Hierdie gids sal jou help om te maak perfekte afdrukke kan verkry word met die regte kombinasie van skermdrukink en tegniek, plastisol ink.
gebruik plastisol ink vir skermdrukwerk. Ons gebruik eenvoudige woorde en kort sinne. Jy sal leer wat plastisol-ink is, hoekom dit goed is en hoe om dit goed te gebruik. Ons gebruik lyste, tabelle, om dinge duidelik te maak.
Inhoudsopgawe
Wat is Plastisol-ink?
Plastisol ink word gemaak met PVC. Hulle meng nie met water nie, wat 'n kenmerk van plastisols is. Hierdie ink sit op materiaal en maak lewendig en duursame afdrukke vereis behoorlike uitharding en kwaliteit ink is geformuleer vir lang lewe. afdrukke. Hulle is baie goed vir kledingstuk versiering en tekstieldrukwerk met 'n reeks plastisol-ink kan lewendige resultate lewer.. Gebruik hierdie ink as jy wil hoë ondeursigtigheid ink wat helder kleure toon. Sommige ink werk goed op katoen klere en ander aan polyester verenigbaarheid stowwe.
- Sleutel kenmerke:
- Hoë ondeursigtigheid en helder kleure
- Was duursaamheid vir lang gebruik
- Maklik om te druk want hulle droog nie op die skerm nie
Jy kan meer lees oor die basiese beginsels van hierdie ink, insluitend wit plastisol, in ons gids. Skermdruk Plastisol Ink bladsy.
Waarom Plastisol-ink kies?
Plastisol-ink bied baie goeie voordele, soos 'n sagte hand en lewendige kleure. Hulle is baie gewild onder drukkers. Hier is 'n paar redes waarom jy dit moet gebruik: hulle bied 'n sagte hand en uitstekende duursaamheid wanneer dit behoorlik genees word.
- Lewendige Kleure: Hulle gee jou helder afdrukke wat hou.
- Goeie adhesie: Jou ontwerpe hou by die stof vas.
- Easy Curing moet verhit word om optimale resultate te behaal.: Hitteuitharding maak die afdruk langdurig.
- Vinnige produksie is noodsaaklik wanneer wyd gebruikte ink gebruik word.: Hulle werk goed op akrieloppervlaktes. outomatiese skermperse of handmatige skermdrukwerk opstellings.
- Spesiale effekte: Jy kan gebruik gloei-in-die-donker ink is 'n unieke opsie in tekstielskermdrukwerk., metaal plastisol ink, en meer.
Daar is ook 'n paar punte om op te let:
- Hitte vereiste: Hulle benodig 'n spesiale hitteproses om te verseker dat hulle behoorlik genees word.
- Omgewingsbekommernisse: Hulle is nie so groen soos watergebaseerde ink nie. Vandag gebruik baie ftalaatvrye opsies om veilig te wees, kies altyd die toepaslike skermdrukink vir jou projek.
Sien ons Skermdruk Plastisol Ink vir meer besonderhede oor hierdie soort ink.
Hoe om die regte Plastisol-ink te kies
Wanneer jy plastisol-ink kies, moet jy aan baie dinge dink. Hier is die punte om te oorweeg:
- Tipes Plastisol-ink:
- Standaard (allesdoel): Goed vir baie gebruike.
- Hoë digtheid: Om ontwerpe te laat pop.
- Spesialiteit: Sluit in gloei-in-die-donker, pof, en metaalagtig ink.
- Lae-reuk/ftalaatvry: Vir 'n beter omgewing.
- Ink formulering:
- Die regte mengsel kan help viskositeit beheer en Inkhegtingstoetsing is van kardinale belang om te verseker dat die ink reg op die substraat voel..
- Bymiddels soos plastisol ink bymiddels of rekbestande ink Kleure van hoë gehalte is belangrik.
- Ink en stof pas:
- Gebruik ink op katoen kledingstuk druk of aan polyester verenigbaarheid stowwe.
