Discover the functions, applications, and key differences of puff additive in printing. Master essential techniques and tips for optimal print quality.
Table of Contents
The Distinction Between Puff Base and Puff Additive
In the realm of printing, puff additive and puff base may sound similar, but they serve distinct roles.
Puff base is a pre-mixed foaming ink that comes ready-to-use straight out of the container. It contains the necessary foaming agents, making it ideal for beginners or those seeking a hassle-free printing experience.
In contrast, puff additive is a concentrated agent designed to be mixed with other base inks (such as water-based or solvent-based inks) to create a foaming effect. This flexibility allows users to adjust the foaming ratio, achieving varying levels of three-dimensional texture and softness while preserving the original ink color.
In summary, puff base is perfect for standardized production, while puff additive offers greater creative freedom. This is the fundamental difference between the two in printing applications.
How to Clean Puff Ink Prints
Clothing with puff prints requires special care during washing to maintain the quality of the print. Here are the recommended steps:
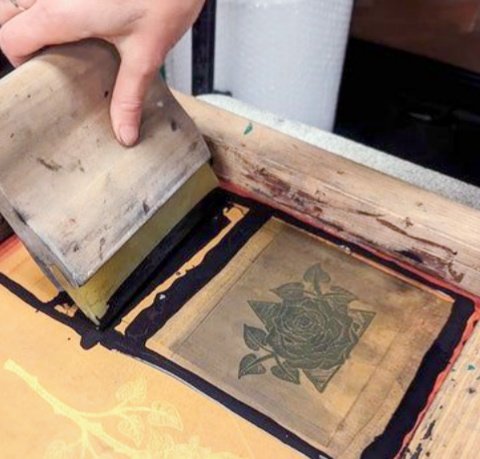
- Wash Inside Out: Turn the garment inside out to minimize friction on the print.
- Cold Water Wash: High temperatures can damage the puff structure, so cold water is recommended.
- Mild Detergents: Avoid bleach or harsh chemical cleaners.
- Low-Speed Spin or Air Dry: Strong centrifugal forces or high-temperature drying can cause the puff print to peel or crack.
Proper washing techniques can extend the life of puff ink, keeping the print plump and textured.
What is Rapid Cure Puff Additive? Will Puff Prints Crack?
Rapid cure puff additive is a quick-drying variant designed for high-volume printing operations. It offers faster curing times without compromising the foaming effect, significantly boosting productivity.
A common question is: “Will puff prints crack?”
The answer is: They might, but it can be controlled.
Overusing puff additive, improper mixing of ink, or insufficient curing can lead to cracking during washing or stretching. Additionally, the elasticity of the fabric itself can affect the durability of the puff print.
To avoid this, carefully control the amount of puff additive added and follow the recommended drying temperatures and times (typically around 160°C). This will help minimize cracking issues.
The Difference Between Puff and High-Density Inks
Both puff and high-density prints create a three-dimensional effect, but they achieve it through different mechanisms and result in distinct textures.
- Puff Prints: Puff additive creates a soft, sponge-like texture with a matte finish when heated. The surface is typically rounded and has a gentle, tactile feel.
- High-Density Prints: These are created by layering thick ink to form hard, sharply defined raised lines. The texture is more rigid and sometimes slightly glossy.
In essence, puff prints focus on a “soft and elastic” visual and tactile experience, while high-density prints emphasize “sharp contours” and “precise structure.” In practice, combining both can create unique visual layers.
How to Use Puff Binder
Puff binder is commonly used in water-based printing systems as the base medium for foaming prints. Here’s how to use it correctly:
- Add Pigment Paste: First, mix the desired pigment paste with the puff binder.
- Introduce Puff Additive: Add puff additive to the mixture, typically in a ratio of 5%-15% of the total volume.
- Mix Thoroughly: Ensure the mixture is free of bubbles and particles, achieving a uniform ink consistency.
- Screen Printing: Use a low-mesh screen suitable for puff printing.
- Heat Cure: Water-based puff formulations usually require baking at 150°C-180°C for 1-2 minutes to activate the foaming reaction.
The key to using puff binder lies in precise ratios and temperature control. It’s advisable to conduct small-scale tests before full production to ensure the desired color and foaming effect.
The Ideal Amount of Puff Additive
Controlling the amount of puff additive is crucial for achieving the desired print effect. Here are general recommendations:
- 5%-10%: Suitable for detailed designs with a subtle foaming effect.
- 10%-15%: Ideal for larger areas with a pronounced three-dimensional feel.
- 15%-20%: For special effects requiring a strong expansion, but be cautious of excessive thickness that can lead to peeling.
Using more than 20% can reduce viscosity, destabilize the ink layer, and affect durability. Therefore, adjusting the puff additive ratio is key to successful printing.
Conclusion
This article has provided a comprehensive overview of puff additive in printing applications. From understanding the differences between puff base and puff additive, to washing techniques, potential cracking issues, distinctions from high-density prints, proper use of puff binder, and controlling the additive ratio, each aspect is vital.
Mastering these insights can significantly enhance the quality of your prints and boost customer satisfaction. In future projects, experiment with different puff additive combinations to create prints with enhanced texture and visual appeal.
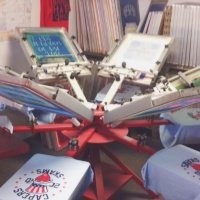