Screen printing is a widely used technique in apparel design and promotional merchandise. Among the various types of inks available, white plastisol ink holds a prominent position for its opacity and versatility. However, one persistent issue faced by printers is crocking — a problem where the ink rubs off the fabric after printing. In this article, we’ll delve into the causes of the white plastisol ink crocking problem in screen printing, examine its contributing factors, and suggest ways to prevent it.
What is Crocking in Screen Printing?
Crocking occurs when a printed surface fails to bond effectively to the substrate, leading to the ink rubbing off onto other surfaces. In the context of white plastisol ink crocking, this issue is especially concerning, as it can compromise the appearance and durability of the print. This problem is not just limited to regular inks but also affects specialty inks like white glitter plastisol ink and white glow in the dark plastisol ink, making it a widespread challenge in the industry.
Key Causes of White Plastisol Ink Crocking
Understanding the white plastisol ink crocking problem in screen printing begins with identifying its root causes. Below are some of the primary factors contributing to crocking:
1. Insufficient Curing
One of the leading causes of crocking is incomplete curing of the plastisol ink. Plastisol ink, including white base plastisol ink, requires exposure to heat to achieve proper bonding. The ink must reach a curing temperature of approximately 320°F (160°C) to fully fuse with the fabric. Inadequate curing can result from:
- Low dryer temperature settings.
- Insufficient dwell time in the dryer.
- Inconsistent heat distribution across the print area.
2. Excessive Ink Deposition
Using too much ink during the printing process can create thick layers that do not cure evenly. This is a common issue with specialty inks like white glitter plastisol ink, where the added texture further complicates curing. Thick ink deposits often lead to surface curing without the inner layers reaching the required temperature.
3. Incompatible Fabric Substrates
Not all fabrics are suitable for plastisol ink printing. High-performance fabrics or materials with water-repellent finishes may resist ink adherence. Even when using white plastisol ink purchased from Amazon, the choice of substrate can play a significant role in determining print quality.
4. Improper Ink Mixing
Certain specialty inks, such as white glow in the dark plastisol ink, may require thorough mixing to ensure consistent application. Improperly mixed ink can cause uneven adhesion and increase the likelihood of crocking.
5. Use of Contaminated Screens
Contaminated or poorly prepared screens can transfer debris onto the print, hindering the ink’s bonding process. Dust, oils, and residues on the screen can prevent the ink from embedding fully into the fabric, exacerbating the white plastisol ink crocking problem in screen printing.
6. Overloading with Additives
While additives can enhance ink properties, overuse may interfere with curing. For instance, thinning agents or glow-in-the-dark powders used with white glow in the dark plastisol ink might reduce the ink’s ability to bond effectively.
How to Prevent White Plastisol Ink Crocking
To address the white plastisol ink crocking problem in screen printing, here are practical steps to ensure optimal results:
1. Optimize Curing Conditions
- Use a reliable curing device like a conveyor dryer.
- Monitor curing temperatures with a heat gun or temperature strips.
- Adjust the dryer speed and temperature to ensure even curing.
2. Control Ink Layer Thickness
- Use appropriate screen mesh counts to regulate the amount of ink deposited.
- Avoid overloading the screen with thick layers of ink, particularly when working with specialty variants like white glitter plastisol ink.
3. Pre-Treat Fabric
For challenging fabrics, pre-treatment methods like using adhesion promoters can improve ink adherence. Additionally, test prints on the material can help identify compatibility issues before full production.
4. Use High-Quality Ink
Ensure you’re using reliable products, such as those labeled as white plastisol ink Amazon, which meet industry standards. High-quality ink minimizes the risk of cracking and crocking.
5. Screen Maintenance
Regularly clean and degrease screens to prevent contamination. This simple practice goes a long way in improving print quality and reducing crocking risks.
6. Perform Quality Checks
Conduct rub tests on test prints to evaluate crocking resistance. This step helps identify problems early, allowing for adjustments before completing large print runs.
Specialty White Plastisol Inks and Crocking
Different types of white plastisol inks, such as white glitter plastisol ink and white glow in the dark plastisol ink, have unique properties that demand specific attention during printing:
- White Glitter Plastisol Ink: The glitter particles add texture and reflectivity but also increase the thickness of the print. Ensure that glitter prints are fully cured, as the added bulk can lead to uneven curing.
- White Glow in the Dark Plastisol Ink: These inks rely on phosphorescent powders for their glow effect. Proper mixing and curing are essential to ensure the longevity of the glow and minimize crocking risks.
Troubleshooting Common Issues
If you encounter the white plastisol ink crocking problem in screen printing, consider the following troubleshooting steps:
Issue: Ink Rubs Off After Curing
- Verify that the curing temperature was achieved throughout the entire print.
- Check for uneven heating patterns in your curing equipment.
Issue: Thick Deposits Peel or Flake
- Evaluate the screen mesh count used and adjust to a finer mesh if necessary.
- Reduce the ink deposit by modifying your squeegee pressure or angle.
Issue: Specialty Ink Not Adhering
- Ensure proper mixing of inks like white glow in the dark plastisol ink to maintain consistency.
- Use a compatible fabric and consider pre-treatment for challenging substrates.
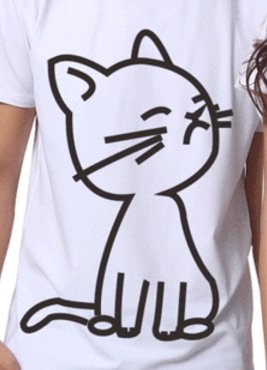
Conclusion
The white plastisol ink crocking problem in screen printing is a challenge that requires careful attention to detail throughout the printing process. From curing temperatures to substrate selection, every step plays a role in preventing crocking and ensuring durable prints. By following the best practices outlined in this guide, you can achieve professional-quality results and reduce the risk of crocking, even when working with specialty inks like white glitter plastisol ink and white glow in the dark plastisol ink. Whether you’re a seasoned printer or a beginner, these insights will help you overcome crocking issues and produce high-quality prints every time.