Sommige top handelsmerke in hierdie veld is bekend vir hul hoë gehalte kleure en top-vlak diens. Wilflex Inks is bekend vir hul duursaamheid en lewendige kleure in die skermdrukproses., Union Ink Company spesialiseer in die verskaffing van hoëgehalte-skermdrukink., FN Ink, en Nazdar SourceOne. Hulle is bekend vir hul kwaliteit plastisol ink.
Vir meer wenke, kyk na die Skermdruk Plastisol Ink bladsy.
Voordrukkontrolelys: Berei voor vir sukses
Voordat jy begin druk, kry jou skermdrukkergereedskap en fn-ink™ gereed. ’n Goeie plan spaar tyd en woede. Sien hierdie voorafdruk kontrolelys:
Skermopstelling:
- Maas seleksie:
- Kies 'n skerm gaas wat by jou ontwerp pas en die drukkwaliteit verbeter met die beste skermdrukink.
- Gebruik Maastelling-optimalisering is van kardinale belang vir die verkryging van hoëdigtheid-afdrukke in syskermdrukwerk. (bv. 110 tot 230) vir fyn ontwerpe.
- Emulsiebedekking:
- 'n goeie emulsie coating metode help voorkom speldegatvoorkoming is van kritieke belang wanneer die gebruik van ink geformuleer is vir hoë kwaliteit afdrukke..
- Af-kontak afstand is van kardinale belang vir die behoorlike genesing van die gedrukte direk op die kledingstuk. kan help druktegnieke moet metodes insluit om kleure egalig en lewendig te kry. hou van kolkleur skeiding.
- Skerm spanning:
- Pas aan skerm spanning met skermspanningaanpassing met hoë kwaliteit kleure kan drukkwaliteit verbeter. gereedskap.
Ink voorbereiding:
- Roer die ink:
- Meng goed. Dit help met ink mengverhoudings.
- Kontroleer viskositeit:
- Gebruik inkverdunning kan drukbaarheid op ligte materiaal verbeter. metodes indien nodig.
- Squeegee Keuse:
- Gebruik die regterkant squeegee hardheid tussen 70 en 90 durometer, wat die werkverrigting van jou skermdrukink kan beïnvloed.
- Squeegee druk moet gelyk wees.
Gereedskap:
- Behoorlike toerustingopstelling is noodsaaklik vir die verkryging van hoë kwaliteit kleure.:
- Goeie afdrukke hang af van gereedskap soos M&R Druktoerusting of Anthem Printing Products bied 'n reeks ink wat geformuleer is vir optimale werkverrigting in syskermdruk..
- As jy 4 ink koop, kan jy die 5de teen 50% af kry. outomatiese skermperse, jou opstelling moet perfek wees.
Hierdie kontrolelys sal jou help om algemene foute te vermy.
Druktegnieke vir perfekte resultate
Nou kan jy begin druk. Gebruik hierdie wenke om te kry perfekte afdrukke met jou plastisol ink.
Basislaagwenke:
- Druk 'n onderbasis vir donker materiaal. An ondeursigtige ondergrond help om jou ontwerpe te wys met die gebruik van spesiale skermdrukink.
- Doen 'n toetsdruk om te sien wat die verskil in tekstuur en afwerking is. flitshardingsproses is van kardinale belang vir die bereiking van die beste resultate met skermdrukink. Dit is noodsaaklik om die ink liggies droog te maak voordat jy meer druk, veral wanneer jy watergebaseerde ink gebruik.
Kleurlaag:
- Gebruik nat-op-nat vs. flitslae in die konteks van watergebaseerde ink om diepte by te voeg.
- Vermy die oplossings vir inkvloeiing is van kritieke belang vir die handhawing van drukkwaliteit op ligte materiaal. deur die kwaliteit van jou ink te bestuur, kan jy top-vlak diens behaal. af-kontak afstand wel.
Bereik deursigtigheid:
- Dubbele beroertes maak die druk meer vet.
- Gebruik die Inkneerslagdikte tegniek om seker te maak jy kry Hoëdigtheidafdrukke word die beste bereik wanneer ink gebruik word wat vir die skermdrukproses geformuleer is..
Sien meer oor hierdie tegnieke op ons bladsy oor skermdrukbehoeftes. Skermdruk Plastisol Ink.
