Siebdruck ist ein weit verbreitetes Verfahren im Bekleidungsdesign und bei Werbeartikeln. Unter den verschiedenen verfügbaren Tintentypen ist weiße Plastisoltinte aufgrund ihrer Opazität und Vielseitigkeit besonders beliebt. Ein hartnäckiges Problem für Drucker ist jedoch das Abfärben der Tinte vom Stoff nach dem Drucken. In diesem Artikel untersuchen wir die Ursachen für das Abfärben weißer Plastisoltinte im Siebdruck, untersuchen die Faktoren, die dazu beitragen, und schlagen Möglichkeiten zur Vermeidung vor.
Was ist Crocking beim Siebdruck?
Abfärben tritt auf, wenn eine bedruckte Oberfläche nicht richtig mit dem Substrat verbunden ist, wodurch die Tinte auf andere Oberflächen abfärbt. Im Zusammenhang mit dem Abfärben von weißer Plastisoltinte ist dieses Problem besonders besorgniserregend, da es das Aussehen und die Haltbarkeit des Drucks beeinträchtigen kann. Dieses Problem betrifft nicht nur herkömmliche Tinten, sondern auch Spezialtinten wie weiße Glitzer-Plastisoltinte und weiße, im Dunkeln leuchtende Plastisoltinte und ist daher ein weit verbreitetes Problem in der Branche.
Hauptursachen für das Verfärben weißer Plastisol-Tinte
Um das Problem des Abfärbens von weißer Plastisoltinte im Siebdruck zu verstehen, müssen zunächst die Ursachen ermittelt werden. Im Folgenden sind einige der Hauptfaktoren aufgeführt, die zum Abfärben beitragen:
1. Unzureichende Aushärtung
Eine der Hauptursachen für das Verfärben ist die unvollständige Aushärtung des Plastisol-TintePlastisoltinte, auch weiße Plastisoltinte, muss erhitzt werden, um eine gute Haftung zu erzielen. Die Tinte muss eine Aushärtungstemperatur von ca. 160 °C erreichen, um vollständig mit dem Stoff zu verschmelzen. Unzureichende Aushärtung kann folgende Ursachen haben:
- Niedrige Trocknertemperatureinstellungen.
- Unzureichende Verweilzeit im Trockner.
- Inkonsistente Wärmeverteilung über den Druckbereich.
2. Übermäßiger Tintenauftrag
Die Verwendung von zu viel Tinte während des Druckvorgangs kann zu dicken Schichten führen, die nicht gleichmäßig aushärten. Dies ist ein häufiges Problem bei Spezialtinten wie weißer Glitzer-Plastisoltinte, bei der die zusätzliche Textur die Aushärtung zusätzlich erschwert. Dicke Tintenablagerungen führen oft dazu, dass die Oberfläche aushärtet, ohne dass die inneren Schichten die erforderliche Temperatur erreichen.
3. Inkompatible Stoffsubstrate
Nicht alle Stoffe sind für den Plastisol-Tintendruck geeignet. Hochleistungsgewebe oder Materialien mit wasserabweisender Ausrüstung können die Tintenhaftung beeinträchtigen. Selbst bei Verwendung weiße Plastisol-Tinte Bei Kauf über Amazon kann die Wahl des Substrats eine bedeutende Rolle bei der Bestimmung der Druckqualität spielen.
4. Unsachgemäßes Mischen der Tinte
Bestimmte Spezialtinten, wie z. B. weiße, im Dunkeln leuchtende Plastisoltinte, erfordern möglicherweise ein gründliches Mischen, um eine gleichmäßige Anwendung zu gewährleisten. Falsch gemischte Tinte kann zu ungleichmäßiger Haftung führen und die Gefahr von Abnutzung erhöhen.
5. Verwendung kontaminierter Bildschirme
Verunreinigte oder schlecht vorbereitete Siebe können Schmutz auf den Druck übertragen und so die Farbhaftung beeinträchtigen. Staub, Öle und Rückstände auf dem Sieb können die vollständige Einbettung der Farbe in den Stoff verhindern und so das Problem der Abnutzung weißer Plastisolfarbe beim Siebdruck verschlimmern.
6. Überladung mit Zusatzstoffen
Additive können zwar die Tinteneigenschaften verbessern, übermäßiger Einsatz kann jedoch die Aushärtung beeinträchtigen. Beispielsweise können Verdünnungsmittel oder im Dunkeln leuchtende Pulver in Kombination mit weißer, im Dunkeln leuchtender Plastisoltinte die Haftung der Tinte beeinträchtigen.
So verhindern Sie das Abfärben weißer Plastisoltinte
Um das Problem des Abfärbens weißer Plastisoltinte beim Siebdruck zu lösen, sind hier die praktischen Schritte, die optimale Ergebnisse gewährleisten:
1. Optimieren Sie die Aushärtungsbedingungen
- Verwenden Sie ein zuverlässiges Aushärtungsgerät wie einen Durchlauftrockner.
- Überwachen Sie die Aushärtungstemperaturen mit einer Heißluftpistole oder Temperaturstreifen.
- Passen Sie die Trocknergeschwindigkeit und -temperatur an, um eine gleichmäßige Aushärtung zu gewährleisten.
