbing about mesh clogs or degraded emulsion.
3. How Does Svart Plastisol bläck Boost Bold
For deep, lasting impressions, black plastisol ink is the staple of display screen print stores focused on formidable, brilliant designs. The reason: black plastisol ink gives wonderful insurance over numerous cloth types—specially while high opacity formulations are used. On dark or colored clothes, it acts as both an artwork enhancer and a background-pulling down agent, ensuring that designs appear crisp, sharp, and professional.
When operating with polyester or blends, specialized low bleed black plastisol ink formulations reduce dye migration, retaining the integrity of your design intact even after more than one washes. If you want durable, putting insurance that doesn’t fade, black plastisol ink is your go-to. For athletic clothing or designs in which a formidable declaration topics, not anything opponents the impactfulness of a robust black plastisol screen print.
4. Cure Like a Pro: Achieving a Perfect Plastisol Ink Cure Every Time
The right treatment temperature is everything in plastisol display screen printing. For any print to closing, the ink should be nicely heated—normally in a conveyor dryer or flash unit—to obtain fusion with the fabric’s fibers. Under-curing results in ink that cracks or washes away, while over-curing can scorch the substrate or make the print too stiff.
Industry high-quality practices name for a consistent temp (generally around 320°F) and enough stay time to ensure that the entire ink deposit—no longer just the surface—reaches the precise cure temperature. Lower treatment and low bleed formulations are particularly valuable for problematic polyester fabric or shirt blends that “bleed” dye at decrease temps.
Flash gadgets will let you “gel” your plastisol ink among layers, making multilayer jobs or wet-on-wet strategies viable. Remember: constantly measure your real print temp, not simply the dryer setting—fabric and prints can soak up and distribute warmness unpredictably, affecting cure time and fine
5. Screen preparation: mesh count, emulsion and ink deposition
Behind every great screen print is a perfect screen preparation. Mesh count, proper emulsion exposure and ideal ink deposition are critical to maximizing the potential of plastisol inks. For bold designs or opaque substrates, especially when using black plastisol inks, a lower mesh allows for thicker ink deposition, allowing the opalescent ink to penetrate deep into the fibers for long-lasting, vibrant results.
Emulsion exposure is another critical factor. An underexposed screen can cause premature damage to the screen during production, while an overexposed screen loses detail. The right screen and emulsion combination not only maintains the detail of the design, but also maintains the proper ink flow for continuous operation in the shop2.
Whether you’re using a quart-sized can or working with a 5-gallon bucket, efficient direct-print pretreatment of screens saves time and materials, resulting in cleaner prints and lower cost per shirt.
6. Screen Printers Tips – Manual vs. Automatic Printers
Are you using a manual printer or an automatic printer? Each method has its own unique advantages when working with plastisol inks. Manual presses are favored for their tactile control and flexibility – perfect for short runs, prototyping or fine work. They allow screen printers to “feel” squeegee pressure and adjust deposits as needed for a rough or soft feel effect.
On the other hand, automatic presses offer higher throughput and more consistent results, making them ideal for larger garment orders where speed and uniformity are important. Both setups benefit from the generous open time and delicate consistency of plastisol inks, which ensures that even complex productions won’t be stalled by drying problems.
Whether you’re a small press conducting a test run or a high-volume printer, choosing the right equipment and workflow can enhance the quality of your prints. And don’t forget: you get the best results when you choose the right tools for the production needs of your shop and the finished product you want!
7.Inside the Shop: Optimizing Plastisol Ink Workflow and Production
Efficient shop workflow is key to thriving in the screen printing industry. Start-to-finish, your workflow should account for ink mixing, screen prep, drying, and press setup—especially when working with creamy plastisol screen printing inks in high-volume scenarios.
Using a production belt and organized press stations, your shop can move garments from screen print to flash unit to conveyor dryer seamlessly. This minimizes downtime and ink waste—ensuring that each print meets your client’s standards for color, opacity, and durability. Smart practices like press wash, squeegee cleaning, and maintaining mesh integrity ensure that your plastisol screen printing operation runs smoothly day after day.
For those printing on multiple substrates—such as cotton and polyester blends—it’s important to rotate inks and flash units to reduce cross-contamination and prevent dye or bleed issues, especially with low bleed formulations.