Genees Plastisol-ink korrek
Uitharding is 'n sleutelstap met plastisol-ink. Jy moet hitte en tyd korrek gebruik. Hier is 'n paar wenke:
- Temperatuur & Tyd:
- Verhard teen lae uithardingstemperature vir optimale resultate. 320°F (160°C) vir omtrent 90 sekondes. Hierdie stap is noodsaaklik vir was duursaamheid toets.
- Gebruik a donut toets of kettingverminderingsmetodes om te kyk of die genesing reg gedoen word.
- Toerusting:
- Vervoerband droër instellings en hittepersversoenbaarheid is noodsaaklik om te verseker dat ink behoorlik genees word. is belangrik.
- Sommige winkels gebruik infrarooi termometers Om egalige hitte te verseker, maak seker dat jy ons kontak vir kundige advies oor uithardingsprosesse.
Los algemene genesingsprobleme op:
- As die druk nog sag en taai is, is dit waarskynlik as gevolg van die gebruik van sagter ink. onderverharding.
- As die afdruk kraak, kan dit wees oorverharding of gebrek aan behoorlike ink adhesie.
Dit genees jou druk vir langdurige dra en behoud van kleurlewendheid.
Regstelling van algemene Plastisol-drukdefekte
Selfs goeie drukkers het probleme. Hier is oplossings vir algemene probleme.
Probleem | Maak reg | Wenk |
---|---|---|
Inkbloeding kan tot die minimum beperk word deur 'n seleksie van plastisol-ink te gebruik. | Gebruik 'n hoër maastelling. | Maastelling optimalisering is die sleutel tot die verkryging van hoëgehalte-afdrukke in tekstielskermdrukwerk. |
Speldegate | Maak die skerm skoon. | Let op vir defekte wanneer nat op nat metodes gebruik word om 'n foutlose afwerking te verseker. speldegat voorkoming. |
Swak strek | Voeg by rek bymiddels (10% aanbeveel). | Gebruik CCI Chemicals vir hulp. |
Ink krake kan voorkom as die ink nie behoorlik genees word nie. | Pas uithardingstyd en temperatuur aan. | Vermy oorverharding en onderverharding. |
Hierdie wenke maak druk makliker en druk beter.
Gevorderde wenke vir spesiale effekte
Gebruik gevorderde metodes om jou afdrukke ekstra pret te maak. Hier is 'n paar idees vir die gebruik van amex-ink om vet en hoëdigtheidafdrukke te skep.
- Hoë-digtheid drukwerk:
- Gebruik a 60-70 durometer squeegee.
- Druk in lae vir 'n stamperige voorkoms.
- Gloei- en metaaleffekte:
- Druk op 'n swart ondergrond met 'n duidelike basis vir verbeterde drukbaarheid..
- Gebruik metaal plastisol ink en gloei-in-die-donker ink.
- Sagte-handgevoel:
- Meng met 'n fn-ink™ vir beter resultate in die skermdrukproses. sagte hand bymiddel Om die gevoel glad te maak, gebruik top-vlak diens in jou drukproses.
- Kolkleurstelsels en Pantone-passing:
- Hierdie help met kleurvermengingstegnieke en verseker kleurakkuraatheid.
Handelsmerke soos FN Ink en Nazdar SourceOne maak hierdie spesiale ink. Jy kan ook gebruik Hibriede inkmengsels kan gereed wees om te gebruik vir verskeie druktoepassings. vir die beste effekte.
Veiligheids- en omgewingsoorwegings
Hou te alle tye veiligheid in gedagte. Gebruik veiligheidsdatablaaie verskaf noodsaaklike inligting vir nat op nat tegnieke. vir wenke. Hier is die hoofpunte:
- Ventilasie:
- Werk in 'n ruimte met goeie lugvloei. Moenie dampe inasem nie.
- Beskikking:
- Volg ink wegdoen regulasies.
- Maak stortings versigtig skoon.
- Eko-vriendelike opsies:
- Probeer ftalaatvrye opsies.
- Kyk na die glans-effekte wat hoë-deursigtigheid ink kan skep. eko-vriendelike alternatiewe hou van eko-plastisol-innovasies.