2. Kontrollieren Sie die Dicke der Tintenschicht
- Verwenden Sie geeignete Siebmaschenzahlen, um die aufgetragene Tintenmenge zu regulieren.
- Vermeiden Sie es, den Bildschirm mit dicken Tintenschichten zu überladen, insbesondere wenn Sie mit Spezialvarianten wie weißer Glitzer-Plastisol-Tinte arbeiten.
3. Stoff vorbehandeln
Bei anspruchsvollen Stoffen können Vorbehandlungsmethoden wie Haftvermittler die Tintenhaftung verbessern. Zusätzlich können Testdrucke auf dem Material helfen, Kompatibilitätsprobleme vor der Produktion zu erkennen.
4. Hochwertige Tinte verwenden
Stellen Sie sicher, dass Sie zuverlässige Produkte verwenden, z. B. solche mit der Bezeichnung „weiße Plastisoltinte“ von Amazon, die den Industriestandards entsprechen. Hochwertige Tinte minimiert das Risiko von Rissen und Abnutzung.
5. Bildschirmwartung
Reinigen und entfetten Siebe regelmäßig, um Verunreinigungen vorzubeugen. Diese einfache Vorgehensweise trägt wesentlich zur Verbesserung der Druckqualität und zur Verringerung des Verschmutzungsrisikos bei.
6. Führen Sie Qualitätsprüfungen durch
Führen Sie Reibetests an Testdrucken durch, um die Abriebfestigkeit zu bewerten. Dieser Schritt hilft, Probleme frühzeitig zu erkennen und Anpassungen vorzunehmen, bevor große Auflagen gedruckt werden.
Spezielle weiße Plastisol-Tinten und Crocking
Verschiedene Arten weißer Plastisol-Tinten, wie etwa weiße Glitzer-Plastisol-Tinte und weiße, im Dunkeln leuchtende Plastisol-Tinte, haben einzigartige Eigenschaften, die beim Drucken besondere Aufmerksamkeit erfordern:
- Weiße Glitzer-Plastisol-Tinte: Die Glitzerpartikel verleihen dem Druck Struktur und Reflektivität, erhöhen aber auch die Dicke. Stellen Sie sicher, dass die Glitzerdrucke vollständig ausgehärtet sind, da die zusätzliche Masse zu einer ungleichmäßigen Aushärtung führen kann.
- Weiße, im Dunkeln leuchtende Plastisol-Tinte: Diese Tinten erzeugen ihren Leuchteffekt durch phosphoreszierende Pulver. Richtiges Mischen und Aushärten sind unerlässlich, um die Leuchtdauer zu gewährleisten und das Risiko von Abnutzung zu minimieren.
Fehlerbehebung bei häufigen Problemen
Wenn beim Siebdruck das Problem des Abfärbens der weißen Plastisoltinte auftritt, ziehen Sie die folgenden Schritte zur Fehlerbehebung in Betracht:
Problem: Tinte reibt sich nach dem Aushärten ab
- Überprüfen Sie, ob die Aushärtungstemperatur während des gesamten Drucks erreicht wurde.
- Überprüfen Sie, ob in Ihrem Aushärtungsgerät ein ungleichmäßiges Heizmuster vorliegt.
Problem: Dicke Ablagerungen lösen sich ab oder blättern ab
- Bewerten Sie die verwendete Siebmaschenzahl und passen Sie sie gegebenenfalls an eine feinere Maschenzahl an.
- Reduzieren Sie den Farbauftrag, indem Sie den Druck oder Winkel Ihres Rakels ändern.
Problem: Spezialtinte haftet nicht
- Sorgen Sie für eine ordnungsgemäße Mischung von Tinten wie im Dunkeln leuchtender weißer Plastisoltinte, um die Konsistenz zu wahren.
- Verwenden Sie ein kompatibles Gewebe und ziehen Sie bei schwierigen Untergründen eine Vorbehandlung in Betracht.
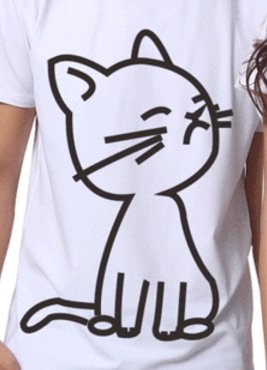
Schlussfolgerung
Das Problem des Abfärbens von weißer Plastisoltinte im Siebdruck ist eine Herausforderung, die während des gesamten Druckprozesses sorgfältige Aufmerksamkeit erfordert. Von der Aushärtungstemperatur bis zur Substratauswahl trägt jeder Schritt dazu bei, Abfärben zu verhindern und langlebige Drucke zu gewährleisten. Mit den in diesem Leitfaden beschriebenen Best Practices erzielen Sie professionelle Ergebnisse und reduzieren das Abfärberisiko, selbst bei der Verwendung von Spezialtinten wie weißer Glitzer-Plastisoltinte und weißer, im Dunkeln leuchtender Plastisoltinte. Egal, ob Sie erfahrener Drucker oder Anfänger sind, diese Erkenntnisse helfen Ihnen, Abfärbeprobleme zu überwinden und stets hochwertige Drucke zu erstellen.