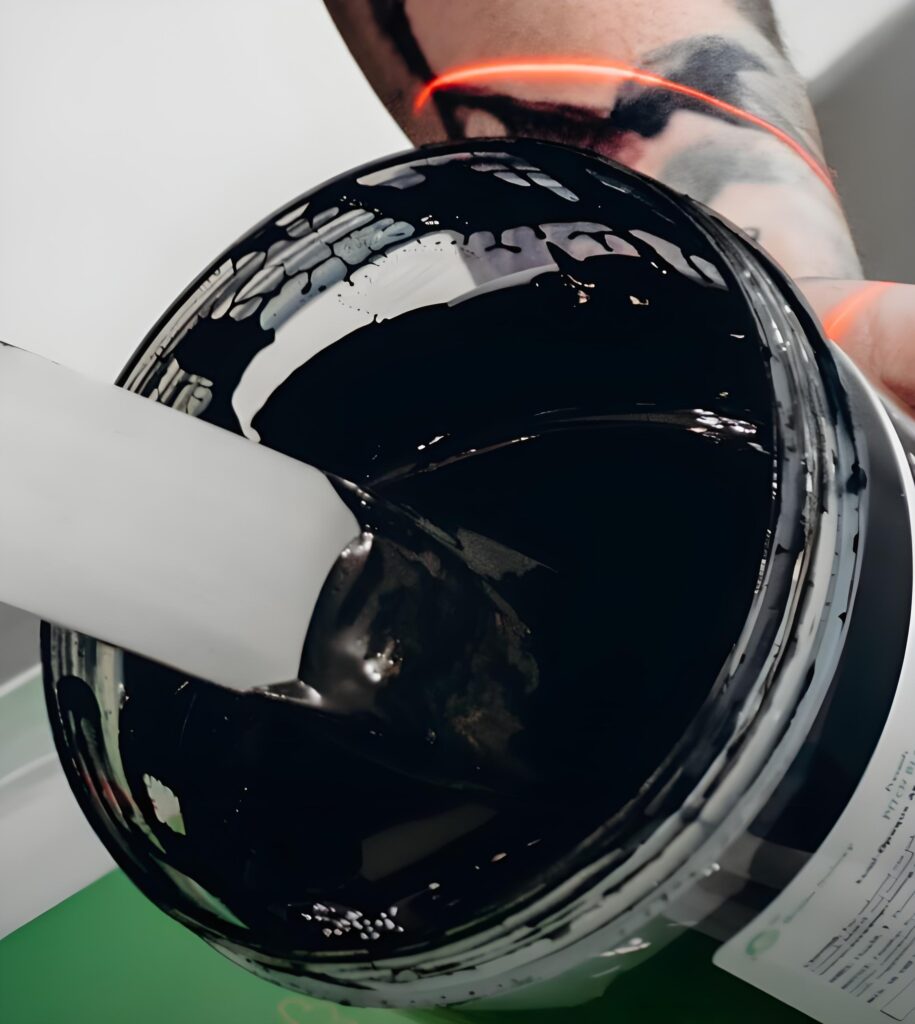
8.What Makes International Coatings a Leading Brand for Plastisol Screen Printing Inks?
When it comes to reliable results, International Coatings stands out as a brand synonymous with excellence in plastisol ink manufacturing. Their Series plastisol inks and specialty colors offer unmatched vibrancy, high opacity, and easy to print formulations tailored for both manual and automatic shops.
International Coatings’ non-phthalate lines, low cure offerings, and wide range of Pantone-matched colors make them a go-to for professional screen printers aiming to produce bold, consistent prints on a variety of garments and athletic wear. Whether you need small quarts for sampling or 5 gallon buckets for major orders, this brand covers all the workflow bases.
Ruggedness, adaptability, and reliable curing—we can see why International Coatings is an industry favorite. Their dedication to formulation quality and innovation sets the bar for what top-tier screen printing plastisol ink should deliver
9.Troubleshooting: Bleed, Opacity, Flash, and Common Plastisol Ink Challenges
Even with the best plastisol ink and workflow, challenges arise. Dye migration, or “bleed,” often occurs on polyester and blends—turning bright whites pink or grays muddy. That’s why low bleed and high opacity formulas are essential for certain fabrics.
Opacity issues often stem from using mesh that’s too fine, too little ink deposit, or improper flash timing. A print-flash-print approach boosts coverage, especially on dark colors or when layered with black plastisol ink12. Watch out for under-cured prints—they might appear set on the surface but fail durability tests after washing.
For every problem, there’s a solution. Keep emulsion exposure, ink deposit, and dryer temp dialed in. Monitor exposure and washout times to keep mesh clear and detail sharp. Use ink degradent and press wash routines to avoid buildup from run to run.
10.Plastisol vs. Water Based Ink & Other Alternatives—Which is Best For Your Fabric?
While plastisol ink is the undisputed king of screen print production for bold, vibrant results, alternatives like water based ink and hybrid inks have their place. Water based ink offers a softer hand and eco-conscious appeal but comes with shorter open time, quicker drying on screens, and typically less opacity on dark garments or polyester substrates.
Plastisol shines when you need versatility across cotton, polyester, and blends, reliable low bleed performance, and maximum color vibrancy. For direct printing on t-shirts and sweatshirts destined for heavy washing, stick with plastisol for longevity and performance.
Hybrid solutions and specialty inks continue to grow, but for most print shops—especially those with high runs or detailed bold colors—plastisol screen printing inks remain the gold standard the world over