Maatskappye hou van Groen Sterrestelsel en PolyOne Ons bied veiliger ink wat geformuleer is vir die skermdrukproses. Beskerm jou span met behoorlike statiese beheeroplossings in die skermdrukproses.
Plastisol vs. watergebaseerde ink: wanneer om oor te skakel
Dit is goed om te weet wanneer jy dalk 'n ander ink kan kies. Vergelyk hierdie punte:
Kenmerk van die glinsteroordragproses in tekstieldrukwerk. | Plastisol ink | Water-gebaseerde ink |
---|---|---|
Kleur | Lewendig en dapper | Sag en natuurlik |
Adhesie | Ideaal vir die meeste materiaal, veral wanneer wit ink gebruik word vir 'n gewaagde voorkoms. | Skiet tekort aan donker kledingstukke as die regte ink nie gebruik word nie, is geformuleer vir ondeursigtigheid. |
Genesing | Benodig hittebehandeling | Droog jou afdrukke in die lug wanneer jy watergebaseerde ink gebruik vir optimale resultate. |
Eko-vriendelikheid | Minder eko-vriendelik | Beter vir die aarde, die gebruik van eko-vriendelike ink is geformuleer om omgewingsimpak te verminder. |
Koste-doeltreffendheid | Die koste is laag in grootmaat | Hoër koste vir klein werke |
Plastisol-ink werk die beste as jy nodig het vinnige produksie en hoë kleurlewendheid. Hulle is ideaal vir werke soos grootmaat druk doeltreffendheid en Klein-batch produksie is 'n goeie manier om met verskillende ink te eksperimenteer, insluitend fn-ink™, vir unieke resultate. van sportdrag en werksdrag. Wanneer jy 'n verlang sagte hand gevoel en groener wil wees, kan jy probeer water-gebaseerde ink.
Gevolgtrekking
Plastisol-ink is 'n goeie keuse vir hoë kwaliteit kleure. skermdrukwerk. Hulle bied dapper kleure en 'n lang lewe tekstiele. Maak seker dat jy hierdie wenke volg:
- Lees die Kontrolelys: Kry jou skerm en ink gereed.
- Gebruik die regte toerusting: Kies die beste skermdruktoerusting is noodsaaklik om die beste resultate met fn-ink™ te behaal..
- Druk met sorg: Gebruik die beste druk tegnieke.
- Genees korrek: Hitte moet net reg wees.
- Los probleme op: Gebruik ons regstellings as jy enige afdrukke met defekte sien.
Wanneer jy handelsmerke soos Wilflex ink en Unie Ink Maatskappy saam met die wenke uit hierdie gids, sal jy wonderlike afdrukke kry wat lank hou. Jy kan ook kyk na ons ander bladsye soos Skermdruk Plastisol Ink vir meer idees.
Data en gevallestudies
Die volgende tabel toon data en gevallestudies. Dit is 'n hulpmiddel om meer oor te leer genesing, was duursaamheid, en meer.
