In the vibrant world of screen printing, reflective plastisol screen print ink stands out as a unique and versatile material that adds a dazzling dimension to your designs. Whether you’re creating safety apparel for nighttime visibility or simply wanting to add a pop of eye-catching shine to your artwork, understanding what reflective plastisol screen print ink is and how it works is crucial. This article delves into the depths of this fascinating ink type, exploring its properties, applications, and the intricacies of its operation.
Understanding Reflective Plastisol Ink
Reflective plastisol screen print ink is a specialized type of ink formulated to incorporate reflective particles. These particles, often made of glass beads or microprismatic lenses, are embedded within the ink’s plastisol base. Plastisol ink, known for its versatility and durability, consists of a vinyl resin suspended in a liquid plasticizer. When heated, the plasticizer evaporates, leaving behind a resilient, flexible print that adheres well to various fabrics.
Reflective plastisol ink works by redirecting light. The embedded reflective particles scatter incident light back towards its source, creating a bright, visible glow under low-light conditions. This property makes reflective plastisol screen print ink ideal for applications requiring nighttime visibility, such as athletic wear, roadworker uniforms, and children’s clothing.
The Science Behind Reflex Blue Plastisol Ink
One popular color variation within the reflective plastisol ink family is reflex blue plastisol ink. This particular shade leverages the reflective properties of the ink while adding a bold, vibrant blue hue to designs. Reflex blue plastisol ink works similarly to other reflective inks, with the added aesthetic appeal of its striking color.
The science behind reflex blue plastisol ink’s reflectiveness lies in its formulation. The ink contains a precise concentration of reflective particles, balanced to ensure optimal light reflection without compromising the ink’s flow and coverage. This balance is crucial for achieving crisp, even prints that maintain their reflective properties even after multiple washes.
Working with Reflective Plastisol Ink
Using reflective plastisol screen print ink requires a few considerations to ensure the best results. Here’s a closer look at the process:
Preparing the Screen
Before printing, ensure your screen is clean and free of any residue from previous prints. Residual plastisol ink can interfere with the reflective particles’ performance, reducing the ink’s effectiveness. Use a dedicated screen cleaner and scraper to remove any cured plastisol ink or other contaminants.
Mixing the Ink
Proper mixing is essential for achieving consistent results with reflective plastisol ink. Use a mechanical mixer to thoroughly blend the ink, ensuring an even distribution of reflective particles. Over-mixing can lead to air bubbles, while under-mixing can result in uneven particle distribution, affecting the ink’s reflective properties.
Printing Techniques
When printing with reflective plastisol screen print ink, use a slower print stroke to avoid spreading the ink too thinly. A thicker application ensures better coverage and reflection. Additionally, maintain consistent pressure on the squeegee to ensure even ink deposition across the fabric.
Drying and Curing
After printing, dry the ink at a moderate temperature to prevent premature curing. Once dry, cure the ink at the recommended temperature and time to ensure proper adhesion and durability. Improper curing can lead to ink cracking, fading, or loss of reflective properties.
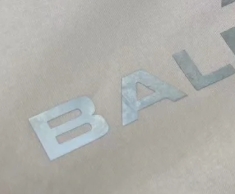
Common Issues and Solutions
While reflective plastisol screen print ink offers numerous benefits, it can present some challenges, particularly for inexperienced printers. Here are some common issues and solutions:
Ink Clogging
Reflective particles can sometimes cause ink clogging in the screen. Regular screen cleaning and the use of a higher mesh count can help minimize this issue. Higher mesh counts allow for finer ink deposition, reducing the likelihood of particle accumulation.
Ink Scattering
Over-application or excessive pressure during printing can cause reflective plastisol ink to scatter, leading to blurred prints. Use a lighter touch and ensure even, controlled pressure during the print stroke to avoid this problem.
Removal of Cured Plastisol Ink
If you need to remove cured plastisol ink from a screen, whether it’s reflective or not, use a dedicated ink remover or a strong solvent like mineral spirits. Soak the screen in the solvent, then scrub gently with a soft brush to loosen and remove the ink. Rinse thoroughly and allow the screen to dry completely before reusing.
Removing Plastisol Ink from Screens
Removing plastisol ink from screens, whether cured or uncured, is an essential part of maintaining screen printing equipment. For uncured ink, simple rinsing with water may suffice, depending on the ink’s formulation. However, for cured plastisol ink, a more robust cleaning solution is required.
Using a solvent-based cleaner or ink remover is the most effective way to tackle cured ink residue. Ensure proper ventilation when using these chemicals and follow the manufacturer’s instructions for safe handling and disposal. Always wear gloves and protective eyewear when working with solvents to avoid skin and eye irritation.
Advanced Applications of Reflective Plastisol Ink
Beyond its use in nighttime safety wear, reflective plastisol screen print ink has various advanced applications. It can be used to create eye-catching graphics on promotional materials, automotive decals, and even architectural signage. The versatility of reflective plastisol ink allows it to be adapted for use on a wide range of substrates, including paper, metal, and plastic.
In the automotive industry, reflective plastisol ink is often used to create high-visibility markings on vehicles, enhancing safety and compliance with traffic regulations. Its durability and resistance to weathering make it a reliable choice for long-lasting, high-performance applications.
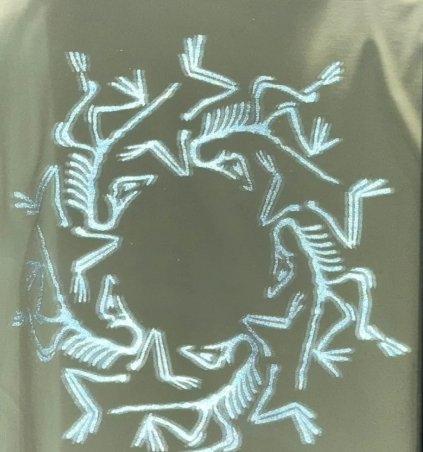
Conclusion
Reflective plastisol screen print ink is a powerful tool for adding visibility and aesthetic appeal to your screen printing projects. By understanding its formulation, printing techniques, and potential challenges, you can harness its full potential to create stunning, functional designs. Whether you’re working on a small-scale project or a large-scale production run, investing in high-quality reflective plastisol ink and proper equipment will pay off in the form of superior prints and satisfied customers.