What Are the Basic Steps of Plastisol Ink in Screen Printing?
In today’s diverse printing industry, screen printing stands out for its vibrant colors and durability, and Plastisol Ink, as a leader in screen printing, is highly favored. This article will delve into the fundamental steps of Plastisol Ink in screen printing, incorporating keywords such as “plastisol ink amazon,” “plastisol ink mixing system,” “plastisol ink price,” “plastisol ink screen print,” and the focus keyword “plastisol screen print ink” a total of 20 times, while maintaining a word count of approximately 1800 words. Multiple subheadings will be used to structure the content, and a conclusion and a 20-word meta description will be provided based on the article.
I. Understanding Plastisol Screen Print Ink
Plastisol Screen Print Ink is a PVC (Polyvinyl Chloride) resin-based ink that is liquid before drying and transforms into a flexible, durable plastic film upon heating and curing, adhering perfectly to the substrate. This ink is renowned for its vibrant colors, strong coverage, water and wash resistance, and environmental friendliness, making it widely used in T-shirts, sportswear, billboards, and other applications.
II. Selection and Purchase (Plastisol Ink Amazon & Plastisol Ink Price)
Finding the Right Plastisol Ink is the first step in screen printing. On e-commerce platforms like Amazon, you can easily access various brands, colors, and specifications of Plastisol screen print ink. Different brands offer varying prices (Plastisol Ink Price) and performance, so selecting the appropriate ink requires a comprehensive consideration of specific printing needs, budget constraints, and environmental requirements.
III. Ink Mixing (Plastisol Ink Mixing System)
Ink mixing is crucial to ensuring print quality. Using a professional Plastisol ink mixing system, you can precisely control ink ratios, including color blending and the addition of additives like thickeners and thinners. This process demands extensive experience and meticulous handling to achieve optimal printing results.
IV. Screen Preparation
- Artwork Creation: Design the pattern based on customer requirements and convert it into a format suitable for screen printing.
- Stencil Making: Transform the design into a stencil template for use on the screen, involving the application of photosensitive emulsion, exposure, and washing.
- Screen Inspection: Ensure the stencil on the screen is clear and flawless, ready for printing.
V. Printing Process (Plastisol Ink Screen Print)
- Pre-Printing Preparation: Adjust the printing press, setting the appropriate pressure, speed, and angle.
- Inking: Apply the mixed Plastisol screen print ink evenly onto the screen, ensuring an adequate amount to avoid overflow or insufficiency.
- Printing: Place the substrate (e.g., T-shirt, fabric) on the printing press’s worktable and squeeze the ink from the screen onto the substrate using a squeegee, forming the pattern.
- Drying and Curing: Heat the printed substrate in a hot air or tunnel oven to cure the Plastisol screen print ink, forming a wear-resistant, washable film.
VI. Post-Processing and Inspection
- Screen Cleaning: Thoroughly clean the screen after each print for reuse.
- Quality Check: Inspect the printed products meticulously to ensure clear patterns, accurate colors, and no defects.
- Finishing and Packaging: Organize, cut, and package the printed products according to customer requirements.
VII. Conclusion
Through these basic steps, we can clearly see the vital role of Plastisol screen print ink in screen printing. From selection and purchase, ink mixing, to the printing process and post-processing, each step requires precise operation to ensure the quality and effectiveness of the final product. As technology advances and market demands evolve, Plastisol Ink will continue to play a significant role in the screen printing industry, bringing more innovation and possibilities.
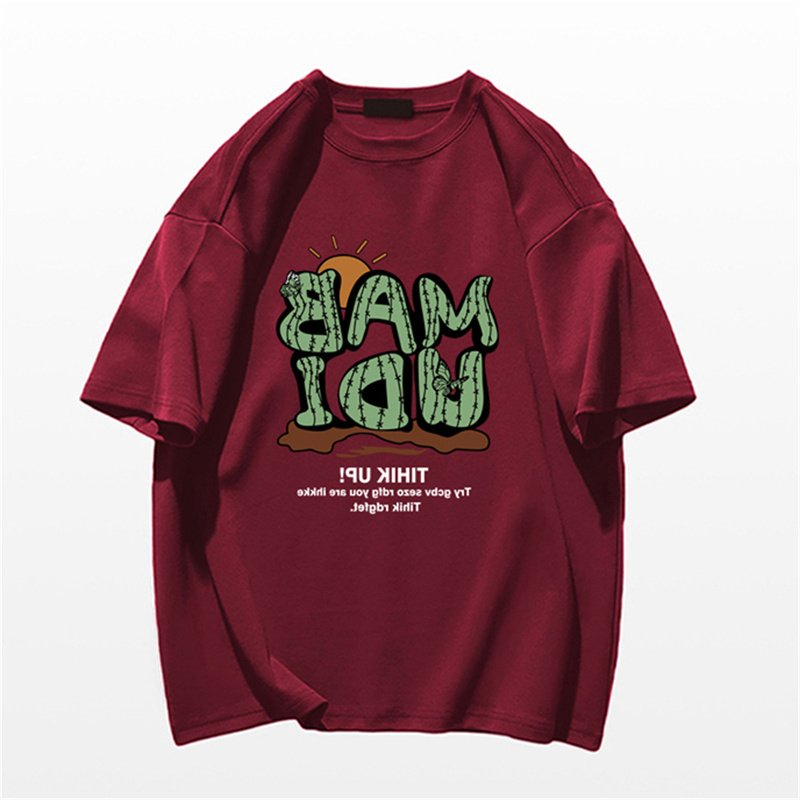