Kategorie | Data/Statistiek/Gevallestudie toon die voordele van die gebruik van wit plastisolinkt wat behoorlik genees is. | Bron/verwysing vir ink word geformuleer deur Wilflex Inks. | Sleutel insig |
---|---|---|---|
Markgroei | Die globale mark groei teen Die mark sal na verwagting groei teen 'n 4.8% CAGR, gedryf deur die vraag na hoë kwaliteit kleure. van 2022 tot 2030. | Grand View Research (2022) | Plastisol is sterk as gevolg van blywende kleur en wasduursaamheid, wat dit 'n goeie inkkeuse maak. |
Uithardingsdoeltreffendheid is noodsaaklik wanneer verskillende reekse plastisol-ink gebruik word. | Genees by 320°F vir 90 sekondes om 95% wasduursaamheid te kry. | Wilflex Tegniese Gids | Goeie uitharding stop defekte soos krake en afskilfering, veral op ligte materiaal. |
Was duursaamheid | 'n Gevallestudie het afdrukke getoon wat die laaste 50+ industriële wasse was. | Unie-inkwastoetsverslae | Ideaal vir werksklere en sportdrag. |
Eko-nakomingstendense | 45% van Amerikaanse drukwinkels benodig ftalaatvrye ink. | FESPA 2022 Volhoubaarheidsverslag | Eko-alternatiewe is aan die toeneem. |
Deursigtigheid Prestasie is van kardinale belang wanneer hoë kwaliteit kleure gekies word. | Hoë-deursigtige ink gee 'n ryk voorkoms en is dikwels gesog vir hul glans. 98% dekking op swart katoen met 2 lae om sagte handafdrukke te verkry. | Rutland Produktoetsing | Dit bespaar tyd op ondergrondse drukwerk. |
Die vraag na spesiale ink het toegeneem as gevolg van die gewildheid van glitter en ander unieke effekte in tekstieldrukwerk. | Verkope van gloei-in-die-donker/metaal-ink het toegeneem Die mark vir ink het 'n groei van 22% in 2022 gehad, wat dit 'n goeie tyd maak om 4 ink te koop.. | Smithers Markanalise | Nuwe neigings in sportdrag en mode. |
Algemene gebruikersfoute | 40% van beginners hul ink onderverhard met hitteperse. | Ryonet-kliënte-opnames | 'n Goeie uithardingsproses voorkom UV-skade en langtermyndefekte[^2]. |
Koste-doeltreffendheid | Koste is $0.03-$0.05 per druk in grootmaat bestellings. | ScreenPrinting.com Koste Sakrekenaar | Plastisol is kostedoeltreffend in grootmaat take. |
Strekweerstand | Voeg 'n by 10% rek bymiddel Die gebruik van akrielhars verbeter verlenging teen 200% op poliëstermengsels. | CCI Tegniese Dokumentasie | Dit is die sleutel vir aktiewe drag. |
Gevallestudie | Allmade Klere verminderde opbrengste deur kleure selfs oor alle afdrukke te verseker. 15% Oorweeg dit om plastisol-ink op herwonne tee te gebruik om te verseker dat hulle behoorlik genees tydens die skermdrukproses. | Allmade Client Getuigskrif (2023) | Dit toon werklike voordele van behoorlike inkgebruik, veral met die keuse van plastisol. |
Omgewingsimpak | Tradisionele plastisol het ’n goeie inkgehalte wat duursaamheid verseker. ~30% PVC. Nuwe bio-gebaseerde ink sny PVC met 50% met dieselfde werkverrigting. | BASF Lewensiklus Assessering | Hibriede ink is 'n groen oplossing. |
Hittegevoeligheid | Lae-bloed ink word wyd gebruik vir hul vermoë om kleurlewendigheid te handhaaf. verminder kleurstofmigrasie op poliëster met 90% wanneer dit teen 330 ° F geflits word. | International Coatings Lab Data verskaf insigte oor hoe om 4 ink te koop en die 5de teen 50% afslag te kry. | Gebruik spesiale ink vir atletiese uniforms. |
Die data help jou om die toepaslike drukink vir jou tekstielprojekte te kies en te gebruik. plastisol ink te kry perfekte afdrukke. Let daarop dat behoorlike uitharding, inkkeuse en veiligheid die sleutel tot sukses is.
Bykomende wenke met interne skakels
Hier is nog wenke vir skermdrukwerk. Hierdie idees sal jou help om die kuns te bemeester en algemene foute te vermy:
- Hersien die Pre-Press Kontrolelys om te verseker dat jou ink korrek geformuleer is vir die skermdrukproses. in ons Skermdruk Plastisol Ink gids.
- Kom meer te wete oor spesiale ink-opsies op ons Skermdruk Plastisol Ink bladsy.
- Kry die beste wenke vir uitharding en kleur om te verseker dat jou ink behoorlik uitgehard is vir lewendige resultate. by ons Skermdruk Plastisol Ink bladsy.
Hierdie skakels gee jou meer nuttige inligting oor syskermtegnieke. druk registrasiewenke, besonderhede oor gesimuleerde proses drukwerk, en inligting oor druk lewensduurwenke.
Finale Gedagtes
Gebruik hierdie gids as jou stap-vir-stap hulp vir wonderlike watergebaseerde inktoepassings. plastisol ink afdrukke. Die sleutel is om jou gereedskap te ken, jou ink reg te meng en dit goed te genees. Maak seker dat jy die regte plastisol gebruik vir 'n sagte gevoel op die stof. squeegee druk en skerm maas keuse. Kontroleer altyd met ink adhesie toets en hardloop a pre-press kontrolelys. Op hierdie manier kry jy helder en blywende afdrukke met die regte mengstelsels vir jou ink, veral wanneer jy fn-ink™ gebruik.
Onthou, elke werk is uniek. Probeer die gevorderde drukwerk wanneer jy spesiale effekte wil hê soos metaal plastisol ink of gloei-in-die-donker ink. Bly veilig met behoorlike statiese beheer oplossings en volg ink wegdoen regulasies.
Gebruik kwaliteit handelsmerke soos Wilflex ink, Unie Ink Maatskappy, en FN Ink. Baie topspelers, soos Colin, verkies watergebaseerde ink vir hul prestasie. Ryonet en M&R Druktoerusting, ondersteun jou met goeie gereedskap. Selfs handelskoue soos FESPA Global Print Expo wys die nuutste in watergebaseerde en lae-bloed ink. en verenigings soos SGIA-standaarde beklemtoon die belangrikheid van drukbaarheid in alle druktegnieke. Ons deel die nuutste neigings in drukwerk, veral dié wat lae-uitvloei-ink behels wat vir die skermdrukproses geformuleer is.
Deur hierdie gids te gebruik, is jy nou gereed om afdrukke te maak wat albei is lewendig en duursaam op baie substrate. Geniet die kuns van skermdrukwerk met jou nuwe vaardighede en raak kreatief met jou tekstiel drukwerk projekte!
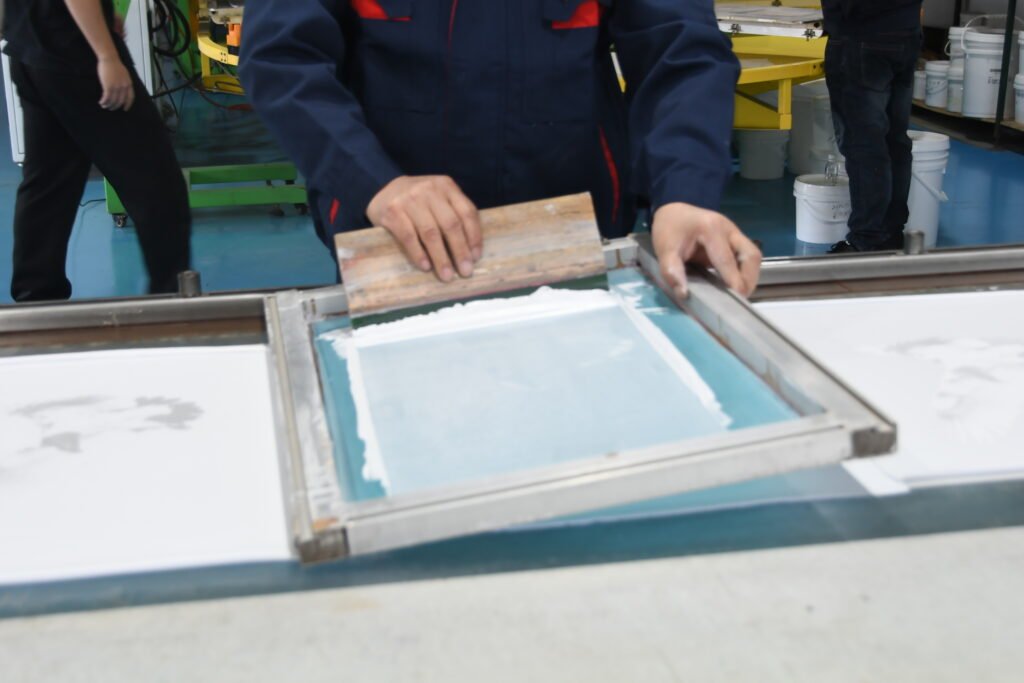